
Renee Soppe
Cost Accountant at KPI Concepts- Claim this Profile
Click to upgrade to our gold package
for the full feature experience.
Topline Score
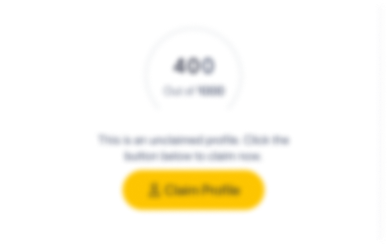
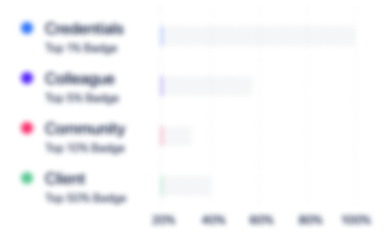
Bio

Gary Bezner
Whenever I needed a partner and guide for improving my managed business systems, Renee was the person that I reached out to for assistance. I knew that I could always rely on her honesty, integrity, common sense, and customer need focus to help me define the core problems and ways to prevent them. Renee has acquired a significant knowledge of continuous improvement analysis techniques, and she is able to pull out the right tool at the correct time to systematically define a problem and a plan of attack toward solving it. She is passionate in identifying productive system solutions for her customers and is a very strong leader who can bring people together to achieve them. I can highly recommend Renee as an effective continuous improvement professional.

Gary Bezner
Whenever I needed a partner and guide for improving my managed business systems, Renee was the person that I reached out to for assistance. I knew that I could always rely on her honesty, integrity, common sense, and customer need focus to help me define the core problems and ways to prevent them. Renee has acquired a significant knowledge of continuous improvement analysis techniques, and she is able to pull out the right tool at the correct time to systematically define a problem and a plan of attack toward solving it. She is passionate in identifying productive system solutions for her customers and is a very strong leader who can bring people together to achieve them. I can highly recommend Renee as an effective continuous improvement professional.

Gary Bezner
Whenever I needed a partner and guide for improving my managed business systems, Renee was the person that I reached out to for assistance. I knew that I could always rely on her honesty, integrity, common sense, and customer need focus to help me define the core problems and ways to prevent them. Renee has acquired a significant knowledge of continuous improvement analysis techniques, and she is able to pull out the right tool at the correct time to systematically define a problem and a plan of attack toward solving it. She is passionate in identifying productive system solutions for her customers and is a very strong leader who can bring people together to achieve them. I can highly recommend Renee as an effective continuous improvement professional.

Gary Bezner
Whenever I needed a partner and guide for improving my managed business systems, Renee was the person that I reached out to for assistance. I knew that I could always rely on her honesty, integrity, common sense, and customer need focus to help me define the core problems and ways to prevent them. Renee has acquired a significant knowledge of continuous improvement analysis techniques, and she is able to pull out the right tool at the correct time to systematically define a problem and a plan of attack toward solving it. She is passionate in identifying productive system solutions for her customers and is a very strong leader who can bring people together to achieve them. I can highly recommend Renee as an effective continuous improvement professional.

