Rafael Pons
Chief Manufacturing Officer at Trecora Resources- Claim this Profile
Click to upgrade to our gold package
for the full feature experience.
-
English Native or bilingual proficiency
-
Spanish Native or bilingual proficiency
Topline Score
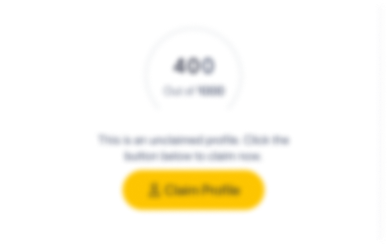
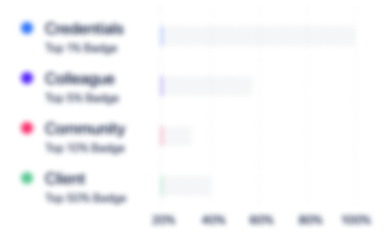
Bio

Greg Logue - BS, MBA, MS
Ralph is a consummate executive operations professional and embodies all of the skills and traits that an organization seeks in a senior executive leader. He makes data driven decisions while coaching and mentoring his teams to generate outside the box improvement initiatives through collaboration and teamwork. He relates well with all levels of the organization and will readily assist with operational issues and opportunities and drives a strong culture of safety, operational excellence and efficiency. His integrity, knowledge and experience will move the organizational culture in the direction of long term sustainable success.

Aashish Bansal
I have had the pleasure of working with Ralph as a valued client for almost an year and a half. During that period he has consistently demonstrated that he is open to new ideas, is innovative in addressing strategic and operational challenges, is laser focused on safety and process improvement, and is inclusive in the way he involves the larger team and deploys best practices in problem solving.

Greg Logue - BS, MBA, MS
Ralph is a consummate executive operations professional and embodies all of the skills and traits that an organization seeks in a senior executive leader. He makes data driven decisions while coaching and mentoring his teams to generate outside the box improvement initiatives through collaboration and teamwork. He relates well with all levels of the organization and will readily assist with operational issues and opportunities and drives a strong culture of safety, operational excellence and efficiency. His integrity, knowledge and experience will move the organizational culture in the direction of long term sustainable success.

Aashish Bansal
I have had the pleasure of working with Ralph as a valued client for almost an year and a half. During that period he has consistently demonstrated that he is open to new ideas, is innovative in addressing strategic and operational challenges, is laser focused on safety and process improvement, and is inclusive in the way he involves the larger team and deploys best practices in problem solving.

Greg Logue - BS, MBA, MS
Ralph is a consummate executive operations professional and embodies all of the skills and traits that an organization seeks in a senior executive leader. He makes data driven decisions while coaching and mentoring his teams to generate outside the box improvement initiatives through collaboration and teamwork. He relates well with all levels of the organization and will readily assist with operational issues and opportunities and drives a strong culture of safety, operational excellence and efficiency. His integrity, knowledge and experience will move the organizational culture in the direction of long term sustainable success.

Aashish Bansal
I have had the pleasure of working with Ralph as a valued client for almost an year and a half. During that period he has consistently demonstrated that he is open to new ideas, is innovative in addressing strategic and operational challenges, is laser focused on safety and process improvement, and is inclusive in the way he involves the larger team and deploys best practices in problem solving.

Greg Logue - BS, MBA, MS
Ralph is a consummate executive operations professional and embodies all of the skills and traits that an organization seeks in a senior executive leader. He makes data driven decisions while coaching and mentoring his teams to generate outside the box improvement initiatives through collaboration and teamwork. He relates well with all levels of the organization and will readily assist with operational issues and opportunities and drives a strong culture of safety, operational excellence and efficiency. His integrity, knowledge and experience will move the organizational culture in the direction of long term sustainable success.

Aashish Bansal
I have had the pleasure of working with Ralph as a valued client for almost an year and a half. During that period he has consistently demonstrated that he is open to new ideas, is innovative in addressing strategic and operational challenges, is laser focused on safety and process improvement, and is inclusive in the way he involves the larger team and deploys best practices in problem solving.
