Rick Fleming
Vice President of Operations at Irish Boat Shop, Inc.- Claim this Profile
Click to upgrade to our gold package
for the full feature experience.
Topline Score
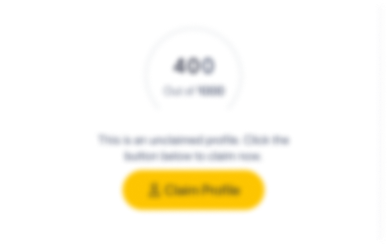
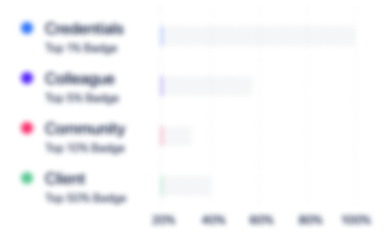
Bio

David Harris
I have known and worked with Rick for the past several years as a fellow Haas Factory Outlet service manager. I have had the opportunity to serve on the Haas service council along with the other service managers nationwide while Rick was chair of this council. I found his organizational skills and knowledge to be next to none. Rick is a terrific manager who is able to get things done and even under the most difficult circumstances. I would highly recommend Rick to any organization that values excellence.

David Harris
I have known and worked with Rick for the past several years as a fellow Haas Factory Outlet service manager. I have had the opportunity to serve on the Haas service council along with the other service managers nationwide while Rick was chair of this council. I found his organizational skills and knowledge to be next to none. Rick is a terrific manager who is able to get things done and even under the most difficult circumstances. I would highly recommend Rick to any organization that values excellence.

David Harris
I have known and worked with Rick for the past several years as a fellow Haas Factory Outlet service manager. I have had the opportunity to serve on the Haas service council along with the other service managers nationwide while Rick was chair of this council. I found his organizational skills and knowledge to be next to none. Rick is a terrific manager who is able to get things done and even under the most difficult circumstances. I would highly recommend Rick to any organization that values excellence.

David Harris
I have known and worked with Rick for the past several years as a fellow Haas Factory Outlet service manager. I have had the opportunity to serve on the Haas service council along with the other service managers nationwide while Rick was chair of this council. I found his organizational skills and knowledge to be next to none. Rick is a terrific manager who is able to get things done and even under the most difficult circumstances. I would highly recommend Rick to any organization that values excellence.

