Richard MacDonald
Validation Engineer at ProPharma Group- Claim this Profile
Click to upgrade to our gold package
for the full feature experience.
Topline Score
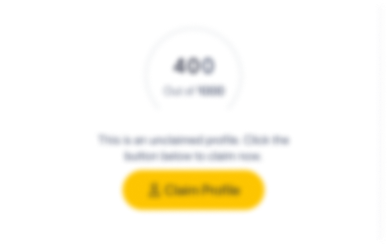
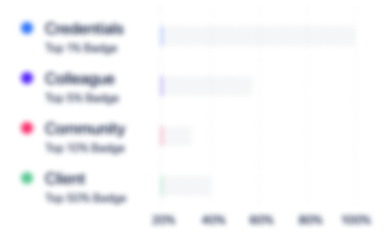
Bio


Experience
-
ProPharma
-
United States
-
Business Consulting and Services
-
700 & Above Employee
-
Validation Engineer
-
Dec 2016 - Apr 2017
Performing vadilation activities Performing vadilation activities
-
-
-
Validant
-
United States
-
Business Consulting and Services
-
100 - 200 Employee
-
Validation Engineer
-
Jan 2016 - Jul 2016
Process improvement focusing on autoclave sterilization. Projects include work with vendors to fabricate new autoclave carts, design and fabricate new dry heat oven carts, build sterilization boxes for machine parts for sterilization. Upgrade and replace parts washing sink, create new labels for ID of parts for sterilization. Update SOP's and forms used in preparation of machine parts for sterilization.
-
-
Validation Engineer
-
Jul 2014 - Dec 2015
Process improvement focusing on autoclave sterilization. Projects include work with vendors to fabricate new autoclave carts, design and fabricate new dry heat oven carts, build sterilization boxes for machine parts for sterilization. Upgrade and replace parts washing sink, create new labels for ID of parts for sterilization. Update SOP's and forms used in preparation of machine parts for sterilization.
-
-
-
ProPharma
-
United States
-
Business Consulting and Services
-
700 & Above Employee
-
Validation Engineer
-
Mar 2014 - Jun 2014
Currently contracted to Bayer Crop Science in Kansas City, Mo. Performing duties related to Quality Assurance for the installation of equipment. Currently contracted to Bayer Crop Science in Kansas City, Mo. Performing duties related to Quality Assurance for the installation of equipment.
-
-
-
ProPharma
-
United States
-
Business Consulting and Services
-
700 & Above Employee
-
Validation Engineer
-
Oct 2012 - Jan 2014
Write and execute protocols for temperature mapping in -80˚C freezers, autoclaves, depyrogenation oven, incubators, coolers, and freeze dryers. Protocols also included re-qualification studies with BI’s and temperature probes executing half cycles. Equipment for testing included Kaye Validator and Val Probes. Execution of IQ/OQ protocols for autoclave, dry heat oven, and filling line. Write and execute protocols for temperature mapping in -80˚C freezers, autoclaves, depyrogenation oven, incubators, coolers, and freeze dryers. Protocols also included re-qualification studies with BI’s and temperature probes executing half cycles. Equipment for testing included Kaye Validator and Val Probes. Execution of IQ/OQ protocols for autoclave, dry heat oven, and filling line.
-
-
-
Novartis
-
Suffern, NY
-
Validation Engineer
-
Feb 2012 - Oct 2012
Perform periodic equipment validation status reviews. Perform periodic equipment validation status reviews.
-
-
-
ProPharma
-
United States
-
Business Consulting and Services
-
700 & Above Employee
-
Vailidation Engineer
-
Aug 2011 - Dec 2011
Performing validation activites for drug product transfer. Performing validation activites for drug product transfer.
-
-
-
ProPharma
-
United States
-
Business Consulting and Services
-
700 & Above Employee
-
Validation Engineer
-
Sep 2010 - Jun 2011
Working in St Joseph, MO at Boehringer-Ingelheim Vetmedica, Inc as a sub-contractor. Involved with execution of IQ/OQ for installation of autoclaves, parts washers, CIP skid, Steam generator, High speed filling line, and RO system.
-
-
Process Validation Technologist
-
Jun 2010 - Aug 2010
Execution of Protocol for validation of new equipment at King Pharmaceuticals in Madison, WI.
-
-
-
Novartis
-
Switzerland
-
Pharmaceutical Manufacturing
-
700 & Above Employee
-
Process Technologist
-
Jul 2009 - Feb 2010
In the first 6 months at Novartis I was in Europe for 90 days doing a technology transfer of a drug for commercial sale with a Pharmaceutical company in Slovenia. Then to Holly Springs, NC working in the Technology Development Group performing valdation to bring a new syringe line into production. In the first 6 months at Novartis I was in Europe for 90 days doing a technology transfer of a drug for commercial sale with a Pharmaceutical company in Slovenia. Then to Holly Springs, NC working in the Technology Development Group performing valdation to bring a new syringe line into production.