0
/5.0 / Based on 0 ratingsFilter reviews by:
Experience
-
Trecora Resources
-
United States
-
1 - 100 Employee
-
Chief Manufacturing Officer
-
2021 - Present
Reporting to the CEO, responsible for the performance of all manufacturing assets. Reporting to the CEO, responsible for the performance of all manufacturing assets.
-
-
-
South Hampton Resources
-
United States
-
Oil and Gas
-
1 - 100 Employee
-
Plant Manager
-
2020 - 2021
Reporting to the Chief Manufacturing Officer, responsible for the overall performance of the plant with an annual operating budget of $ 75M, a capital budget of 10M and workforce of 150. Reporting to the Chief Manufacturing Officer, responsible for the overall performance of the plant with an annual operating budget of $ 75M, a capital budget of 10M and workforce of 150.
-
-
-
Preferred
-
United States
-
Oil and Gas
-
1 - 100 Employee
-
Vice President of Operations
-
2018 - 2019
Provide leadership, direction, and coordination of all production activities at 5 Sand Plants in Genoa,NE; Sanders, AZ; Monahans,TX; Atascosa,TX and Oklahoma and 2 Coating Plants in Genoa and Monahans. Provide leadership, direction, and coordination of all production activities at 5 Sand Plants in Genoa,NE; Sanders, AZ; Monahans,TX; Atascosa,TX and Oklahoma and 2 Coating Plants in Genoa and Monahans.
-
-
-
Celanese
-
United States
-
Chemical Manufacturing
-
700 & Above Employee
-
Site Director
-
2016 - 2017
Reporting to the Vice President of Manufacturing, responsible for overall performance of the Clear Lake Site consisting of 6 plants. Managing $2B+ in assets with an annual operating budget of $130M, and workforce of 470. In addition, provide services to 4 other companies and 4 other plants that are tenants on the site. • Arriving as the new Site Director in Sept ‘16, successfully led an April ‘17 $80M+, first ever, total site outage achieving zero safety incidents and better than top… Show more Reporting to the Vice President of Manufacturing, responsible for overall performance of the Clear Lake Site consisting of 6 plants. Managing $2B+ in assets with an annual operating budget of $130M, and workforce of 470. In addition, provide services to 4 other companies and 4 other plants that are tenants on the site. • Arriving as the new Site Director in Sept ‘16, successfully led an April ‘17 $80M+, first ever, total site outage achieving zero safety incidents and better than top quartile performance on schedule and cost. • Set new production records at the Methanol and Ethylene Oxide plants. • Increased on stream reliability of all 5 plants versus previous year. Show less Reporting to the Vice President of Manufacturing, responsible for overall performance of the Clear Lake Site consisting of 6 plants. Managing $2B+ in assets with an annual operating budget of $130M, and workforce of 470. In addition, provide services to 4 other companies and 4 other plants that are tenants on the site. • Arriving as the new Site Director in Sept ‘16, successfully led an April ‘17 $80M+, first ever, total site outage achieving zero safety incidents and better than top… Show more Reporting to the Vice President of Manufacturing, responsible for overall performance of the Clear Lake Site consisting of 6 plants. Managing $2B+ in assets with an annual operating budget of $130M, and workforce of 470. In addition, provide services to 4 other companies and 4 other plants that are tenants on the site. • Arriving as the new Site Director in Sept ‘16, successfully led an April ‘17 $80M+, first ever, total site outage achieving zero safety incidents and better than top quartile performance on schedule and cost. • Set new production records at the Methanol and Ethylene Oxide plants. • Increased on stream reliability of all 5 plants versus previous year. Show less
-
-
-
Nalco Champion, an Ecolab Company
-
United States
-
Oil and Gas
-
700 & Above Employee
-
Plant Manager
-
2015 - 2016
Reporting to the Vice President of Manufacturing, responsible for overall performance of Nalco Champion’s largest and most diverse plant. Managing $250M in assets with an annual operating budget of $75M, and workforce of 250. • Sustained strong safety performance achieving 3+ years OSHA free. • Improved mechanical integrity program. • Sustained 100% regulatory compliance. • Reduced spending by 14% ($9M) through improved productivity. Reporting to the Vice President of Manufacturing, responsible for overall performance of Nalco Champion’s largest and most diverse plant. Managing $250M in assets with an annual operating budget of $75M, and workforce of 250. • Sustained strong safety performance achieving 3+ years OSHA free. • Improved mechanical integrity program. • Sustained 100% regulatory compliance. • Reduced spending by 14% ($9M) through improved productivity.
