Rhannie Deng
Manager at E Ink Corporation- Claim this Profile
Click to upgrade to our gold package
for the full feature experience.
-
English (TOEIC: 890) Native or bilingual proficiency
Topline Score
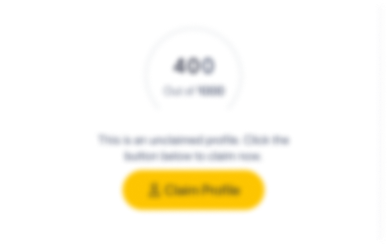
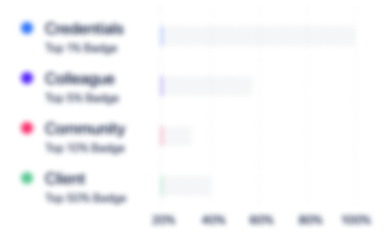
Bio


Experience
-
E Ink Corporation
-
United States
-
Appliances, Electrical, and Electronics Manufacturing
-
400 - 500 Employee
-
Manager
-
Mar 2015 - Present
Team build for three functions: Cost Control, Efficiency improvement & Capacity Planning -Set the plan and objectives of the operating unit: Integrate the production, sales, people, development, finance and other departments to complete the task. Meet the mission objectives. Establish cross-departmental workflows. Track the progress of the project and break through key bottlenecks to achieve our targets. -IE organization management and IE function implementation. -FPL Section Sheet Optimization: Saving NTD 50M/year -Execute cost reduction plan & promote efficiency.: Saving NTD 200M/year -Short, Middle & Long-term planning. -Investment analysis, payback & ROI evaluation: Saving NTD 300M/year -Performed capacity loading plan, simulated capacity loading scenarios, tools move-in schedule control and monitor -Enhance to improve headcount productivity: productivity up 20% -New FAB & Site Layout planning ,coordinate all Dept., and schedule control -Advance Std Time system & database. -Promote LCD, Module & FPL FAB Std Time systemization & shorten the invalid working hours. -KPI define, review & tracing: Scrap Rate 12%->6% Saving 720M/year -Provide rational solutions for executives’ decision making. Show less
-
-
-
AUO
-
Taiwan
-
Appliances, Electrical, and Electronics Manufacturing
-
700 & Above Employee
-
Engineering Manager
-
Aug 2005 - Mar 2015
-RD Line Allocation Project (Cost Saving: NTD 400 millions): -For AUO L3B Shut Down, I use LSS method & organize a team with RD, Facility, FAB & Layout Dept. I’m the project leader. The project save NTD 400 million to avoid re-allocation. -TV Panel Optimum Recycle Ratio Evaluation: For hot season & consider the opportunity cost, find the best large size ratio for recycle to optimize G6~G8 capa. -China Site Plan: Considering growing of panel & salary, plan 1~3 years investment 、Labor 、Layout & capa and utilize idle place. -Packing Recycle for Vestel Project (Yearly Saving: NTD 0.4E) For Green policy, promote outsourcer to make package material recycle. OEM Fee decreases USD 1.2/pcs. -Activity-base Cost Phase-in & Systematization (Establish AUO Standard Cost & Simplify operation period) -For Activity-base Cost project, set up AUO standard cost methodology, and make it systematization. The operating efficiency was improved significantly. The systematization period was shortened