
Rafal Szczepanczyk
SHEQ Manager at Norse Commercial Services Limited- Claim this Profile
Click to upgrade to our gold package
for the full feature experience.
-
Polish Native or bilingual proficiency
-
English Full professional proficiency
Topline Score
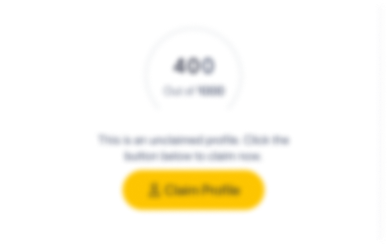
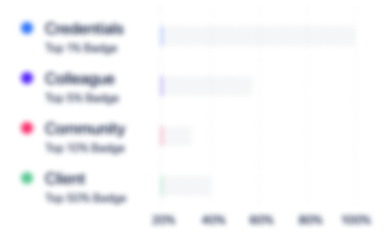
Bio


Credentials
-
Internal Auditor of ISO Standards 9001, 14001, 45001
Norse Commercial Services LimitedMar, 2019- Nov, 2024 -
Oxford Cambridge Diploma in Business Management (QCF)
OXFORD CAMBRIDGE AND RSA EXAMINATIONSFeb, 2017- Nov, 2024 -
HABC Level 3 Award in HACCP for Food Manufacturing (QCF)
-Nov, 2014- Nov, 2024 -
NEBOSH Certificate in Occupational Health and Safety
-Jul, 2010- Nov, 2024 -
IOSH Managing Safely
St Johns AmbulanceJun, 2008- Nov, 2024 -
Car Driving Licence
-Feb, 2002- Nov, 2024 -
Counterbalance Licence
-Feb, 2007- Nov, 2024 -
Reach Truck Licence
-Feb, 2007- Nov, 2024 -
Emergency Response Certificate
Ecolab -
Fire Marshal Certificate
CHUBB FIRE & SECURITY LIMITED -
Internal Auditor Certificate
NSF International -
MyJet Canadian AirBus Simulators
My jet -
Oxford Cambridge Functional Skills Qualification in English - Business Sector
OXFORD-CAMBRIDGE CENTRE FOR ADVANCED MANAGEMENT EXPERIENCE LTD -
Oxford Cambridge Functional Skills Qualification in Mathematics - Business Sector
OXFORD CAMBRIDGE AND RSA EXAMINATIONS -
Oxford Cambridge Functional Skills Qualifications in Information & Communication Technology (ICT)
OXFORD-CAMBRIDGE CENTRE FOR ADVANCED MANAGEMENT EXPERIENCE LTD
Experience
-
Norse Commercial Services Limited
-
United Kingdom
-
Facilities Services
-
100 - 200 Employee
-
SHEQ Manager
-
Mar 2019 - Present
-
-
-
Ralph Coleman International Ltd
-
United Kingdom
-
Transportation, Logistics, Supply Chain and Storage
-
1 - 100 Employee
-
Site General Manager
-
Jan 2018 - Nov 2018
Reporting to the Board of Directors of the company.Overall responsibility to Manage Wellingborough production site.Managing all aspects of site performance, making sure objectives were attained in a cost-effective manner that was consistent with safety and quality requirements.Managing personnel and all resources.Administered daily operations with daily delegation of tasks during one to one or daily management team meetings.Managing and controlling site P&LInfluencing senior Managers by suggesting solutions for day to day problems & to support cooperative policies and plans.Reviewing and updating weekly financial report & flash report for Operations Director detailing site performance and operational effectiveness, as well as areas for improvement.Responsible for organising recruitment process for Senior Managers,conducting interviews and making employment offers.Challenging and reviewing all site expenditure requestsPreparing and presenting weekly reports to determine profitability and areas of improvement.Managing multiple site projects.Introduced continuous auditing of the production processes to ensure products achieved highest quality standard.Investigating customer complaints by analysing the root cause and implementing corrective and preventative actions.Introduced safety and quality standards on site to maintain compliance with ISO standards and all HSE requirements, Reviewed and signed off all site risk assessments and accident investigations,Introduced numerous accidents prevention policies and procedures, shared best practices with sister sites. Actively promoted Zero Harm culture and Safe working environment.
