Randy G Brunnet
Operations Manger at RPC Electronics- Claim this Profile
Click to upgrade to our gold package
for the full feature experience.
Topline Score
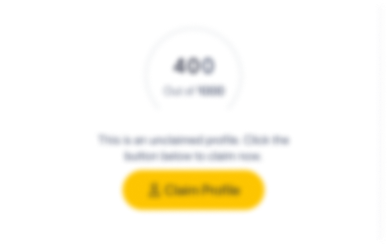
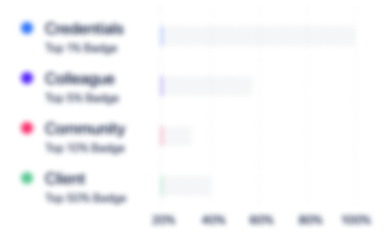
Bio

Rick Link
Randy was our 3rd shift supervisor for our Laser Operation. Randy did an excellent job supervising his shift. He treated the employees with respect and held them accountable. He was fair and consistent and quickly gained the trust and respect of the entire organization.

Rick Link
Randy was our 3rd shift supervisor for our Laser Operation. Randy did an excellent job supervising his shift. He treated the employees with respect and held them accountable. He was fair and consistent and quickly gained the trust and respect of the entire organization.

Rick Link
Randy was our 3rd shift supervisor for our Laser Operation. Randy did an excellent job supervising his shift. He treated the employees with respect and held them accountable. He was fair and consistent and quickly gained the trust and respect of the entire organization.

Rick Link
Randy was our 3rd shift supervisor for our Laser Operation. Randy did an excellent job supervising his shift. He treated the employees with respect and held them accountable. He was fair and consistent and quickly gained the trust and respect of the entire organization.

