Ramanagarajan Meenakshinathan
Engineer - Product Procurement, Resource Industries at Caterpillar India Pvt Ltd- Claim this Profile
Click to upgrade to our gold package
for the full feature experience.
-
English Professional working proficiency
-
Tamil Native or bilingual proficiency
-
Hindi Elementary proficiency
Topline Score
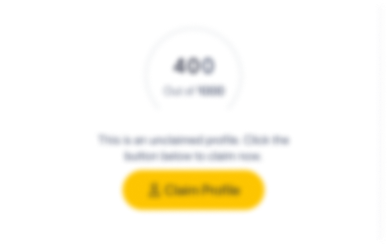
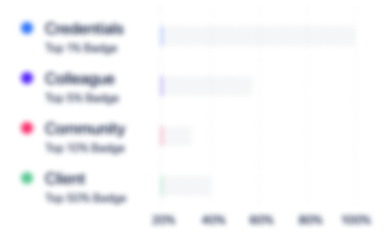
Bio

LinkedIn User
Me and Ram have worked together for more than 4 years. In those 4 years, I have found him to be very hard working, intelligent and passionate about this work. He has excellent communication skills and understands customer needs very well. He was also great at working with suppliers to get the work done in time with efficient use of resource. Ram had a keen eye for efficiency improvement. He was also looking for room to improvement in any existing process and then working with development team to create GUIS/tools to improve. He would then also do a good job of marketing new tools to the rest of the company for improved usage. He will be an excellent asset to any team he will work with.

Krishna (Kris) Kulkarni
Ram worked under my supervision for about 3 years. In the early days, he worked from India as a Structural Analyst and Design Engineer. As a result of his strong performance, I invited him for an Expatriate assignment in our Surface Drills facility in Denison, TX. Ram's performance as an Engineer during these years continued to greatly exceed my expectations. Ram displays a continuous learning mentality and is a creative problem solver. He pioneered new processes for FEA model development for Flexible Body Dynamics simulation during his work for the Surface Drills product group. Ram's skills in Analysis, as well as Design of structures, grew rapidly during this time, making him an indispensable part of the Surface Drills Engineering team. Ram displays a positive attitude and is a pleasure to work with. He will be a great asset to any Engineering team.

LinkedIn User
Me and Ram have worked together for more than 4 years. In those 4 years, I have found him to be very hard working, intelligent and passionate about this work. He has excellent communication skills and understands customer needs very well. He was also great at working with suppliers to get the work done in time with efficient use of resource. Ram had a keen eye for efficiency improvement. He was also looking for room to improvement in any existing process and then working with development team to create GUIS/tools to improve. He would then also do a good job of marketing new tools to the rest of the company for improved usage. He will be an excellent asset to any team he will work with.

Krishna (Kris) Kulkarni
Ram worked under my supervision for about 3 years. In the early days, he worked from India as a Structural Analyst and Design Engineer. As a result of his strong performance, I invited him for an Expatriate assignment in our Surface Drills facility in Denison, TX. Ram's performance as an Engineer during these years continued to greatly exceed my expectations. Ram displays a continuous learning mentality and is a creative problem solver. He pioneered new processes for FEA model development for Flexible Body Dynamics simulation during his work for the Surface Drills product group. Ram's skills in Analysis, as well as Design of structures, grew rapidly during this time, making him an indispensable part of the Surface Drills Engineering team. Ram displays a positive attitude and is a pleasure to work with. He will be a great asset to any Engineering team.

LinkedIn User
Me and Ram have worked together for more than 4 years. In those 4 years, I have found him to be very hard working, intelligent and passionate about this work. He has excellent communication skills and understands customer needs very well. He was also great at working with suppliers to get the work done in time with efficient use of resource. Ram had a keen eye for efficiency improvement. He was also looking for room to improvement in any existing process and then working with development team to create GUIS/tools to improve. He would then also do a good job of marketing new tools to the rest of the company for improved usage. He will be an excellent asset to any team he will work with.

