Raghu shetty
Supply Chain Analyst at Foodfx Australia- Claim this Profile
Click to upgrade to our gold package
for the full feature experience.
-
English Full professional proficiency
-
Kannada Professional working proficiency
-
Telugu Limited working proficiency
-
Hindi Limited working proficiency
Topline Score
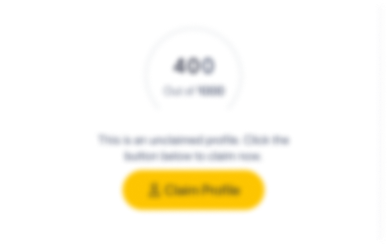
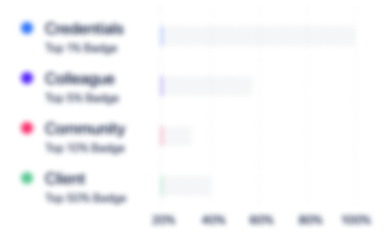
Bio

Somasundaram A
Raghu was a passionate & smart worker . Besides being a start-up,he had put up a lot of efforts in bringing the Operations in line . We worked together around 2 years where in we could share our market knowledge and Operations of C2C & B2B business .

Anupam A.
Raghu was part of the early team when we were building the C2C business and he contributed on his best note. he not only managed the centre but helped in expanding the Operations to other centres / cities. he's a hard working guy and very analytical in his approach. It was great to have him in the team. I wish Raghu all the very best in future endeavors and would be glad to work with him again.

Somasundaram A
Raghu was a passionate & smart worker . Besides being a start-up,he had put up a lot of efforts in bringing the Operations in line . We worked together around 2 years where in we could share our market knowledge and Operations of C2C & B2B business .

Anupam A.
Raghu was part of the early team when we were building the C2C business and he contributed on his best note. he not only managed the centre but helped in expanding the Operations to other centres / cities. he's a hard working guy and very analytical in his approach. It was great to have him in the team. I wish Raghu all the very best in future endeavors and would be glad to work with him again.

Somasundaram A
Raghu was a passionate & smart worker . Besides being a start-up,he had put up a lot of efforts in bringing the Operations in line . We worked together around 2 years where in we could share our market knowledge and Operations of C2C & B2B business .

Anupam A.
Raghu was part of the early team when we were building the C2C business and he contributed on his best note. he not only managed the centre but helped in expanding the Operations to other centres / cities. he's a hard working guy and very analytical in his approach. It was great to have him in the team. I wish Raghu all the very best in future endeavors and would be glad to work with him again.

Somasundaram A
Raghu was a passionate & smart worker . Besides being a start-up,he had put up a lot of efforts in bringing the Operations in line . We worked together around 2 years where in we could share our market knowledge and Operations of C2C & B2B business .

Anupam A.
Raghu was part of the early team when we were building the C2C business and he contributed on his best note. he not only managed the centre but helped in expanding the Operations to other centres / cities. he's a hard working guy and very analytical in his approach. It was great to have him in the team. I wish Raghu all the very best in future endeavors and would be glad to work with him again.

