
Priscila Lopes
Supply Chain Manager at Response Biomedical Corp.- Claim this Profile
Click to upgrade to our gold package
for the full feature experience.
-
Inglês Native or bilingual proficiency
-
Francês Professional working proficiency
-
Portuguese Native or bilingual proficiency
Topline Score
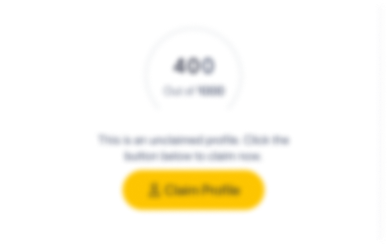
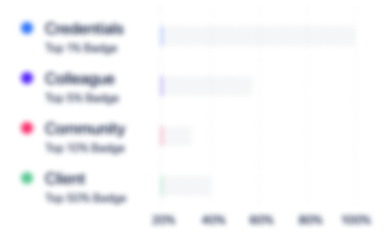
Bio

Mariana C.
I started working with Priscila in 2008 when she acted as a Planner in Biomérieux. At this time we had a product line whose planning was very complex, but Priscila did very well! After a while, she assumed the position of Supply Chain Manager, which she always played in partnership with Quality area and focused on the objectives of the company.

Mariana C.
I started working with Priscila in 2008 when she acted as a Planner in Biomérieux. At this time we had a product line whose planning was very complex, but Priscila did very well! After a while, she assumed the position of Supply Chain Manager, which she always played in partnership with Quality area and focused on the objectives of the company.

Mariana C.
I started working with Priscila in 2008 when she acted as a Planner in Biomérieux. At this time we had a product line whose planning was very complex, but Priscila did very well! After a while, she assumed the position of Supply Chain Manager, which she always played in partnership with Quality area and focused on the objectives of the company.

Mariana C.
I started working with Priscila in 2008 when she acted as a Planner in Biomérieux. At this time we had a product line whose planning was very complex, but Priscila did very well! After a while, she assumed the position of Supply Chain Manager, which she always played in partnership with Quality area and focused on the objectives of the company.

