Quintessa Akins
Supply Chain Manager - New Product Development at InVue- Claim this Profile
Click to upgrade to our gold package
for the full feature experience.
Topline Score
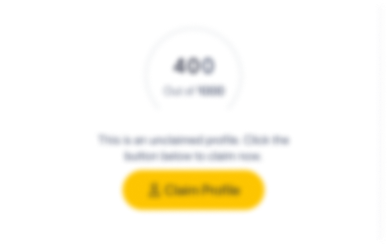
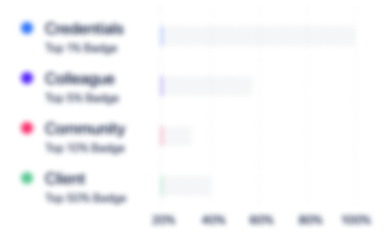
Bio


Experience
-
InVue
-
United States
-
Security Systems Services
-
100 - 200 Employee
-
Supply Chain Manager - New Product Development
-
Oct 2022 - Present
United States • Communicate (email and phone) with global suppliers as needed both during the day and the evening. • Conducts raw material risk analysis for preliminary BOM to identify lead-time risks to the product launch schedule • Develops supply plans, issue purchase orders, and manages appropriate inventory levels in support of forecasted demand for new product launch items. • Conduct periodic review meetings with Sales, Marketing and Demand Planners to review inventory supply plan and current… Show more • Communicate (email and phone) with global suppliers as needed both during the day and the evening. • Conducts raw material risk analysis for preliminary BOM to identify lead-time risks to the product launch schedule • Develops supply plans, issue purchase orders, and manages appropriate inventory levels in support of forecasted demand for new product launch items. • Conduct periodic review meetings with Sales, Marketing and Demand Planners to review inventory supply plan and current stock levels for new launch items. • Communicates project supply plan progress, escalations, and issue analysis to product stakeholders weekly. • Expedite and monitor production and shipments as needed to maintain appropriate inventory in support of actual and planned demand. • Follows established inventory policies, guidelines, and approvals. • Review customer orders and forecasts and adjust supply/demand plans in the system accordingly to ensure accuracy. • Interface with appropriate personnel regarding engineering change requests and the resulting impact on current product supply plan for new product launch items. • Develop, maintain and communicate a planned purchase forecast to the global supply base facilitating planning of long lead-time raw materials for all active items. • Collaborates with internal cross functional team to implement changes to products, processes, or project timelines to resolve escalated issues and produce solutions to ensure adherence to established product launch schedule. • Assist with raw material supply issues with global suppliers, both InVue and vendor supplied, in order to help manage/reduce lead times, excess, obsolete inventories and high MOQs. • Monitor supplier owned raw material inventories for NPD items to ensure appropriate supply to support forecast within agreed lead-times. • Monitor and ensure item attributes are set up in base master system: item description, weights and dimensions, bill of materials, other critical item attributes.
-
-
Supply Chain Manager Brands- ECR
-
Feb 2021 - Oct 2022
Charlotte, North Carolina, United States • Develops supply plans, issue purchase orders, and manage appropriate inventory levels in support of forecasted demand for custom product items. • Conduct periodic review meetings with Sales, Marketing, and Demand Planners to review inventory supply plan for custom product item. • Expedite and monitor production and shipments as needed to maintain appropriate inventory in support of actual and planned demand. • Follow established inventory policies, guidelines, and approvals. •… Show more • Develops supply plans, issue purchase orders, and manage appropriate inventory levels in support of forecasted demand for custom product items. • Conduct periodic review meetings with Sales, Marketing, and Demand Planners to review inventory supply plan for custom product item. • Expedite and monitor production and shipments as needed to maintain appropriate inventory in support of actual and planned demand. • Follow established inventory policies, guidelines, and approvals. • Review customer orders and forecasts and adjust supply plans accordingly ensuring supply/demand information in the system is accurate. • Communicates planned product launch details for custom product items to the global supply base facilitating planning of long lead-time raw materials and manufacturing capacity planning when applicable. • Assist with raw material supply issues with global suppliers, both InVue and vendor supplied, in order to help manage/reduce lead times and high MOQs. • Monitor supplier owned raw material inventories for custom/standard product items to ensure appropriate supply to support product launch within agreed lead-times reducing risk of excess and obsolete inventories. • Interface with appropriate personnel regarding engineering change requests and the resulting impact to current product launch schedules and supply plans for standard and custom products. • Monitor and ensure product attributes are set up in base master system including but not limited to descriptions, units of measure, weights and dimensions, bills of materials and other critical product attributes. • Communicate (email and phone) with global suppliers as needed both during the day and the evening.
