Premendra Patil
Supply Chain Manager at Vision Food Innovations- Claim this Profile
Click to upgrade to our gold package
for the full feature experience.
-
English -
-
Hindi -
-
Gujarati -
Topline Score
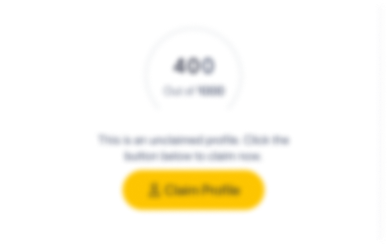
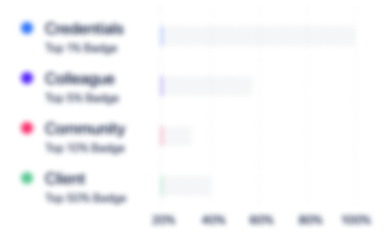
Bio

Cliffordviegas Clifford
I know Premendra as a hard working and focused person. He was always systematic and carries a cool head on his shoulders. Wish him all the best.

Lakshman Balakrishnan
I have known Premendra Patil for over 6 years .Patil's strength lies in his ability to break a requirement into minutest details and identifying the problem areas . He is an excellent planner with very strong analytical abilities . He is a cool customer with lots of patience and endurance. An asset wherever he goes .

Cliffordviegas Clifford
I know Premendra as a hard working and focused person. He was always systematic and carries a cool head on his shoulders. Wish him all the best.

Lakshman Balakrishnan
I have known Premendra Patil for over 6 years .Patil's strength lies in his ability to break a requirement into minutest details and identifying the problem areas . He is an excellent planner with very strong analytical abilities . He is a cool customer with lots of patience and endurance. An asset wherever he goes .

Cliffordviegas Clifford
I know Premendra as a hard working and focused person. He was always systematic and carries a cool head on his shoulders. Wish him all the best.

Lakshman Balakrishnan
I have known Premendra Patil for over 6 years .Patil's strength lies in his ability to break a requirement into minutest details and identifying the problem areas . He is an excellent planner with very strong analytical abilities . He is a cool customer with lots of patience and endurance. An asset wherever he goes .

Cliffordviegas Clifford
I know Premendra as a hard working and focused person. He was always systematic and carries a cool head on his shoulders. Wish him all the best.