-
-
Production Manager
-
May 2016 - Jan 2018
-
-
-
IFCO SYSTEMS
-
Germany
-
Transportation, Logistics, Supply Chain and Storage
-
700 & Above Employee
-
Operations Manager
-
Sep 2012 - May 2016
Responsible for the operation of a production facility and achieving production targets, controlling stock levels, product quality, liaising with suppliers on quality and delivery issues, raising and implementing engineering changes, managing over 100 site employees.Leading , developing and inspiring the warehouse and service office team to achieve KPIs whilst achieving high levels of customer service.Planned and monitored labour requirements and managed budget of circa £1,000,000 Leading daily and weekly management team meetingsResponsible for development and implementation of maintenance system for a production facilityResponsible for ISO22000 adherence and maintenance of set standards.Conducting team leaders appraisals Tracking shifts OEE and machines downtime, Investigating and identifying root cause problems and immediately solving them to maintain high performance Managing staff holidays and absence recordsDeputising Plant Manager Key Achievements • Implemented multiple small scale projects raising the efficiency of production• Implemented a new management system bringing a better technical solution into a plant and reducing production costs by £80,000 per year.• Reduced cost of waste management by £47,000 per year 48% reduction in cost• Implemented number of process improvements such KIZEN, 5s programme and OPEX• Introduced and implemented new shift patterns to optimise labour costs and boost production to meet increasing customer demand
-
-
-
CHEP
-
United Kingdom
-
Transportation, Logistics, Supply Chain and Storage
-
700 & Above Employee
-
OHSE Manager
-
Jul 2008 - Sep 2012
Coordinating site OHS&E action plan to achieve target compliance on Occupational Health, Safety & Environmental StandardsMonitoring and reporting OHS&E KPI’s Implementing OHS&E systems flowing from the Regional Safety Teams (Safety, Environment, Fire & Security) Leading continuous improvement programme via systematic change based on data and root cause analysis (Risk assessments, accidents root cause analysis), Delivered multiple projects based on ; Kaizen, Lean Manufacturing - 5 lean principles , OPEX, 5S, KanBan systems, ( everything in place and place for everything)Developed, implemented and maintained Behaviour Observation System (MOT), Responsible for generating network monthly reports for European Health & Safety Managers )Developed, implemented and maintained risk assessment dashboard.Developed, implemented and maintained management system for sub - contractors visiting CHEP depotLeading daily plant management meetings Monitoring & ensuring consistent, timely responses to all issues relating to OHS&E. Conducted multiple site safety inspections ,GAP analysis, Fire Risk & Security audits. Ongoing Communication & documentation of changes to OHS&E SOP’s and Management Systems. Leading Plant OHS&E employee training and qualificationLeading the Job Element and Instruction training programmeThis role have substantially improved my confidence, knowledge and skills in OHSE Management. Key AchievementsRugby Site Achieved award for 4 years LTI freeDeveloped and Implemented Behaviour Observation System and MOT Management Observation ToolRugby site was recognised as Health and Safety Champion across all CHEP sites based in Europe Developed and implemented comprehensive individual shifts training matrixDeveloped and implemented risk assessment control dashboard, management system for contractors visiting SiteMany of the tools developed by myself were shared and implemented in all CHEP sites
-
-
Education
-
Technical University - Building Documentation
Technical University from 1999 till 2004 - Building Designs and Documentation Profile
Community
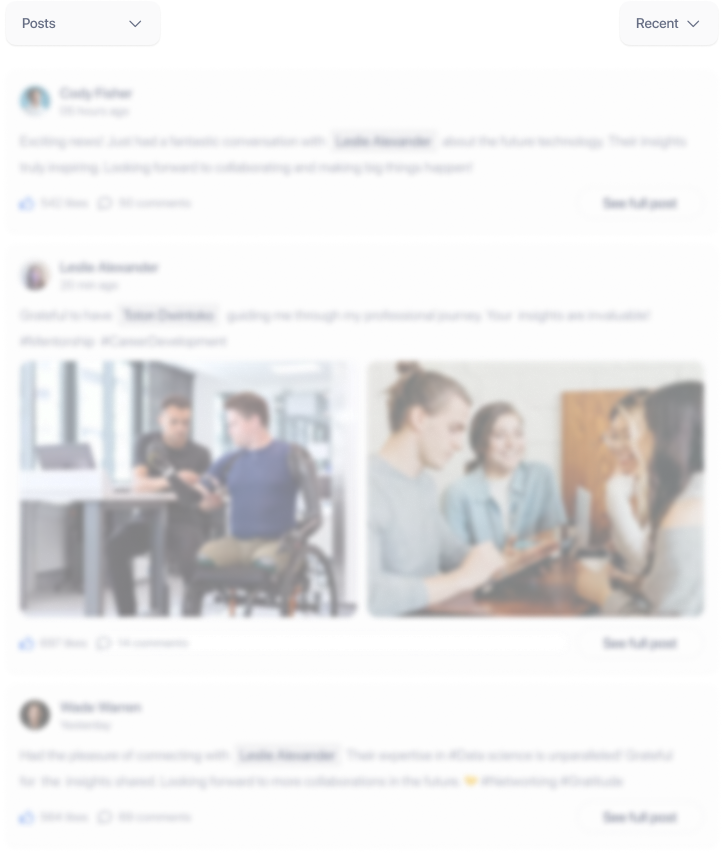