Richard Waddell
Process Engineer at Currently looking for my next opportunity- Claim this Profile
Click to upgrade to our gold package
for the full feature experience.
Topline Score
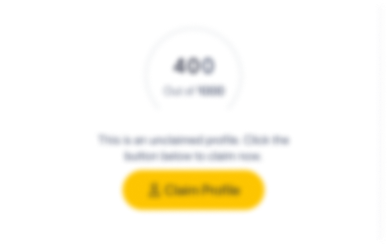
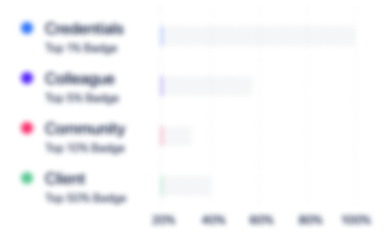
Bio

James Fountas
I had the pleasure of working with Richard at Millipore in the Systems and Solutions group. Richard was the Quality Engineer and I worked on the electrical side. While you may work with a large number people in a large company, very few of them actively work with you and support you. I relied on Richard on multiple occasions to get me familiar with issues. Richard was always helpful and informative. He worked hard to make himself available. When he said that he would look into something, he would and I would get feedback typically within a day. Thank you for all your hard work Richard.

Doug Bruce
I had the pleasure of working directly with Richard on a regular basis while he was at Life Technologies / Thermo Fisher. We worked closely on many sustaining engineering, validation and scale-up projects. Richard has a great sense of teamwork and does a very good job of driving a team to complete the required tasks in a timely, yet professional manner. In one case, Richard and I worked to troubleshoot a persistent quality problem that we believed to be equipment related. Richard and his team discovered that it was actually a vendor issue and his efforts ultimately lead to a change of supplier. He was instrumental in discovering the issue and he drove the supplier change including drafting and executing the required validations. I would highly recommend Richard. His skills, knowledge and experience will be an asset to any company.

James Fountas
I had the pleasure of working with Richard at Millipore in the Systems and Solutions group. Richard was the Quality Engineer and I worked on the electrical side. While you may work with a large number people in a large company, very few of them actively work with you and support you. I relied on Richard on multiple occasions to get me familiar with issues. Richard was always helpful and informative. He worked hard to make himself available. When he said that he would look into something, he would and I would get feedback typically within a day. Thank you for all your hard work Richard.

Doug Bruce
I had the pleasure of working directly with Richard on a regular basis while he was at Life Technologies / Thermo Fisher. We worked closely on many sustaining engineering, validation and scale-up projects. Richard has a great sense of teamwork and does a very good job of driving a team to complete the required tasks in a timely, yet professional manner. In one case, Richard and I worked to troubleshoot a persistent quality problem that we believed to be equipment related. Richard and his team discovered that it was actually a vendor issue and his efforts ultimately lead to a change of supplier. He was instrumental in discovering the issue and he drove the supplier change including drafting and executing the required validations. I would highly recommend Richard. His skills, knowledge and experience will be an asset to any company.

James Fountas
I had the pleasure of working with Richard at Millipore in the Systems and Solutions group. Richard was the Quality Engineer and I worked on the electrical side. While you may work with a large number people in a large company, very few of them actively work with you and support you. I relied on Richard on multiple occasions to get me familiar with issues. Richard was always helpful and informative. He worked hard to make himself available. When he said that he would look into something, he would and I would get feedback typically within a day. Thank you for all your hard work Richard.

Doug Bruce
I had the pleasure of working directly with Richard on a regular basis while he was at Life Technologies / Thermo Fisher. We worked closely on many sustaining engineering, validation and scale-up projects. Richard has a great sense of teamwork and does a very good job of driving a team to complete the required tasks in a timely, yet professional manner. In one case, Richard and I worked to troubleshoot a persistent quality problem that we believed to be equipment related. Richard and his team discovered that it was actually a vendor issue and his efforts ultimately lead to a change of supplier. He was instrumental in discovering the issue and he drove the supplier change including drafting and executing the required validations. I would highly recommend Richard. His skills, knowledge and experience will be an asset to any company.