-
-
Senior Materials Buyer
-
Jul 2018 - Feb 2021
Charlotte, North Carolina Area • Develops and recommends supply strategies for buy/sell materials and other high risk materials. • Analyzes lead times, expected volumes, manufacturing trends and availability of spot market supply or alternatives. • Issues purchase orders to raw materials vendors and manages appropriate inventory levels in support of demand for supplied raw materials. • Processes shipment request from contract manufacturers and provide timely and accurate delivery schedules. • Expedites and… Show more • Develops and recommends supply strategies for buy/sell materials and other high risk materials. • Analyzes lead times, expected volumes, manufacturing trends and availability of spot market supply or alternatives. • Issues purchase orders to raw materials vendors and manages appropriate inventory levels in support of demand for supplied raw materials. • Processes shipment request from contract manufacturers and provide timely and accurate delivery schedules. • Expedites and monitors production and shipments as needed to maintain appropriate inventory in support of actual and planned demand. • Develops, maintain and communicates a planned purchase forecast to the supply base facilitating planning of their long lead-time raw materials. • Assists with raw material supply issues with Global suppliers to help manage/reduce lead times and high minimum order quantities (MOQs). • Monitors supplier owned raw material inventories on critical components to insure appropriate supply to support demand within agreed lead-times reducing risk of excess and obsolete inventories. • Works closely with the Electrical Engineering team to insure selected parts have a sustainable supply chain and also develops supply strategies to insure continuous supply. Planner: • Develops ordering, supply plan, and inventory projections in order to manage inventory turns. • Places purchase orders with suppliers (primarily in China) and expedites/monitors production and shipments as needed to support customer orders. • Places purchase orders with suppliers (primarily in China) and expedites/monitors production and shipments as needed to meet orders. • Recommends capacity additions and/or inventory builds based on demand signals. • Develops special production plans, manage, execute and communicate such plans to support demand.
-
-
-
ATS Corporation
-
Canada
-
Automation Machinery Manufacturing
-
700 & Above Employee
-
Internal Auditor
-
Nov 2017 - Jul 2018
South Carolina **Plant Closing Summer 2018** • Ensure compliance with ISO 9001:2015 standards and requirements •Perform regular internal audits of the Quality Management System •Perform department inspections across local division •Work closely with the Quality Systems and HSE Coordinator and program managers •Report audit conclusions and corrective actions to program managers and corporate management • Manage root cause analysis, development of corrective and preventive actions and… Show more **Plant Closing Summer 2018** • Ensure compliance with ISO 9001:2015 standards and requirements •Perform regular internal audits of the Quality Management System •Perform department inspections across local division •Work closely with the Quality Systems and HSE Coordinator and program managers •Report audit conclusions and corrective actions to program managers and corporate management • Manage root cause analysis, development of corrective and preventive actions and follow-up for effectiveness
-
-
Buyer
-
Jan 2017 - Jul 2018
South Carolina **Plant Closing Summer 2018** • Request quotations, negotiate pricing and lead-times and execute purchase orders for specified material released in ERP system. Pre-quote bill of materials prior to station release. • Perform purchase order administration, order acknowledgements, ASN, expedite items for earlier delivery, follow-up on late deliveries, and back order items. • Administer data collection regarding supplier quotation price and lead-times and on-time delivery. • Monitor… Show more **Plant Closing Summer 2018** • Request quotations, negotiate pricing and lead-times and execute purchase orders for specified material released in ERP system. Pre-quote bill of materials prior to station release. • Perform purchase order administration, order acknowledgements, ASN, expedite items for earlier delivery, follow-up on late