Reno Gusman
HSE Manager at P.T Ichikoh Indonesia- Claim this Profile
Click to upgrade to our gold package
for the full feature experience.
Topline Score
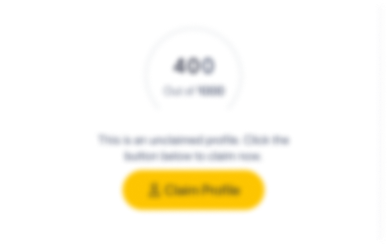
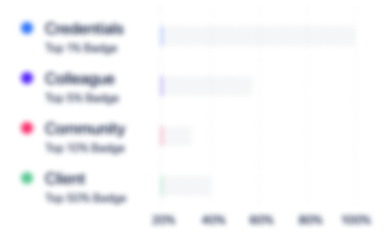
Bio


Experience
-
P.T Ichikoh Indonesia
-
Motor Vehicle Manufacturing
-
100 - 200 Employee
-
HSE Manager
-
Mar 2021 - Present
Technical aspects: • Ensure continuously that all buildings, processes, equipment, machines, installations, all devices, materials and products of the site present the minimum hazard, through his involvement upstream of the projects, the issuance of HSE specifications, reception and the audit of these means on a continuous basis. • Planning, assigning, budgeting and monitoring the implementation of all corrective or preventive improvement actions in the technical field following to internal/ external audits, inspections and exchange of best practices. Organizational aspects: • Analyze the regulatory compliance of its site and maintain it continuously. • Perform risk assessments for all HSE fields on the site, including emergency mode, non prescribed / unplanned work such as contractor works, unplanned maintenance, deviation to validated process, and each deviations is captured in database with an updated mitigation plan to cover deviation lead time. • Ensure and audit by OJT that safety tools, safety standards are adapted, known, understood, applied, and enforced by management • Communicate internally (operators, managers, employee representatives) and externally (authorities, inspectors, neighbors, other companies, etc.) on HSE issues • Assess and monitor safety risks from deviations to standard.(Deviation Database) • Monitor incidents and accidents on the site using QRQC & PDCA/FTA tools Behavioral aspects: • Develop manager Safety Skills using Safety first, Risk Hunting, PFMEA, Safety Talks and Safety Briefing tools to certified and autonomous in safety. • Train people to react in emergency and unexpected situation
-
-
-
PT Hyundai Motors Indonesia
-
Indonesia
-
Motor Vehicle Manufacturing
-
500 - 600 Employee
-
Environment, Health and Safety Manager
-
Jul 2020 - Jan 2021
• Supports the Top Management in the HSE Policy and Guidelines issue. • Supports the Top Management in the Organization roles and responsibilities definition, for what concerns safety aspects. • Supports the Top Management in the HSE Management System standard issue. • Ensures, in accordance with the corporate guidelines, the implementation, updating, review and auditing of the Company HSE Systems. • Monitors the effective implementation of appropriate Safety and Environment System procedures and provide for their updating in line with changes in Legislation and Company Directives. • Provides for motivation and familiarization of all Company personnel respecting the importance of complying with Company system procedures and all Safety equipment provided. • Assists the Commercial, Engineering and Operations Department in their dealings with Clients in all issues concerned with Health and Safety at work. • Conducts safety audits both internal and external. • Takes part in accident / incident investigation. • Carries out analysis of accident / incident statistics, identifying trends and suggesting improvement plans. • Provides technical support to Senior Management on any safety related subjects.
-
-
-
PT SGMW Motor Indonesia
-
Indonesia
-
Motor Vehicle Manufacturing
-
300 - 400 Employee
-
HSSE Manager
-
Oct 2018 - Jun 2020
• Arrange daily, monthly and yearly schedule/work plan based on company objectives and requirement • Plan and coordinate plant’s safety audits and follow up • Develop safety policies and procedures. • Comply, monitor and advise changes in standard legislation to management and employees, as per requirement by Indonesia Laws. • Develop and plan health and safety committee support • Develop security and fire protection policies & procedures, and audit the plant’s performance. • Establish safety training master plan to meet Company HSSE (Health Safety Security and Environment) requirements • Develop policies and procedures for contractor’s health and safety • Establish occupational health and ergonomic management plan • Develop Plant Safety coordination and promotion of all planned safety activities
-
-
-
Adient
-
United States
-
Motor Vehicle Manufacturing
-
700 & Above Employee
-
Environment, Health and Safety Manager
-
May 2015 - Sep 2018
• Creating and maintain HSE policy, procedures and standards of Health, Safety, Environment and ergonomic implemented, maintained and sustained continuously and to determine method to improve the standard of HSE. • Implement and maintain AMS program from enterprise has been applied and implemented properly to every department. • Provide reports and is responsible directly to the president regarding the development of the implementation of the work program Occupational Health, Safety and the environment and also to report to HSE Regional • Implementation of Hazard Identification and Risk assessment as well as Aspects and Impact studies based on OHSAS 18001 and ISO 14001 • Creating and implementing Health, Safety, Environment and Ergonomic management system based on AMS, global enterprise, OHSAS 18001 and ISO • Design and establish the HSE policy also set strategic planning to implement legal compliances that applicable • Organize and monitoring HSE performance of all plant and department, reporting and follow up the result • Creating system to organize and implementation of Emergency response planning.
