Ricardo Vargas
Corporate Lean Manager at Collado Industries by Grupo Collado- Claim this Profile
Click to upgrade to our gold package
for the full feature experience.
Topline Score
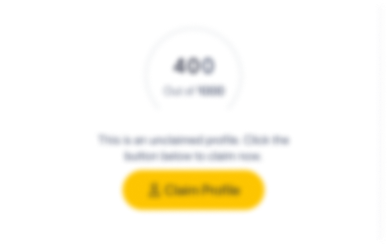
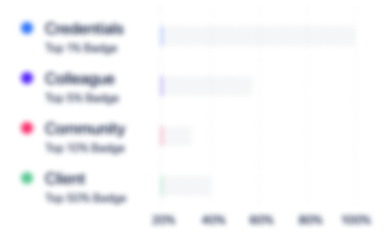
Bio


Experience
-
Collado Industries by Grupo Collado
-
Mexico
-
Mining
-
300 - 400 Employee
-
Corporate Lean Manager
-
Feb 2019 - Present
Leading Change Management System,, Member of Top Management Team (including CEO) to design and drive Management Change Strategy for 12 Facilities. Worldwide and National Locations. Customers working together to Improve Quality and Short and Long Term Operative Performance. Quality and Lean Core Tools coach and Kaizen Driver for Current and New Programs. Leading Change Management System,, Member of Top Management Team (including CEO) to design and drive Management Change Strategy for 12 Facilities. Worldwide and National Locations. Customers working together to Improve Quality and Short and Long Term Operative Performance. Quality and Lean Core Tools coach and Kaizen Driver for Current and New Programs.
-
-
-
BOS Automotive Products, Inc.
-
United States
-
Motor Vehicle Manufacturing
-
300 - 400 Employee
-
Lean Manufacturing Manager
-
Mar 2017 - Jan 2019
-Develop a robust continuous improvement strategy in partnership with the Management Team and key business stakeholders -Implement and support cultural change across the organisation and drive business improvement -Develop a robust continuous improvement strategy in partnership with the Management Team and key business stakeholders -Implement and support cultural change across the organisation and drive business improvement
-
-
-
Henniges Automotive
-
United States
-
Motor Vehicle Manufacturing
-
700 & Above Employee
-
Lean Manufacturing Manager
-
Oct 2013 - Oct 2016
Lean coaching rol and execution for stabilization journey, high customer satisfaction and operative & finantial indicators positive impact based on Lean Management Systems architecture and implementation leader. Key lean leader for current and new coming programs to guarantee successful lean operations with Kaizen 3P, VSM among other tools. Lean coaching rol and execution for stabilization journey, high customer satisfaction and operative & finantial indicators positive impact based on Lean Management Systems architecture and implementation leader. Key lean leader for current and new coming programs to guarantee successful lean operations with Kaizen 3P, VSM among other tools.
-
-
-
Mabe Global
-
Mexico
-
Appliances, Electrical, and Electronics Manufacturing
-
700 & Above Employee
-
Lean Consultant
-
Aug 2010 - Sep 2013
Developing manufacturing processes to ensure the highest quality products with lean principles at mabe facilities. Elimination of waste (in terms of time, materials and manpower) throughout desing and implementation production system. Learning with Shingijutsu Consulting, Japan Developing manufacturing processes to ensure the highest quality products with lean principles at mabe facilities. Elimination of waste (in terms of time, materials and manpower) throughout desing and implementation production system. Learning with Shingijutsu Consulting, Japan
-
-
-
Flex
-
United States
-
Appliances, Electrical, and Electronics Manufacturing
-
700 & Above Employee
-
Global Lean Manager
-
Apr 2007 - Aug 2010
In charge to design and lead Lean Transformation Programs for Worldwide Sites (India, Brazil, China, Malaysia, Hungary). Design and Implement a Lean System at all the sites. Key role to lead efforts to accelerate transformation to business excellence with Lean – 6 Sigma Tools, Responsible for coordination and KAIZEN program execution. Training with Shingijutsu Consulting. In charge to design and lead Lean Transformation Programs for Worldwide Sites (India, Brazil, China, Malaysia, Hungary). Design and Implement a Lean System at all the sites. Key role to lead efforts to accelerate transformation to business excellence with Lean – 6 Sigma Tools, Responsible for coordination and KAIZEN program execution. Training with Shingijutsu Consulting.
