Rich Rendleman
Senior Manager Quality Assurance at Kia Motors Manufacturing Georgia, Inc.- Claim this Profile
Click to upgrade to our gold package
for the full feature experience.
Topline Score
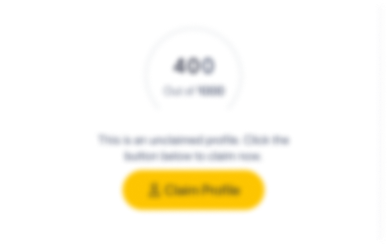
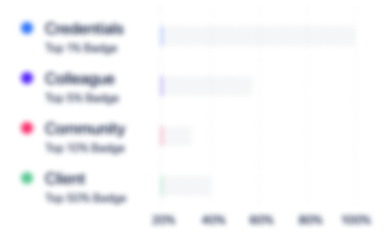
Bio


Experience
-
Kia Georgia, Inc.
-
Motor Vehicle Manufacturing
-
700 & Above Employee
-
Senior Manager Quality Assurance
-
Jan 2020 - Present
• Awarded JD Powers and Associates Awards for vehicles produced at facility.• Manage engineering team of 25 and support root cause investigations, data analysis, emissions testing, equipment calibration, and material testing.• Lead internal Cost Reduction CFT for the Quality Division by collaborating with the operational teams to coordinate cost reduction strategies, resulting in cost savings of more than $2.5M.• Empower employees showcasing relationship building and leadership development, resulting in promotions for 12 people. • Collaborate with Production and Suppliers for cost reduction of 14% over the past two years.• Execute the Quality Assurance group for 3 years with 0 OSHA recordable or lost time accidents.• Manage compliance activities with Kia North American Safety Office and NHTSA. • Monitor KPI’s and keep executive members informed of the results, actions, and improvements. • Selected to Lead ISO 9001-2015 certification process with 5 years with no major non-conformance findings and implemented and facilitated internal ISO training rather than external training.• Spearhead emissions lab testing activities and submit monthly testing results to HQ and EPA/CARB. • Ensure that all vehicles meet country, regional, and state compliance requirements.• Successfully build teams that embrace and promote diversity. • Complete 12 trips to South Korea for new model or advanced training for job specific skills.• Reduced warranty cost by 5% through software updates and lowering part replacement need. Show less
-
-
Senior Manager-Quality Control
-
Jun 2015 - Present
• Oversee 46 salaried employees including supervisors and specialists and 153 hourly team members. • Increased employee satisfaction and retention by #% through mentoring, providing tools, resource allocation, and training needed for individual and team success. • Assist students with AWIM and STEM activities to help inspire the next generation workforce.• Collaborated with 36 U.S. and overseas suppliers to ensure incoming parts meet quality standards. • Audited and inspected facilities, PFMEA, plant safety, quality systems, and production performance.• Generated and maintained quality control operating budget more than $1,000,000. • Participated in benchmarking trips to BMW Germany, Hyundai/Kia plants in the Czech Republic, Slovakia, Mexico, and South Korea. Additionally, lead trips to Hyundai/Kia Research and Development Center in South Korea to assist engineers with new model development Show less
-
-
Manager Quality Control-Weld/Paint/Stamping
-
Nov 2013 - Jun 2015
• Launched 3D white light inspection system to complement CMM measurement activities.• Trained 72 staff members on containment and yard sort procedures to prevent customer concerns.• Improved team member inspection environment by introducing high-intensity LED lighting and adjusting height of inspection deck to be in line with customer view to improve detection of concerns.
-
-
Assistant Manager Quality Control-Weld/Paint/Stamping
-
Apr 2013 - Nov 2013
• Created training plan to include job knowledge survey and vehicle standards.• Implemented new model pilot team to assist with model launch activities
-
-
Assistant Manager Quality Control-General Assembly
-
Mar 2011 - Mar 2013
• Updated inspection processes to align with customers' expectations.• Implemented new model pilot team to assist with model launch activities
-
-
Group Leader Quality Control-General Assembly
-
Jul 2010 - Mar 2011
• Expanded QC organization from 1 shift to 3 shifts.• Implemented double-check process to accommodate the introduction of two new models.
-
-
-
Mitsubishi Motors North America, Inc.
-
United States
-
Retail
-
300 - 400 Employee
-
Group Leader Quality Control Vehicle Testing
-
Nov 2000 - Jul 2010
• Created and streamlined processes that reduced department labor costs by more than $400,000.• Reduced rework costs by $300,000 annually while increasing vehicle quality and reliability through standardization of rework processes. • Trained team members on new model process and inspection standards and performed audits to check accuracy and effectiveness. Met compliance for ISO9002 and ISO14002.
-
-
Group Leader- Final Assembly
-
Jun 1996 - Nov 2000
-
-
Associate- Weld Shop
-
Feb 1994 - Jun 1996
-
-
Education
-
John A. Logan College
-
Southern Illinois University, Carbondale
Criminal Justice and Public Safety
Community
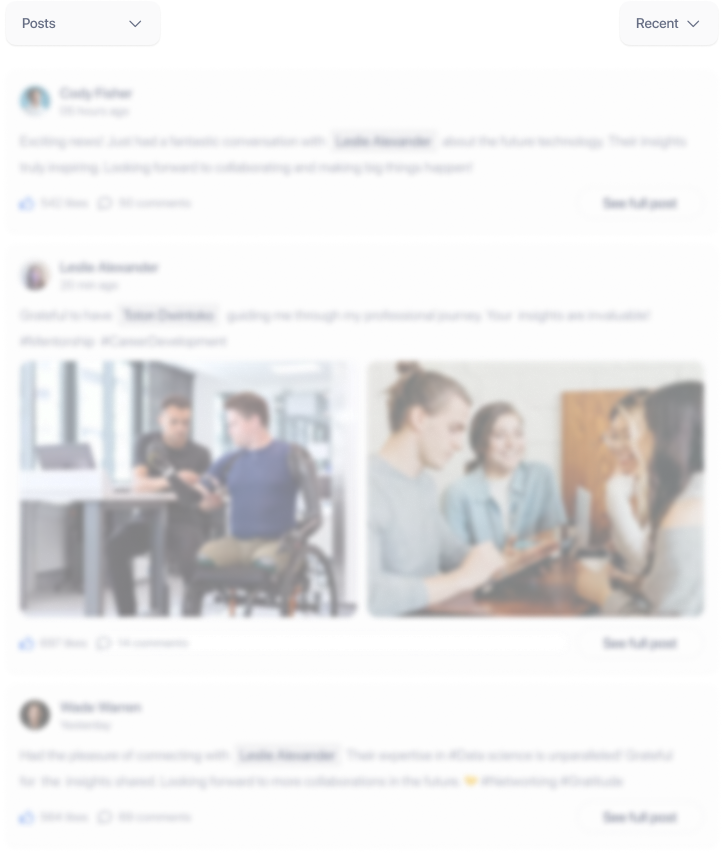