RIDHA DARMAWAN
Supply Chain Manager at PT. Daikin Airconditioning Indonesia- Claim this Profile
Click to upgrade to our gold package
for the full feature experience.
-
English Full professional proficiency
-
Indonesian Native or bilingual proficiency
-
French Professional working proficiency
Topline Score
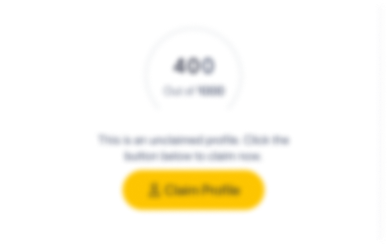
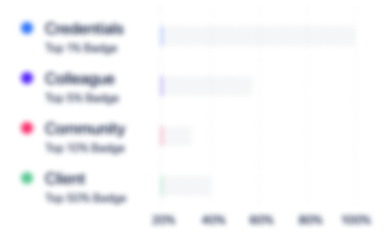
Bio

LinkedIn User
I was met him 2 years ago while I've just started my day in MBI, my first impression about him was he is good person, smart, good personality, supple, full sense of humor, good thinker, man behind brilliant ideas and the most important he very fluent in French. We were worked together to control inventory in and out accurately, maintain stock level in optimal point to serve our customer very best.

LinkedIn User
I was met him 2 years ago while I've just started my day in MBI, my first impression about him was he is good person, smart, good personality, supple, full sense of humor, good thinker, man behind brilliant ideas and the most important he very fluent in French. We were worked together to control inventory in and out accurately, maintain stock level in optimal point to serve our customer very best.

LinkedIn User
I was met him 2 years ago while I've just started my day in MBI, my first impression about him was he is good person, smart, good personality, supple, full sense of humor, good thinker, man behind brilliant ideas and the most important he very fluent in French. We were worked together to control inventory in and out accurately, maintain stock level in optimal point to serve our customer very best.

LinkedIn User
I was met him 2 years ago while I've just started my day in MBI, my first impression about him was he is good person, smart, good personality, supple, full sense of humor, good thinker, man behind brilliant ideas and the most important he very fluent in French. We were worked together to control inventory in and out accurately, maintain stock level in optimal point to serve our customer very best.

Experience
-
PT. Daikin Airconditioning Indonesia
-
Wireless Services
-
300 - 400 Employee
-
Supply Chain Manager
-
Nov 2015 - Present
1. Ensuring 3 PL to implement efficient and best practice of warehousing activity as well as process of distribution. 2. Reassuring stock accuracy by weekly and monthly monitoring and share its report to other department (mainly sales, sales planning, sales administration as well as top management). 3. Reassuring all of Import orders are well followed up internally and externally (shipper, shipping line, customs agent and other government authorities). 4. Evaluation of overall monthly… Show more 1. Ensuring 3 PL to implement efficient and best practice of warehousing activity as well as process of distribution. 2. Reassuring stock accuracy by weekly and monthly monitoring and share its report to other department (mainly sales, sales planning, sales administration as well as top management). 3. Reassuring all of Import orders are well followed up internally and externally (shipper, shipping line, customs agent and other government authorities). 4. Evaluation of overall monthly logistic cost. 5. Evaluation of Logistic KPI (warehousing and transport). 6. Maintaining and checking all report for managerial purposes (weekly delivery report, weekly stock report). 7. Follow up urgent matters regarding outstanding delivery and outstanding import orders. 8. Maintaining good relationships with external parties such as customer, customs, logistic vendor and other legal authorities. 9. Monitoring all logistic center operation performance which run by 3PL or Daikin itself throughout Indonesia. 10. Logistic annual budget planning. 11. Actively joining logistic project for upgrading performance with Daikin Japan team. 12. Together with service team to follow up damage product due to mishandling process at warehouse and during distribution process. Show less 1. Ensuring 3 PL to implement efficient and best practice of warehousing activity as well as process of distribution. 2. Reassuring stock accuracy by weekly and monthly monitoring and share its report to other department (mainly sales, sales planning, sales administration as well as top management). 3. Reassuring all of Import orders are well followed up internally and externally (shipper, shipping line, customs agent and other government authorities). 4. Evaluation of overall monthly… Show more 1. Ensuring 3 PL to implement efficient and best practice of warehousing activity as well as process of distribution. 2. Reassuring stock accuracy by weekly and monthly monitoring and share its report to other department (mainly sales, sales planning, sales administration as well as top management). 3. Reassuring all of Import orders are well followed up internally and externally (shipper, shipping line, customs agent and other government authorities). 4. Evaluation of overall monthly logistic cost. 5. Evaluation of Logistic KPI (warehousing and transport). 6. Maintaining and checking all report for managerial purposes (weekly delivery report, weekly stock report). 7. Follow up urgent matters regarding outstanding delivery and outstanding import orders. 8. Maintaining good relationships with external parties such as customer, customs, logistic vendor and other legal authorities. 9. Monitoring all logistic center operation performance which run by 3PL or Daikin itself throughout Indonesia. 10. Logistic annual budget planning. 11. Actively joining logistic project for upgrading performance with Daikin Japan team. 12. Together with service team to follow up damage product due to mishandling process at warehouse and during distribution process. Show less
