Randii Waddell
Project Manager at Red Wing Ignite- Claim this Profile
Click to upgrade to our gold package
for the full feature experience.
Topline Score
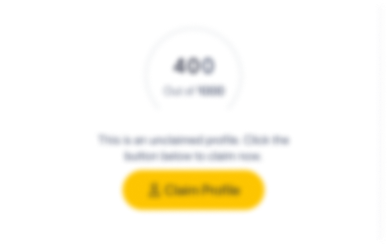
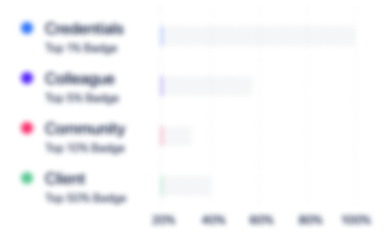
Bio


Credentials
-
Lean Certification
University of Kentucky Lean Systems ProgramMar, 2018- Oct, 2024 -
PMP (Project Management Professional)
Project Management InstituteJun, 2016- Oct, 2024 -
CPIM (Certified in Production and Inventory Management)
Association for Supply Chain ManagementJan, 2013- Oct, 2024
Experience
-
Red Wing Ignite
-
United States
-
Civic and Social Organizations
-
1 - 100 Employee
-
Project Manager
-
Nov 2022 - Present
-
-
Entrepreneurial Specialist / Lead
-
Mar 2022 - Oct 2022
-
-
-
-
Operations & Process Coach
-
Oct 2022 - Present
-
-
-
-
Owner
-
Mar 2022 - Present
Helping small businesses and nonprofits improve their processes through simplification, developing grant tracking tools, and building connections! Helping small businesses and nonprofits improve their processes through simplification, developing grant tracking tools, and building connections!
-
-
-
-
Small Business Owner
-
Jun 2019 - Present
Coordinate an annual summer woodworking camp for middle school girls. Design and create handmade wooden art. Teach woodworking classes to adults and youth. Emphasis is on providing women and girls opportunities to learn new skills and build confidence in themselves. Coordinate an annual summer woodworking camp for middle school girls. Design and create handmade wooden art. Teach woodworking classes to adults and youth. Emphasis is on providing women and girls opportunities to learn new skills and build confidence in themselves.
-
-
-
Red Wing Shoe Co.
-
United States
-
Manufacturing
-
700 & Above Employee
-
Planning & Scheduling Manager
-
Aug 2021 - Apr 2022
-
-
-
Asmodee Group
-
France
-
Computer Games
-
1 - 100 Employee
-
Business Transformation Manager
-
Oct 2020 - Aug 2021
-
-
-
Hearth & Home Technologies
-
United States
-
Manufacturing
-
500 - 600 Employee
-
Automation Project Manager
-
Oct 2018 - Mar 2020
I was responsible for prioritizing and leading automation projects that ranged from simple kaizen improvements up to $4.8 million dollar line renovations. To help streamline these projects, I implemented a new stage gate process flow for all aspects of creating equipment for the production lines and instituted a centralized idea submission process. While working with a great group of engineers and electricians, we were able to improve communication and our ability to meet milestone dates while designing and building parts, machines, and robots in an effort to improve Operations. I also identified a lack of training for the plant employees who were asked to step into initiative leadership roles so created a "Project Management 101" series to help train basic skills. Over 60 people attended this series to learn how to lead and communicate better!