-
-
-
HELLA
-
Germany
-
Motor Vehicle Manufacturing
-
700 & Above Employee
-
Lean Manager
-
Jan 2003 - Apr 2007
Senior position responsabile for utilize the Lean methodologies, tools and mindset as a means to break traditional thinking and drive systematic continuous improvement by relentlessly pursuing simplification, velocity, waste elimination. Kaizen Leader Senior position responsabile for utilize the Lean methodologies, tools and mindset as a means to break traditional thinking and drive systematic continuous improvement by relentlessly pursuing simplification, velocity, waste elimination. Kaizen Leader
-
-
-
Ford Motor Company
-
United States
-
Motor Vehicle Manufacturing
-
700 & Above Employee
-
Senior Industrial Engineer
-
Jan 1995 - Jan 2003
Ford Production System Trained Perform assembly work station C/T analysis to break out value-add vs. non-value-add work content to balance workload and reduce C/T. Develop and Implement Lean Program (Ford Production System) Variability Reduction Team Leader for Quality Improvements (Wind Noise/Water leaks/Squeaks &Rattles)-Green belt Project Ford Production System Trained Perform assembly work station C/T analysis to break out value-add vs. non-value-add work content to balance workload and reduce C/T. Develop and Implement Lean Program (Ford Production System) Variability Reduction Team Leader for Quality Improvements (Wind Noise/Water leaks/Squeaks &Rattles)-Green belt Project
-
-
-
Valeo
-
France
-
Motor Vehicle Parts Manufacturing
-
700 & Above Employee
-
Process Engineer
-
Feb 1990 - Dec 1994
Valeo 5 cores trained. Leadership position Relocated to Germany, France, & Spain for training & Manage APQP & Launch Review process. Continuous Improvement, Corrective Actions and TS16949 Systems. Participated for implementing VPS and Continuous Improvement Programs Valeo 5 cores trained. Leadership position Relocated to Germany, France, & Spain for training & Manage APQP & Launch Review process. Continuous Improvement, Corrective Actions and TS16949 Systems. Participated for implementing VPS and Continuous Improvement Programs
-
-
Education
-
Tecnológico de Monterrey
Lean Diplomat -
Instituto Tecnológico Autónomo de México
Master of Business Administration (MBA) -
Instituto Politécnico Nacional
Bachelor's degree, Industrial Engineering
Community
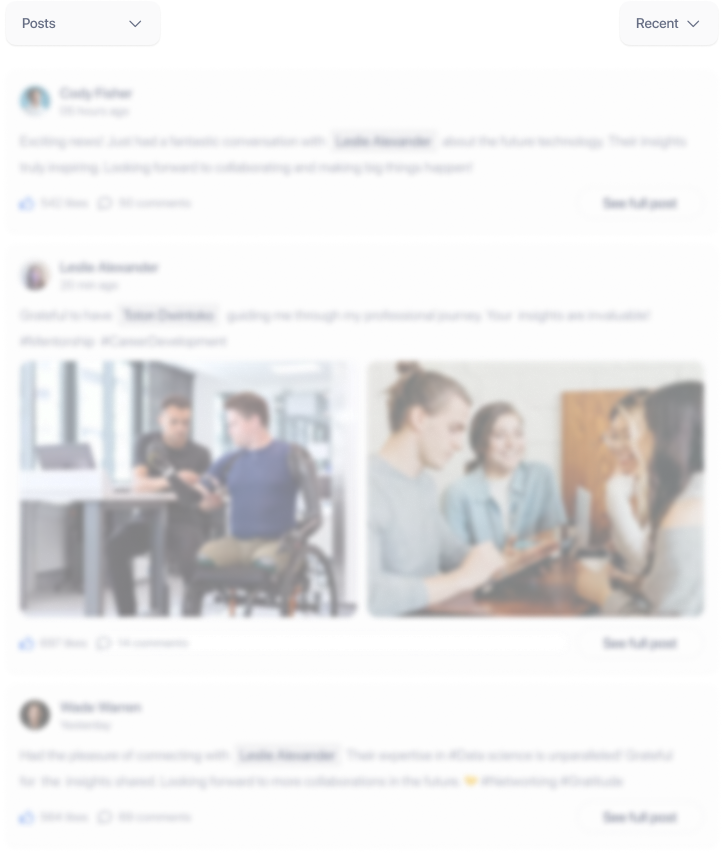