Robert Bickle
Chief Quality Officer at Acacia Communications Inc.- Claim this Profile
Click to upgrade to our gold package
for the full feature experience.
-
English -
Topline Score
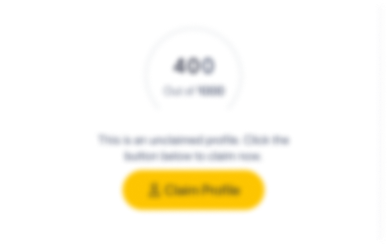
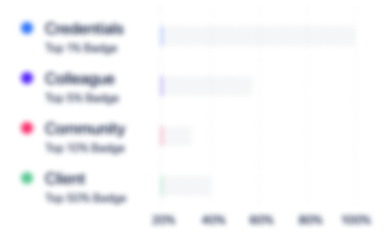
Bio
0
/5.0 / Based on 0 ratingsFilter reviews by:
Credentials
-
Lean Gold
ARRISOct, 2013- Sep, 2024 -
Master Black Belt
MotorolaApr, 2013- Sep, 2024 -
Private Pilot
FAAJun, 2010- Sep, 2024 -
Lead Auditor
RABQSAMar, 2006- Sep, 2024 -
Demand Flow Manufacturing and Business Processes
John Costanza Institute of TechnologyJan, 1999- Sep, 2024 -
Statistical Process Control
Lockheed MartinJan, 1998- Sep, 2024
Experience
-
-
Chief Quality Officer
-
Mar 2018 - Present
Reporting to the CEO, responsible for developing and implementing strategies for reliability and quality of hardware, software, and services offered by Acacia Communications. Lead Quality Engineering; Reliability Engineering; Component Engineering; Quality and Business Improvement; Reverse Logistics; and Compliance. Lead development of Services as a business. Work with the CEO and the Senior Leadership Team to develop and deploy quality strategies to exceed quality objectives and drive customer satisfaction. P&L Responsibility.
-
-
-
Telecommunications Industry Association
-
United States
-
Telecommunications
-
100 - 200 Employee
-
Board Member
-
Nov 2017 - Mar 2018
Board member of TIA as part of the QuEST Forum and TIA merger. TIA represents manufacturers and suppliers of global communications networks through standards development, policy and advocacy, business opportunities, market intelligence, and events and networking. Board member of TIA as part of the QuEST Forum and TIA merger. TIA represents manufacturers and suppliers of global communications networks through standards development, policy and advocacy, business opportunities, market intelligence, and events and networking.
-
-
-
QuEST Forum
-
United States
-
Telecommunications
-
Member Board of Directors
-
Jan 2016 - Mar 2018
QuEST Forum is the collaboration of information and communication technologies (ICT) service providers and suppliers across the world who are dedicated to improving operational and supply chain quality and performance. QuEST Forum unifies the global ICT community through the implementation of TL 9000, an industry specific quality management system that is built on ISO 9001 and the eight quality principles. QuEST Forum is the collaboration of information and communication technologies (ICT) service providers and suppliers across the world who are dedicated to improving operational and supply chain quality and performance. QuEST Forum unifies the global ICT community through the implementation of TL 9000, an industry specific quality management system that is built on ISO 9001 and the eight quality principles.
-
-
-
ARRIS
-
United States
-
Real Estate
-
1 - 100 Employee
-
Vice President, Global Customer and Business Quality
-
May 2013 - Mar 2018
Senior Executive responsible for Customer Loyalty, Quality, Compliance, and Productivity for a $5B global business. Deliver software, hardware and services quality strategies. Lead international responses to customer issues. Directly negotiate with customer senior leadership, coordinate with international government regulatory agencies, and task integrated supply chain resources. Coordinate alignment and integration activities to control costs while maintaining capabilities. Develop and deploy a global Lean/Six Sigma strategy. Manage global quality teams supporting development, production, and customers in locations worldwide. Develop and deploy life cycle and development models. Deliver big data tools and analytic tools to predict customer trends and quality issues. Deliver global quality strategies to drive reductions in warranty expenses and CoPQ to increase Operating Earnings year-over-year. Integrate two quality systems and cultures into one.