-
-
-
Post Consumer Brands
-
United States
-
Consumer Goods
-
700 & Above Employee
-
Business Transformation Manager
-
Dec 2016 - Sep 2018
As a BTM, I was the liasion between 8 manufacturing plants to our IT department. In addition to leading all merger and acquisition efforts, I was responsible for organizing and leading the prioritization of all initiatives, documenting and improving process flows, and developing long range plans for manufacturing and quality systems. In my first year, I created a dashboard for plant sanitation departments which significantly improved their communication across teams, led an application rationalization exercise to ensure we fully understood all systems being used and supported in manufacturing and quality functions, and participated on multiple lean events to reduce costs including one that enabled $600k in cost savings by finding a way to reuse bulk totes. Based on my performance leading teams to improve processes and standardize workflows, I was asked to lead all business functions through our ERP upgrade in addition to leading the addition of a Canadian plant onto our existing systems. I was responsible for coordinating business requirements, cutover activities, contingency plans, and general communication through the business. Managed 2 direct reports.
-
-
-
-
IT Project Manager - Supply Chain
-
Oct 2015 - Dec 2016
My primary focus was leading the implementation of several multi year projects. I led the first archive of financial data in the history of the company (which was successful, thank goodness!) and managed the team responsible for redesigning all boot labels and replacing inline production printers. I was also involved in coordinating ERP upgrade efforts with our Norwegian business. While my position was within the IT department, I also went outside my sandbox to really learn how the boot making and leather tanning processes worked. In doing so, I identified a gap in how materials were being ordered at the plant that was causing continual shortages and high inventory on parts they did not use often. I worked with the plant team to implement some recommendations and we were able to reduce inventory by $800k in just three months.
-
-
-
Kraft Foods
-
United States
-
Food and Beverage Manufacturing
-
1 - 100 Employee
-
PCDM - Product Change Development Manager
-
Aug 2014 - Aug 2015
I loved the fast pace and high visibility this position provided as I led cross functional project teams through new item commercializations, reformulations, productivity initiatives, and packaging improvements. I provided leadership and Supply Chain expertise to help ensure a successful launch while getting great exposure to all other business functions. I was recognized by Oscar Mayer for my ability to improve team communication and manage over 50 projects simultaneously.While in this role I got to work on groundbreaking projects like launching Lunchables Juniors which was the first product Oscar Mayer made that wasn't located in the refrigerated section of a grocery store. I also led the launch of Lunchables Uploaded which was so successful ($125 million in sales the first year!) that our team had to quickly adapt to keep the shelves full.Key launches included: * Lunchables UPLOADED* P3 Meat Snacking* Lunchables Juniors * revitalization of Boca Naturals.Received the Oscar Mayer Business Unit award for leadership on new product launches.
-
-
Network Production Planner Mgr / HQ Materials Mgr
-
Oct 2008 - Aug 2014
I loved the true ownership of a business at a hands on level in this role as I was responsible for all aspects of inventory management across multiple categories. I had the opportunity to work with multiple business units, plants, co-manufacturers, and suppliers. I was recognized for my flexibility and ability to adapt when I took on additional roles covering 5 categories (Lunchables, Boca, Bacon, Claussen, and Cold Cuts) within a years time span due to multiple maternity leaves. However, my primary position managed over 100 FG skus and 500 materials on a daily basis and I dealt with capacity constraints, short shelf life, allocations, and regulations around importing and exporting product. My critical thinking skills, ability to build relationships, and negotiation skills came in handy as I continuously demonstrated improved customer service rates, reduced inventories, and coached team members on how to sustain implemented process improvements. Key improvements included:* Drove a 40% reduction in raw/pack/wip inventory plus 45% reduction in FG inventory while achieving record customer fill rates in the same year for the Boca Foods business.* Completed data analysis and developed a strategic inventory plan to improve service on a commodity driven business significantly impacted by weather. Result was a sustainable way to achieve record service levels.* Led the implementation of SAP at Kraft's only external co-man to use Kraft's systems.* Designed a predictive customer service recovery date tool that was expanded across all categoriesManaged 1 direct report.
-
-
Product Supply - Product Change Development Manager
-
Jul 2008 - Oct 2008
This was a very short experience due to a department restructure and job elimination.