Experience
-
RPC Electronics Inc.
-
United States
-
Appliances, Electrical, and Electronics Manufacturing
-
1 - 100 Employee
-
Operations Manger
-
Aug 2008 - Present
-
-
-
Silicon Turnkey Express
-
Computer Hardware Manufacturing
-
1 - 100 Employee
-
Operations Manager
-
Aug 2008 - Oct 2010
-
-
-
Norman Noble, Inc.
-
United States
-
Medical Equipment Manufacturing
-
100 - 200 Employee
-
Supervisor
-
Jan 2006 - Apr 2007
·Supervised, third shift employees (15), working with Lasers to produce medical items. ·Identified opportunities for continuous improvement, and participated in projects related to those continuous improvements. ·Maintained a production efficiency of 98% ·Trained employees on Work Instructions and Procedures. ·Supervised, third shift employees (15), working with Lasers to produce medical items. ·Identified opportunities for continuous improvement, and participated in projects related to those continuous improvements. ·Maintained a production efficiency of 98% ·Trained employees on Work Instructions and Procedures.
-
-
-
-
Production Manager
-
Aug 2002 - Sep 2004
·Maintained work flow by monitoring steps of the process, personnel and resources; studying methods; implementing cost reductions; developing reporting procedures and systems; initiating and fostering a spirit of cooperation within and between departments.·Completed production plan by scheduling and assigning personnel; accomplishing work results; establishing priorities; monitoring progress; revising schedules; resolving problems.·Provided information by compiling, initiating, sorting and analyzing performance records and data.·Created and revised systems and procedures by analyzing operating practices, record-keeping systems, forms of control and budgetary and personnel requirements.·Improved repair process by re-designing work space to allow testing of multiple products by each technician. ·Member of implementation team for new ERP system. Extensive knowledge of JD Edwards.·Trained 20 Associates on the workings of JD Edwards
-
-
-
-
Production Manager
-
2001 - 2001
·Managed the assembly and test facilities to provide maximum output while maintaining exceptional quality. ·Developed assembly instructions for all products. ·Developed scheduling and shop floor tracking procedures. ·Defined and documented all operational processes. ·Working knowledge of Great Plains and Sieble Software. ·Managed the assembly and test facilities to provide maximum output while maintaining exceptional quality. ·Developed assembly instructions for all products. ·Developed scheduling and shop floor tracking procedures. ·Defined and documented all operational processes. ·Working knowledge of Great Plains and Sieble Software.
-
-
-
Packard Bell NEC
-
Computer Hardware Manufacturing
-
1 - 100 Employee
-
Operations Manager Service Logistics
-
1995 - 2000
·Responsible for Yearly Budgets with Quarterly reviews, for a Division of 130 employees. ·Managed a Production floor for Computer Manufacturing, this included receiving, Purchasing, QA, Inventory Control, and overall Facility control. ·Directed the design of a new facility to house the Service Logistics Division. ·Managed the division toward ISO 9000 and 14000 certification. ·Hired a total of 200 employees, this included 8 Supervisor, regular and temporary work force. ·Managed yearend Inventory for division, this included the training of over 50 employees in auditing, counting, and reconciliation.
-
-
-
Packard Bell
-
France
-
Computer Hardware Manufacturing
-
1 - 100 Employee
-
Manager Production
-
1995 - 2000
·Relocated Monitor division from Southern Ca to Northern Ca. ·Negotiated Monitor repair contracts with overseas companies. ·Managed the Procurement of Monitor spare parts from overseas companies ·Negotiated shipping contracts, for service returns using Airborne, Federal Express and UPS. ·Increased and maintain a same day shipping requirement of 99% plus. ·Reduced inventory levels from $8 million to $3.5 million. ·Relocated Monitor division from Southern Ca to Northern Ca. ·Negotiated Monitor repair contracts with overseas companies. ·Managed the Procurement of Monitor spare parts from overseas companies ·Negotiated shipping contracts, for service returns using Airborne, Federal Express and UPS. ·Increased and maintain a same day shipping requirement of 99% plus. ·Reduced inventory levels from $8 million to $3.5 million.
-
-
-
-
Manager, Central Service Center
-
1993 - 1994
·Directed the design and opening of a new self contained building to house the Central Service Center, to process the entire return and repair operation. ·Reduced turn-around time from 21 days to an average of 3 days in house. ·Managed a $200,000 on-site inventory of Apple repair parts. ·Directed the design and opening of a new self contained building to house the Central Service Center, to process the entire return and repair operation. ·Reduced turn-around time from 21 days to an average of 3 days in house. ·Managed a $200,000 on-site inventory of Apple repair parts.
-
-
-
Everex
-
Computer Hardware Manufacturing
-
1 - 100 Employee
-
Manager, Product Service Center
-
1986 - 1992
·Directed the design and development of a customized Return Material Authorization tracking system. This database contained all information on customer returns sent in for repair. It also collected information on the product as it was received, tested, repaired, QA, packaged, and shipped back to the customer. This eliminated paperwork while allowing for on-line tracking of the repair. ·Promoted and directed the design of RF technology, with use of our barcode systems, this increased the turn around time for the cycle count of on-site inventory. -Enhanced the RMA system to include pre-authorization for out-of-warranty repairs. · Negotiated contract requirement to improve processing time, cost, and quality of repairs.·Trained 500 employees in Eltro Static Discharge Classes.
-
-
-
-
Product Support Specialist
-
1983 - 1986
·Wrote technical bulletins and trained new Support Representatives. ·Assisted customers in the installation and trouble-shooting of various computers and their peripherals. ·Troubleshoot and repaired peripherals down to component level. ·Wrote technical bulletins and trained new Support Representatives. ·Assisted customers in the installation and trouble-shooting of various computers and their peripherals. ·Troubleshoot and repaired peripherals down to component level.
-
-
Education
-
ETI
Associate, Electronic Engineering Technology -
Cleveland State University
-
Collinwood High School
Electronics
Community
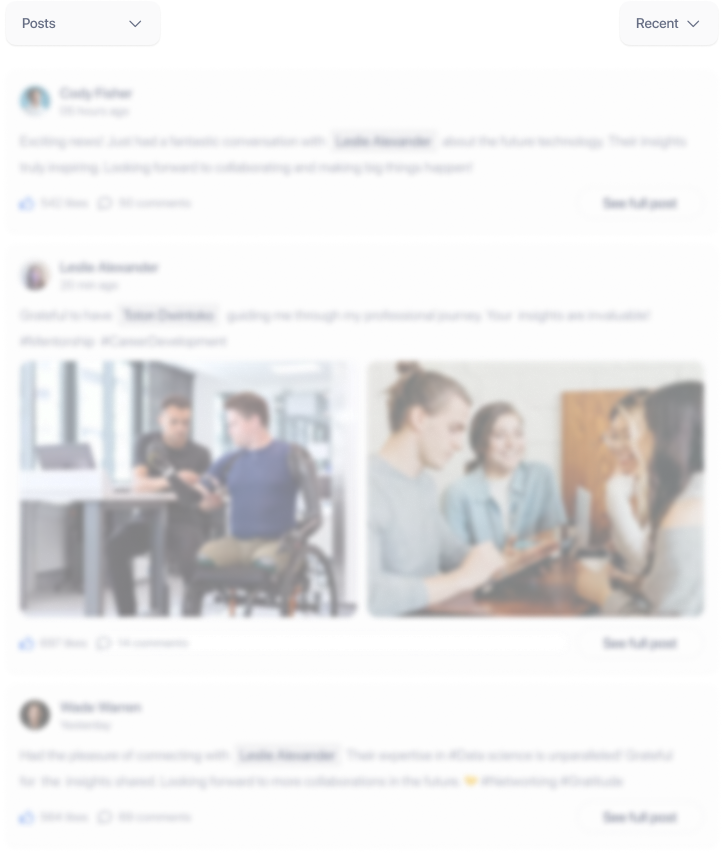