Raja Khan ACMI
Business Improvement - Integration & Performance Coordinator at GFG Alliance- Claim this Profile
Click to upgrade to our gold package
for the full feature experience.
Topline Score
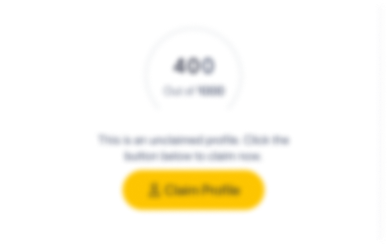
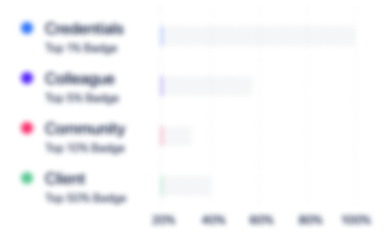
Bio


Experience
-
GFG Alliance
-
United Arab Emirates
-
International Trade and Development
-
400 - 500 Employee
-
Business Improvement - Integration & Performance Coordinator
-
Jun 2020 - Present
Key Responsibilities: • Operational optimisation & improvement projects (Safety, Quality, Delivery, Cost, & People). Applied through a fully developed, standardised Business Excellence System & approach • Providing ongoing support across the complete operational platform, through application of continuous improvement workstream leadership, while working alongside the senior site leadership team to establish operational improvement structures, processes & results Key Duties:• Leading an efficient operating C.I. program of improvement • Deploy communication workstreams, meeting structures, PMO development, visual management & information processes• Improve Business Key Performance Indicators • Establish individual and workstream performance management to achieve high standards• Lead to ensure C.I. resources are applied in an efficient and effective manner to meet improvement requirements• Ensure C.I. members follow defined manufacturing procedures and comply with quality requirements • Ensure full adherence to 5S • Track, monitor, and recorded accurately & appropriately workstream activity • Establish lean manufacturing practices within the company • Support and monitor the TPM performance/TPM program • Support and lead productivity improvements program • Lead and perform root cause analysis and resolve problems • Identify business improvement opportunities within the organisation • Identify and deploy the technical skill sets, resource levels and systems to deliver projects• Coordinate Project Management Office (PMO)
-
-
-
LIBERTY Steel Group
-
United Arab Emirates
-
Industrial Machinery Manufacturing
-
700 & Above Employee
-
Manufacturing Manager/LMOS 360 Coordinator (Liberty Manufacturing Operating System 360)
-
Apr 2018 - Jun 2020
• Responsible for the daily operation of the Foundry, manage budget, manpower and plant• Ensure agreed quality standards are maintained and improved upon where possible• In conjunction with the Personnel Manager, monitor works wage cost• Train and support all employees in Safe Working Practices, Job Safety, Machine Safety, Awareness of Hazards• Dealt with Grievances and Disciplinary’s • Took part in Union meetings & disputes• Investigate, recommend, and discuss any improvements and changes to improve Company efficiency• Responsibility for the implementation & assessment of the “Best Practice Continuous Improvement Tool” - LMOS 360 (Liberty Manufacturing Operating System) covering the following business areas:- Strategy, Communication, People Culture, Quality, Standard Work, Planning & Logistics, Engineering & AQP, Project Engagement, Health, Safety & Virus Risk Reduction
-
-
-
Aktrion Group
-
United Kingdom
-
Motor Vehicle Manufacturing
-
200 - 300 Employee
-
BMW Group Client Operations Manager
-
Sep 2017 - Apr 2018
• Managing all aspects of the customer relationship including site operations and service• Client business development (e.g., additional sites, other services, etc.)• Client sales and profitability including pricing• Recruitment, training and management of site supervisors & all staff working for the key clients• Contribute to the development and implementation of company and group strategy with ideas and involvement in strategic development• Work with company management to compile budgets and ensure budget requirements are met
