RANDY PEREZ GONZALES, RPh, MBA
Compliance Services Manager at Pascual Laboratories, Inc.- Claim this Profile
Click to upgrade to our gold package
for the full feature experience.
-
English Professional working proficiency
-
Filipino Native or bilingual proficiency
Topline Score
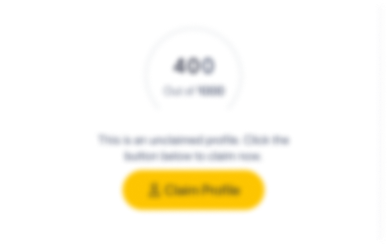
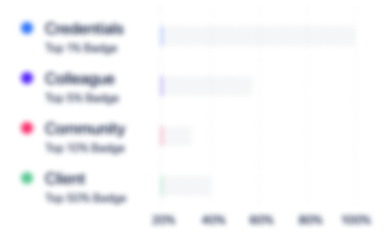
Bio
0
/5.0 / Based on 0 ratingsFilter reviews by:
Credentials
-
Registered Pharmacist
Philippine Professional Regulation CommissionJan, 1996- Sep, 2024
Experience
-
Pascual Laboratories, Inc.
-
Philippines
-
Pharmaceutical Manufacturing
-
200 - 300 Employee
-
Compliance Services Manager
-
Sep 2017 - Present
Reporting to the Director of Quality Affairs and Product Development Division (QAPD), performs specific quality monitoring and periodic audits in the organization in order to check if the organization follows quality management systems properly. Conducts GMP, ISO 9001 and Halal related-trainings. Provides assistance, guidance, education and training to different departments regarding compliance to GMP (PIC/S and WHO), ISO 9001, Business Social Compliance Initiative (BSCI) and Halal Assurance guidelines and standards.
-
-
Deputy Integrated Quality Management Representative (DIQMR)
-
May 2015 - Present
Reporting to the PascualLab’s Supply Group Quality Management Representative (QMR) / Director of Quality Affairs and Product Development Division (QAPD), provides assistance to QMR in managing the design, development, documentation and improvement and implementation of the quality management system (QMS). Reports on the performance of the management system by collating, summarizing, analyzing and reporting the overall results of QMS performance. QMS Development and Implementation Assists the Quality Management Representative (QMR) and PascualLab’s management team in ensuring quality management system processes are established, implemented and maintained. Determines the effectiveness of the QMS and facilitates internal communication of QMS within the organization through internal quality audit and management review. QMS Feedback and Improvement Reports on the performance and where improvements are needed to PascualLab’s management team. Helps identify, implement and manage continual improvement programs in the quality management system. QMS Certification Activities Assists in ensuring that PascualLab third party accreditations are obtained and maintained. QMS Documentation Prepares Management Review agenda and minutes of the meeting. Provides support in ensuring all quality related company policies, procedures and work instructions are documented in a clear, simple and concise manner.
-
-
H e a d , I n t e r n a l Q u a lit y A u d it
-
Oct 2014 - Present
Reporting to the PascualLab’s Supply Group Quality Management Representative (QMR) / Director of Quality Affairs and Product Development Division (QAPD), manages the entire internal quality audit (IQA) program of PascualLab manufacturing plant. Performs the selection, training and management of the internal quality auditors. Establishes the objective and extent of the internal quality audit program. Sets the internal quality audit plan or schedule for the organization. Determines and establishes the resources, responsibilities and procedures for the IQA program. Ensures the efficient and effective implementation of the IQA program. Performs the training and appraisal of performance of the IQA team. Safe keeps and maintains confidential and appropriate IQA documents. Determines the appropriateness and effectiveness of the corrective actions related to the audit. Ensures the timely conduct of audit and issuance of IQA report based on the defined audit plan or schedule.
-
-
Assistant Manager, GMP/Audit
-
Feb 2014 - Sep 2017
Reporting to the Director of Quality Affairs and Product Development Division (QAPD), performs specific quality monitoring and periodic audits in the organization in order to check if the organization follows quality management systems properly. Conducts GMP training and provides support to the management in all GMP-related trainings using various tools and techniques to comply with the current GMP standard. Provides assistance, guidance, education and training to different departments regarding GMP compliance.
