Rene Gagnier
Estimating Engineer at WMG Technologies- Claim this Profile
Click to upgrade to our gold package
for the full feature experience.
Topline Score
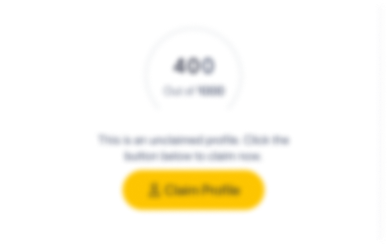
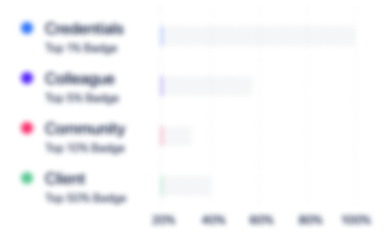
Bio


Experience
-
WMG Technologies
-
Canada
-
Motor Vehicle Manufacturing
-
200 - 300 Employee
-
Estimating Engineer
-
Jan 2013 - Present
Gather information and work with internal team to collaborate and provide better solutions. Compared quotes against requests for quotations to identify gaps. Followed up with vendors to drive complete and compliant quotes for proposal or provide clear exceptions to spec. Conducted research to obtain data on labor costs, materials and production times. Drafted requests for quotations to comply with project specifications. Identified areas of risk or lack of information to produce estimates or provide suggestions for risk mitigation. Communicated with project management, engineering and purchasing personnel to solicit feedback on cost and lead-time estimation. Attended customer and vendor meetings to answer technical questions and complete required deliverables. Leveraged estimating tools and quotes from vendors to develop cost estimates and lead times for proposals. Provided accurate estimates by defining scope, timelines, potential setbacks and limitations. Collected historical cost data to estimate costs for current or future products. Utilized cost estimation systems to document project information, create estimates and revise project costs to reflect current data. Calculated correct costs for project-specific goods and services by gathering information from team members, sub-contractors and vendors. Maintained privacy and confidentiality of all information for existing and prospective clients to protect personal and business interests. Delivered comprehensive bid proposals for online auctions for several OEM
-
-
Health And Safety Coordinator, Human Resources, Accounts Receivable and Logistics
-
Jan 2007 - Jan 2013
Conducted incident investigations, participated in audits and collected data and information to maximize workplace safety. Mentored and supported staff in identifying and implementing procedures and practices to protect safety and security of workers. Supported interaction with local emergency response agencies and responders to coordinate work site security requirements. Provided new-employee health and safety orientations and developed materials for presentations. Identified accident causes and optimal prevention strategies by conducting thorough investigations and analyses. Recommended measures to help protect workers from potentially hazardous work methods, processes and materials. Attended CTMA safety meetings, created policies and procedures and implemented by plant wide training. Managed all WSIB, STD and LTD claims. Reviewed and screened applicant resumes to identify qualified candidates. Reviewed existing policies and procedures to make recommendations for enhancing work productivity, recruitment, hiring processes and talent management. Liaised between management and employees to deliver conflict resolution, alleviate problems and interpret compensation and benefits policies. Planned and managed recruitment activities for new hires using strategic personnel, staffing and position management practices. Oversaw and managed hiring process and assisted human resources. Advocated for staff members and counsel supervisors to identify and resolve conflicts. Maximized team knowledge and productivity by training, monitoring and directing employees in application of best practices and regulatory protocols. Partnered with senior leadership to establish and develop corporate and HR policies and procedures
-
-
Data Processor
-
Jun 2006 - Jan 2007
Sorted and processed incoming files, customer RFQ's, before putting data into processing software for translation Managed data entry and accuracy verification for large data projects. Tracked and maintained records for Engineering and Estimating department. Scanned documents and saved in database to keep records of essential organizational information. Accurately handled data entry for several OEM's into company-based software.