Krishna (Kris) Kulkarni
Ram worked under my supervision for about 3 years. In the early days, he worked from India as a Structural Analyst and Design Engineer. As a result of his strong performance, I invited him for an Expatriate assignment in our Surface Drills facility in Denison, TX. Ram's performance as an Engineer during these years continued to greatly exceed my expectations. Ram displays a continuous learning mentality and is a creative problem solver. He pioneered new processes for FEA model development for Flexible Body Dynamics simulation during his work for the Surface Drills product group. Ram's skills in Analysis, as well as Design of structures, grew rapidly during this time, making him an indispensable part of the Surface Drills Engineering team. Ram displays a positive attitude and is a pleasure to work with. He will be a great asset to any Engineering team.

LinkedIn User
Me and Ram have worked together for more than 4 years. In those 4 years, I have found him to be very hard working, intelligent and passionate about this work. He has excellent communication skills and understands customer needs very well. He was also great at working with suppliers to get the work done in time with efficient use of resource. Ram had a keen eye for efficiency improvement. He was also looking for room to improvement in any existing process and then working with development team to create GUIS/tools to improve. He would then also do a good job of marketing new tools to the rest of the company for improved usage. He will be an excellent asset to any team he will work with.

Krishna (Kris) Kulkarni
Ram worked under my supervision for about 3 years. In the early days, he worked from India as a Structural Analyst and Design Engineer. As a result of his strong performance, I invited him for an Expatriate assignment in our Surface Drills facility in Denison, TX. Ram's performance as an Engineer during these years continued to greatly exceed my expectations. Ram displays a continuous learning mentality and is a creative problem solver. He pioneered new processes for FEA model development for Flexible Body Dynamics simulation during his work for the Surface Drills product group. Ram's skills in Analysis, as well as Design of structures, grew rapidly during this time, making him an indispensable part of the Surface Drills Engineering team. Ram displays a positive attitude and is a pleasure to work with. He will be a great asset to any Engineering team.