Credentials
-
Allen Bradley, CNC
- -
Brown & Sharpe Mfg. Machine Tool Apprenticeship
- -
Class A Commercial Drivers License CDL
- -
Control Laser, Laser repair
- -
HAAS Automation, Machine Tool Factory Certificate
- -
HAAS Automation, Rotary Products Factory Certificate
- -
Makino, Machining Center Factory Certificate
- -
Private Pilot
-
Experience
-
Irish Boat Shop, Inc.
-
United States
-
Recreational Facilities
-
1 - 100 Employee
-
Vice President of Operations
-
Jun 2019 - Present
-
-
Vice President of Service
-
Mar 2018 - Present
Director of Service, Parts, Training, and OSHA Compliance for 3 locations in Northern Michigan. Fiscal Responsibility for Service Department, Parts Department, Equipment and related Facilities. Shared responsibility for IT, Telephone and technology throughout all locations.• Customer Satisfaction, Vendor Relations, Warranty • Budget, Financial Projections, Financial and Business Analysis• Facilities, IT, Technology and Equipment• Service, Mobile Service, and Parts.
-
-
-
DOC Services Inc.
-
United States
-
Field Services Engineer
-
May 2017 - Mar 2018
Troubleshooting, repair and calibration of automated paint tinting dispensers. Diagnose and repair of electrically operated order pickers and stock-lifting equipment. Repair, maintenance and troubleshooting of personal mobility devices. Troubleshooting and calibration of high volume fluid handling equipment. Diagnose, align and repair of rail guided warehouse stock handling and management system. Repair and calibration of spectrophotometers. • Field Service, Electro Mechanical Service, Automation and Electronics. • BYK-Gardner, X-Rite color spectrophotometers. • Fluid Management, Red Devil and Hero automated paint mixing equipment. • Fluid Management, Corob and Hero paint tinting dispensers.
-
-
-
-
Chief Operating Officer
-
Nov 2010 - May 2017
Executive Director of Machine Tool Service, Applications, Training, and Repair Parts. Director of Operations for Facilities and Commercial Lease Properties. Defined and developed the 3D printing product line to include the training of applications, sales, technical sales, and service. Diverse background allows operation in areas that transition multiple technologies and disciplines providing clarity and direction between multiple trades and levels of management.• Financial responsibility for P&L of Facilities, Service, and Repair Parts. • Directed the expansion, construction, and design, of a new facility.• Experience with 3D Modeling / Printing / Additive Manufacturing.• Introduced and implemented Cloud based mobile scheduling, billing, and inventory management.
-
-
Vice President of Customer Service
-
Jul 2008 - Nov 2010
Vice President of service, parts, applications and training. • Financial responsibility of service, and repair parts department.• Improve machine tool builder / supplier relations.• Direct applications and customer training.• Trade Show planning, sales of preventative maintenance, and contract services.• Award winning Customer service and customer satisfaction.
-
-
-
-
CNC Machine Tool Service Manager
-
Sep 1997 - Jul 2008
Manager of service, parts, applications and training. • Improved the customer service experience by streamlining the process of service scheduling, standardized the installation process, and providing superior telephone support. • Manage repair parts, inventory, and service fleet. • Developed Applications and customer training standards. • Increased Sales of preventative maintenance and contract services. • Service Department operations and financial responsibility. • Improved machine tool builder / supplier relations.
-
-
-
-
CNC Machine Tool Service Manager
-
Nov 1989 - Sep 1997
Working field service manager, in addition to providing applications and training support to customers throughout, Colorado, Utah, New Mexico, Wyoming, Idaho, Nebraska and Montana. • Customer relations, scheduling, consignment parts correspondence and communication with manufactures, applications support. • Trade Show planning, logistics and coordination. • Developed a database to automate the service log, streamline scheduling, and reporting. Working field service manager, in addition to providing applications and training support to customers throughout, Colorado, Utah, New Mexico, Wyoming, Idaho, Nebraska and Montana. • Customer relations, scheduling, consignment parts correspondence and communication with manufactures, applications support. • Trade Show planning, logistics and coordination. • Developed a database to automate the service log, streamline scheduling, and reporting.
-
-
-
Brown & Sharpe
-
Machinery Manufacturing
-
1 - 100 Employee
-
Field Service Engineer
-
Mar 1986 - Nov 1989
Senior member of a management team providing support and service for the entire machine tool product line. Travel both domestic and international in support of customers and distributors of Brown & Sharpe machine tools. • Trouble-Shooting machines by telephone for distributors and customers, international field service, work with engineering for quality control, support rebuild with electrical engineering. • Contributing member of the Brown & Sharpe product quality review board. • Hands on experience with Creep Feed and Conventional Grinding process.
-
-
Education
-
East Coast Aero Technical School Lexington, MA
A&P, Avation -
Community College of Rhode Island
Fortran, Basic, Cobol, Computer Programming
Community
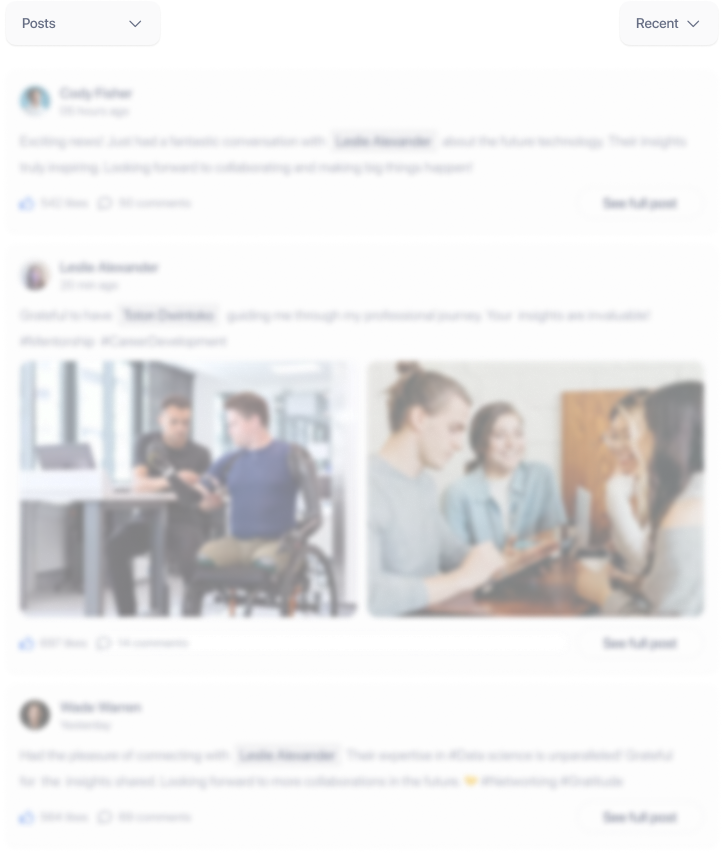