Rabin Pokharel
Turnaround Mechanical Engineer at Engineering & Inspection Services, LLC- Claim this Profile
Click to upgrade to our gold package
for the full feature experience.
-
Nepali -
-
Hindi -
-
English -
Topline Score
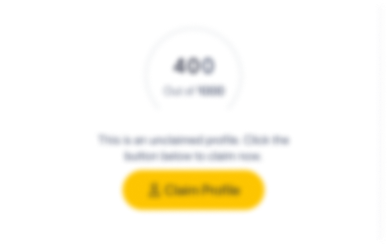
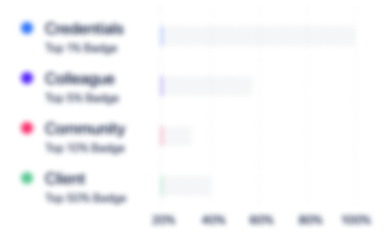
Bio


Experience
-
Engineering & Inspection Services, LLC
-
United States
-
Industrial Machinery Manufacturing
-
100 - 200 Employee
-
Turnaround Mechanical Engineer
-
Nov 2016 - Present
-
-
Reliability Engineer
-
Dec 2015 - Nov 2016
Championed the use of IntelaTrac software in improving operational tasks to ensure reliability of rotating equipment. Created and implemented exchanger backflush program to enhance performance and increase run life of cooling water exchangers. Assisted in executing Turbine Trip Linkage Test and Trip and Throttle Valve Stroking programs. Performed Mitigate Threats to Availability (MTA) work process to identify, prioritize, and mitigate reliability threats. Piloted the use of Critical Task Analysis (CTA) tool to identify potential consequences, controls, and recovery barriers before executing a critical task. Supported rotating equipment failure investigation process by facilitating reliability investigations. Developed pump tool to help operation and maintenance departments prioritize pump repairs. Assisted in developing Fin-Fan Equipment Strategy. Steered rotating and fixed equipment Preventive Maintenance (PM) optimization program. Led interdisciplinary teams to devise and implement systemic solutions for operational and technical issues. Generated monthly Reliability Centered Maintenance (RCM) progress reports and led the presentation to the site leadership team. Collected and analyzed reliability performance data and reliability metric data using GSAP and IntelaTrac. Conducted weekly meetings with unit operators to identify and resolve existing reliability and safety concerns. Assisted in implementing, maintaining and auditing Preventive Maintenance (PM) tasks.
-
-
Mechanical Contact Engineer
-
Aug 2015 - Nov 2015
Covered day to day mechanical engineering issues in Gasoline Hydrotreater, #1 and #3 Reformer, Cat Feed Hydrotreater, Sulfolane, Paraxylene, Pre-treater, Hydrogen Plant, and Hydro Cracker Units. Performed Hot Tap calculation in VCESage and provided necessary welding conditions to the maintenance group to repair steam leaks. Generated and reviewed Management of Change (MOC) documents and completed necessary action items which included Mechanical Engineering Review, Process Hazard Analysis, updating unit records, red lining P&IDs and ISOs, and field verification. Modeled shell and tube heat exchanger in PVElite to calculate maximum allowable differential pressure across existing feed exchangers tubesheets. Evaluated temporary repair options such as clean and coat, engineered clamps, and thermal wrap for corroded thin pipes and recommended the most reliable option to the business team. Developed permanent repair plans for corroded pressure vessel and piping per applicable ASME and API codes and standards. Generated RFQ (Request for Quotation) for exchanger bundle upgrades. Performed minimum thickness and area reinforcement calculations for existing ASME Section VIII Division 1 pressure vessel nozzles using PVElite and provided alert thickness to the inspection group. Assisted ExxonMobil Research and Engineering (EMRE) in generating Mspec and RFQ for upgrading vertical feed exchanger bundle from straight tube to twisted tube technology (Million Dollar Project). Provided mechanical engineering support during unplanned outage of #1 Reformer.
-
-
-
-
Fixed Equipment Engineer
-
Oct 2013 - May 2015
Provided engineering support during three major turnarounds and revamp of Hydrocracker, FCC, Gas Con, and Alky Units. Reviewed and approved turnaround work packages and routine maintenance work packages. Supported turnaround execution activities in the field. Provided assistance in resolving fixed equipment design, operations, and maintenance problems, as well as developed pressure vessel and piping repair plans as per applicable ASME, API, and TEMA codes and standards. Generated and reviewed Management of Change (MOC) documents and updated unit records, tabulations and drawings through the MOC process. Analyzed stresses in leaking bolted flange connections and successfully stopped leaks by upgrading gaskets and providing suitable bolt torque/tension values. Developed torque sheets for new and existing heat exchangers and maintained proper documentation of gaskets, bolts, and washers needed along with specific guidelines essential for consistent leak free service. Performed remaining life assessment of heat exchanger bundles. Assisted in development of Meraux Fired Heater Tube Life Assessment for 21 heaters by analyzing each heater’s operational history. Designed new nozzles in existing pressure vessel and performed reinforcement calculations using CodeCalc and PlantManager. Calculated minimum required thickness and alert thickness for vessels, nozzles, and piping. Reviewed and revised Valero Meraux’s Flange Bolting Basic Practice. Performed Fitness for Service level 1 assessments.