Credentials
-
Analytics on SAS
Great LearningMar, 2023- Nov, 2024 -
Career Essentials in Data Analysis by Microsoft and LinkedIn
MicrosoftMar, 2023- Nov, 2024 -
Mentorship Program on Excel and Power BI
Skill NationMar, 2023- Nov, 2024 -
Microsoft SQL for Beginners
UdemyMar, 2023- Nov, 2024
Experience
-
Caterpillar India Pvt Ltd
-
India
-
Retail Office Equipment
-
200 - 300 Employee
-
Engineer - Product Procurement, Resource Industries
-
Jul 2018 - Present
• Maximizing OPACC through Electrification and Next Gen NPI programs• Developed and maintained the Microsoft Power BI dashboard to track KPIs (key performance indicators) to provide business insights to leaders and stakeholders.• Conducted data analysis on direct material cost to identify trends and patterns in supplier spend and commodity cost.• Assistance to engineering value chain to develop data driven business strategies such as cost reduction opportunities through part regionalization from Europe to AP region.• Collaborated with cross functional teams like category, business resources, and logistics to get total cost of ownership analysis (TCO) done for source council gateway reviews and presented to stakeholders.• Conducted supplier selection based on their corporate QCLDM metrics, issuing purchase order, scheduling agreement and supervised the development progress to meet pillar standards• Acquired skills and developed competencies through work experience in a multifaceted environment in purchasing and supply chain.• Send the Request for Quotation (RFQ) to one or more suppliers through email and compare their quotations against the cost estimate derived from should cost model analysis• Select the suitable supplier based on their key performance metrics (quality, cost, capacity, financial and logistics), negotiate on pricing wherever applicable, and finally issue a purchase order • Collaborate with supplier development engineer (SDE) and design engineer during part development stages following all the relevant quality principles such as Advanced Product and Quality Planning (APQP), Failure Mode Effects Analysis (FMEA), and Concurrent Product Process Development (CPPD).• Once the part is developed, complete the Production Part Approval Process (PPAP) together with the design engineer to ensure the part is produced as per drawing without any quality defects Show less
-
-
Senior Associate Engineer - FEA
-
Feb 2015 - Jun 2018
• Supported virtual validation and simulation for Caterpillar products such as Large Mining Trucks, Motor Graders, Track Type Tractors, Electric Rope Shovels, and Surface Mining Drills.• Gathered in-depth knowledge and hands-on experience with machine dynamics and real-time testing at the Surface Mining Drills facility at Denison, Texas, USA (from Aug 2015 to Sep 2016)• Worked closely with testing and electrical engineers to mark the strain gauge and load sensor locations on the machine components to prepare for On-Machine Load and Stress analysis.• Supervised the installation of strain gauges and load sensors on the machine components at the proving ground site to ensure the output signals are reliable and accurate• Conducted the testing for multiple events based on the real-time machine composite work cycle• Gathered the test data from testing engineers to clean up and prepare for data analysis.• Conducted research on the test data, filtered, post-processed, plotted the strain and load data w.r.t time• Calculated the stress, and fatigue life (in hrs), plotted them in the form of a chart and prepared test report.• Presented the test report to stakeholders to describe how real-time testing correlates with FEA.• Test report helped the design engineers to strengthen the weak locations by understanding the damage-causing loads, and vibrations of the critical mechanical systems that lead to low fatigue life.• Successfully provided a design solution for a critical structural crack problem which saved the enterprise $1.2M and published a US Patent for the creative design solution which improved the weld fatigue life. Show less
-
-
Associate Engineer
-
Oct 2011 - Jan 2015
• Prepared a list of feasible projects to be completed every year along with the process partners• Created a goal plan for each project which measures the quality, velocity and cost targets• Managed each project effectively to complete them on time with high quality and accuracy• Conducted weekly meetings with participants about the progress of each project schedule• Collaborated with cross-functional teams such as the machine performance team to understand the dynamics of the machine structure to arrive at the boundary and loading conditions• Drawn Free Body Diagram (FBD) and resolved Force and Moment using hand calculations.• Designed the 3D models using computer-aided design (CAD) applications such as Creo or Solidworks• Lead a team of offshore engineers to prepare the finite element models (FEM) out of the 3D CAD models that are required for further analysis• Analysed the FEM model using computer-aided engineering (CAE) applications such as Ansys, Abaqus, Creo Simulate, etc., based on the linear or non-linear analysis conditions.• Investigated the finite element analysis (FEA) results to observe whether the model simulation is close to real-time machine dynamics to ensure the accuracy of the analysis process• Provided optimal design solutions wherever the structure is weaker for the given loading condition• Worked closely with electrical engineers to ensure the component modification does not affect the wiring harness which could lead to electrical failures.• Prepared project summary report, reviewed with peers, and presented in each design gateway phase and received feedback from stakeholders• Published technical papers at Caterpillar Technical Information Center (TIC) to capture unique skills and knowledge on the simulation projects Show less