-
-
-
DPO International
-
Malaysia
-
Food and Beverage Services
-
100 - 200 Employee
-
Supply Chain Manager
-
Jul 2013 - Nov 2015
1. Implementing efficient and best practice of Inventory management of material 2. Checking, reassuring and confirming whether purchase request raised by Sales team are in correspondence to the actual stock and future stock. 3. Reassuring stock accuracy by weekly and monthly monitoring. 4. Reassuring all of Import orders are well followed up 5. Cost Evaluation and performance evaluation of freight and forwarder/custom broker. 6. Evaluation of delivery achievement (transport cost… Show more 1. Implementing efficient and best practice of Inventory management of material 2. Checking, reassuring and confirming whether purchase request raised by Sales team are in correspondence to the actual stock and future stock. 3. Reassuring stock accuracy by weekly and monthly monitoring. 4. Reassuring all of Import orders are well followed up 5. Cost Evaluation and performance evaluation of freight and forwarder/custom broker. 6. Evaluation of delivery achievement (transport cost and on time target) 7. Follow up Purchase Order of customer by setting up delivery schedule. 8. Maintaining all report for managerial purposes (weekly delivery report, weekly stock report) 9. Follow up urgent matters regarding outstanding delivery and outstanding import orders. 10. Maintaining all supporting documents of import are updated so that custom clearance process are well managed. 11. Maintaining good relationships with external party such as customer, customs, shipping lines, freight forwarders and other legal authorities. 12. Determining minimum and maximum stock policy together with Sales department and Finance department 13. Setting up Annual operational budget plan for Supply Chain Department of Indonesia Show less 1. Implementing efficient and best practice of Inventory management of material 2. Checking, reassuring and confirming whether purchase request raised by Sales team are in correspondence to the actual stock and future stock. 3. Reassuring stock accuracy by weekly and monthly monitoring. 4. Reassuring all of Import orders are well followed up 5. Cost Evaluation and performance evaluation of freight and forwarder/custom broker. 6. Evaluation of delivery achievement (transport cost… Show more 1. Implementing efficient and best practice of Inventory management of material 2. Checking, reassuring and confirming whether purchase request raised by Sales team are in correspondence to the actual stock and future stock. 3. Reassuring stock accuracy by weekly and monthly monitoring. 4. Reassuring all of Import orders are well followed up 5. Cost Evaluation and performance evaluation of freight and forwarder/custom broker. 6. Evaluation of delivery achievement (transport cost and on time target) 7. Follow up Purchase Order of customer by setting up delivery schedule. 8. Maintaining all report for managerial purposes (weekly delivery report, weekly stock report) 9. Follow up urgent matters regarding outstanding delivery and outstanding import orders. 10. Maintaining all supporting documents of import are updated so that custom clearance process are well managed. 11. Maintaining good relationships with external party such as customer, customs, shipping lines, freight forwarders and other legal authorities. 12. Determining minimum and maximum stock policy together with Sales department and Finance department 13. Setting up Annual operational budget plan for Supply Chain Department of Indonesia Show less
-
-
-
-
General and raw material warehouse section head
-
Feb 2012 - Jul 2013
1. Maintaining stock accuracy (physical vs SAP system) 2. Working closely with marketing and sales department regarding receiving and delivery of merchandise goods 3. Receiving and input data of incoming material and outgoing material 4. Conducting weekly and monthly stock taking. 5. Initiating, controlling and monitoring of Housekeeping of warehouse through implementing 5S 6. Reporting weekly and monthly stock position to PPIC and Accounting department. 7. Weekly… Show more 1. Maintaining stock accuracy (physical vs SAP system) 2. Working closely with marketing and sales department regarding receiving and delivery of merchandise goods 3. Receiving and input data of incoming material and outgoing material 4. Conducting weekly and monthly stock taking. 5. Initiating, controlling and monitoring of Housekeeping of warehouse through implementing 5S 6. Reporting weekly and monthly stock position to PPIC and Accounting department. 7. Weekly coordination with production department, engineering department and PPIC department regarding weekly production plan and evaluation of target achievement 8. Sustaining improvement for upgrading service level. Show less 1. Maintaining stock accuracy (physical vs SAP system) 2. Working closely with marketing and sales department regarding receiving and delivery of merchandise goods 3. Receiving and input data of incoming material and outgoing material 4. Conducting weekly and monthly stock taking. 5. Initiating, controlling and monitoring of Housekeeping of warehouse through implementing 5S 6. Reporting weekly and monthly stock position to PPIC and Accounting department. 7. Weekly… Show more 1. Maintaining stock accuracy (physical vs SAP system) 2. Working closely with marketing and sales department regarding receiving and delivery of merchandise goods 3. Receiving and input data of incoming material and outgoing material 4. Conducting weekly and monthly stock taking. 5. Initiating, controlling and monitoring of Housekeeping of warehouse through implementing 5S 6. Reporting weekly and monthly stock position to PPIC and Accounting department. 7. Weekly coordination with production department, engineering department and PPIC department regarding weekly production plan and evaluation of target achievement 8. Sustaining improvement for upgrading service level. Show less
