
Raven Mayhall
Regional GMO at Sunbelt Forest Products- Claim this Profile
Click to upgrade to our gold package
for the full feature experience.
Topline Score
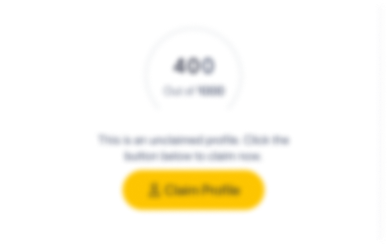
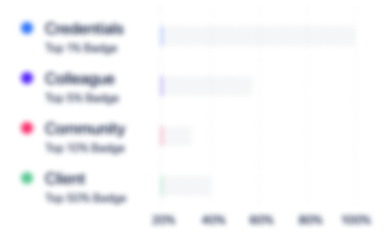
Bio


Experience
-
Sunbelt Forest Products
-
United States
-
Wholesale Building Materials
-
1 - 100 Employee
-
Regional GMO
-
Jan 2022 - Present
-
-
Plant Manager
-
Jun 2020 - Jan 2022
Steer and direct a Production Facility that generates $100M in annual revenue.
-
-
-
EFI Automotive
-
France
-
Motor Vehicle Parts Manufacturing
-
400 - 500 Employee
-
Plant Manager
-
Jan 2017 - Jun 2020
Steer and directed plastic Tier-1 Automotive manufacturing operations that generate $50M in annual revenue. Establish operational policies and implement process improvements to ensure superior quality and outstanding output of custom molded and extruded parts. Directly supervise 4 managers (Production Supervisor, Logistics, Facilities and Safety Manager.) overseeing 170+ exempt and non-exempt employees. Design and implement coaching and training programs to develop staff, facilitate efficiency, and improved performance. Manage operational and capital expense budgets exceeding $1.5M. Ensured adherence to strict quality control procedures.• Key user in M3 (MRP system).• Hands-on experience working with Motoman Robotics, Batten field & Arburg Injection molding presses.• Through developing staff resulted in reduction of scrap (Overall 6% • 1.5%), non-conforming material and unidentified usage of material (3% • .05) by implementing action plans from root cause analysis projects with due dates on top offenders in cost.• Improved Labor Efficiency from 80% • 95% by implementing production tracking system • overall scrap reduction • reduction machine of break downs. = positive result on P&L & Labor Efficiency• Boosted on-time and error-free service rate (OTS) from 75% • 100% by improving machine efficiency, implementing a master production schedule with production work center schedules.• Increased Raw Material Supplier OTD from 80% • 100% by working with offending suppliers to provide action plans with due dates for improvement + daily follow up to insure 100% OTD is sustained.• Reduced production staff by 40 while maintaining production levels through a redesign of operational processes, improved training and staff utilization.• Implemented Just-in-Time (JIT) production methodology to control costs and inventory, resulting in a 15% improvement in efficiency.
-
-
-
Marelli
-
Japan
-
Motor Vehicle Manufacturing
-
700 & Above Employee
-
Production Shift Manager
-
Jan 2016 - Jan 2017
Managed production team in a Tier-1 fast-paced automotive manufacturing environment. Key areas: 5S, safety, efficiency and quality. Managed production team in a Tier-1 fast-paced automotive manufacturing environment. Key areas: 5S, safety, efficiency and quality.
-
-
-
Hexcel Corporation
-
United States
-
Aviation & Aerospace
-
700 & Above Employee
-
Production Shift Supervisor
-
Feb 2011 - Jan 2016
Headed product changes to improve changeover performance and reduce changeover time. Held hands-on training sessions for new and less experienced employees. Relayed training results to Production Manager. Led troubleshooting efforts to overcome process-related issues. Identified opportunity areas to improve process safety and ergonomics. Ensured safety and ISO 9001 compliance. Headed product changes to improve changeover performance and reduce changeover time. Held hands-on training sessions for new and less experienced employees. Relayed training results to Production Manager. Led troubleshooting efforts to overcome process-related issues. Identified opportunity areas to improve process safety and ergonomics. Ensured safety and ISO 9001 compliance.
-
-
Community
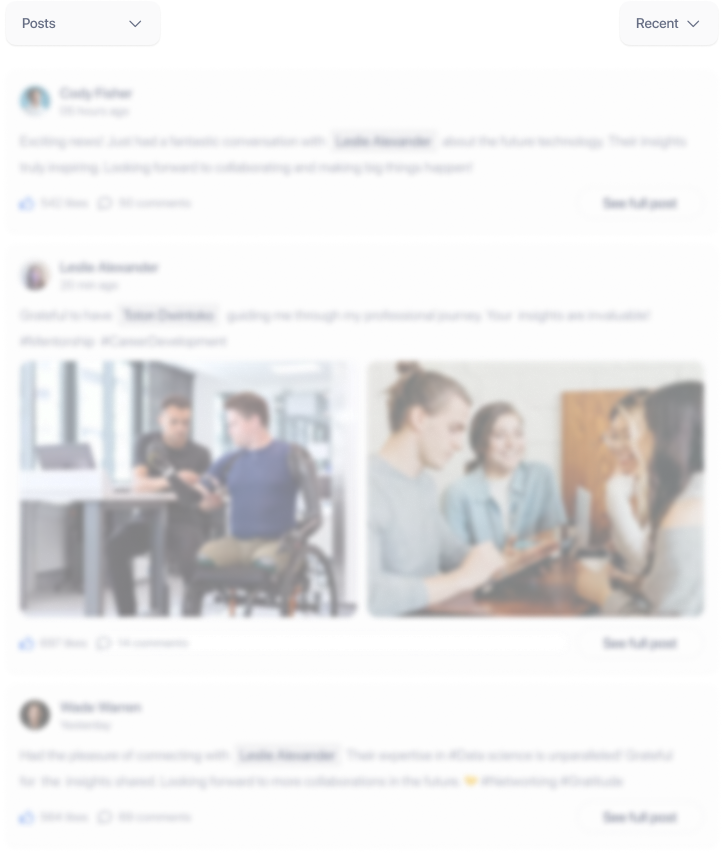