-
-
-
Phillips 66
-
United States
-
Oil and Gas
-
700 & Above Employee
-
Project Manager, Major Projects
-
2014 - 2015
Reporting to the General Manager of Projects, responsible for major projects exceeding $70M. Managed four projects totaling $285M. • Aggressively took over project management role for projects in construction with poor safety performance and significantly behind schedule. Successfully led a recovery effort restoring safe and on schedule performance.
-
-
Manager Maintenance Functional Excellence Team
-
2013 - 2014
Reporting to the General Manager of Business Improvement, responsible for the maintenance, development, and implementation of required standards, best practices, and the refinery engineering practices in support of 13 refineries. • Successfully led development and implementation of corporate turnaround work process, including all supporting best practices and tools. • Led effort to develop Reliability Improvement Initiative. This included business case development, stakeholder buy in… Show more Reporting to the General Manager of Business Improvement, responsible for the maintenance, development, and implementation of required standards, best practices, and the refinery engineering practices in support of 13 refineries. • Successfully led development and implementation of corporate turnaround work process, including all supporting best practices and tools. • Led effort to develop Reliability Improvement Initiative. This included business case development, stakeholder buy in, best practices, tools and organizational improvements. • Facilitated analysis and decisions on actions to address anticipated contractor labor demand peak to help minimize impact on turnarounds. • Worked in collaboration with Project Services to define project engagement expectations and additional resources needed to support company’s growing capital needs.
-
-
-
Dow Chemical
-
China
-
Chemical Manufacturing
-
1 - 100 Employee
-
Director, Houston Area Operations Maintenance & Reliability
-
2011 - 2013
Reporting to the Site Leader, ultimate responsibility for the maintenance and reliability performance of 5 sites located in the Houston area. Managed $5B in assets; annual budget of $200M; 250 direct reports, and a significant contractor workforce (Daily 600, Turnarounds up to 3k). • Reorganized Maintenance Department to improve results delivered to the Business by delayering, increasing accountability through metrics, and adding needed resources. • Improved efficiency allowing reduction… Show more Reporting to the Site Leader, ultimate responsibility for the maintenance and reliability performance of 5 sites located in the Houston area. Managed $5B in assets; annual budget of $200M; 250 direct reports, and a significant contractor workforce (Daily 600, Turnarounds up to 3k). • Reorganized Maintenance Department to improve results delivered to the Business by delayering, increasing accountability through metrics, and adding needed resources. • Improved efficiency allowing reduction of 200 contractors saving $1M / month. • Implemented additional structural cost reductions totaling $5M / yr. • Accelerated the implementation of Maintenance & Reliability work processes resulting in cost savings and 1% improvement in asset availability.
-
-
Director, Environmental Operations
-
2009 - 2011
Reporting to the VP of Texas Operations, responsible for overall performance of environmental assets at one of the largest integrated chemical complexes in the world. Managed $800M in assets with an annual budget of $100M, and 100 direct reports. • Led effort that reduced safety and environmental unplanned events by 75%. • Implemented projects that reduced costs by $3M-$4M per year. • Successfully led site effort to mitigate environmental events by facilitating activities across 40+… Show more Reporting to the VP of Texas Operations, responsible for overall performance of environmental assets at one of the largest integrated chemical complexes in the world. Managed $800M in assets with an annual budget of $100M, and 100 direct reports. • Led effort that reduced safety and environmental unplanned events by 75%. • Implemented projects that reduced costs by $3M-$4M per year. • Successfully led site effort to mitigate environmental events by facilitating activities across 40+ plants.
