Rick Geissler
FlowTherm Systems- Vice President of Operations at California Hydronics Corporation at CHC Hydro- Claim this Profile
Click to upgrade to our gold package
for the full feature experience.
Topline Score
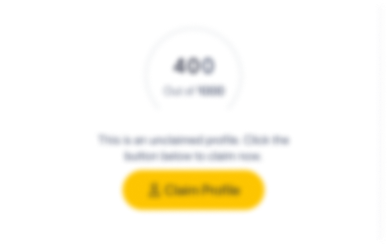
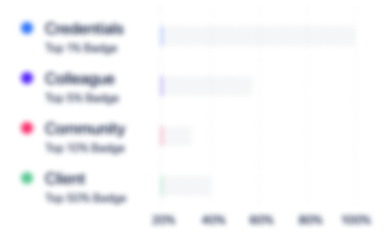
Bio


Experience
-
CHC Hydro
-
United States
-
Construction
-
1 - 100 Employee
-
FlowTherm Systems- Vice President of Operations at California Hydronics Corporation
-
Feb 2021 - Present
- Developed and deployed Company Safety Program: near miss/injury & loss time prevention along with scheduled safety audits and monthly Safety Steering Team Meetings. - Operational responsibility for complete ETO (Engineer to Order) FlowTherm Division Mechanical, Plumbing and HeatTransfer packaged skids and pressure booster for all Hydronic applications. - Responsible for Multi site Division Goals/Objectives: Profit & Loss, Planning, SIOP/Forecasting, Supply Chain improvements, Strategic Initiatives and funded facility expansion efforts. - Developed Business Case and ROI to accomplish an Industrial UL508a Certified Panel Shop: insourced ETO (Engineer to Order) Control Panel Manufacturing with a 1-year ROI. - Established Divisional metrics/dashboards: defined and deployed all Division “critical to business” metrics for hour-by-hour performance reporting including Monthly Operations Reviews. - Aligned Sales targets for YOY (Year Over Year) 10% compounded growth: Improved Sales & Marketing Strategy to enable Division YOY Performance targets. - Developed Division National Sales Strategy and staffing to expand regional territory Customer base. - Manage Division full-service equipment installation, commission, seismic performance testing and applicable Customer start-up support. - Developed and deployed organizational Business Operating System (BOS) in compliance with industry standards/certification requirements. - Measure and Improve Customer Satisfaction with improved Quality and leading indicators. Show less
-
-
-
Honeywell
-
United States
-
Appliances, Electrical, and Electronics Manufacturing
-
700 & Above Employee
-
SR Global Integrated Supply Chain (Operations) Director
-
Aug 2019 - Sep 2020
- Developed and executed Supply Chain strategies to improve footprint rationalization and optimization in these functional areas: Supply Chain Efficiency, Quality Operating System, Continuous Improvement while driving Operational Income to World Class levels. - Managed all aspects of daily Operations for Smart Energy Elster Division: 2025 Employees, $900M annual Revenue - Multi-site locations (20 locations): Americas/EMEA Global network for Gas/Water/Electric Products - Developed Strategic Footprint Capacity with overall Business Case/ROI execution for current and future Capital Investment (Capital Appropriation Request). - Managed monthly S&OP reviews adjusting for both backlog/past due demand and labor efficiency planning. - Developed and drove organizational KPI's/Scorecards to overdrive Operating Income above AOP with emphasis on DLE (Direct Labor Efficiency) and RTY (Rolled Through-put Yield). - Established Global footprint BBP (Best Business Practice) sharing to drive and culture of Continuous Improvement. - Direct Responsibility for NPI (New Product Introductions) across all Regions including launch metrics to confirm product launch success. Show less
