Rachel Tanner
Quality Manager at Cummins at Accelera by Cummins- Claim this Profile
Click to upgrade to our gold package
for the full feature experience.
-
English -
Topline Score
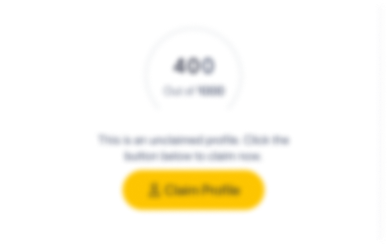
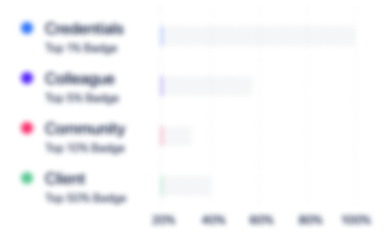
Bio


Credentials
-
ASQ Certified Quality Engineer
American Society of Quality
Experience
-
Accelera by Cummins
-
Industrial Machinery Manufacturing
-
300 - 400 Employee
-
Quality Manager at Cummins
-
Jan 2018 - Present
Well we are officially Cummins employees now! I am excited to start this journey in the New Accelera by Cummins group with my quality team! So ready to take my experience with electrification manufacturing of heavy duty vehicles to the next level! Let's do this! Well we are officially Cummins employees now! I am excited to start this journey in the New Accelera by Cummins group with my quality team! So ready to take my experience with electrification manufacturing of heavy duty vehicles to the next level! Let's do this!
-
-
-
Cummins Inc.
-
United States
-
Motor Vehicle Manufacturing
-
700 & Above Employee
-
Quality Manager
-
May 2022 - Present
ISO 9001:2015 management for manufacturing of electrification of heavy duty vehicles. Corrective Action management for customers and suppliers. PPAP management for customer and suppliers. Management review reporting metrics. Managed up to 10 quality salary and hourly employees.
-
-
Supply Chain Manager
-
Oct 2021 - Aug 2022
Management of the supply chain for electric vehicle components. Sales order entry, purchasing, planning, inventory control, production control, MRB control, product delivery, admin of MRP systems, and provided supply chain metrics and reports, Managed up to 17 salary and hourly supply chain employees.
-
-
Sr Quality Engineer
-
Jan 2020 - Sep 2021
Sustaining quality management of one customer production program, provided customer PPAP submissions and nonconforming materials responses and processing. Provided quality training for multiple new quality employees for second customer production program. Supervised 3 quality technicians.
-
-
Quality Manager
-
Jan 2018 - Jan 2020
ISO 9001 management and implementation for startup company TransPower (who was purchased by Meritor and then Cummins). Provided training and documentation for all ISO 9001 systems. Corrective action management for customers and suppliers. Administrator for nonconforming and change processes at initial implementation of quality systems. Managed 1 quality technician.
-
-
-
Flux Power
-
United States
-
Appliances, Electrical, and Electronics Manufacturing
-
1 - 100 Employee
-
Quality Manager
-
May 2017 - Jan 2018
Responsible for first certification and management of ISO 9001:2015 quality systems for an electrical battery pack fabricator (new technology : lithium ion battery cells), a US based company. Tasks included: Internal audits as a certified ISO 9001 lead auditor, ISO 9001 training and reviews with all departments, first article product reports, reporting and communicating engineering and manufacturing performance metrics to management and all departments, manufacturing and engineering support for electrical pack testing, support for customer service/corrective action (8D), support for UL traceability process, support for safety process. Show less
-
-
-
McCain Manufacturing
-
United States
-
Automation Machinery Manufacturing
-
1 - 100 Employee
-
Quality Systems Manager
-
Mar 2016 - May 2017
Responsible for management of ISO 9001 quality systems for a large sheet metal fabrication manufacturer, a US based company. Tasks included: Internal audits as a certified lead ISO auditor, ISO training and reviews with all departments, submission of PPAP and other first article type document packages to customers, assisting with dimensional inspection and component testing when necessary, reporting and communicating manufacturing performance metrics to management and all departments, customer service/corrective action (8D), customer support for UL traceability process, and revised the entire quality management documentation system from ISO 9001:2008 to transition into ISO 9001:2015 requirements. Managed up to 5 quality employees. (Position eliminated) Show less
-
-
-
Clean Air Power
-
United States
-
Automotive
-
1 - 100 Employee
-
Quality Manager
-
Dec 2010 - Mar 2016
Responsible for management of ISO 9001/ISO 14001 quality and environmental systems for an automotive alternative fuel system components manufacturer, a UK based company. Tasks included: internal audits as a certified lead ISO auditor, developing and creating documented procedures and inspections when necessary, ISO training and reviews with all departments, development and creation of APQP system and documents for engineering process including assisting with drawing review and approval, submission of automotive PPAP and material document packages to the customer, facilitated PFMEA development and documentation, managed 2 quality employees, performed incoming, in-process, and final dimensional inspection, managing calibration process for all measuring equipment, reporting and documentation of manufacturing and engineering performance metrics to management and all departments, Supplier Management and supplier on-site audits in China, Taiwan and Mexico, Customer service/corrective action (8D) reporting. (Plant closed) Show less
-
-
-
S.K.Y. (Sakaiya) Corp.