James Fountas
I had the pleasure of working with Richard at Millipore in the Systems and Solutions group. Richard was the Quality Engineer and I worked on the electrical side. While you may work with a large number people in a large company, very few of them actively work with you and support you. I relied on Richard on multiple occasions to get me familiar with issues. Richard was always helpful and informative. He worked hard to make himself available. When he said that he would look into something, he would and I would get feedback typically within a day. Thank you for all your hard work Richard.

Doug Bruce
I had the pleasure of working directly with Richard on a regular basis while he was at Life Technologies / Thermo Fisher. We worked closely on many sustaining engineering, validation and scale-up projects. Richard has a great sense of teamwork and does a very good job of driving a team to complete the required tasks in a timely, yet professional manner. In one case, Richard and I worked to troubleshoot a persistent quality problem that we believed to be equipment related. Richard and his team discovered that it was actually a vendor issue and his efforts ultimately lead to a change of supplier. He was instrumental in discovering the issue and he drove the supplier change including drafting and executing the required validations. I would highly recommend Richard. His skills, knowledge and experience will be an asset to any company.

Experience
-
Currently looking for my next opportunity
-
Motor Vehicle Manufacturing
-
1 - 100 Employee
-
Process Engineer
-
Jan 2023 - Present
-
-
-
TAKEDA PHARMACEUTICALS AMERICA, INC.
-
United States
-
Pharmaceutical Manufacturing
-
1 - 100 Employee
-
Data Engineer
-
Jun 2021 - Feb 2023
-
-
-
Columbia Tech
-
Appliances, Electrical, and Electronics Manufacturing
-
200 - 300 Employee
-
Quality Engineer
-
Jan 2020 - Jun 2021
• Responsible for all quality aspects for the release of Amazon Robotics products • Lead the Material Review Board (MRB) for disposition of non-conforming materials • Quality Engineer for the manufacture of the guidance system for Amazon Scout – the Autonomous Robotic Delivery System • Led Brainstorming sessions to process and document deviations from Amazon Robotics • Train quality engineers, quality inspectors, and manufacturing operators on procedures, processes, and inspection points • Documented the “Material Approval Process (MAP), which helped to manage the New Product Introduction from AR • Work on Corrective Actions / Preventative Actions (CAPAs) both internally and from AR • Joined the organizations Toastmasters group to practice and improve my public speaking capabilities • Write Quality Assurance Forms (QAF) to document inspection processes
-
-
-
MilliporeSigma
-
United States
-
Biotechnology Research
-
700 & Above Employee
-
Quality Engineer
-
Oct 2016 - Jan 2020