deliveries, and back order items. • Administer data collection regarding supplier quotation price and lead-times and on-time delivery. • Monitor and execute project and department metrics relative to material budgets, material availability and on-time delivery. • Participate on assigned project team; attend team meetings, maintain material availability, communicate/follow up with supply chain team regarding project schedule and priorities, and review project budget status. • Provide immediate feedback to appropriate project managers and/or supply chain project lead regarding material issues, expediting fees and delivery concerns. • Maintain supplier contact lists and line cards. • Execute supplier set-up process with all required documentation. • Assist in warehouse as needed; receive, kit, and ship materials. • Follow all procedures and work instructions as defined in the ISO 9001 Quality Management System. • Manage global relationships with selected major suppliers. • Negotiate cost with suppliers to receive the best discount structure possible. • Negotiate with suppliers to resolve problems on prices, deliveries or specifications. • Accountable for material order dates and delivery to coincide with shop floor requirements. • Organize and provide visibility of materials at the point of use for assembly by shop personnel.
-
-
-
HUBER+SUHNER
-
Switzerland
-
Appliances, Electrical, and Electronics Manufacturing
-
700 & Above Employee
-
Buyer
-
Dec 2015 - Dec 2016
Charlotte, North Carolina • Review and negotiate purchase price, quality, lead-time and delivery of product to engineered specifications. • Issue RFQ’s ensuring pricing and build requirements are in line with customer needs • Research and analyze current / future requirements and manage inventory levels to meet production and customer demands, while achieving company inventory turn goals. • Operations interaction on inventory controls, shortage analysis and responsiveness, production schedule flexibility… Show more • Review and negotiate purchase price, quality, lead-time and delivery of product to engineered specifications. • Issue RFQ’s ensuring pricing and build requirements are in line with customer needs • Research and analyze current / future requirements and manage inventory levels to meet production and customer demands, while achieving company inventory turn goals. • Operations interaction on inventory controls, shortage analysis and responsiveness, production schedule flexibility, customer delivery requirements. • Participate in Engineering change activities, communicating revisions to suppliers and assess cut-in dates based on existing supply position, minimizing obsolete or slow moving inventory. • Participate in cross-functional teams on new product development, process improvements and continuous improvement initiatives.
-
-
Expeditor
-
Jul 2015 - Nov 2015
Warren, New Jersey • Develops and maintains necessary records and files for efficient operation. Performs other position-related duties as assigned by General Manager. • Prepares purchase orders using SAP • Discusses defective or intolerable goods or services with inspection or quality control personnel • Prepares orders and follows up on orders to expedited delivery and shipment. • Follows the sequence of operations on required parts and progress of purchase orders • Reports all schedule and… Show more • Develops and maintains necessary records and files for efficient operation. Performs other position-related duties as assigned by General Manager. • Prepares purchase orders using SAP • Discusses defective or intolerable goods or services with inspection or quality control personnel • Prepares orders and follows up on orders to expedited delivery and shipment. • Follows the sequence of operations on required parts and progress of purchase orders • Reports all schedule and operating/mechanical difficulties to all parties associated • Provides exceptional customer service to internal and external customers • Processes and coordinates with production, quality control, inventory, and shipping to maintain production requests • Checks production schedules, priorities jobs, verify progress of jobs, investigate hold-ups and intervene when variations must be made to meet deadlines. • Participates in the purpose of procedures designed to increase operations efficiency and work flow processes (metrics report).