-
-
Compliance Services Supervisor
-
Oct 2011 - Feb 2014
Self-Inspection (Internal Quality Audit)• Prepared an annual self-inspection or internal quality audit program.• Reviewed and revised internal quality audit checklist using PIC/S and ISO 9001:2008 guidelines.• Conducted and assisted periodic audit of all departments and vendors as required by internal audit schedule and facilitated remediation activities.• Participated in the implementation of best manufacturing practices.• Contributed in the development and implementation of quality management strategy and plans.• Assisted in the implementation of Good Manufacturing Practice (GMP) remediation program.External Inspection• Coordinated internal and external audits.• Assisted in the monitoring and review of the corrective and preventive action (CAPA) submitted by the auditee organization.Third Party Manufacturing Qualification• Facilitated qualification of toll or third party manufacturing companies, suppliers and third party laboratory testing.Training• Educated employees in GMP through training activities and conducts echo seminar to PascualLab (PLI) after attending an outside seminar.• Ensured compliance with PLI standard operating procedures (SOP) as well as Philippine Food and Drug Administration (FDA) guidelines to ensure regulatory requirements are met and strictly adhered to.• Provided proper guidance to employees in relation to regulatory concerns, quality trends and GMP.
-
-
Internal Quality Auditor
-
Sep 2002 - Oct 2011
Implemented all the activities indicated in the audit program of the Quality Affairs Division; have determined the effectiveness of the Quality Management System (QMS) in meeting the quality objectives. • Have performed internal quality audit, reviewed the document, prepared audit report and made follow-through of corrective and preventive action submission and implementation based on the agreed timeline.• Assisted in vendor or supplier audit in order to assess the quality of the materials based from the existing GMP standard.
-
-
Production Supervisor
-
Feb 2002 - Oct 2011
Solid Dosage Form Department (Synthetic, Penicillin and Cephalosphorin and Herbal Section)Planning• Arranged the daily/weekly production schedules to meet the target/delivery.• Have regularly coordinated with Material, Production Planning and Control (MPPC) and other support groups production schedule in order to attain:1. 95 -100% production hit rate vs. schedule.2. 95 -100% capacity utilization vs. available capacity.Supervision• Directed and scheduled 25-40 personnel (regular and casual employees).• Have analyzed and studied operation bottle neck and made necessary recommendation to streamline process.• Ensured that manufacturing procedures are accomplished following the approved Standard Operating Procedures (SOP) and GMP guidelines.• Controlled the labor and overtime cost and overhead, materials and supply usages.• Implemented deviation management or change control procedure and good manufacturing practices (GMP) in the processing of products.• Integrated quality principles, safety and health precautions to direct reports.Documentation• Monitored and ensured on-time accomplishment and submission of Batch Production Record (BPR) and production-related reports.• Kept scorecard and training records of direct report.Resource Management• Monitored and controlled budget within the approved level.• Implemented the company policies, rules and regulations to direct reports.• Improved production output and controlled expenses vs. target/benchmark.• Conducted one on one performance appraisal and counsel/motivates subordinates.• Have optimized production batches through economy of scale strategy.
-
-
Document Controller/Record Keeper
-
Feb 2002 - Oct 2011
Have organized, improved and maintained the documentation system of the Solid Dosage Form Department; have controlled the accessibility to the highly confidential and significant documents and quality records.• Pioneered and maintained sound documentation system of the Solid Dosage Form Department in compliance to ISO 9001:2000.• Prepared and assisted in the validation of Standard Operating Procedure (SOP) covering drug production general procedures, machine and equipments operation and cleaning procedures.• Controlled the accessibility of all highly classified and important drug production documents in the department.
-
-
Property Custodian/Coordinator
-
Feb 2002 - Feb 2007
Maintained list of fixed assets (FA) in the Solid Dosage Form Department and monitored its transfer, retirement and disposal.• Have maintained list of fixed assets (FA) located inside the drug production area such as tablet, capsule, and powder machines and equipments.• Assisted in the fixed assets counting together with the auditors of the accounting department of the company.• Received new fixed asset acquisitions and monitored movement of fixed assets within the area of responsibility.• Monitored and properly documents retirement and disposal of fixed assets.• Monitored fixed assets which are taken out of the company premises for repair, fabrication and the like. • Maintained the lists of other non-capitalizable company assets within the area of responsibility.