-
-
-
-
PPIC SECTION HEAD
-
Jul 2011 - Feb 2012
1. Setting up and updating monthly Production schedule 2. Managing Material Requirement Planning and raise purchase request to Purchasing Department 3. Updating Incoming Material Status and follow up further with purchasing department 4. Evaluating daily, weekly and monthly production achievement 5. Analysis of production cost (plan vs actual) 6. Inventory control function 7. Setting up COGM (Cost Of Good Manufacturing) 8. Daily coordination with Production, Maintenance… Show more 1. Setting up and updating monthly Production schedule 2. Managing Material Requirement Planning and raise purchase request to Purchasing Department 3. Updating Incoming Material Status and follow up further with purchasing department 4. Evaluating daily, weekly and monthly production achievement 5. Analysis of production cost (plan vs actual) 6. Inventory control function 7. Setting up COGM (Cost Of Good Manufacturing) 8. Daily coordination with Production, Maintenance, Quality, Purchasing and engineering department regarding daily target achievement.
-
-
Commercial section head of coal mining subdivision
-
Sep 2010 - Jul 2011
1. Preparing logistic and delivery schedule 2. Analysing new contract 3. Coordinating with supplier and operating committee at sight regarding product readiness for delivery 4. Feasibility study of new contract 5. Reporting result of feasibility study and planning 6. Setting up stock policy 7. Updating Cost Of Good Sold (COGS) monthly and annually
-
-
PPIC Section Head
-
Feb 2010 - Aug 2010
1. Setting up and updating monthly Production schedule 2. Managing Material Requirement Planning and raise purchase request to Purchasing Department 3. Updating Incoming Material Status and follow up further with purchasing department 4. Evaluating daily, weekly and monthly production achievement 5. Analysis of production cost (plan vs actual) 6. Inventory control function 7. Setting up COGM (Cost Of Good Manufacturing) 8. Daily coordination with Production, Maintenance… Show more 1. Setting up and updating monthly Production schedule 2. Managing Material Requirement Planning and raise purchase request to Purchasing Department 3. Updating Incoming Material Status and follow up further with purchasing department 4. Evaluating daily, weekly and monthly production achievement 5. Analysis of production cost (plan vs actual) 6. Inventory control function 7. Setting up COGM (Cost Of Good Manufacturing) 8. Daily coordination with Production, Maintenance, Quality, Purchasing and engineering department regarding daily target achievement.
-
-
Production Section Head
-
Mar 2007 - Feb 2010
1. Executing Production target as scheduled by PPIC 2. Confirming production result are well recorded and reported to all related department 3. Coordinating with foreman regarding target achievement and solving problem at sight 4. Planning for human resource demand for executing target 5. Reassuring that daily production report is well maintained 6. Confirming to foreman that 5 S and QSHE has been done correctly 7. Reassuring implementation of Step 1 of Total Productive… Show more 1. Executing Production target as scheduled by PPIC 2. Confirming production result are well recorded and reported to all related department 3. Coordinating with foreman regarding target achievement and solving problem at sight 4. Planning for human resource demand for executing target 5. Reassuring that daily production report is well maintained 6. Confirming to foreman that 5 S and QSHE has been done correctly 7. Reassuring implementation of Step 1 of Total Productive Maintenance (TPM) 8. Improving work methods to raise up productivity as well as maintaining quality acceptence level
-
-
PPIC Section Head of Plastic Injection, Pressing and Painting Business Unit
-
Mar 2006 - Mar 2007
1. Setting up and updating monthly Production schedule 2. Managing Material Requirement Planning and raise purchase request to Purchasing Department 3. Updating Incoming Material Status and follow up further with purchasing department 4. Evaluating daily, weekly and monthly production achievement 5. Analysis of production cost (plan vs actual) 6. Inventory control function 7. Setting up COGM (Cost Of Good Manufacturing) 8. Daily coordination with Production, Maintenance… Show more 1. Setting up and updating monthly Production schedule 2. Managing Material Requirement Planning and raise purchase request to Purchasing Department 3. Updating Incoming Material Status and follow up further with purchasing department 4. Evaluating daily, weekly and monthly production achievement 5. Analysis of production cost (plan vs actual) 6. Inventory control function 7. Setting up COGM (Cost Of Good Manufacturing) 8. Daily coordination with Production, Maintenance, Quality, Purchasing and engineering department regarding daily target achievement.