-
-
-
-
Interim Business Unit Director/Production Director/Production Supervisor
-
Oct 2013 - Aug 2017
Interim Business Unit Director / Production Director - March 2015 – August 2017 Production Supervisor - October 2013 – March 2015Key Duties: • Leadership of 52 production operatives and 5 Team Leaders all within the remanufacturing process• Successfully developed a strategy/process for reducing unit cost and throughput time• In conjunction with the Quality Department ensured that the quality was at the required level• Provided guidance, support, and direction to the middle management team• Planned, managed, and developed a team to ensure optimum buy in and operational success• Drive the 5S initiatives• Developed and maintained effective TPM routines and ensured full adherence• Carried out Risk Assessments and verify the Safe Systems of Working• Focus on customer requirements for a competitive, high quality product delivered on time• Managed Grievance, Investigation and Disciplinary meeting/processes• Develop a strategy for Operational Excellence• Constantly review all operational processes to drive improvement and add value • Review processes to ensure maximisation of resource, improving productivity and eliminating waste• Carry out risk assessment and verify the Safe Systems of Working• Manage the employee performance review process ensuring effective communication of company and individual objectives
-
-
-
DRÄXLMAIER Group
-
Germany
-
Motor Vehicle Manufacturing
-
700 & Above Employee
-
Operations Zone Leader
-
Aug 2012 - Sep 2013
Continuation of Service from SAS Automotive Ltd (TUPE)
-
-
-
SAS interior modules
-
Germany
-
Motor Vehicle Manufacturing
-
400 - 500 Employee
-
Operations Supervisor/Team Leader (Continuation of Service from Siemens VDO)
-
Jan 2007 - Aug 2012
Operations Supervisor - March 2012 – August 2012Team Leader – January 2007 – February 2012Key Duties:• Direct reporting line to Head of Operations, with responsibility for 80 staff, including 7 Team Leaders & 7 Deputy Team Leaders covering 7 zones and all operations for Assembly and Logistic • Contributing to the development and implementation of “Best in Class” operations with local demands and SAS standards• Continuous optimisation of the assembly and logistics (resources/headcounts) in coherence with JLR schedules and internal SAS needs• Tracking of assembly and logistics indicators/costs, leading to corrective actions• Responsible for the quality of delivered parts and the processes involved (PPM, scrap etc.)
-
-
-
Siemens
-
Germany
-
Automation Machinery Manufacturing
-
700 & Above Employee
-
Team Leader/New Model Year Launch Team Assistant Co-ordinator
-
Oct 2001 - Dec 2006
-
-
Education
-
In-Comm Training Services
Internal Quality Auditing - IATF 16949:2016 -
Impellus Business Performance Training
Organisational Leadership Skills -
Impellus Business Performance Training
Developing Winning Teams -
Impellus Business Performance Training
Strategic Thinking & Decision Making -
Impellus Business Performance Training
Coaching Skills for Managers -
Dudley College
Lean Manfacturing -
CPI Ltd
IOSH - Institute of Occupational Health & Safety - Managing Safety in the Workplace -
CPI Ltd
Key Skills for Leading & Managing Teams -
Bournville College
Certificate In Management, Chartered Management Institute -
East Birmingham College
Mechanical/Fabrication Engineering, Level 3 -
Bishop Challoner R.C School
x9 GCSES (Grades A-C)
Community
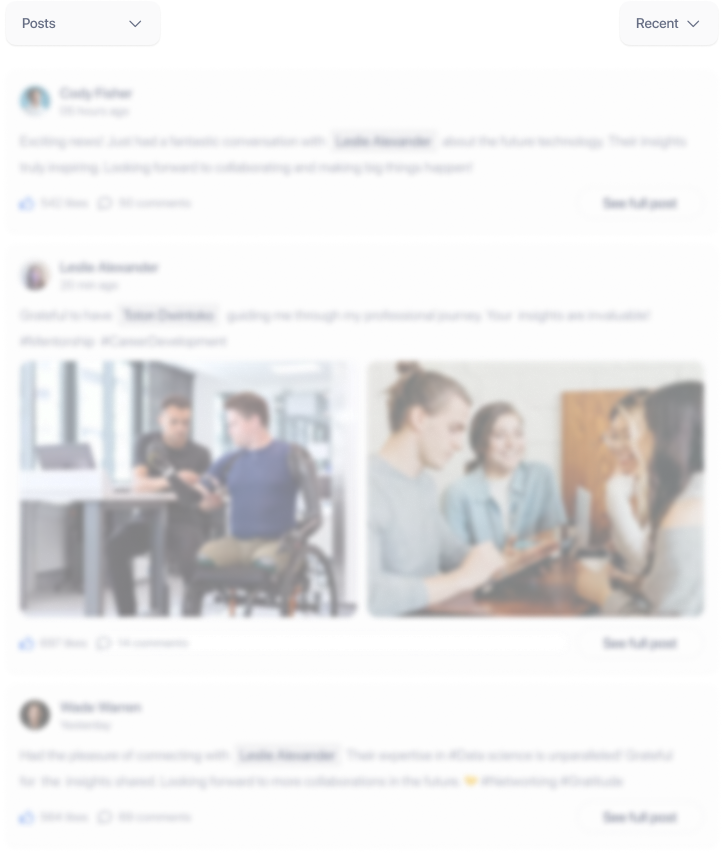