• Responsible for all quality aspects for the release of custom engineered pharmaceutical equipment • Custom engineered pharmaceutical equipment includes Bioreactors, Tangential Flow Filtration equipment (TFF), Mixers, and Chromatography Equipment • Work with clients to write Installation Qualification (IQ) and Operational Qualification (OQ) procedures for new equipment, including bioreactors and Tangential Flow Filtration equipment • Manage investigations into complaints – work closely with suppliers to resolve customer issues, Including the implementation of Corrective Actions / Preventative Actions (CAPA) • Supplier Quality Engineer for five major North American suppliers • Compile monthly metrics for the North American group, including First Pass Yield, Complaints, and FAT Survey Data • Project Manager for the ISO 9001:2015 Implementation for the S&S group in Billerica in 2018 * Ensure all processes are documented and controlled (ManGo) * Perform internal audits on project managers * Ensure projects managers understand the Quality Management System (QMS) Including: Training requirements, job descriptions, controlled documents * Received ISO 9001:2015 certification in December, 2018
-
-
-
DPS Group Global
-
Ireland
-
Architecture and Planning
-
700 & Above Employee
-
Senior Process Engineer
-
Nov 2015 - Jul 2016
• Responsible for the design of new Pharmaceutical Systems, and upgrades to existing facilities • Responsible for the design of bioreactors, pumps, process piping, and heat exchangers • Complete calculations for all process equipment, including pressure relief valves, heat exchangers, and process pumps • Responsible for the design of new Pharmaceutical Systems, and upgrades to existing facilities • Responsible for the design of bioreactors, pumps, process piping, and heat exchangers • Complete calculations for all process equipment, including pressure relief valves, heat exchangers, and process pumps
-
-
-
Life Technologies
-
United States
-
Biotechnology Research
-
700 & Above Employee
-
Scale Up Engineer
-
Feb 2014 - Nov 2015
Responsible for the scale-up activities for three product lines: 1) POROS resin beads 2) POP polymers 3) Tropix chemiluminescence products An ISO 9001 and ISO 13485 registered manufacturing facility • Validated new Protein A source – Completed Process Qualification for new Protein A. This material is coupled to existing POROS resin • Collaborated with Research & Development, Manufacturing, and Quality for the process optimization for new Protein A • Conduct Process Hazard Analyses (PHA) for new products and processes • Completed Installation Qualification (IQ), Operation Qualification (OQ), and Process Qualification (PQ) for the Scale up of Tropix CDP-Star products • Completed Cleaning Validations for the scale up of new processes • Lead investigations into Problem Records (PR’s) and customer complaints • Participate in Six Sigma events, including: Value Stream Mapping, Kaizens, Failure Mode Effects Analysis (FMEAs) and Design of Experiments (DOEs)
-
-
-
Merck Life Science
-
Germany
-
Biotechnology Research
-
700 & Above Employee
-
Process Engineer
-
May 2011 - Feb 2014
Process Engineer – Bedford Membrane Manufacturing Technical Organization An ISO 9001 registered manufacturing facility • Responsible for all aspects of the polyvinylidene difluoride (PVDF) and polyethersulfone (PES) membrane manufacturing processes, including troubleshooting issues and all documentation • Complete IQ’s, OQ’s, PQ’s for membranes and membrane applications • Qualify new raw materials and products in the manufacturing process • Auditor for both internal (process) and external (supplier) audits • Lead Green Belt projects utilizing many Black Belt tools including Gage R&R, and Root Cause Analysis (RCA) using Fishbone Analysis and “Is / Is Not” Analysis • Black Belt certification in process: Completed 2 weeks of Black Belt classroom training; mentored both Blue Belt and Green Belt Projects; Black Belt project to reduce visual defects in membranes