-
-
Order Fulfillment Representative
-
May 2014 - Jul 2015
• Developed and maintained necessary records and files for efficient operation. Performed other position-related duties as assigned. • Prepared purchase orders using SAP • Participated in the purpose of procedures designed to increase operations efficiency and work flow processes (metrics report). • Entered purchase orders in a timely fashion, scrubbed bills of materials for component availability and quality clauses • Provided customer support including order status, changes… Show more • Developed and maintained necessary records and files for efficient operation. Performed other position-related duties as assigned. • Prepared purchase orders using SAP • Participated in the purpose of procedures designed to increase operations efficiency and work flow processes (metrics report). • Entered purchase orders in a timely fashion, scrubbed bills of materials for component availability and quality clauses • Provided customer support including order status, changes, follow up on discrepancies, and resolves customer issues as a contact between multiple departments • Provided order status and tracking information to every customer. • Interacted with customers positively and professionally at all times for all general customer service activities. • Provided support pertaining to all aspects of Customer and Consumer Support via phone and email as required. • Assisted Customer Service Manager with additional tasks as requested.
-
-
-
-
Executive Assistant
-
Jul 2012 - Mar 2014
Edison, NJ • Operated as a team player. Responded to requests for assistance from other business units and groups as required and offered assistance during down times. • Performed administrative duties in an efficient and timely manner. Sought ways to improve efficiency. • Prioritized conflicting needs; handled matters expeditiously, proactively, and followed through on projects to ensure successful completion, often with deadline pressures. • Prepared documents required to maintain balanced… Show more • Operated as a team player. Responded to requests for assistance from other business units and groups as required and offered assistance during down times. • Performed administrative duties in an efficient and timely manner. Sought ways to improve efficiency. • Prioritized conflicting needs; handled matters expeditiously, proactively, and followed through on projects to ensure successful completion, often with deadline pressures. • Prepared documents required to maintain balanced accounts for review and approval. • Screened telephone calls, answered inquiries or directed caller to the appropriate individual for further information and/or resolution. •Maintained a high degree of personal organization and self-management. Show less
-
-
Education
-
Berkeley College
Bachelor of Applied Science (BASc), Business Administration and Management, General
Community
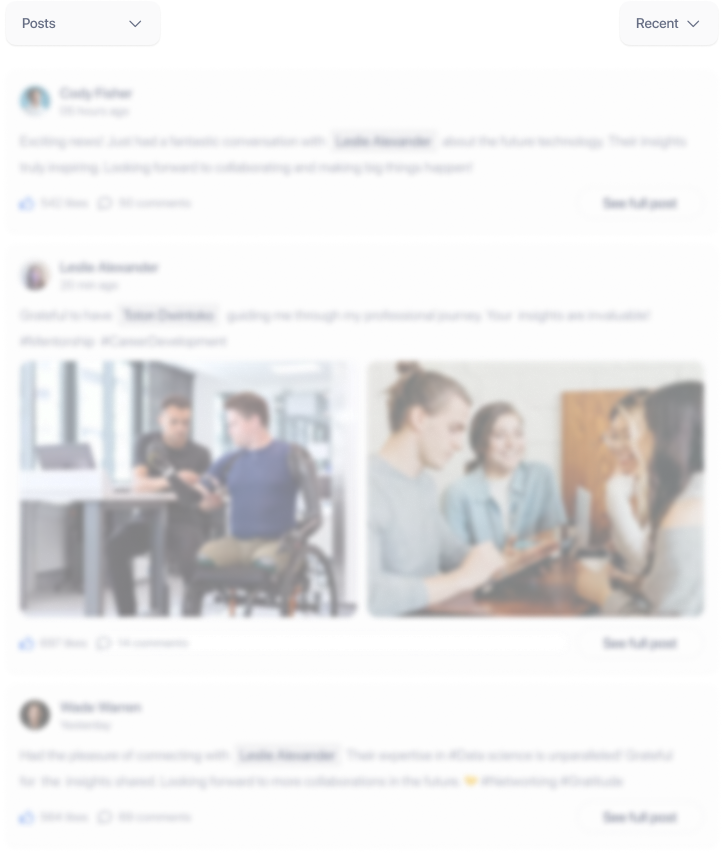