-
Lansing, Michigan Area
-
Quality Manager
-
Mar 2006 - Aug 2009
Responsible for management of ISO/TS 16949 quality systems for automotive appliques screen printing and plastic molded components, a Japan based company. Tasks included: internal audits as the company delegated lead ISO auditor, developing and creating ISO system documentation from scratch for a new facility in Mexico, developing and creating documented procedures and inspections when necessary, ISO training and reviews with all departments, facilitating APQP process for engineering when necessary, submission of automotive PPAP and material document packages to the customer including IMDS reports and travel to Japan to facilitate customer capacity audits, facilitated PFMEA development and documentation, managed up to 15 visual inspectors, performed incoming, in-process, and final dimensional inspection when necessary, reporting and documentation of manufacturing and engineering performance metrics to management and all departments, Supplier Management and supplier on-site audits, Customer service/corrective action (8D). (Plant downsized) Show less
-
-
-
Wellington, MTI
-
Flint, MI
-
Quality Engineer
-
Feb 2004 - Feb 2006
Wellington: Metal stamping, welding, and assembly of vehicle exterior body components, tier 1 company. Managed ISO/TS 16949 & ISO 14001 quality systems, included tasks for APQP, FMEA, and SPC. Also responsible for supplier management, customer service, and supervised 6 mechanical inspectors. MTI: Metal stamping and assembly of seat belt and engine components. Managed ISO/TS 16949 quality systems. Also main responsibility for new program entry and PPAP submissions to customers. Other tasks were supplier management, customer corrective actions, and in-process manufacturing improvements. (Plant closure) Show less
-
-
-
H.E. Services (Delphi)
-
Flint, Michigan area
-
Supplier Quality Engineer (contract)
-
Nov 2000 - Feb 2004
SE02 Managed all suppliers for Delphi Interiors–Columbus, OH plant. This involved supplier on-site audits, corrective action resolution and verification, and monitored improvement of manufacturing processes for suppliers of: powdered metals, molded plastics, metal castings, metal stampings, electronics, fasteners, motors, assemblies, etc. Travel 25-50%, U.S. travel. MR01 Managed ISO/TS 16949 quality systems, assisted in APQP process, and involved in SPC data development and analysis for Delphi advanced engineering division-Flint, MI. NO00 Managed ISO/TS 16949 quality systems and performed internal audits for Delphi product engineering division - a 7 plant engineering and manufacturing complex in Saginaw, MI. Show less
-
-
Education
-
California Coast University
not complete, Bachelor of Science, Management -
California National University for Advanced Studies
college closed, Quality Assurance Science -
Mott Community College
Associate, Computer Science -
Mott Community College
Certificate, Mathematics
Community
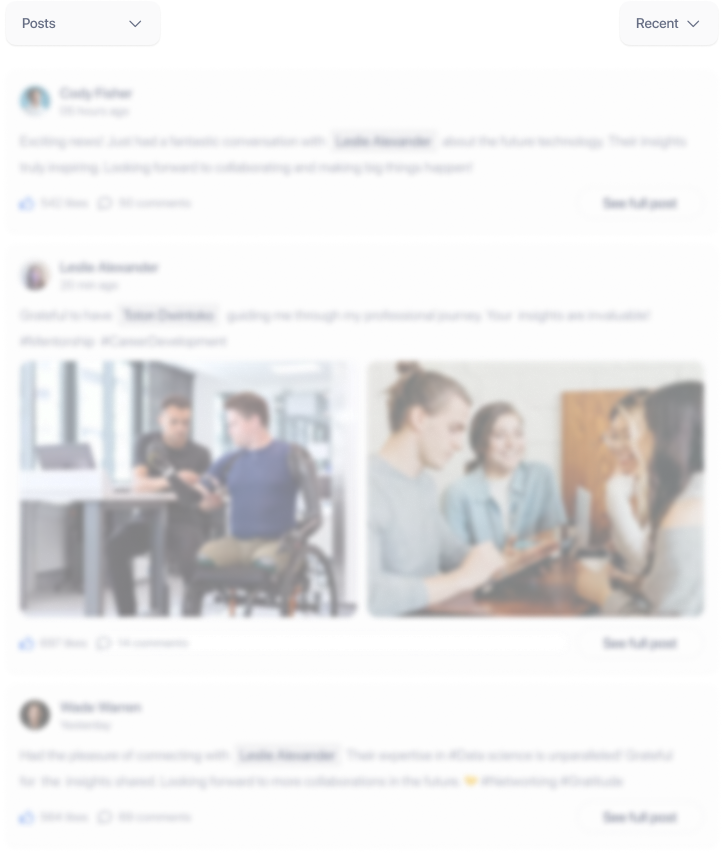