Lakshman Balakrishnan
I have known Premendra Patil for over 6 years .Patil's strength lies in his ability to break a requirement into minutest details and identifying the problem areas . He is an excellent planner with very strong analytical abilities . He is a cool customer with lots of patience and endurance. An asset wherever he goes .
0
/5.0 / Based on 0 ratingsFilter reviews by:
Experience
-
Vision Food Innovations
-
Canada
-
Food and Beverage Manufacturing
-
1 - 100 Employee
-
Supply Chain Manager
-
Oct 2022 - Present
-
-
-
CT Bakery
-
Canada
-
Food and Beverage Manufacturing
-
1 - 100 Employee
-
Warehouse & Logistic Manager
-
May 2021 - Jul 2022
Responsible for the day-to-day performance of the warehouse / logistics, through all shifts, including safety, labour planning, efficiencies and ensuring compliance with the organization policies and Vision. • Oversees Daily Warehousing functions, monitoring work to ensure all activities are carried out effectively and efficiently. • Maintains a safe, organized and clean work environment. • Oversees the daily Shipping and Receiving & input of statistical data in support of measuring KPI’s. • Performs setup, layout and ensures the efficient utilization of storage space. • Ensure employees follow the correct procedure for picking orders, in accordance with organization and customer specific policies and procedures. • Ensure equipment is in proper condition and take necessary action when needed to minimize down time. • Ensure only qualified employees operate equipment and that they are operated safely at all times. • Ensure customer specifications for code dating, as outlined in picking documents, are being met at all times and in lieu of specific instruction, FIFO is strictly adhered to. • Develop regular channels of communication with suppliers to the warehousing function, as well as, the direct functional customer in Transportation, to help mitigate circumstances that could impact daily and / or weekly plans. • Ageing analysis • Provide support for Human Resources functions applicable to the team including hiring, onboarding, performance management and disciplinary matters. Retrain a team that meets the needs of the organization. • Develop team capabilities through continued on-the-job and formal training opportunities and coaching. • Adhere/comply with company policies and procedures. • Recommend, develop and implement enhancements and improvements to departmental policies and procedures • Apply Functional knowledge of warehouse best practices, oversee warehouse efficiency. Show less
-
-
-
C T BAKERY
-
United Kingdom
-
Manufacturing
-
Operations Manager
-
Mar 2020 - Apr 2021
• Ensure all operations are carried on in an appropriate, cost-effective way • Improve operational management systems, processes and best practices • Formulate strategic and operational objectives • Examine operational labour cost and use them to improve profitability • Monitor production KPIs • Issue Daily Production Schedule to Production team, verify variance and compliance to schedule. • Weekly / Daily meeting with all departments. Pass on management vision and exceptions from the team. • Recruit, train and supervise staff • Find ways to increase quality of customer service through employee engagements and analyse root cause of customer complaints. • As a Health and Safety management representative ensure H&S practices are in place. • Motivate Sanitation team to be best in class • Approve the PM Schedule of maintenance. • Partner with HR in building the right team for the company. • Strategic decision for inventory management through Purchase / Warehousing. • Support the regulatory affairs team and make the plant AUDIT ready at all times. Show less
-
-
-
-
Materials / Shipping-Receiving Supervisor ; Production Scheduler : Supervisor
-
Mar 2012 - Mar 2020
• Supervised Material coordinators & shipper - receiver. • Coordinate with production leads in Bakery & Packaging. • Generate Master Production Scheduling and control • Managed Production Scheduling and Capacity Planning through forecast and firm orders. • Logistics – Set appointments for Shipping Finish Goods, Receiving raw & packing materials • Manage Production works order & reconciliation. • Execute Inventory Analysis : Periodic Cycle Counts & variances reconciliation, ABC analysis • Managed Tractability exercise for product recall. • Compliance to Schedules, Document controls & cross job training. • Manage Procurement Process. • Handled foretasted demand to suppliers for timely availability of materials, MOQ etc. • Monitored contracts, determine the need for changing suppliers or Transport. • Managed and review records of items bought, costs, deliveries, product performance, and inventories transaction. • Supervised schedules, documents control & cross job training. • Review forecast for Capacity Management for effective production scheduling and maximum customer satisfaction. • Coordination with QA for CAPA and CIP • The British Retail Consortium (BRC) - Internal Auditor • Hazard Analysis Critical Control Point (HACCP) - Plan developer • Waste management, cross functional training & support; • JIT; GMP practices; Health & Safety compliance. • Support in investigations from account parables of invoices / Queries. • Coordination and support to customer service for effective planning processes. Show less
-
-
-
-
Manager Production Planning, Purchasing, Logistics & Inventory control
-
Mar 1992 - Aug 2011
• Supervised team of 4 production planners & production coordinators. • Analyzed, maintained and executed materials requirement plan (MRP). • Give action plans to Purchase/buyers for procurement as per MRP outputs i.e. need date, Quantity and standard agreed buying cost with MOV/MOQ approvals. • Periodic reviews of Potential Excess inventory, Potential Obsolete Materials, High Stocks levels, safety stocks working, reorder point, ABC analysis, write-off proposals etc. • Tracking inventory - Record Accuracy - Cycle Counting - Physical inventory. • Controlled Bill of Material & Item Master accuracy. • Analyzing and verification of all forecast data provided by sales, feedback on schedule plan based on inventory position. • Generated accurate forecasts by reviewing past data, inventory levels, current plans and incoming Orders. • Liaising between sales and operations / participate in monthly S&OP Process • Lead forecasting process, stability analysis in the process. • Tracking & Chasing of Finished Products from Order inquiry to Shipment to customer feedback on safe receipt • Rejection management and their root cause analysis with quality department • Work closely with Sales & Production departments to prepare and maintain the Sales & Operation Plan. • Focused in development & launching of new products as per specs provided, incorporation of the same in Master data control. • Maintained Documents as per ISO 9001:2008, Adherence to Standard Operating Procedures • Maintained strong relationships & processes with all interfacing departments for productivity and efficiency. • Coaching, guidance and motivation to staff Show less
-
-
Education
-
Sardar Patel University
Bachelor of Science (B.Sc.), Physics -
Guelph Food Technology Centre
BRC internal Auditor -
Guelph Food Technology Centre
HACCP -
APICS
BSCM - Supply Chain Management, Production and Inventory Management
Community
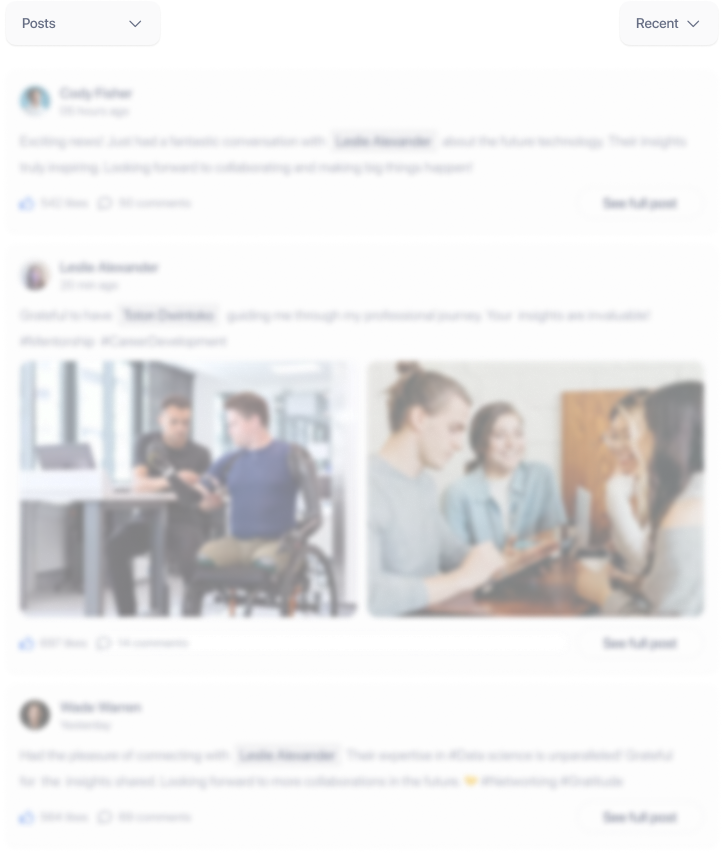