-
-
-
Johnson Controls
-
Ireland
-
Industrial Machinery Manufacturing
-
700 & Above Employee
-
SR Director of Operations- Air Systems Components & Koch Filter Manufacturing
-
Feb 2016 - Aug 2019
- Managed all aspects of Daily Operations for Air Systems Components and Koch Filter Manufacturing. - Direct Responsibility for NPI (New Product Introductions) across multiple Product Brands including PDP (Product Development Process) adherence and accountability. - Drove and accomplish Continuous Improvement efforts in all aspects of daily Manufacturing: Safety/Customer/Quality/Delivery/Service/CI and Lean- Responsible for Strategic Footprint analysis and overall Business Case execution. Supported and developed Footprint Strategy/Scope as well as Business Case for all relevant Strategic Initiatives. - Ensured Program Management Tools are an integral part of Business Planning and Execution. - Drove ASC/Koch Filter Organizational KPI's/Scorecards to deliver Yr. over Yr. performance improvements with emphasis of key stretch targets.- Instituted daily/monthly Operations Reporting to drive and deliver BBP (Best Business Practice). - Deployed and managed Business Best Practice sharing deployment across all Air Systems/Koch Filter Manufacturing locations to create and deliver World Class Manufacturing environment. Show less
-
-
Senior Director of Global Operations-Air Handling Units Division
-
Apr 1996 - Aug 2019
Senior Ops Leader for Air Handling Units for Building Efficiency Division. Manage all aspects of Daily Global Operations including P&L responsibility. Develop and drive strategic footprint analysis and business case execution within the AHU Division. Deliver BBP (Best Business Practice) sharing across all Air Handling Unit Manufacturing locations to create and deliver in a World Class Manufacturing environment. Establish and deliver "Better than Market" industry lead times and Customer Satisfaction across Customer Portfolio. Direct Responsibility for NPI (New Product Introductions) across multiple Product Brands including PDP (Product Development Process) adherence and accountability. Drive and accomplish Continuous Improvement efforts in all aspects of daily manufacturing: Safety/Customer/Quality/Delivery/Service/CI and Lean. Roles include:- Director of Operations - Air Systems Components & Koch Filter Manufacturing, Feb 2016 - Feb 2017- Director of Programs - Air System Components & Koch Filter Manufacturing, Feb 2015 - Jan 2016- Director of Continuous Improvement North America, Feb 2011 - Feb 2015 - Building Efficiency - GWS Business Development Manager, April 2008- Feb 2011- Director of Manufacturing Utilization Improvement: Metals and Mechanisms, Mar 2007 - April 2008- Plant Manager, Jan 2003 - Feb 2007- Launch Manager, Quality Manager, Materials Manager, Apr 1996 - Dec 2002 Show less
-
-
Director of Programs-Air Systems Components & Koch Filter Manufacturing
-
Mar 2015 - Jan 2016