-
-
-
-
Senior Director of Global Quality
-
Jan 2012 - May 2013
Senior Executive responsible for Customer Loyalty, Quality, Compliance, and Productivity for a $5B global business. Manage global quality teams supporting development, production, and customers in locations worldwide. Deliver software, hardware and services quality strategies. Develop and deploy life cycle and development models. Deliver big data tools and analytic tools to predict customer trends and quality issues. Deliver global quality strategies to drive reduction in warranty expense and CoPQ to increase Operating Earnings year-over-year. Lead the reorganization, alignment, and retooling of quality and continuous improvement systems. Lead change management. Maintain TL9000 certification while improving customer loyalty.
-
-
-
-
Senior Director, Quality
-
Jan 2011 - Jan 2012
Senior Executive responsible for Quality, Continual Improvement, and Customer Satisfaction efforts for a $3B portion of Motorola Mobility as a member of the Business senior leadership team. Manage a global quality team with responsibility for global network equipment quality, repair, and overall customer satisfaction in Europe and Asia. In coordination with global customers, develop software new product introduction strategies. Develop strategies to improve repair and reverse logistics performance. Lead mufti-functional teams to improve customer satisfaction and lower the total cost of ownership. Work with customers’ executive teams to improve relationships and champion initiatives to reduce customer failures and improve customer loyalty. Develop the quality vision and strategies and champion business-wide improvement efforts that result in lower total Cost of poor Quality (CoPQ). Implement Software Quality strategies. Develop Big Data systems and tools to predict customer loyalty and quality trends.
-
-
Senior Director, Quality
-
Oct 2009 - Jan 2011
Provide executive, end-to-end quality leadership and strategic direction for a $2B business focused on network infrastructure equipment. Develop, align, and implement comprehensive business strategies to align the organization to customer expectations to drive market share growth and increased profitability. Work with the senior leadership team, their direct reports, and global customers to understand the current and future business and marketplace environments. Monitor and analyze industry trends to identify potential growth opportunities, challenges, and disruptors. Champion initiatives to leverage opportunities and counter challenges. Lead customer focused teams to better understand the customer while supporting their current and future needs.
-
-
Director of Quality Strategy and Continual Improvement
-
Nov 2008 - Oct 2009
Design, develop, and deploy quality, customer, and sustainability strategies for a $10B global company in support of the Chief Quality Officer and the Chief Technology Officer. Provided executive guidance, program management, and oversight on critical business projects in a matrix environment. Lead projects and programs in support of the integration of two global $5B businesses. Integrate two quality and continuous improvement systems while driving improved efficiency and increased customer satisfaction.
-
-
Consultant Master Blackbelt / Director, Business Improvement
-
Oct 2006 - Nov 2008
Mentor, train, and lead business improvement resources and teams. Project manage cross-business projects. Design, develop and implement the first Quality Management System (QMS) for the Motorola Home Sector. Implement business systems, processes, measures, and controls for a $5B business. Identify and implement sector-wide Key Process Indicators (KPI). Lead the first TL9000 and ISO 9001 certification for the Motorola Home sector, achieving full certification in less than six months.
-
-
Site Leader
-
Jan 2002 - Oct 2006
Profit and loss responsibility for a $50M year business. Lead business manager of the optical product development and manufacturing site with over 100 employees. Responsible for all aspects of business operations. Lead the product transition from internal manufacturing resources to overseas locations. Lead the transition of development and design functions to a new center of excellence for optics.
-
-
-
-
Intelligence Officer (Retired)
-
Dec 1980 - Jun 2004
Multiple positions of progressive responsibility advancing from Aviation Recruit (Enlisted) to Officer-in-Charge ONI-4 Pacific (Commissioned Officer). Command teams of interrogators in support of the Office of Naval Intelligence’s Human Intelligence Collection requirements. Debrief technical experts, enemy combatants, and senior foreign officers on critical subject matter. Analyze foreign nations’ economic, social, military, and political structures and technological capabilities and assess probable applications. Anticipate the probable future actions of foreign nations and organizations based on research and analysis and make recommendations and risk assessments to senior military and government leadership. Develop and present comprehensive presentations and written reports on research findings. Security Clearance: Top Secret (SCI) (Not Current). Multiple Military Decorations and Commendations.
