Przemyslaw Mrozek
Quality Assurance Specialist at Kerakoll Group- Claim this Profile
Click to upgrade to our gold package
for the full feature experience.
-
polski Native or bilingual proficiency
-
angielski Professional working proficiency
-
niemiecki Elementary proficiency
Topline Score
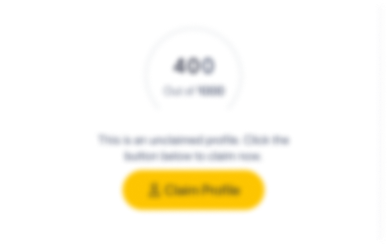
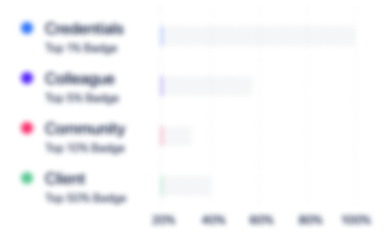
Bio


Credentials
-
MES workshops: Plant Application, Historian 6.0, Client Access API
VIX AutomationMar, 2016- Nov, 2024 -
Manager of Occupational Health and Safety Management Systems against OHAS 18001:2007 specification
Lloyd's RegisterJul, 2013- Nov, 2024 -
Internal QMS Auditor
Lloyd's RegisterJun, 2013- Nov, 2024 -
Manager of Environmental Management Systems against ISO 14001:2004
Lloyd's RegisterJun, 2013- Nov, 2024 -
Manager of Quality Management Systems against ISO 9001:2008
Lloyd's RegisterJun, 2013- Nov, 2024
Experience
-
Kerakoll Group
-
Italy
-
Wholesale Building Materials
-
700 & Above Employee
-
Quality Assurance Specialist
-
Nov 2022 - Present
The specific responsibility of this function is to represent GM in the context of the Quality Management System, assuring the correct implementation thereof at all levels. Main tasks: ❑To prepare and keep the Quality Management System Manual up-to-date, cooperate and ensure the generation of all Quality Management System documents; ❑Prepare and issue Quality Management System documents and provides their distribution. ❑To cooperate with SI in the preparation of appropriate procedures assuring the correct implementation and application of the Quality Management System. ❑Support personnel involved in application of disposition of Quality Management System performing any necessary audits. ❑Ensuring the promotion of awareness of customer requirements throughout the organization. ❑To supply GM with everything he needs for the periodic review of the Quality Management System, submitting suggestions on how to improve quality on the basis of notifications received, random audits and meetings with various organisational departments; ❑Gather and appraise proposals and suggestions received from all levels of the company in order to ensure that the Quality Management System appropriately reflects the actual context of the company; ❑To assure quality standards are complied with throughout the entire organisational system, performing any necessary audits; ❑To continually raise the awareness in organisational departments of quality problems and compliance with procedures by way of regular meetings at all levels; ❑To manage nonconformities and corrective/preventive actions, checking the implementation and effectiveness thereof. ❑To supervise the activity of calibration to assure the calibration documents are released and all instruments are conform. Show less
-
-
-
ABB
-
Switzerland
-
Automation Machinery Manufacturing
-
700 & Above Employee
-
Supplier Developement Specialist/Supplier Quality Engineer
-
Aug 2017 - Oct 2022
