Raul Vera
Maintenance Technician at Axelgaard Manufacturing Company- Claim this Profile
Click to upgrade to our gold package
for the full feature experience.
Topline Score
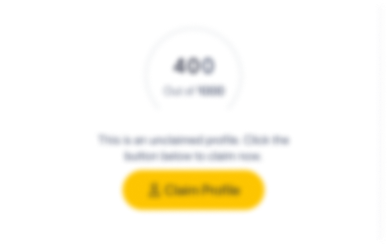
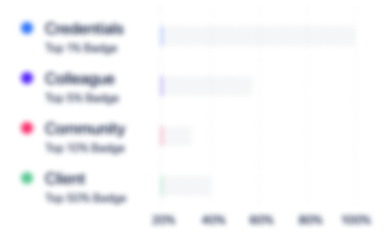
Bio


Credentials
-
Certificate of completion- Dispensing Liquefied Petroleum Gas
All American PropaneJun, 2015- Nov, 2024 -
Certificate of completion- Permit Required Confined Space Operations
Hands On Technical Training L.L.C.May, 2013- Nov, 2024 -
Certificate of Completion- Permit Required Confined Space Awareness
Hands On Technical Training L.L.C.Apr, 2013- Nov, 2024 -
Certificate of completion- Boom lift & Scissor Lift Training
Scissor Lift Academy, IncAug, 2021- Nov, 2024 -
Certificate of completion- Class 1-7 Powered Industrial Trucks
Forklift Academy, IncAug, 2021- Nov, 2024
Experience
-
Axelgaard Manufacturing Company
-
Medical Equipment Manufacturing
-
1 - 100 Employee
-
Maintenance Technician
-
Jan 2022 - Present
-
-
-
Paulson Manufacturing Corp.
-
United States
-
Plastics Manufacturing
-
1 - 100 Employee
-
Maintenance Manager
-
Oct 2020 - Oct 2021
Scheduling and overseeing all maintenance-related work by managing a team of maintenance technicians, ensuring that all maintenance operations are done in accordance with company policy and OSHA guidelines. Ensuring the facility satisfies all industry regulations. Forecasting, ordering, and price negotiation for spare parts inventory, developing and implementing a (proactive) maintenance strategy, coordinating the completion of complex repairs. Hiring subcontractors for specialized maintenance work and signing off. Looking for new ways/tools/assets to improve productivity and cut costs, Minimizing down time and increasing production.
-
-
Maintenance Mechanic
-
Apr 2019 - Oct 2020
Maintained and or repaired all mechanical equipment and building facilities, such as, Industrial air compressors, Vacuum pumps, paper cutters, hydraulic presses, sewing machines, air rivet guns, motors, electric hoists, pressure washer, air conditioning units, drill presses, lawn mowers, chainsaw, weed eater, irrigation system, automated gates, garage doors, pumps, welders, forklifts, scissor lift, all terrain forklift, Tig welding mild steel, stainless steel, and aluminum. Mig welding mild steel and stainless steel, repaired plumbing in facilities, repaired damaged water lines, faucets, replaced and repaired toilets, sinks. Electrical, running of new circuits, upgrade lighting, LED retrofits, replace fixtures, install light switches, wall outlets, trouble shoot failing systems. troubleshoot Injection molding machines, mold controls, CNC machines, CNC chiller units. Exhaust fans, solder electronics, repair conveyor belt systems, operated forklift, scissor lift, all terrain forklift. managed time very well to prevent to much downtime and help increase production.
-
-
-
Michelsen Packaging
-
United States
-
Packaging and Containers Manufacturing
-
1 - 100 Employee
-
Tooling Technician
-
Oct 2016 - Jan 2019
Manufacture molds using epoxy and hardeners to produce the forms that make molded fiber trays. Form wire mesh screens using a hydraulic press, and spot weld to finalize the mold. Perform final quality control check of forms by removing inconsistencies using air grinding tools. Clean, repair, and replace the forms on a weekly maintenance routine. Adjust and calibrate using feeler gauges to properly align molds. Responsible for building, installing, servicing of tray dispensing machines to apple packing warehouses statewide, Responsibilities include basic maintenance, diagnostics test, check performance, test damaged parts to determine weather major repairs are necessary for optimal performance of machinery.