Experience
-
KPI Concepts
-
United States
-
Retail Office Equipment
-
1 - 100 Employee
-
Cost Accountant
-
Mar 2022 - Present
-
-
-
Staffing Partners, Inc.
-
United States
-
Staffing and Recruiting
-
1 - 100 Employee
-
Contractor
-
Jun 2018 - Sep 2018
-
-
-
Parker and Lynch
-
United States
-
Staffing and Recruiting
-
100 - 200 Employee
-
Contractor
-
Aug 2016 - Jul 2017
Responsible for service revenue and fixed asset accounting (filling interim need): month-end close & reporting, account reconciliations, internal controls, audit support, capital spend tracking, and relevant ad-hoc tasks Responsible for service revenue and fixed asset accounting (filling interim need): month-end close & reporting, account reconciliations, internal controls, audit support, capital spend tracking, and relevant ad-hoc tasks
-
-
-
Upsher-Smith
-
Pharmaceutical Manufacturing
-
300 - 400 Employee
-
Independent Consultant
-
Jan 2015 - Feb 2015
Engaged to execute and document the annual product standard cost roll. Reviewed and revised costing methodologies to ensure proper accounting treatment and product profitability reporting. Engaged to execute and document the annual product standard cost roll. Reviewed and revised costing methodologies to ensure proper accounting treatment and product profitability reporting.
-
-
-
Upsher-Smith
-
Pharmaceutical Manufacturing
-
300 - 400 Employee
-
Assoc Manager, Financial Planning & Analysis (CI, Supply Chain, Quality Operations)
-
Jul 2013 - May 2014
Managed Cost Accounting and all aspects of planning and analysis for Inventory, Operations, Quality, Supply Chain (including annual plans, quarterly forecasts, monthly reporting, and ad-hoc requests). Maintained Continuous Improvement leadership for the organization: training, mentoring, projects.Accomplishments:-Built and maintained a balanced Corporate Metrics Dashboard for executive leadership team; partnered with VPs/Directors to develop actional 2nd-tier metric dashboards to cascade corporate level- Established departmental metrics to manage cost accounting transition, workload, and performance- Enhanced cost and inventory accounting to meet all SEC quarterly reporting and controls requirements
-
-
Continuous Improvement Specialist
-
Apr 2010 - Jul 2013
Transitioned outside of Finance to company-wide Continuous Improvement (CI) leadership.Accomplishments:- Built and delivered ongoing CI workshops and tools around Root Cause Analysis, Process Mapping, and Metrics; focused on the application of knowledge with personal follow-up and project development- Communicated CI engagement and results through success stories and metrics- Through mentoring and projects, developed a network of CI Ambassadors as functional focus points- Benchmarked numerous organizations and attended training to constantly expand CI knowledge base; updated CI Steering Committee to propose strategic initiatives for long-term planning- Actively participated on several successful cross-functional teams assembled to analyze, prioritize, and manage accountability on initiatives that directly improved company profitability- Facilitated projects in every functional area of the business to drive engagement and results
-
-
Sr Cost Accountant / Analyst
-
Mar 2006 - Apr 2010
Started as traditional Cost Accountant role - standard product costing, planning/forecasting, financial analysis and reporting. Grew role to senior analyst level, working closely with Operations/Supply Chain on product profitability analysis and operational efficiency.Accomplishments:- Built and owned processes to analyze and communicate plant variances, resulting in improved standard costing accuracy and the identification of production process issues- Led initiative to develop actionable inventory analytics; partnered with Supply Chain to improve working capital - Partnered with Operations on numerous process improvement and capital projects, prioritized based on variance metrics- Recognized as SAP Super User for Finance team, responsible for first-level troubleshooting; working with other super users on company-wide improvement projects- Took a significant role on a cross-functional team aimed at improving profitability on the generic drug portfolio; delivered outstanding results (>$10M) through product rationalization, pricing recommendations, cost/scrap reduction, and volume gains through improved capacity
-
-
-
Honeywell
-
United States
-
Appliances, Electrical, and Electronics Manufacturing
-
700 & Above Employee
-
Staff Accountant
-
Jun 2003 - Mar 2006
Staff Accountant (Engineering) and Capital Accountant: Finance support at dynamic semiconductor manufacturer. Primary responsibilities were financial planning, analysis, and reporting; additional experience with government compliance and SOX. Earned Six Sigma Green Belt certification, working with accounting processes and financial modeling for Engineering and Operations. Staff Accountant (Engineering) and Capital Accountant: Finance support at dynamic semiconductor manufacturer. Primary responsibilities were financial planning, analysis, and reporting; additional experience with government compliance and SOX. Earned Six Sigma Green Belt certification, working with accounting processes and financial modeling for Engineering and Operations.
-
-
Education
-
University of Northern Iowa
Bachelor of Arts (B.A.), Accounting
Community
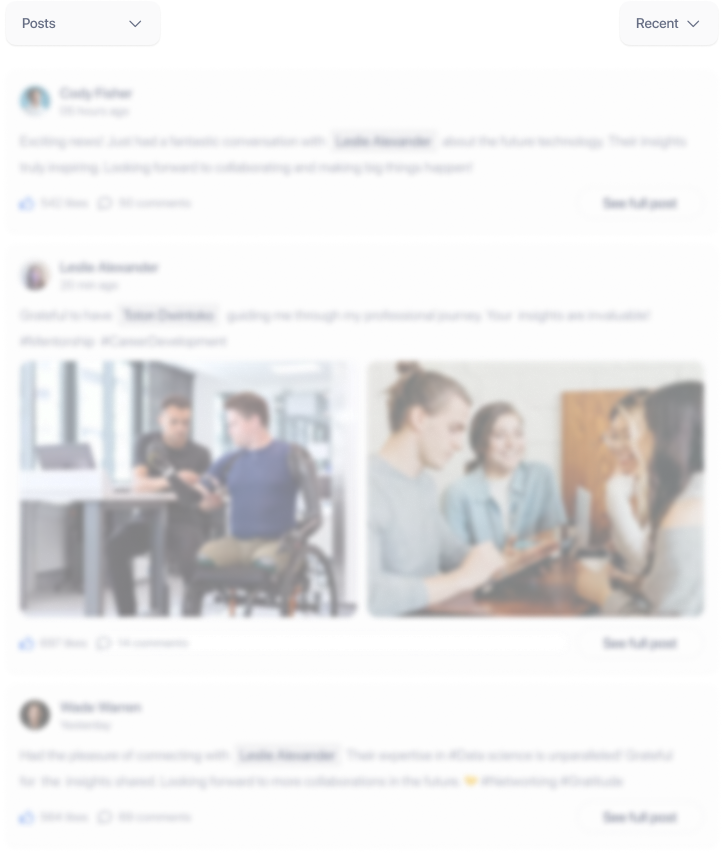