-
-
-
Entegris
-
United States
-
Semiconductor Manufacturing
-
700 & Above Employee
-
Senior Quality Engineer
-
Aug 2009 - Oct 2011
• Investigate customer complaints, implement corrective actions, and write 8D reports • Responsible for the polyethylene membrane process; deal with process, product, and customer issues • Conduct audits of raw material vendors, and get audited on process related to UPE membrane • Investigate customer complaints, implement corrective actions, and write 8D reports • Responsible for the polyethylene membrane process; deal with process, product, and customer issues • Conduct audits of raw material vendors, and get audited on process related to UPE membrane
-
-
-
Rohm and Haas Electronic Materials
-
Semiconductor Manufacturing
-
100 - 200 Employee
-
R&D Scale Up Product Team Leader
-
Aug 2008 - Aug 2009
An ISO 9001 registered manufacturing facility • Manage three direct reports in the production of sample products for customer testing • Responsible for production of 4 main product groups: 193, 248 and i-line Photoresists; and Anti-Reflective Coatings (ARCs) • Manage New Product Development through the Model Shop manufacturing process. This includes generating paperwork, scheduling, material movements, testing, and shipment to customer An ISO 9001 registered manufacturing facility • Manage three direct reports in the production of sample products for customer testing • Responsible for production of 4 main product groups: 193, 248 and i-line Photoresists; and Anti-Reflective Coatings (ARCs) • Manage New Product Development through the Model Shop manufacturing process. This includes generating paperwork, scheduling, material movements, testing, and shipment to customer
-
-
-
Rohm and Haas
-
Chemical Manufacturing
-
400 - 500 Employee
-
R&D scale up engineer
-
May 2007 - Aug 2009
• Responsible for troubleshooting customer quality issues related to relevant product lines. This includes setting up meetings, teams, testing, reports, and closing of the issue with the customers • Synthesize, Precipitate, and Characterize acrylate polymers for use in Anti Reflective Coatings • Completed 6 Sigma training class, part of the Green Belt Certification • Use many 6 Sigma tools on an almost daily basis, including: Gauge R&R, DOE, FMEA, and MSAs • Responsible for troubleshooting customer quality issues related to relevant product lines. This includes setting up meetings, teams, testing, reports, and closing of the issue with the customers • Synthesize, Precipitate, and Characterize acrylate polymers for use in Anti Reflective Coatings • Completed 6 Sigma training class, part of the Green Belt Certification • Use many 6 Sigma tools on an almost daily basis, including: Gauge R&R, DOE, FMEA, and MSAs
-
-
-
SAP
-
Germany
-
Software Development
-
700 & Above Employee
-
Implementation Consultant
-
1999 - 2000
-
-
-
-
Process Engineer
-
1995 - 1999
-
-
-
-
Process Engineer
-
1993 - 1994
-
-
-
United States Air Force
-
United States
-
Defense and Space Manufacturing
-
700 & Above Employee
-
Airman
-
1984 - 1988
-
-
Education
-
Babson F.W. Olin Graduate School of Business
MBA, Entrepreneurship -
Worcester Polytechnic Institute
B.S., Chemical Engineering
Community
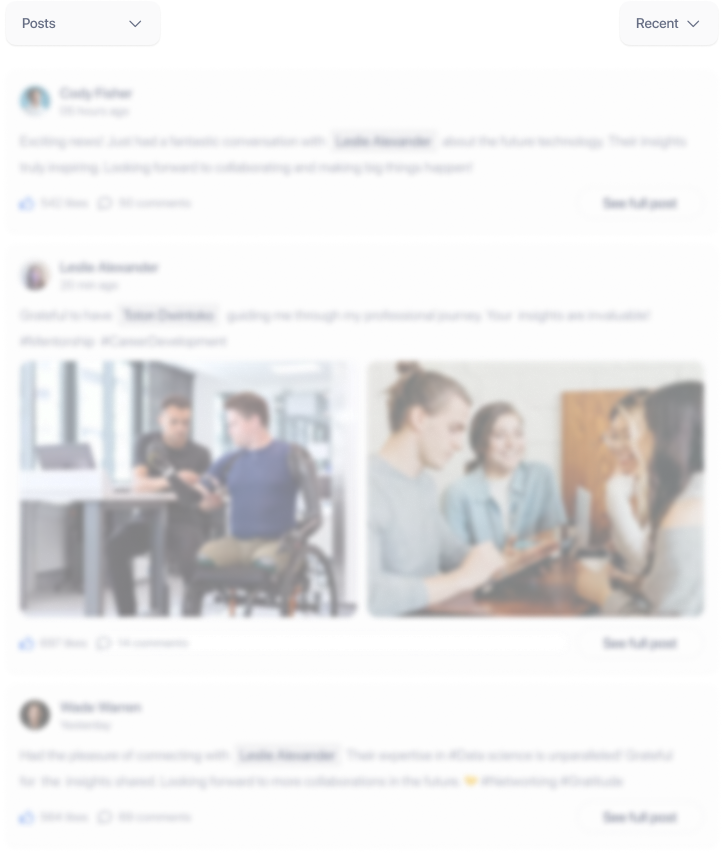