-
-
Maintenance Mechanic
-
Oct 2011 - Oct 2016
Ensured operation of machinery and mechanical equipment by completing preventative maintenance requirements, repaired or replaced broken components on motors, conveyor systems, molding machines, industrial size gas dryers, hydraulic presses, large storage tanks, chemical pumps, hoists, industrial pressure washer, industrial air compressors, and cooling towers. Completed work orders as assigned. Read technical manuals to understand equipment and controls. Disassemble machinery and equipment when problems occurred, locate sources of problems by observing mechanical devices in operation; listening for problems; using precision measuring and testing instruments. Detect minor problems by performing basic diagnostic tests, clean and lube machinery, adjust and calibrate equipment and machinery to optimal specifications. Fabricated parts by performing various types of welding like TIG and MIG. Provided mechanical maintenance information by answering questions and requests to supervisors. Prepared mechanical maintenance reports by collecting, analyzing and summarizing information and trends. Maintained a safe and clean working environment by complying with procedures, rules, and regulations. Operated fork lift, scissor lift, snorkel lift for daily operations. Maintained continuity among shift operators by documenting and communicating repairs, irregularities, and the continuing needs of the machinery.
-
-
Machine Operator- Molder
-
Oct 2007 - Oct 2011
Ran wet end operations and machinery to make fiber molded trays, Tasks included operation of molding drums by using (HMI) Human Machine Interface program on computer systems, making proper adjustments to achieve consistency and thickness of product, supervision of machinery for optimal performance, fix and or report any equipment failure to proper personnel, Inspected product to make sure it met industry standards. Managed wet end chemistry and equipment, such as various chemical pumps and mixing devices, Replenished chemicals as needed and disposed of them according to hazardous waste regulations, Ran product through industrial sized drying ovens before finalizing end product. Adjusted controls on HMI to achieve proper set points. Tracked trends on computer to optimize production.
-
-
Machine Operator- Stock Prep
-
Oct 2004 - Oct 2007
Ran wet end operations for the preparation of raw materials to be used for molded fiber trays. Tasks included the unloading of recycled bales of paper from shipping containers by operating a forklift, mixing and adjusting percentages of raw materials for proper recipe and consistency requirements, adding raw materials to a skip hoist to weigh proper kg's before being dumped in to a mixing pulper. Made adjustments by using a custom computer program, Human Machine Interface (HMI) to monitor trends, monitor equipment for optimal performance, repaired and or report any failures to proper personnel. Logged operations for the day and reported records and trends to the next shift.
-
-
Product Handler- Supervisor Assistant
-
Dec 2001 - Oct 2004
Handled trays at dry end operations, monitored for jams of conveyor belts. Controlled proper count of product, oversaw weights and moistures levels were within set standards and recorded on computer, Inspected product for any defects, informed machine operator of any product issues, offloaded it from conveyors to be placed into air presses to be compacted to proper size, removed and placed on separate conveyor ready to be put on pallets. set final product on pallets with proper sizes to be sent to next stage of production. Assisted supervisor and machine operators with cleaning, lunch coverages, record production numbers, place pallets with product at final destination.
-
-
Community
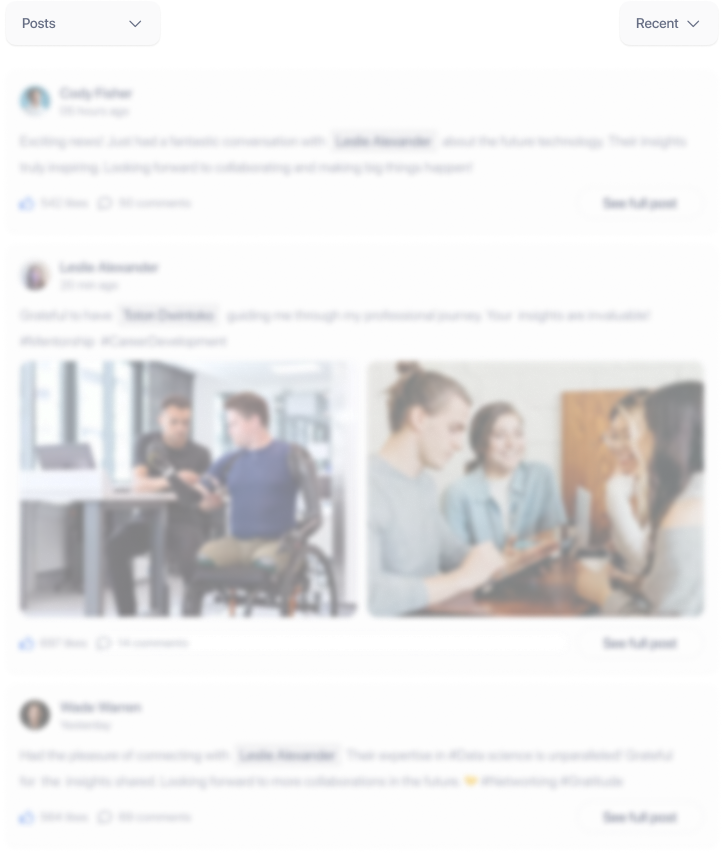