-
-
-
Pfizer
-
United States
-
Pharmaceutical Manufacturing
-
700 & Above Employee
-
Senior Process Technologist
-
2006 - 2008
Responsible for equipment improvement projects and cost reduction for production processes. Participate on method one teams to investigate unusual incidents. Work on teams to bring new products and equipment into production. Work across units and areas to assist with solving equipment and process problems. Design specs with vendors, visit vendor for print review. Provide leadership for the installation of a parts washer including IQ/OQ and P/Q and give assistance on an installation of an… Show more Responsible for equipment improvement projects and cost reduction for production processes. Participate on method one teams to investigate unusual incidents. Work on teams to bring new products and equipment into production. Work across units and areas to assist with solving equipment and process problems. Design specs with vendors, visit vendor for print review. Provide leadership for the installation of a parts washer including IQ/OQ and P/Q and give assistance on an installation of an autoclave. Participate on a team for the development of a sterile production area. Focusing on installation of a parts washer, steam sterilizer, and steam stopper sterilizer. Also FAT, I/Q, O/Q and P/Q of parts washer. Supervising the day-to-day operations for 15 employees in Sterile Prep Area. Trained in the Deviation Reporting System which included root cause analysis. Review, update, and revise SOP’s, and batch records. Coordinate activities with other units for autoclaving; stopper processing, tray washing and sterilizing, and processing items for entry into the aseptic area. Attend project meetings for Autoclave, Stopper Processor, Dry Heat Ovens, and miscellaneous projects in Sterile Prep. Certified for entrance into the Aseptic processing area (APA).
-
-
Supervisor/Team Leader
-
Aug 1987 - Dec 2006
Directly supervised a staff of twelve. Responsible for following FDA guidelines and cGMPs. Participating with team concepts, team leaders, coaches, and a flexible work force. Interviewing new employees. Reviewing production records. Training workers allowing them to work more efficiently in the production area. Setting up filling lines and monitoring production. Responsible for process improvement projects. Operating computers with production lines to monitor production processes and… Show more Directly supervised a staff of twelve. Responsible for following FDA guidelines and cGMPs. Participating with team concepts, team leaders, coaches, and a flexible work force. Interviewing new employees. Reviewing production records. Training workers allowing them to work more efficiently in the production area. Setting up filling lines and monitoring production. Responsible for process improvement projects. Operating computers with production lines to monitor production processes and generate reports. Receiving “Distinguished Service Award” for process improvement two years in a row. Involved with a team to develop an operations tracking system for downtime and defects.
-
-
Education
-
University of Phoenix
BSBM, Management
Community
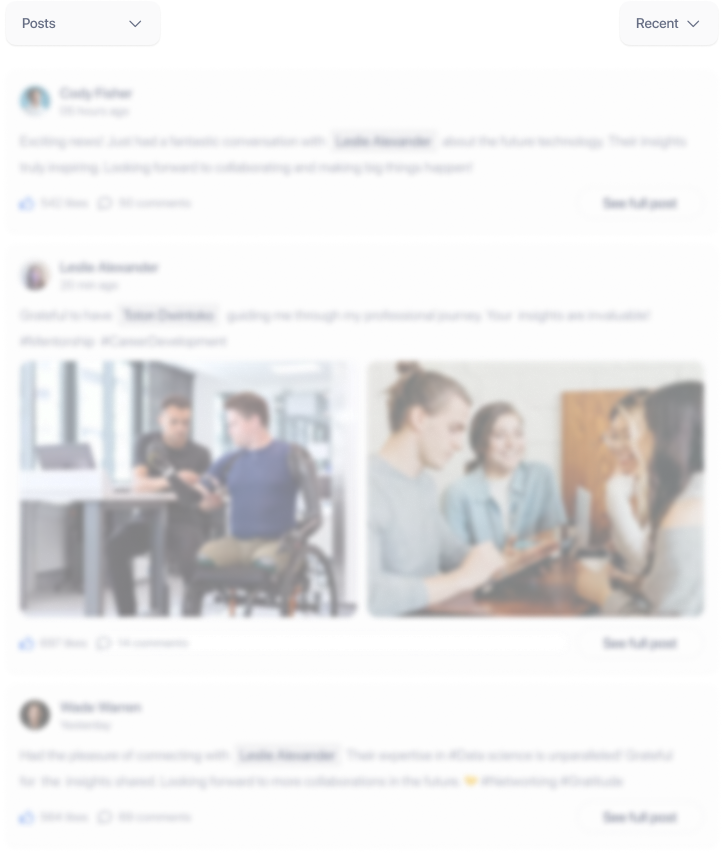