Qualify potential and existing external suppliers of direct materials and services (DM&S). Quality surveillance at supplier manufacturing site. Perform supply quality issue resolution including supplier claims preparation. Lead supplier performance evaluation and supplier quality development activities. Establish and maintain local supplier quality related procedures & practices, based on global procedures and secure full supplier management in ProSupply. Constant developement of existing external suppliers based on Lean Management. Show less
-
-
-
BSH Sprzęt Gospodarstwa Domowego Polska
-
Poland
-
Manufacturing
-
700 & Above Employee
-
Supplier Developer
-
Jul 2016 - Jul 2017
• Leading Supplier Development projects on existing supplier processes in terms of improving quality, productivity, internal logistic • Enabling new suppliers and products during relocations projects • VSM/ VSD, CSA, using lean tools (SMED, 5S, Poka Yoke, Kanban), problem solving techniques (Ishikava, 5W), TPM tools (e.g. OEE, Autonomous/ Planned Maintenance), leading cross-functional workshops • First and direct contact person for internal customers as there are Purchasing, Quality Management, Logistics and Development • Supporting internal customer pro-actively in the selection, specification and projects set-up and suggesting constructively most adequate approaches • Defining the current cost situation, providing negotiation arguments to the Purchaser based on CSA and Cost Transparency Show less
-
-
-
Procter & Gamble
-
United States
-
Manufacturing
-
700 & Above Employee
-
-
Oct 2015 - Jun 2016
project supervision, coordination and implementation management of SAP/RTCIS/Proficy for new business in P&G Factory in Aleksandrow, monitoring and realization of Implementation Plan, ensuring the proper conduct of the project implementation, current, close contact with an external provider, daily cooperation with project teams in the Czech Republic and Poland, professional support in the design, configuration and startup of systems, standardization and validation of the implemented systems. Show less
-
-
-
Aug 2013 - Oct 2015
merit-based support for Making & Packing production lines in terms of SAP/RTCIS, technical support for production in configuration and optimization of technological processes, performing ongoing trainings for production technicians, initiating actions to improve and optimize production process, involved in implementation of cost saving projects within SAP/RTCIS,
-
-
-
Oct 2008 - Aug 2013
implementation and coordination of quality procedures, preparation and supervision of quality control documentation, daily reports delivery analyzing quality problems, identification of discrepancies, production support in terms of quality control and performing the highest quality standards, approval of Individual Packing Specification and Batch Production Report;
-
-
Education
-
Uniwersytet Łódzki
Post-graduate studies, Quality Manager, Auditor, Quality Management Systems ISO 9000 -
Uniwersytet Łódzki
Bachelor's degree, Managing People in Organizations -
Politechnika Łódzka
Civil Engineering
Community
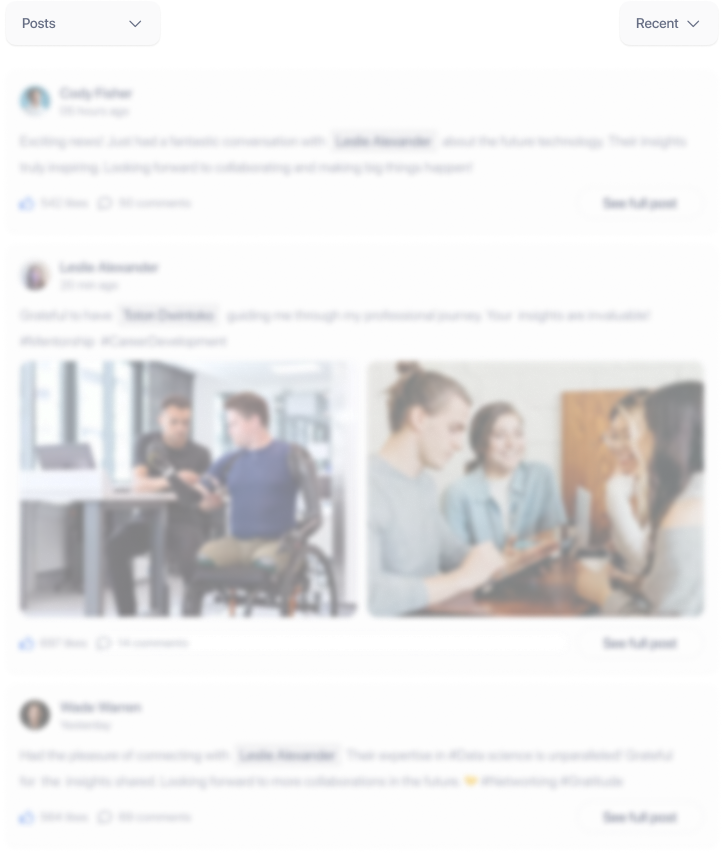