-
-
-
PT. Armada Johnson Controls
-
Tambun, Jawa Barat, Indonesia
-
Health Safety Environment Assistant Manager
-
Mar 2011 - Sep 2015
• Create working program for HSEE • Develop training schedule for HSEE program • Deliver training to employee for HSEE program • Monitoring to HSEE program implementation • Creating SOP, HIRADC, Work Instruction • Prepare monthly meeting, P2K3 Meeting periodically • Creating HSE and P2K3/Safety Committee team activity report to Labor and Manpower office/Disnakertrans Every quarter. • Create working program for HSEE • Develop training schedule for HSEE program • Deliver training to employee for HSEE program • Monitoring to HSEE program implementation • Creating SOP, HIRADC, Work Instruction • Prepare monthly meeting, P2K3 Meeting periodically • Creating HSE and P2K3/Safety Committee team activity report to Labor and Manpower office/Disnakertrans Every quarter.
-
-
-
SHARP SEMICONDUCTOR INDONESIA, PT
-
Indonesia
-
Appliances, Electrical, and Electronics Manufacturing
-
1 - 100 Employee
-
Health Safety Environment Officer
-
Jan 2006 - Dec 2011
• Make a working program for HSE • Make training schedule for HSE program • Give training to employee for HSE program • Monitoring to HSE program implementation • Making SOP, HIRAC, Work Instruction • Prepare monthly meeting, P2K3 Meeting periodically • Make a working program for HSE • Make training schedule for HSE program • Give training to employee for HSE program • Monitoring to HSE program implementation • Making SOP, HIRAC, Work Instruction • Prepare monthly meeting, P2K3 Meeting periodically
-
-
Education
-
Universitas Mercu Buana
Bachelor's degree, Teknik Industri
Community
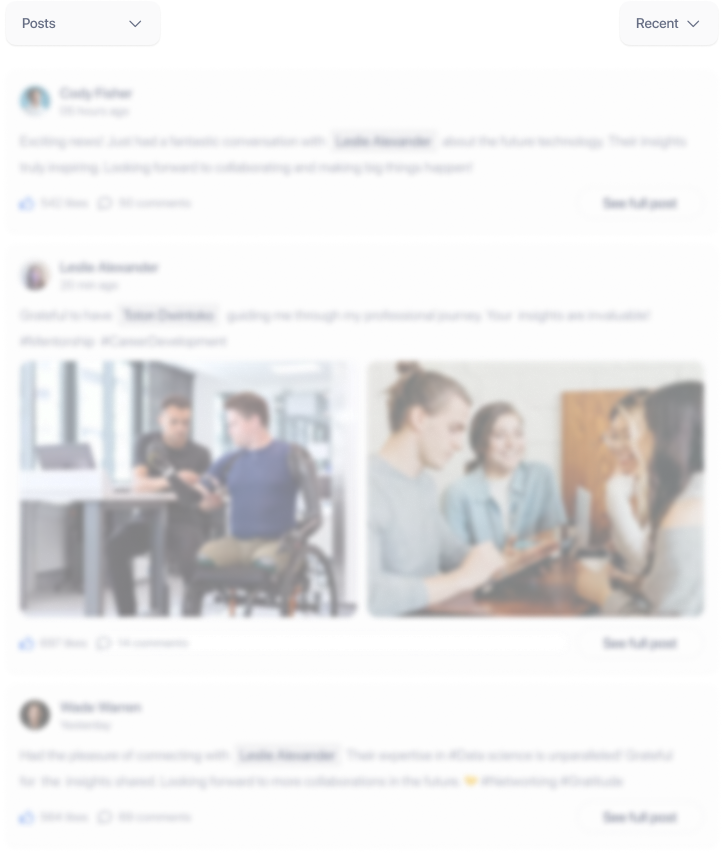