-
-
Shop Floor Manufacturing Supervisor
-
Jan 2003 - Jun 2006
Communicated job expectations and monitored employees. Read and interpreted schematics, technical documentation and production orders. Identified problems and implemented effective solutions. Completed production plans by scheduling and assigning personnel to daily tasks. Reported tool, machinery and equipment issues to maintenance personnel. Recorded and reported attendance and hours worked for all area employees. Performed accident investigations. Ordered parts and materials for plastic injection molds. Collaborated with other leaders and executives to direct workflow and support operations. Kept accurate and detailed records of personnel progress and productivity. Planned, organized and monitored resources to deliver efficient use of labor, equipment and materials. Implemented policies and standard operating procedures for continuous improvement. Interpreted work order information and specifications to plan, schedule and complete jobs precisely. Oversaw, coached and evaluated team leaders in several departments. Conducted performance reviews each year, offering praise and recommendations for improvement. Coordinated project workflows for departments. Analyzed mold tryouts using various troubleshooting methods. Collaborated with internal teams to streamline operations across materials handling, production and shipping. Developed strong relations with company associates, reducing turnover. Designed floor plan and equipment placement.
-
-
Team Leader
-
Jun 1994 - Jan 2003
Mentored and guided employees to foster proper completion of assigned duties. Conducted training and mentored team members to promote productivity, accuracy and commitment to friendly service. Demonstrated knowledge of company mission and goals and mentored employees in reaching objectives aligned with company core values. Established open and professional relationships with team members to achieve quick resolutions for various issues. Implemented new working processes to deliver multiple improvements. Maximized efficiency by removing safety hazards and debris from work areas. Participated in cross-functional team-building activities. Set up and calibrated machinery to meet specific production requirements and meet desired tolerances. Overseen complete plastic injection tool builds using blue prints. Created machine line up utilizing blue prints for coordinates and programming.
-
-
Mould Maker Apprentice
-
Jun 1990 - Jun 1994
Quickly learned new skills and applied them to daily tasks, improving efficiency and productivity. Carried out day-day-day duties accurately and efficiently. Demonstrated respect, friendliness and willingness to help wherever needed. Worked flexible hours; night, weekend, and holiday shifts. Maintained energy and enthusiasm in fast-paced environment. Proved successful working within tight deadlines and fast-paced atmosphere. Used critical thinking to break down problems, evaluate solutions and make decisions. Offered friendly and efficient service to customers, handled challenging situations with ease. Developed and maintained courteous and effective working relationships. Maintained excellent attendance record, consistently arriving to work on time. Improved operations through consistent hard work and dedication. Exceeded goals through effective task prioritization and great work ethic.
-
-
Education
-
St. Clair College
Community
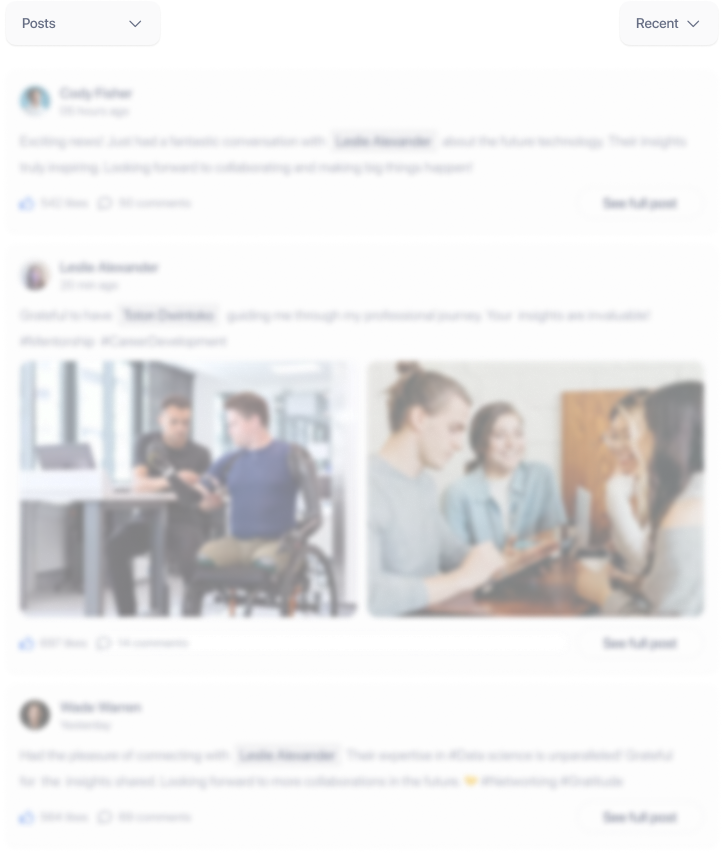