-
-
Mechanical Engineer
-
Oct 2012 - Oct 2013
Upgraded gaskets in shell and tube exchangers following industry best practices for client site to improve reliability of bolted joints. Performed ASME Section VIII Division I Appendix 2 calculations to ensure leak free service. Modeled ASME Section VIII Division I pressure vessel in PV Elite and reviewed code calculations prior to fabrication of the vessel. Designed API 650 Oil Storage Tank using TANK software and reviewed code calculations. Analyzed stresses on Steam Turbine nozzles as per NEMA SM 23. Evaluated stresses and structural responses of various piping systems using CAESAR II. Re-rated ASME Section VIII Division I pressure vessel to a higher design temperature. Assisted client site develop torque sheets of existing equipment prior to startup of new unit.
-
-
-
Coastal Protection and Restoration Authority
-
United States
-
Government Administration
-
1 - 100 Employee
-
Engineering Intern/Co-op
-
Jul 2011 - May 2012
•Assisted the supervisor with administrative work and helped senior engineers in field work. •Maintained various office vehicles and boats and solved day-to-day technical problems in the office. •Assisted the supervisor with administrative work and helped senior engineers in field work. •Maintained various office vehicles and boats and solved day-to-day technical problems in the office.
-
-
-
-
Volunteer Research/Lab Assistant
-
Sep 2010 - Dec 2011
•Explored the lab; exposure to laboratory instruments related to fluid dynamics. •Researched gasification technology and various types of gasifiers. •Assembled a Cold Flow Model Gasifier in laboratory and devised an experimental set up to understand the fluid mechanics of particles injected into the gasifier. •Used research knowledge and principles taught in Fluid Mechanics class to design and install feeding system for the Cold Flow Model Gasifier. •Explored the lab; exposure to laboratory instruments related to fluid dynamics. •Researched gasification technology and various types of gasifiers. •Assembled a Cold Flow Model Gasifier in laboratory and devised an experimental set up to understand the fluid mechanics of particles injected into the gasifier. •Used research knowledge and principles taught in Fluid Mechanics class to design and install feeding system for the Cold Flow Model Gasifier.
-
-
Education
-
UNIVERSITY OF NEW ORLEANS (UNO), COLLEGE OF ENGINEERING
BS, Mechanical Engineering with summa cum laude
Community
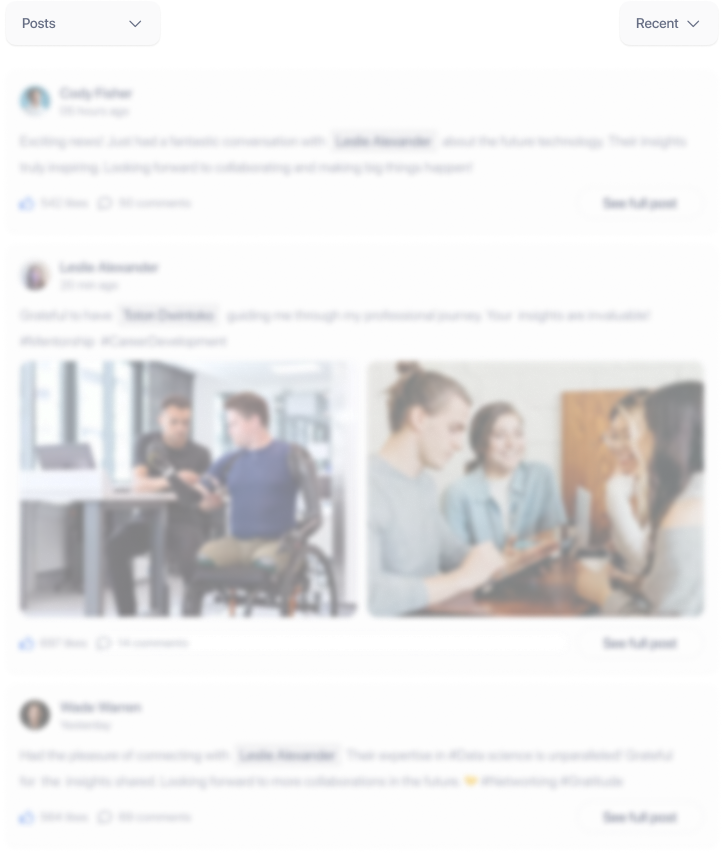