-
-
Project Director
-
2007 - 2009
Reporting to the VP of Manufacturing, responsible for successful execution of capital projects of approximately $500M, as well as management of the division’s projects portfolio. Led effort that achieved capital budget plan each year. • Successfully leveraged knowledge from EG2 Project in Kuwait to another major Ethylene Oxide Project. • Led effort that improved organizational effectiveness of Ethylene Oxide Technology Center and Ethylene Oxide Licensing. • Helped lead major project… Show more Reporting to the VP of Manufacturing, responsible for successful execution of capital projects of approximately $500M, as well as management of the division’s projects portfolio. Led effort that achieved capital budget plan each year. • Successfully leveraged knowledge from EG2 Project in Kuwait to another major Ethylene Oxide Project. • Led effort that improved organizational effectiveness of Ethylene Oxide Technology Center and Ethylene Oxide Licensing. • Helped lead major project team complete Basic Engineering Package on time and on budget. • Key participant in corporate six sigma teams to improve capital planning, prioritization and cash flow management. This was used effectively to reduce capital plan by $1B.
-
-
Global Business Improvement Leader
-
2003 - 2007
Reporting to the Business Manufacturing Leader, responsible for successful execution of capital projects, six sigma projects, and maintenance and reliability performance of 13 plants. Managed $2.5B in assets; annual capital budget of $50M and maintenance budget of $50M. Supervised 20 direct reports. • Project teams implemented $70M in capital with zero OSHA violations and zero spills, and were delivered on time, on budget, and met project objectives. • Managed portfolio of approximately… Show more Reporting to the Business Manufacturing Leader, responsible for successful execution of capital projects, six sigma projects, and maintenance and reliability performance of 13 plants. Managed $2.5B in assets; annual capital budget of $50M and maintenance budget of $50M. Supervised 20 direct reports. • Project teams implemented $70M in capital with zero OSHA violations and zero spills, and were delivered on time, on budget, and met project objectives. • Managed portfolio of approximately 200 capital and six sigma projects per year at ten sites. • PDC Bottoms project delivered $1M / yr. in savings and avoided $5M in capital costs, which led to award of Chemical Processing Magazine’s Plant Innovation Award for 2007. • Achieved total hard dollar savings of $12M and soft dollar savings of $90M. • Led the development and implementation of Environmental Operations Plant Specific Technology Plan. This work process is still being used globally by Dow. • Key contributor in leading Environmental Technology Center through two reorganizations that significantly reduced personnel costs.
-
-
Production Leader PDC Hydrogenation
-
2001 - 2003
(RAB-$100MM; Total Cost $26MM/yr; Direct Reports-13) •Zero Spills (9/01-4/03) •Initiated and acted as Local Champion for Catalyst and Yield Improvement 6 sigma projects that resulted in $2.0 MM/yr savings. The Yield project received a Technology Award (2002-2003) •Cost reduced from $0.12/lb in 2000 to less than $0.07 cents/lb in 2002 •Asset Capability increased from 72% in 2001 to 80% in 2002
-
-
Environmental Operations Business Global Maintenance and Reliability Leader
-
2000 - 2003
•Maintenance OSHA rate reduced from 1.7 to 0.5 from 2000 to 2003 •Spills due to equipment failure reduced from 11 in 2000 to zero in 2002 •Maintenance Costs- $6MM under in 2002; $6.5 MM under in 2003; base spending reduced by 20% from 2000 to 2003 •Incineration Mechanical Reliability increased from 91% in 2000 to 97% in 2002; •Established a Global Maintenance Excellence Award and a Perfect Execution Award that drove improvement. Perfect Execution award winners in 2002 and 2003… Show more •Maintenance OSHA rate reduced from 1.7 to 0.5 from 2000 to 2003 •Spills due to equipment failure reduced from 11 in 2000 to zero in 2002 •Maintenance Costs- $6MM under in 2002; $6.5 MM under in 2003; base spending reduced by 20% from 2000 to 2003 •Incineration Mechanical Reliability increased from 91% in 2000 to 97% in 2002; •Established a Global Maintenance Excellence Award and a Perfect Execution Award that drove improvement. Perfect Execution award winners in 2002 and 2003 resulted in >1MM/yr in savings
-
-
Maintenance & Engineering Process Leader for Polyurethanes and Propylene Oxide
-
1998 - 2000
(RAB-$1Billion; Maintenance-$20MM/yr; Direct Reports-53) •Initiated Spill reduction charter for Freeport Polyurethanes. Acted as local champion. LOPC’s were reduced from 41 in ’99 to 28 in ’00 •Polyol plant Mechanical Reliability increased by 1% (96%-97%). Copolymer from 86%-91% and TDI by 3% •Helped lead effort to solve equipment problems during the TDI Tr 2 startup. These solutions allowed TDI to startup •Achieved Stage 2 Empowerment with all 22 elements at stage 2 with… Show more (RAB-$1Billion; Maintenance-$20MM/yr; Direct Reports-53) •Initiated Spill reduction charter for Freeport Polyurethanes. Acted as local champion. LOPC’s were reduced from 41 in ’99 to 28 in ’00 •Polyol plant Mechanical Reliability increased by 1% (96%-97%). Copolymer from 86%-91% and TDI by 3% •Helped lead effort to solve equipment problems during the TDI Tr 2 startup. These solutions allowed TDI to startup •Achieved Stage 2 Empowerment with all 22 elements at stage 2 with Maintain Facility team of 50+ people •Member of team that developed and implemented the Global Improve Reliability Work Process for the Company. Led the sub-team that developed the training posters. I was recognized for both
-
-
Hanging Rock Site Maintenance Leader.
