Radka Serafimova
Lean Manager at Ideal Standard International NV- Claim this Profile
Click to upgrade to our gold package
for the full feature experience.
Topline Score
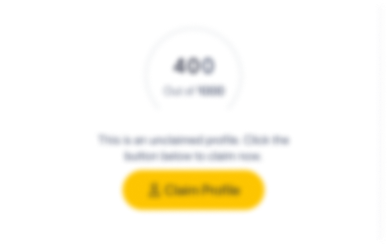
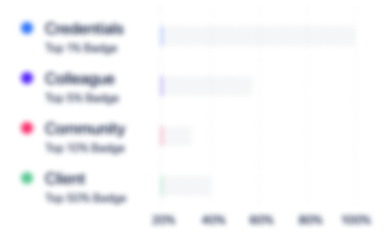
Bio


Credentials
-
Operational Excellence
SKF GroupMar, 2009- Nov, 2024 -
Six Sigma Black Belt
-
Experience
-
Ideal Standard International NV
-
Belgium
-
Manufacturing
-
700 & Above Employee
-
Lean Manager
-
May 2018 - Present
Support, training and follow up of the coordinators of Lean/ Ideal Way implementation within Ideal Standard International (ISI) Operations across Europe. Acting as a Coach, develop the local Coordinators to be able to lead workshops, develop improvement plans, execute diagnostics and implement all Ideal Way tools.• Deliver training to all levels of the company (from Managers to Operators) on Ideal Way transformation philosophy, approach, activity, and appropriate transformation tools• Coach and develop Ideal Way Coordinators, Team Leaders, Line Managers, and others on Ideal Way concepts• Provide the correct methodology in all implementations of Ideal Way within the company• Support the Site Managers on the Steering Committee meetings, guaranteeing that all discussions consider the Lean Principles• Deploy Ideal Way programme and coordinate Transformation projects through all ISI Factories• Lead medium and high complexity Lean events, such as 5S, SMED, TPM, VSM, Kaizen, 3P, Cell Design and Standard Work, Shop Floor Management, Supermarket Design, Logistic Routings, Balanced Receiving, and Supplier Integration• Involve all necessary departments, creating inspiring atmosphere for the company to operate as one team• Perform visits to all company entities, combining review of Lean manufacturing deployment status and results evaluation• Develop new standards for Ideal Way Implementation
-
-
-
-
Media Analyst
-
Feb 2016 - Apr 2018
-
-
-
SKF Group
-
Sweden
-
Industrial Machinery Manufacturing
-
700 & Above Employee
-
Business Excellence & Six Sigma Manager
-
Feb 2007 - Jan 2016
• Perform training on SKF Production System (Toyota Way).• Perform workshops and seminars on Production System philosophy and approach. • Coach and develop SMEs, Team Leaders, Managers, Project leaders on SKF Production System (Toyota Way).• Support Factory management on the Daily management process.• Organize and follow-up Waste walks as per the Lean priorities.• Lead and perform Lean events, such as 5S, TPM, SMED, Kaizen, VSM, Cell Design, Balanced flow, Kan Ban, Andon Lights.• Standardize using of tools, such as Root Cause Analysis, SIPOC, Process map, SPC.• Perform Lean Level Assessment.• Involve all departments to the journey.• Communicate all activities and results.• Present to the management team ongoing projects and results.• Establishing and ensuring close relationship to SKF Group.• Run Six Sigma projects.• Participate in Audit compliance preparation.• Implement best practice thru the organization.
-
-
Education
-
Химико-технологичен и металургичен университет
Master's degree, Industrial Technology/Technician
Community
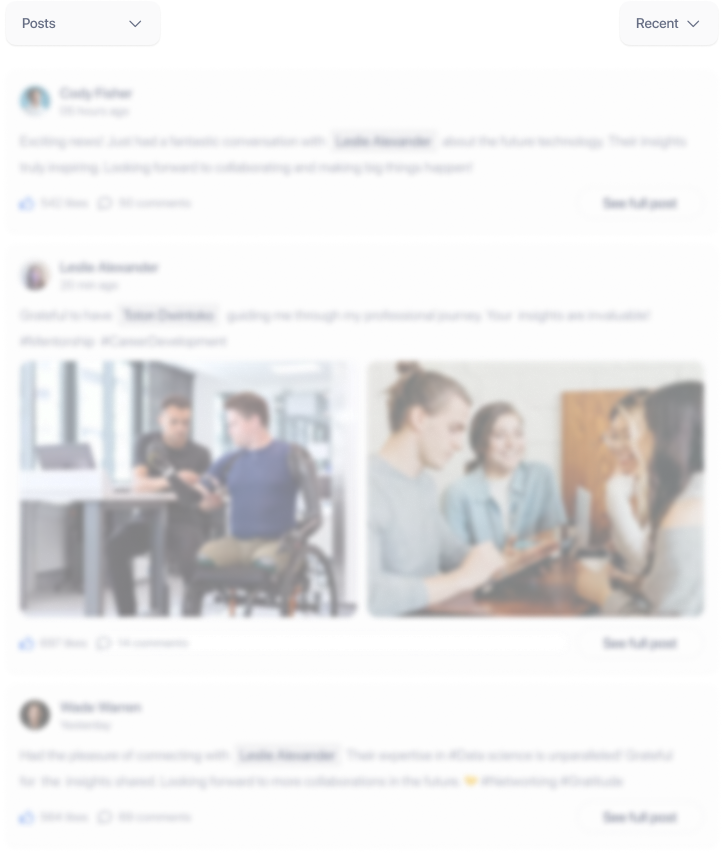