-
-
Transportation - Sr Coach promoted to Process Optimization Manager
-
Dec 2001 - Jun 2008
After 5 years as a Sr. Coach I was promoted into a Manager position based on my proved record of project leadership and successful implementations but my greatest accomplishment was earning the respect and trust of the department and being recognized by leadership as the "go-to" expert for all Transportation process and system concerns.Through both "titles", I supported Kraft's centralized Transportation department as it related to any initiative involving computer systems, configurations, or business processes. I worked on projects with load planning, freight invoicing, procurement, claims, and with our import/export team. I was a leader who had the ability to get hands on in the analysis and execution of the initiative at hand while still pulling up to manage the overall project and provide updates to Sr. VP's in the company.Key initiatives:* Executed a multi year project to replace the Manugistics transportation planning and payment system with OTM (Oracle Transportation Management).* Identified and implemented numerous process improvements including a significant reduction of the carrier rate structure and improving processing speed.* Coordinated an on-board mileage tracking system on 200+ Private Fleet trucks without impact on time or service KPIs.* Co-developed software with external vendors* Developed and established a Help Desk (call in support/service center) for the centralized transportation department* Selected to represent over 70 companies as the Transportation Representative on the Manugistics Client Steering Committee Board.
-
-
Distribution - Process Optimization Senior Coach
-
Nov 2000 - Dec 2001
As a 100% road warrior, I led smaller distribution system initiatives or participated on larger project teams. I led the first implementation of a home-grown raw and packaging materials inventory system at one of our plants and assisted with the zoning and system implementation at a new DC as well. While traveling in this position, I was also attending college full time on the weekends to earn my MBA.
-
-
Oscar Mayer - Production Supervisor
-
Aug 1999 - Nov 2000
Managed multiple production lines on nights and weekends. Around 40-60 Union employees.
-
-
Education
-
Edgewood College
Master's, Business Administration -
Kansas State University
Coursework in Student Affairs -
University of Wisconsin-La Crosse
B.S., Psychology & Public Administration
Community
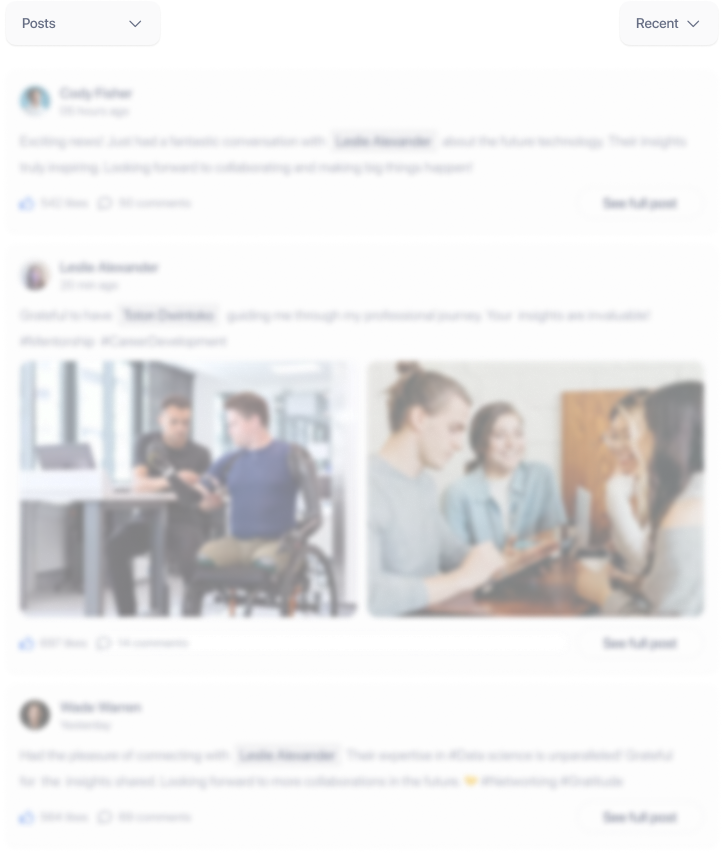