from 8 months to 3 months by cooperating with IT, FIN & factory. -Outsouring Strategy (Yearly Saving:NTD 7E) In the outsourcing strategy, decrease 60% outsourcing fee by comparing outsourcing price with AUO cost. Save 700 million yearly. -Cost Project: In cost project, set the annual target, so the cost per unit area was down 15% to 20%, and increase cost competitiveness at the same time. - Lean for Singapore Site : I also received Lean Six Sigma training. It was to use the skill to promote the AUO Singapore cell beol process to China, and save NTD 100 million manufacturing cost by lowering the thinning cost of outsourcing. -New Thinning Glass FAB in AUO Evaluate possibility & push thinning supplier to decrease price. -Change Business Model for Shipment Suggest that strengthen LCD panel shipment ratio and weaken LCM panel shipment ratio Show less
-
-
-
United Microelectronics Corporation (UMC)
-
Taiwan
-
Semiconductors
-
700 & Above Employee
-
Senior Engineer
-
Oct 2001 - Jul 2005
-12” Layout Planning for Singapore site (Cost Saving NTD 200 m): In UMC, I am responsible for the facility planning of 300 mm Fab. Due to miscellaneous process & devices, expensive equipment, layouts have hung influence on operation efficiency, capital expense, & wafer-out. Briefly speaking, equipment planning is to maximize production efficiency. It’s exiting that Fab costing billions follows my plan in the AutoCad drawings. -8” FAB cost control: Promote 8” fab to have cost competitiveness: -Slurry reduce: Dilute Slurry: Cost saving: NTD 5.4 million/month -Chamber Life Time Extended:2400 hrs->4800 hrs, Cost Saving:600millions/month -Capacity Planning: Decrease PM frequency & time, raise up time & reduce down time: Capa improvement:30% Show less
-
-
-
BenQ Corporation
-
Taiwan
-
Consumer Electronics
-
700 & Above Employee
-
Engineer
-
Mar 2000 - Oct 2001
1.Shop floor Control: Reduce waste, optimize productivity, and drive Line Balance: Productivity up 20%. 2.Shop floor Improvement: The introduction of automation equipment enabled the company to reduce direct labor costs by more than NTD M. The introduction of the Barcode System reduces the cost of quality loss on the wrong materials for operators. 1.Shop floor Control: Reduce waste, optimize productivity, and drive Line Balance: Productivity up 20%. 2.Shop floor Improvement: The introduction of automation equipment enabled the company to reduce direct labor costs by more than NTD M. The introduction of the Barcode System reduces the cost of quality loss on the wrong materials for operators.
-
-
Education
-
Rutgers, The State University of New Jersey-New Brunswick
Master of Science (MS), Industrial & Systems Engineering -
National Chiao Tung University
Bachelor of Science (BS)
Community
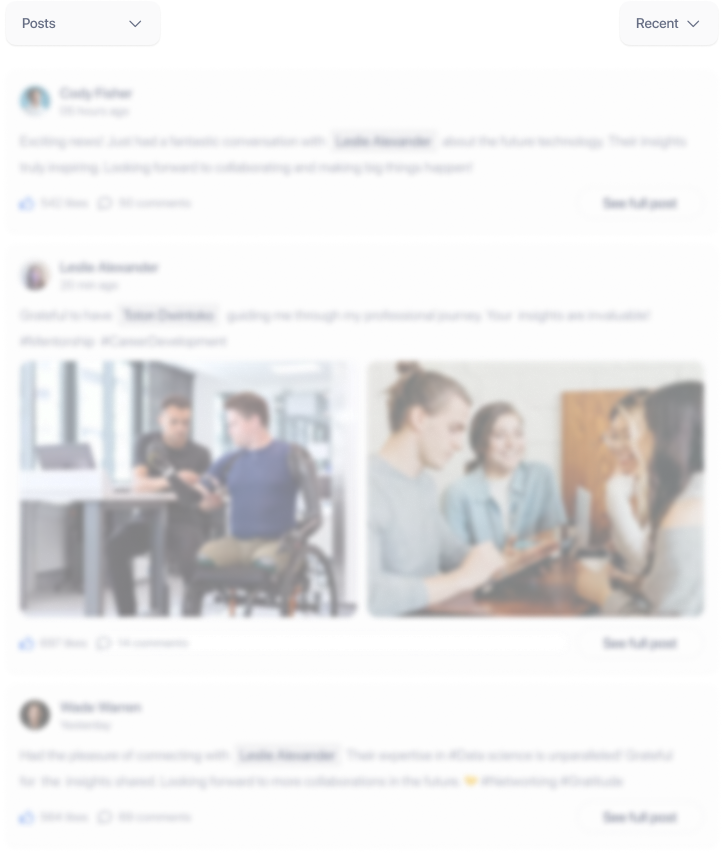