-
-
Quality Control Inspector/Analyst
-
Jul 1996 - Feb 2002
Performed sampling,inspection and evaluation of pharmaceutical products of various dosage forms; ensured that products being released were of good quality and complied with the established specifications.On a daily basis, the following tasked were carried out:• Counterchecked line clearances before every drug production operation.• Conducted independent in-process drug product sampling and testing according to established in-house and internationally accepted drug analysis procedures.• Sampled and evaluated finished drug product packages and collected retention sample according to established procedures. • Performed GMP audit and inspection inside the drug production area.• Reported all the results of drug product tests and evaluations and other related report to the Quality Control supervisor.• Prepared and submittedGMP vigilance report and deviation investigation report in all cases of GMP violation based on the GMP guidelines of the Food and Drugs Administration (FDA).• Prepared finished drug product disposition advice slip to all finished goods ready for releasing and delivery.• Performed daily calibration and maintenance of quality control laboratory equipment based from established procedures.• Prepared Standard Operating Procedure (SOP) of laboratory equipment (cleaning, operation, and calibration procedures).
-
-
-
-
Pharmacist-in-charge
-
Oct 1995 - May 1996
Supervised all production activities from compounding (granulation) to packaging stage according to established procedures, specifications and GMP requirements and reported any deviation on standards in order to ensure the effective and timely production and delivery of quality products at optimum cost; supervised and scheduled 6 employees.On a daily basis, the following tasked were carried out:• Planned and prepared production schedule.• Coordinated with the stock clerk regarding raw and packaging materials and finished product inventory.• Monitored the productivity of production personnel.• Conducted in-process production inspection and monitoring.• Conducted 100% inspection of all finished products before transferring to warehouse.• Counterchecked all computations of manufacturing order (MO) prior to raw materials dispensing.• Implemented good manufacturing practices in all stages of drug production.• Assisted in the conduct of time and motion study; established man-hour standard in all the stages of production activities.
-
-
Education
-
Manila Central University
Master in Arts of College Teaching (MACT), Pharmacy Education -
Bulacan State University
Master of Business Administration (MBA), 1.25 -
Manila Central University
Bachelor of Pharmacy (BPharm), 2.5 -
Governor Andres Pascual College (formerly High School) in Navotas City
Elementary to High School, 90
Community
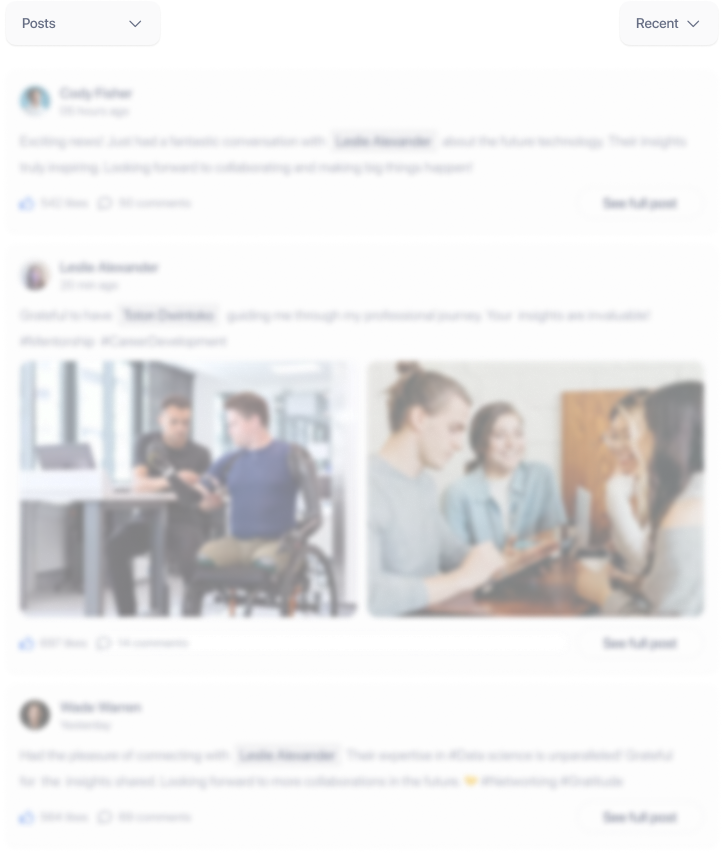