-
-
-
Synchronous
-
United States
-
Insurance
-
Vice-President, Operations
-
Oct 2000 - Jan 2002
Acquired by Motorola in January of 2002. Responsible for the management of customer services, marketing and sales support, OEM relationships, Contracts, Engineering Development, Program Management, Manufacturing, Quality, and Materiel organizations in a telecommunications transport company specializing in optical solutions. Develop strategies that result in competitive advantages in the marketplace. Manage design team leaders in the development of new technologies and products for use in telecommunications networks. Apply strategic vision and direction to the Operations organization to identify company core-competencies and opportunities for current product enhancement, new product penetration, and displacement of encroaching competitors.
-
-
-
Gigatronics
-
United Kingdom
-
1 - 100 Employee
-
Director, Manufacturing and Materiel
-
May 1999 - Oct 2000
Responsible for manufacturing and materiel operations in a RF telecommunications company providing product to commercial and military customers. Lead teams producing products to high-mix-low-volume and low-mix-medium-volume production requirements. Fuse Just-in-Time, Quick Reaction, Flow, Pull, Toyota systems, Kanbans, and kit-based production methodologies to maximize production potential while minimizing costs. Lead design teams developing new technologies and products for use in telecommunications and wireless data distribution. Prepare and implement budgets, cost reduction, cost control, and design-for-cost programs. Directly manage purchasing, procurement, planning, inventory control, logistics, warehousing, sub-contractor management and production control in an MRP environment. Directly manage manufacturing, manufacturing engineering, test engineering, rapid-prototyping, customer services, Indirectly manage quality and information services. Manage new product development teams.
-
-
-
-
Manager of Manufacturing
-
Jul 1985 - May 1999
Responsible for all manufacturing operations, scheduling, and planning. Lead three teams producing multiple products including laser and radio guidance systems to commercial, government, and military customers. Prepare and implement budgets, schedules, cost-to-manufacture estimates, and other production reports. Design and implement complex automated manufacturing processes. Develop manufacturing and quality instructions, procedures, and policies. Analyze and develop manufacturing and quality control practices and methods. Design, develop, and implement methodologies such as Lean, Just-in-Time (JIT), Quick Reaction (QRM), Flow, Pull, Toyota systems, Kanbans, and kit-based production methodologies.
-
-
Education
-
California Lutheran University
MBA, Information Systems Design -
California State University, Northridge
BA, Pre-Law -
Moorpark College
AA, General Education
Community
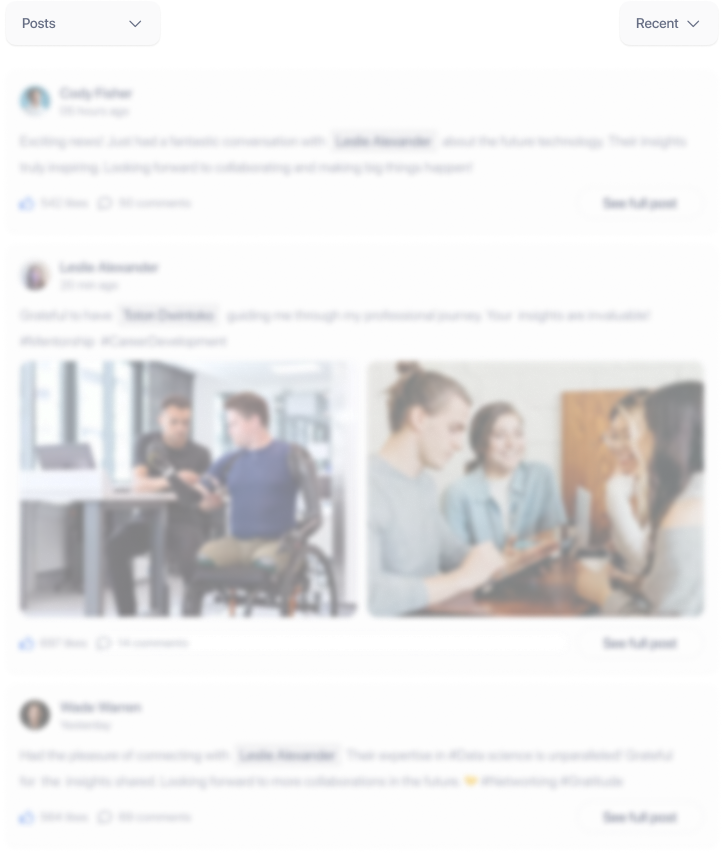