Riaz Ahmed
Plant Manager at Faygo Beverages, Inc- Claim this Profile
Click to upgrade to our gold package
for the full feature experience.
Topline Score
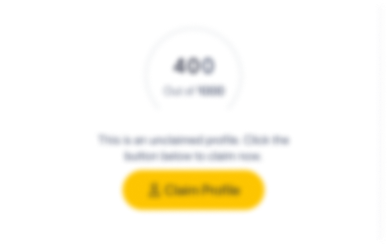
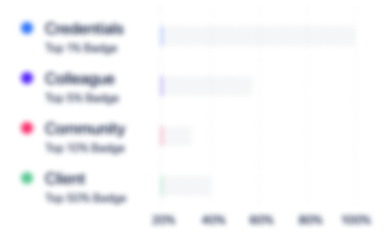
Bio


Experience
-
Faygo Beverages, Inc
-
United States
-
Food & Beverages
-
1 - 100 Employee
-
Plant Manager
-
Dec 2017 - Present
Detroit, Michigan
-
-
-
-
Maintenance Manager
-
Jul 2017 - Nov 2017
Carson City Develop and manage Preventative/Predictive Maintenance Program including managing budget, spare parts inventory, overtime, outside services, continuous improvement and technical downtime on production equipment. Duties, responsibilities and accomplishments: • Provide leadership and direction to the department in all aspects that deal with the maintenance and repair of plant equipment. • Developed technical downtime tracking document to track technical downtime to decrease downtime… Show more Develop and manage Preventative/Predictive Maintenance Program including managing budget, spare parts inventory, overtime, outside services, continuous improvement and technical downtime on production equipment. Duties, responsibilities and accomplishments: • Provide leadership and direction to the department in all aspects that deal with the maintenance and repair of plant equipment. • Developed technical downtime tracking document to track technical downtime to decrease downtime by reviewing and correcting root causes of failures on production equipment. • Developed planned window template for sanitation and maintenance activities to track ontime completion of each task during planned down window. • Implementing preventive and predictive maintenance program on all production equipment to increase equipment reliability. • Monitor equipment efficiency to determine where to use resources and repair cost to reduce downtime and improve production. • Forecasted 2018 budget and managing 2017 budget. • Implementing continuous improvement program. • Implementing equipment ownership program for maintenance technicians. • Develop a plan to implement autonomous maintenance program to give operators a sense of ownership. • Ensure parts availability in the MRO stockroom to minimize equipment downtime while balancing economic maintenance inventory management. • Created critical spare parts list for critical and non critical equipment. • Developing equipment ID system for all production equipment. • Wrote RCAs to buy new checkweigher and spreader conveyor. • Managing maintenance parts procurement and budget for contracted repairs. • Collaborate with cross-functional groups including Production, Quality, Warehousing, and Finance to meet production targets. • Adhere to company LOTO, GMP, safety procedures and all quality processes. • Maintain facility and assets to meet regulatory guidelines of FDA, USDA, OSHA, and EPA. Show less
-
-
-
-
Maintenance Supervisor/Planner/compliance lead
-
Mar 2011 - Jul 2017
Franklin Park, IL Maintain a safe working environment and ensure that all employees are working with the established safety guidelines for their areas. Work with sanitation, quality, safety and operation during planned downtime. Manage Maintenance work orders in SAP. I am also Nestle certified super user for AMM and provide training on AMM systems to mechanics, supervisors and managers. I received “Best in the Nest” nominee award. I also have completed “On-Scene Incident Commander” training. • Release… Show more Maintain a safe working environment and ensure that all employees are working with the established safety guidelines for their areas. Work with sanitation, quality, safety and operation during planned downtime. Manage Maintenance work orders in SAP. I am also Nestle certified super user for AMM and provide training on AMM systems to mechanics, supervisors and managers. I received “Best in the Nest” nominee award. I also have completed “On-Scene Incident Commander” training. • Release and assign weekly, bi-weekly, Monthly, Quarterly, Semi-annual and annual PMs. • Supervise maintenance team to support and maintain production equipment. • Plan activities for production equipment and facilities maintenance weekly. • Manage contracted repair work projects. • Lead and manage 4th of July and Christmas shutdown activities. • Prioritize and assign food safety and safety work orders. • Check and report work order backlog, PM completion and PM03 Schedule Compliance. • Provide training to mechanics to continuously improve their skills . • Manage and update mechanics skills matrix. • Monitor and report unplanned downtime in daily and weekly meetings. • Rolled out BDA (Breakdown Analysis) process for Technical failures to find the root cause. • Created BDA process documents including BDA process flow chart and BDA standard operating procedure. • Perform BDA and GSTD for extended equipment failures. • Perform internal audit on compliance related activities. • Participate in internal and ISO audits. Help Quality, Operations and Safety departments before, during and after the audits. • Monitor compliance related activities and maintain all compliance related maintenance documents for ISO and EFCA audits. • Lead and coordinate EFCA, Engineering Functional Compliance Assessment, audit preparation activities. • Participate in strategic planning meetings for equipment replacement and upgrade. Show less
-
-
Education
-
DeVry University
Bachelor's degree, Electronica Engineering Technology
Community
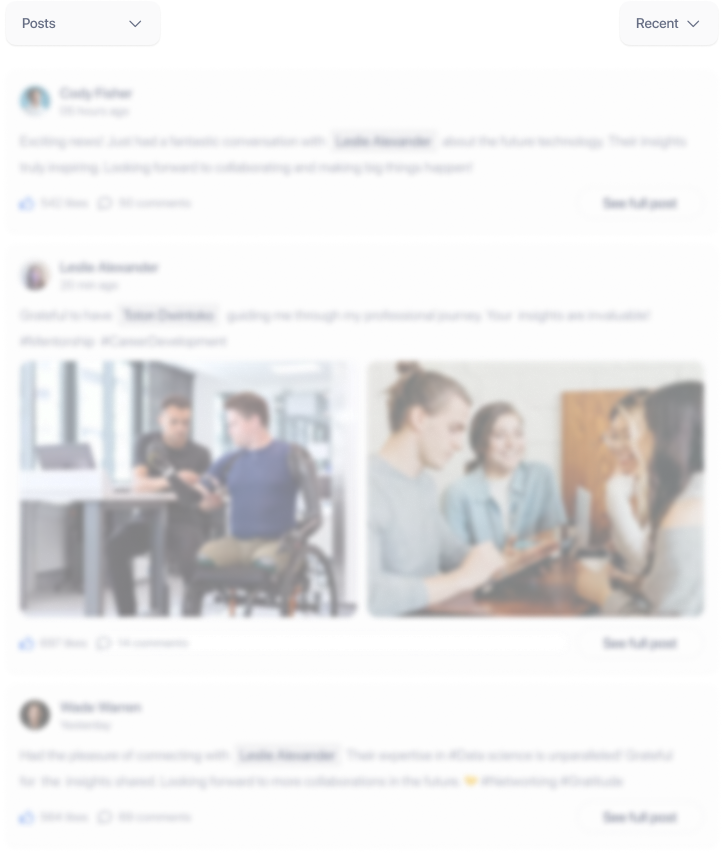