Credentials
-
Excel Supply Chain Analysis: Solving Inventory Problems
LinkedInDec, 2020- Nov, 2024 -
Inventory Management Foundations
LinkedInDec, 2020- Nov, 2024 -
Learning Power BI Desktop
LinkedInDec, 2020- Nov, 2024 -
Power BI Data Methods
LinkedInDec, 2020- Nov, 2024 -
Process Improvement Foundations
LinkedInDec, 2020- Nov, 2024 -
Managing and Analyzing Data in Excel (Office 365/Excel 2019)
LinkedInNov, 2020- Nov, 2024 -
Power BI Essential Training
LinkedInNov, 2020- Nov, 2024 -
Emotional Intelligence
RMIT UniversityOct, 2020- Nov, 2024 -
Power BI: Dashboards for Beginners
LinkedInOct, 2020- Nov, 2024 -
Blockchain for Business
RMIT UniversitySep, 2020- Nov, 2024 -
Building the Community
RMIT UniversitySep, 2020- Nov, 2024 -
Fostering Personal Resilience
RMIT UniversitySep, 2020- Nov, 2024 -
Learning SQL Programming
LinkedInSep, 2020- Nov, 2024 -
Making the Business Case
RMIT UniversitySep, 2020- Nov, 2024 -
Negotiating the System
RMIT UniversitySep, 2020- Nov, 2024 -
Quantitative Methods
RMIT UniversitySep, 2020- Nov, 2024 -
Starting Lean in Business
RMIT UniversitySep, 2020- Nov, 2024 -
Unlocking Resources
RMIT UniversitySep, 2020- Nov, 2024 -
Business Problem Solving
RMIT UniversityAug, 2020- Nov, 2024 -
Programming Foundations: Databases
LinkedInAug, 2020- Nov, 2024 -
Agile Ways of Working
RMIT UniversityJul, 2020- Nov, 2024 -
Developing Global Leadership
RMIT UniversityMay, 2019- Nov, 2024 -
ncc c certificate
-
Experience
-
Foodfx Australia
-
Australia
-
Food Production
-
1 - 100 Employee
-
Supply Chain Analyst
-
May 2021 - Present
1) Conducted demand forecasts of both raw materials and packaging materials every month based on sales and provided those forecast numbers to all the suppliers for a better flow of raw materials 2) Developed a strategic relationship with supply partners and collaborated with them to improve the supply performance 3) Collaborated with cross-functional departments across commercial, production, sales, NPD, and finance and coordinated engineering and cost savings projects relating to continuous improvement and new product launch 4) Analysed the monthly inventory consumption trend by monitoring inventory levels and adjusted the par levels based on consumption, resulting in reduced stock-out chances. 5) Built an alternate supply partner for each material to ensure a contingent supply of materials and negotiated optimal pricing strategies for long-term perspective. 6) Effectively managed product's shelf life by strictly monitoring the FIFO method and coordinated with the sales and production team to utilise the raw material which has nearing expiry date, thus resulting in a reduction of raw materials wastage 7) Responsible for managing end-to-end procurement process and warehouse operations 8) Supervised and directed the employees to achieve productivity in their day-to-day tasks 9) Actively participating in S&OP meetings for supply and demand review Show less
-
-
-
Birk Pty. Ltd
-
Australia
-
Manufacturing
-
Freelance Project
-
Mar 2021 - Apr 2021
Mapped business processes such as Check Measure Scheduling, Procurement, Installation, Warehouse Operations, Reverse Logistics, and Service calls using Preliminary hazard analysis risk methodology and identified the issues hampering the process and suggested solutions to improve the process. Mapped business processes such as Check Measure Scheduling, Procurement, Installation, Warehouse Operations, Reverse Logistics, and Service calls using Preliminary hazard analysis risk methodology and identified the issues hampering the process and suggested solutions to improve the process.
-
-
-
TIMETOSAVE PTY LTD :LED Lighting Solutions
-
Australia
-
Renewables & Environment
-
1 - 100 Employee
-
Warehouse Manager
-
Jul 2019 - Apr 2021
