Richard Wattley
Production Shift Supervisor at Therma-Tru Doors- Claim this Profile
Click to upgrade to our gold package
for the full feature experience.
Topline Score
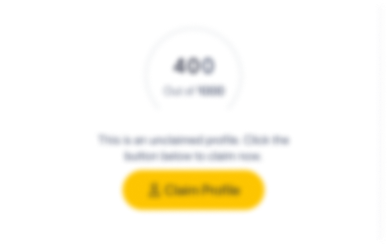
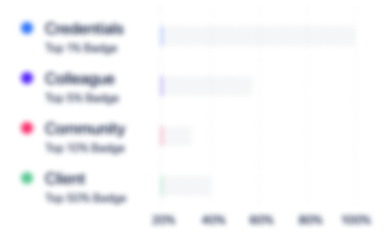
Bio
0
/5.0 / Based on 0 ratingsFilter reviews by:
Experience
-
Therma-Tru Doors
-
United States
-
Wholesale Building Materials
-
500 - 600 Employee
-
Production Shift Supervisor
-
Nov 2014 - Present
• Lead 40-60 individuals along with 3-4 Group Leader in meeting Safety, Quality, and Efficiency objectives • Work collaboratively and build partnerships with various resources and vendors to meet objectives • Select and Develop talent through direct hire interviewing and mentor leadership development initiatives • Plan and prioritize work load in order to meet and align commitments with organizational goals • Manage ambiguity of customer and vendor markets in order to ensure objectives clear for all team members • Utilize a strategic mindset in order to foresee future possibilities and translate them into breakthrough strategies Show less
-
-
-
Guardian Automotive
-
Canada
-
Motor Vehicle Manufacturing
-
Production Shift Supervisor
-
Jan 2014 - Nov 2014
• Supervise a team of 35 individuals in meeting Safety, Quality, Throughput Goals • Coach, Teach, and Develop team members in understanding and demonstration of Standard Work • Daily Review of KPI’s with assigning of Action Items and Work Orders to address deficiencies • Supervise a team of 35 individuals in meeting Safety, Quality, Throughput Goals • Coach, Teach, and Develop team members in understanding and demonstration of Standard Work • Daily Review of KPI’s with assigning of Action Items and Work Orders to address deficiencies
-
-
-
Johnson Controls
-
Ireland
-
Industrial Machinery Manufacturing
-
700 & Above Employee
-
Six Sigma/LEAN Project Manager
-
May 2000 - Jan 2014
• Lead Team Members in Continuously Improving Safety, Quality, & Efficiency Objectives • Identify process improvement opportunities through data collection of key business metrics. • Measure the process for initial performance and provide key process measurable(s) • Analyze key process by identifying and verifying key contributors • Implement validated improvements based on Safety, Quality, Productivity, and Cost • Provide Control Plan to maintain process improvements, Establish Standard Work Instructions • Mentor Green Belts in Six Sigma Tools and Project Completion • Establish LEAN philosophy within key process environments through • Value Stream Mapping, Kaizen, Quick Changeover, Implementation of 6S and Kanban • Audit Process under QS9000 and TS16949 Standards Show less
-
-
Community
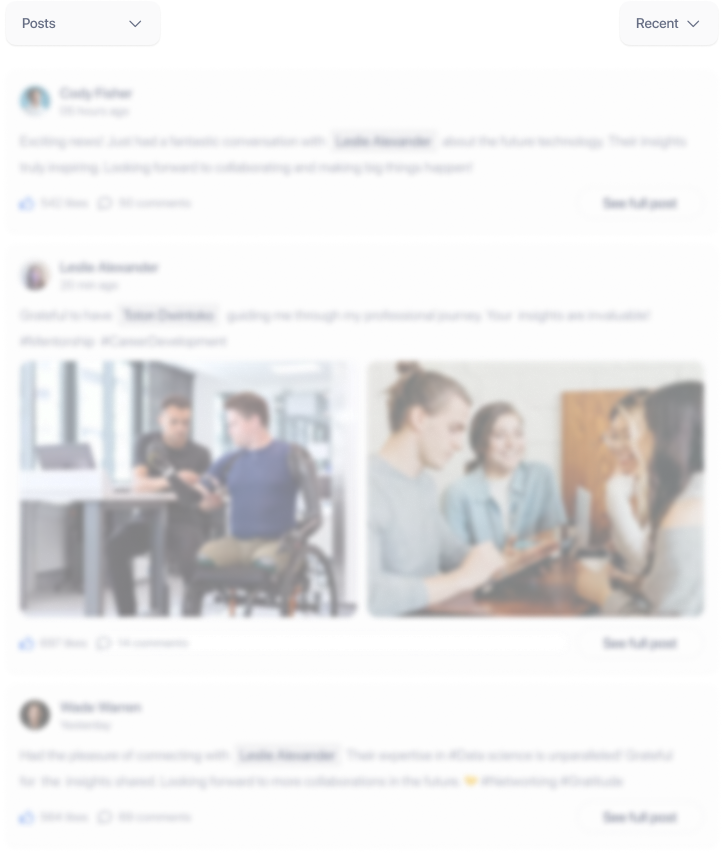