-
-
Quality Assurance Staff of Metal Business Unit
-
May 2005 - Mar 2006
1. Analyzing and updating quality achievement by using statistical methodes 2. Updating Balance scorecard of business unit 3. Auditing process as prescribed by ISO TS 16949 4. Verification and follow up of audit result 5. Facilitator of Quality Control Circle (QCC)
-
-
Quality Management System Staff
-
Mar 2004 - May 2005
1. Auditing business process of each busniess unit existed int PT wijaya karya intrade as prescribed by ISO 9001 : 2000 2. Follow up and verifying of audit result 3. Monthly update of balace scorecard in corporate scope 4. Steering committee of QCC
-
-
-
PT. KMK Global Sports
-
Indonesia
-
Sporting Goods Manufacturing
-
200 - 300 Employee
-
PPIC Supervisor
-
Mar 2003 - Mar 2004
1. Calculating for supporting tool demand (Dies, Jig and fixtures) 2. Scheduling for supporting tool readiness 3. Inventory control of supporting tool 4. Coordinating with purchasing department regarding additional tools for old model as well as new model
-
-
Industrial Engineering Staff
-
Nov 2001 - Mar 2003
-Analysing production process -Motion and time study of each process and standardizing it - Improvement for upgrading capacity
-
-
-
-
PPIC Head
-
Jul 2001 - Nov 2001
-Setting up Production schedule -Material Requirement Planning -Evaluating daily, weekly and monthly production -Inventory control of warehouse activity - Daily coordination with Production, Maintenance, Quality, and engineering department regarding daily target achievement. -Setting up Production schedule -Material Requirement Planning -Evaluating daily, weekly and monthly production -Inventory control of warehouse activity - Daily coordination with Production, Maintenance, Quality, and engineering department regarding daily target achievement.
-
-
Education
-
Universitas Indonesia (UI)
Master, Industrial Engineering -
Universitas Islam Indonesia
Bachelor (S1), Industrial engineering -
CCF/IFI
-
SMA 3 semarang
A1 PHYSICS -
SMP Domenico Savio
Community
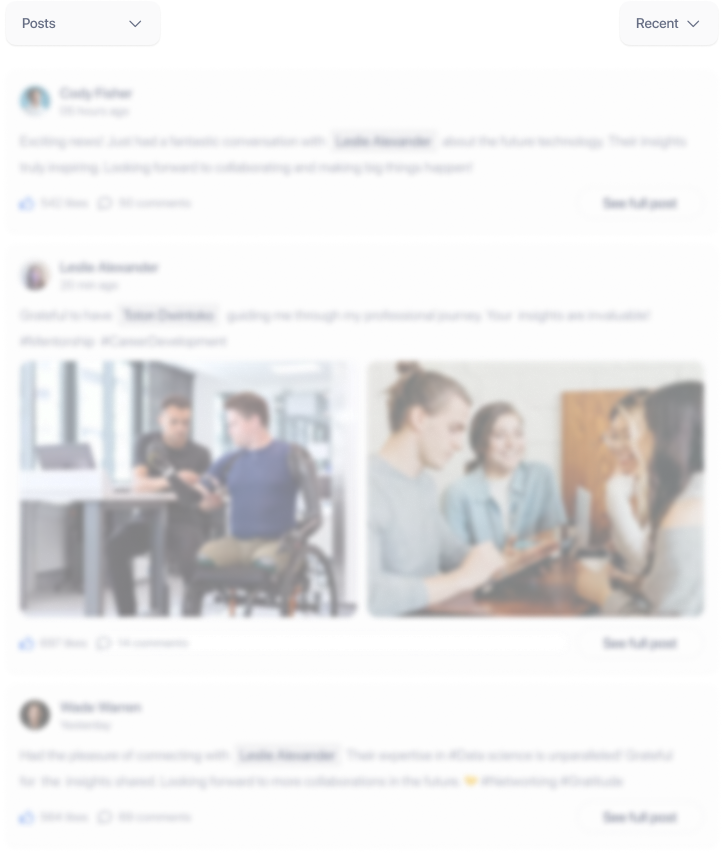