-
1996 - 1998
•Improved safety performance of maintenance dept. (went one year OSHA free (Dow and Contractor) for 1st time ever(1/96-6/98) •Reduced structural maintenance costs by 14% and headcount by 20% •Improved site Mechanical Reliability from 85.9% to 90.5% by implementing the Global Maintenance Work Process in 9 months, focusing on PPM, a"fix it right the 1st time" mentality, and properly allocating resources (1/96-6/98).
-
-
Improvement Leader
-
1995 - 1996
-
-
Production Supervisor
-
1993 - 1995
Led effort to improve plant safety performance- achieved 676 days OSHA free (Dow and Contractor)- previous record was 180
-
-
Quality Coordinator for Styrenics Business
-
1990 - 1993
Led 10 plants to achieve ISO 9002
-
-
Education
-
Rensselaer Polytechnic Institute
M.S., Operations Management -
University of Virginia
BS, Chemical Engineer
Community
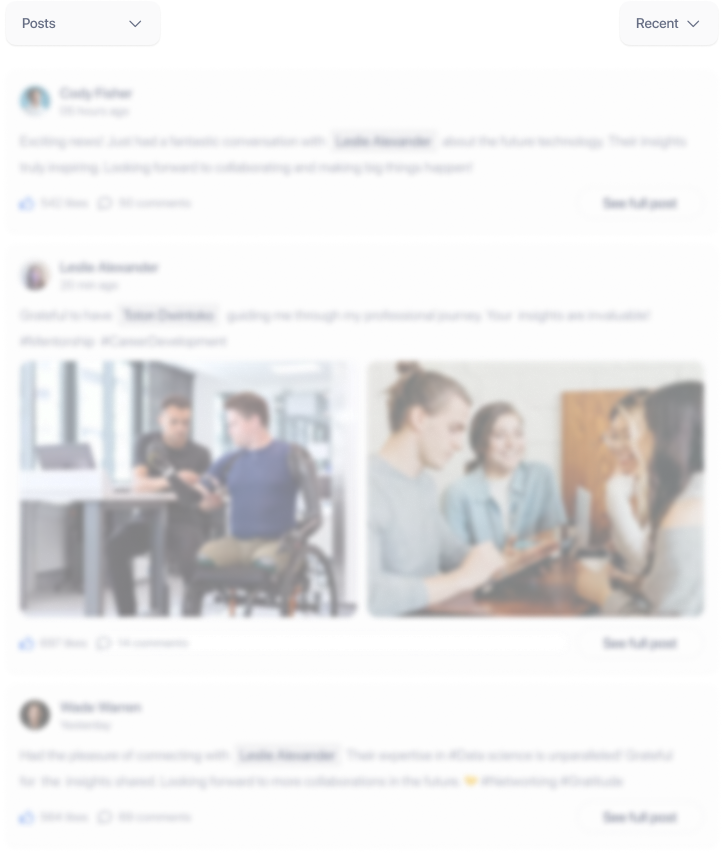