1) Generated inventory replenishment reports for effective stock management and monitored slow-moving stock to minimise the risk of obsolescence 2) Managed inbound and outbound logistics activities of a warehouse and ensured an on-time departure of the stock 3) Liaised with the sales team to ensure products were readily available for installation in line with company targets 4) Improved electrician stock-in-hand accuracy by designing and implementing the electrician stock-take process 5) Managed suppliers and closely collaborated with them to make sure purchase orders were delivered on time 6) Increased product recycling rate from 80% to 95% in 4 months by identifying the gaps and redesigning the recycling process Show less
-
-
-
Cashify
-
India
-
Consumer Services
-
700 & Above Employee
-
Operations Manager
-
Jun 2018 - Dec 2018
1) Built and headed Bangalore operations with a team of 25 members by leveraging the leadership and organisational skills 2) Catered 200 pickup orders on a day-to-day basis and contributed to 20% of the company's overall order volume 3) Maintained on-time pickup performance above 90% by effective planning and generating an optimised route plan. 4) Significantly reduced pickup of duplicate phones, theft phones and undervalued phones by continuously improving the pickup process using the lean tool 5) Monitored and ensured pickup executives'es’ performance was above 80% by practising positive reinforcement, encouraging employee engagement, and offering support to solve work-related problems 6) Constructively liaised with the CS team to solve customer issues on a priority basis, resulting in an increased service level Show less
-
-
-
Delhivery
-
India
-
Transportation, Logistics, Supply Chain and Storage
-
700 & Above Employee
-
Operations Manager ( Large goods )
-
Aug 2015 - Aug 2017
1) Successfully led a team of 50 members consisting of the team lead, executives, and ground staff 2) Expanded logistics operations from One distribution centre to Five distribution centres to cater to 400 heavy orders all over Bengaluru city daily 3) Handled logistics verticals such as B2B, B2C and C2C. It improved logistics performance from 70% to 85% through effective planning, team management, resource management and forecasting pickup and deliveries by collaborating with the BD team. 4) Collaborated with the new product development team in building a transport management system (TMS) and rolled it out across south India and trained executives to use the application 5) Optimised route plan using route allocation engine to maximise truck utilisation and to cater to 500 customers' demand. 6) Established a strong relationship with the external stakeholders and exceeded their expectations by understanding their needs and fulfilling those needs in a short time, which increased the company's service level 7) Implemented 5S Methodology in all 5 Distribution centres, which increased employee productivity from 70% to 85% Show less
-
-
-
Sona Group Of Industries - India
-
India
-
1 - 100 Employee
-
Academic Project ( Productivity Improvement in Watch Strap Manufacturing )
-
Feb 2015 - May 2015
The objective was to enhance productivity in Leather Watch Strap making industry. Aim of the project was to reduce production time, increase production, and reduce waste & over time. The objective was to enhance productivity in Leather Watch Strap making industry. Aim of the project was to reduce production time, increase production, and reduce waste & over time.
-
-
-
Hindustan Aeronautics Limited
-
Aviation and Aerospace Component Manufacturing
-
700 & Above Employee
-
Summer Intern
-
Jul 2014 - Aug 2014
• Attended Vocational Industrial Training at HAL, Bangalore that helped to get familiar with HAL services, products and various helicopter departments such as: o Method & Tooling o Machine Shop o Assembly o Quality & Maintenance • Attended Vocational Industrial Training at HAL, Bangalore that helped to get familiar with HAL services, products and various helicopter departments such as: o Method & Tooling o Machine Shop o Assembly o Quality & Maintenance
-
-
Education
-
RMIT University
Master's degree, Logistics, Materials, and Supply Chain Management -
Sri Siddhartha Institute of Technology
Bachelor of Engineering (BE), Industrial engineering and managment
Community
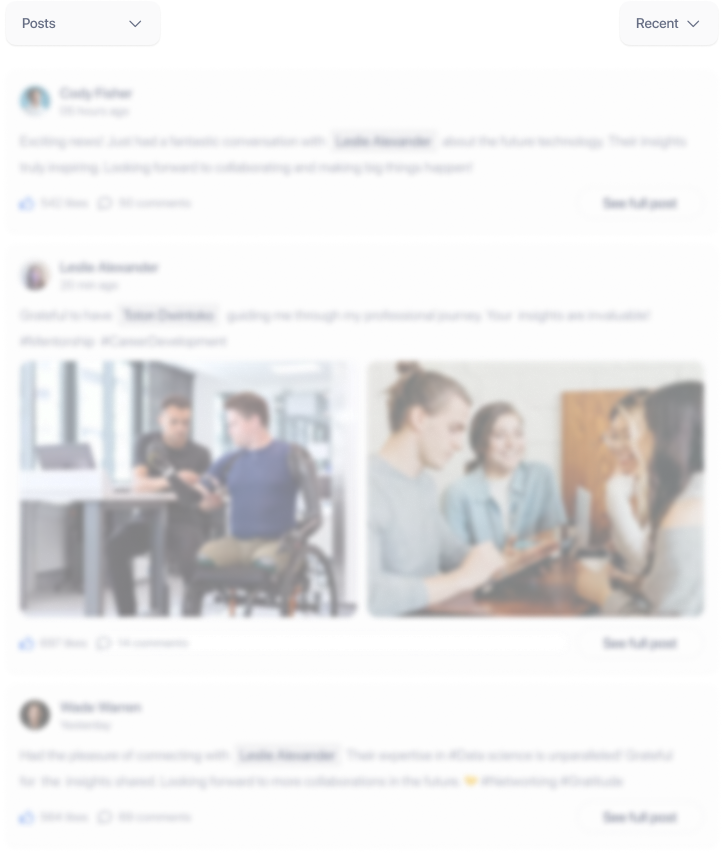