Experience
-
Response Biomedical Corp.
-
Canada
-
Medical Equipment Manufacturing
-
1 - 100 Employee
-
Supply Chain Manager
-
Oct 2021 - Present
-
-
-
Delta Controls Inc.
-
Canada
-
Appliances, Electrical, and Electronics Manufacturing
-
200 - 300 Employee
-
SAP Production Planner and Scheduler
-
Sep 2019 - Oct 2021
-
-
-
bioMérieux
-
France
-
Biotechnology Research
-
700 & Above Employee
-
Supply Chain Manager
-
2013 - Jul 2018
Responsibilities:- Management and training of more than 20 people team, managing the processes of the Planning, Warehouse, Distribution, Procurement, Master data, Foreign Trade, Customer Service, RMA, and Invoicing. - Implementation and application of Policies of Attendance to the Client focused in customers´ satisfaction.- Implementation of process S&OP (Sales & Operations Planning) applied to national and Latin American market.- Management and monitoring of KPIs: OTIF (on time, in full), Stock Level, Scrap, Forecast Accuracy, Logistic Operator Performance, Transport Performance, Budget and Distribution Claims.- Bid management: Carrier, logistic operator, forwarding and loading agents.- Leader of implementation project of MRP/ROP for stock of parts.- Leader of restructuration projects of Warehouse & Shipment areas, focused in optimization of space, storage and rise of dispatch capacity. Leading project of 23 MBRL stock transference, segmenting in reagent, parts and instrument for a Logistic Operator.- Leader of validation project of distribution of cold chain products across Brazil. Management of transport ensuring the best modality, packing quality and products´ safety, preserving the loading integrity and quality, and ensuring the delivery deadlines to the customers. Management and monitoring of the transport performance and transport.- Leader of optimization project of logistic chain and redefinition of best geographic location for Warehouse, transferring 25 MBRL of cold chain stock to other state in a new Logistic Operator.- Leader of SAP implementation project focused in Warehouse and interface between SAP & WMS of the Logistic Operator.- Experience in standard ISO (9001/2015 and 13485/2016), RDC 16 (Good Manufacturing practices, distribution storage), GMP (Good manufacturing practice), being responsible for definition and follow of action plans, preventive and corrective actions of Supply Chain area.
-
-
-
AkzoNobel
-
Netherlands
-
Chemical Manufacturing
-
700 & Above Employee
-
Planning Manager
-
2011 - 2013
Responsibilities:- Responsible for stock management of 3 Warehouse that act as Factory and Distribution Center (São Gonçalo, Recife and Blumenau), managing the stock level, totalizing in 30 million, and the stock supply between them.- Responsible for the planning and management of finished product and raw material stock and for Policies of storage applied to them, as safety stock, economic batch and ABC/XYZ classification.- Implementation and management of KPI of Inventory, Stock out, Schedule Adherence and OTIF measurement. - Leader of development project of S&OP process (Sales & Operation Planning), achieving the monitoring of the process by monthly meetings with the Senior Managers.- Responsible for Demand process. Monitoring and evolution of sales, new projects and customers, signaling the team of Sales to storage strategy necessary for attendance. Implementation of forecast model.- Follow up with Marketing and Sales areas in introduction and discontinuation of finished products.- Leader of implementation projects of MRP model, upgrading the knowledge of model and application in ERP system. Implementation of Replenishment model in 3 Distribution Center. Implementation of Kanban model for inputs of packing type.- Leader of Project of Business Improvement with the objective of upgrade the service level (OTIF) of the company, involving the Supply Chain, Sales, Laboratory, Marketing, IT and Financial Department. - - - Focal point in the contract with the main office of different sectors in subjects of process upgrading and improvement of results. Participation and leadership in Project of processes upgrading of Factory Floor with the objective to reduce time and cost, rising the efficiency.- Management of 4 direct people team, responsible for Planning processes of finished products and raw materials, Warehouse and Distribution Centers.
-
-
-
bioMérieux
-
France
-
Biotechnology Research
-
700 & Above Employee
-
Planning Supervisor
-
2001 - 2011
Responsibilities:- Monitoring of finished products and raw material, all strategical planning related to them, with short, medium and large deadline vision, being responsible for all MRP system and parameterization of each SKU. - Responsible for an inventory of 20MBRL. Practice in methodologies for analysis and revision of safety stock, lead-time, economic batch, classification ABC and all relative parameter to product storage management.- Management of stock control of finished and semi-finished products, raw material and inputs, and control of organizational structure of industrial planning. Experience in factory floor control. Knowledge of importation and exportation.- Creation and management of indicators to measurement of strategical planning, inventory and attendance level. Follow up of accounting of products information.- Leader of implementation project of MRP model, upgrading the knowledge of model and application in ERP system. Participation of Drawback project.- Leader of process development project S&OP (Sales & Operations Planning), achieving the monitoring of process by monthly meetings with the Senior Management.- Participation in the implantation of new ERP system (Movex) as key user, being responsible for all Production Planning process. - Communication center with the main external and internal customers (Marketing, Industrial Directory, Commercial, etc.) and international customers and suppliers.
-
-
Education
-
Universidade Estácio de Sá
Logistics, Logistics, Materials, and Supply Chain Management
Community
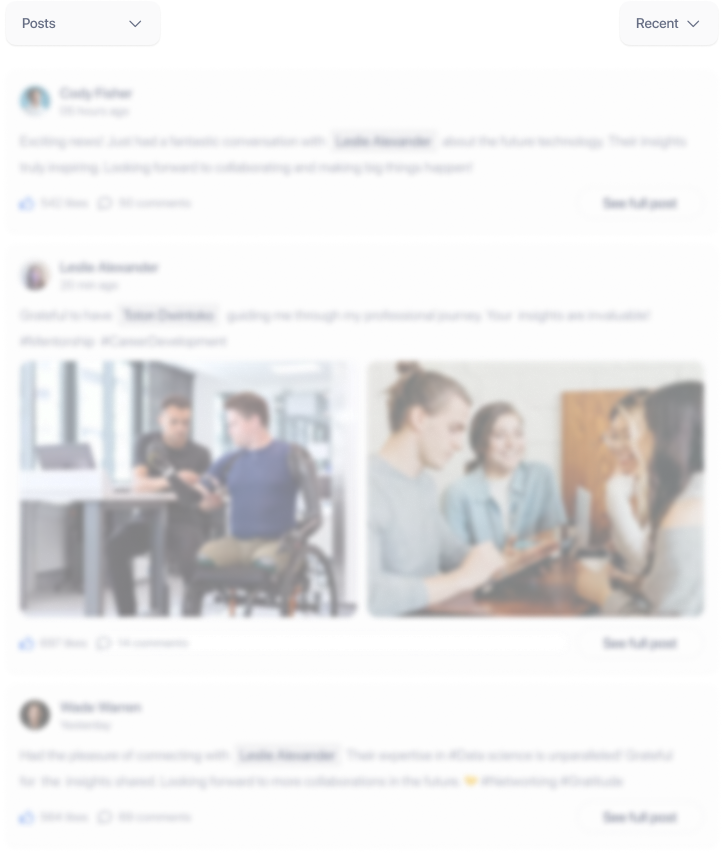