-
-
Design Standard Technician-3 (Assistant Engineer)
-
Jul 2010 - Sep 2011
• Actively participated in New Product Introduction (NPI) and Continuous Process Improvement (CPI) projects and handled them with minimum supervision from the senior engineers within the team.• Highlighted excellence in analyzing the technical feasibility and proposed new product design and concepts without compromising the structural integrity of the product• Lead and managed a small team to oversee multiple projects effectively by creating project plans, task delegations, and conducting meetings to review periodically to ensure project deliverables and timelines are met with quality and technical accuracy.• Showcased effective collaboration and communication skills with both internal as well as global customer• Created an environment of growth; organizing training sessions & mentoring new engineers/interns on simulation applications and leading them on FEA projects• Identified the potential opportunity for process efficiency and implemented appropriate automation tools.• Collaborated with the software team, developed, and successfully deployed an automation tool named “Merge Part” to save time and labor costs spent over manual merge operations in the Creo application.• Received “Best Micro Innovation” award from top-level management for the deployment of the “Merge Part” automation tool which could save the enterprise $790 annually Show less
-
-
Design Standard Technician-2 (Junior Engineer)
-
Dec 2006 - Jun 2010
• Examined design schematics and 3D CAD models that illustrate the intended use of the product.• Worked in partnership with the design team to minimize the errors in the engineering drawings• Confirmed engineering notice delivers all required information about the changes to the component• Provided advice to design control personnel on potential problems in the design review phase• Inspected the design specification of the machine component to comply with Industry standards• Compared Pro/E, Manual and N-size drawings one-to-one with EDS to ensure whether they confirm to Corporate Product and Process Standard (CPPS).• Communicated and assisted Process Partners in the US in case of any rejections or queries through email/phone to get them resolved at a higher velocity.• Worked night shifts on a rotational basis to support the Process Partners in the US. Also, when needed, stayed an extra hour in the late evening during the day shift to complete the priority jobs.• Developed standard operating procedure that acts as guidance to the team members.• Trained and supervised new hires on the drawing-releasing process and procedure Show less
-
-
-
Caterpillar Global Mining America LLC
-
United States
-
Machinery Manufacturing
-
1 - 100 Employee
-
International Service Employee (ISE) - Denison TX, USA
-
Aug 2015 - Aug 2016
Worked as ISE at Caterpillar Global Mining-Drills (previously known as Bucyrus) from Aug 2015-2016. Supported both NPI and CPI projects on virtual validation of Drills heavy structures for Mining Design Center (MDC). Participated in OMSA test at Denison plant on Drills which includes gage mapping, test data post processing using Data Analysis Tool Kit (DATK) and conducting durability analysis. Also attended training on Flex body and Dynasty at Champaign Simulation Center at Champaign, IL, USA which is used for Multi body simulation to evaluate machine performance. Show less
-
-
-
Wheels India Limited
-
India
-
Manufacturing
-
700 & Above Employee
-
Junior Engineer-Product Development & Fatigue Testing
-
Jun 2004 - Dec 2006
• Communicate with Design group and arrive the load range to be applied, locate the places for gauges according to the FEA results (which are obtained externally), deciding the cycle range i.e. High or Low cycle fatigue and data to be recorded while testing. • Design the fixture using AutoCAD that are required for the testing and procure them from purchase group. • Communicate with Scientists in the lab and explain them about the testing procedure and conduct the testing with their guidance. • Observe and record the values of Strain gauge, Dial gauge, LVDT and electronic consoles while testing. • Observe the notable weld area for any flaw and measure its propagation using Ultrasonic Flaw detector. Also measure the permanent set wherever applicable. Warranty analysis of structural components • Observe the damage in the warranty component and collect the history of the component from the customer (i.e.) Vehicle, Kms covered, route etc. • Examine the component for any flaw present if any using manual flaw detectors. • Correlate the failure of the warranty component with the lab tested component and Show less
-
-
Education
-
Anna University
Bachelor’s Degree, Mechanical Engineering -
Alagappa University
Master of Business Administration (M.B.A.), Project Management
Community
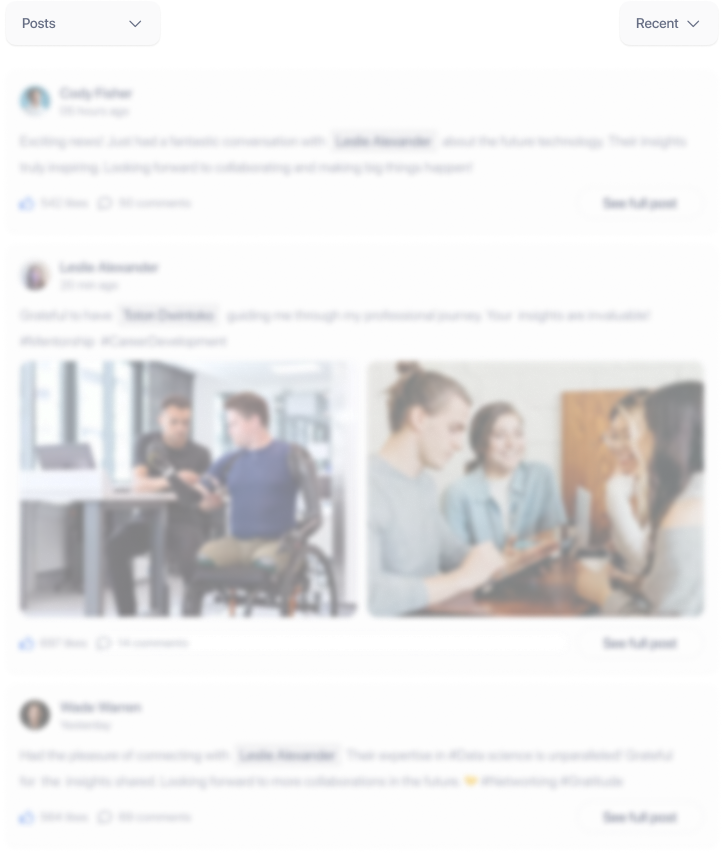