- Manage comprehensive monthly Program Review Process for all Air Systems Division: emphasis on execution of Monarch Phase 2 Strategy and High Impact Projects (Koch Filters, TAO, Chilled Beam Product Launch etc.). - Assume full Program responsibility for Air Systems PMO:- Establish Strategy and Scope of assigned projects: Monarch/Key Project Initiatives and other Brand Footprint Initiatives.- Distribute and assign Program Management Tools: deploy and support both pitching and catching plants for all "high impact" Projects.- Establish applied KPI's/Scorecards for all "high Impact" projects assigned to directly measure performance vs targets.- Compile TGR/TGW for all applicable projects post measure phase and incorporate Lessons Learned methodology across future projects.- Institute Launch Readiness governance and reporting to drive Continuous Improvement efforts. - Support all Air Systems Operational Profit Plan goals and objectives which include gap closure for all established Business Best Practices and Best in Class initiatives. Show less
-
-
Dir of Continuous Improvement NA
-
Feb 2011 - Feb 2015
• Responsible for the Development and Management of Critical Operational Scorecards and Metrics for the BE NA Service Industry. • Assume full responsibility for Continuous Improvement North America Operational planning and budgeting. • Interface with multiple BE Branch Managers in Regional Branch locations to launch and manage BBP and primary metrics. • Create and Deploy BE NA Service Continuous Improvement efforts in 8D, Lean/Process Mapping applications in highly transactional business. • Support Continuous Improvement Measures within the Service Sales and Marketing Information System.• Actively support all BE NA Service Industry Operational Profit Plan goals and objectives which includes gap closure for all established Business Best Practices and Best in Class initiatives. Show less
-
-
Building Efficiency-GWS Business Development Manager
-
Apr 2008 - Feb 2011
• Assume full responsibility for all BE MFG Lines of Businesses Globally. • Responsible for all Commercial Engineering Lab Business Development and project construction activities. • Collaborate with multiple BE Manufacturing facilities Leadership/Plant Managers and the respective Teams to develop Business Case Scenarios/Strategies and costing to support Business Groups core operating goals/objectives. • Support all BE Continuous Improvement efforts as it relates to BE Strategic Footprint. • Manage all forecasting for Sales and Marketing Information System (SMIS) for the BE MFG Business Group. • Support all Facility Services, Energy Optimization and Sustainability Programs for BE Manufacturing LOB. Show less
-
-
Director of Manufacturing Utilization Improvement: Metals and Mechanisms
-
Mar 2007 - Apr 2008
• Assumed full responsibility for directing/managing manufacturing utilization improvement metrics for five Tier II JIT facilities. • Collaborated with facility Plant Managers and Continuous Improvement Managers to develop roadmap initiatives to accomplish BBP objectives. • Perform monthly on-site reviews of manufacturing process and equipment as it relates to continuous improvement.
-
-
Plant Manager, Launch Manager, Quality Manager, Materials Supervisor
-
Apr 1996 - Apr 2008
Responsible for daily JIT(Just-in-Time) Operations in multifaceted Manufacturing Roles.
-
-
Education
-
• EMBA-University of Milwaukee Wisconsin: Sheldon B. Lubar School of Business
EMBA, Business Administration and Management, General -
• University of River Falls Wisconsin
Community
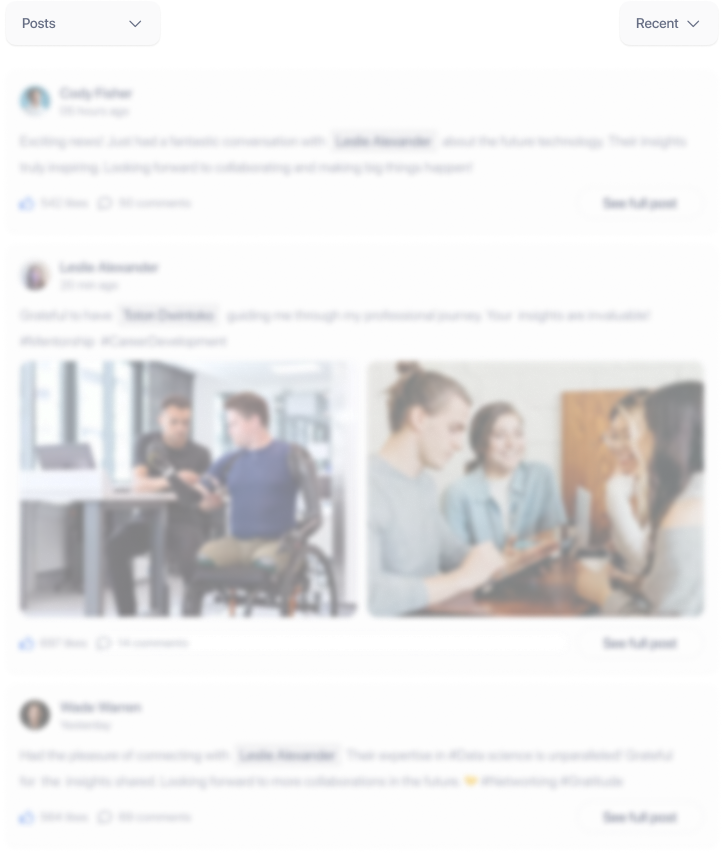