Prasad Kulkarni
Senior Engineer - Body Structures at Mahindra Automotive North America- Claim this Profile
Click to upgrade to our gold package
for the full feature experience.
Topline Score
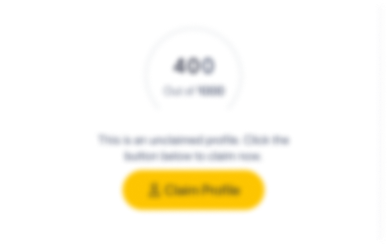
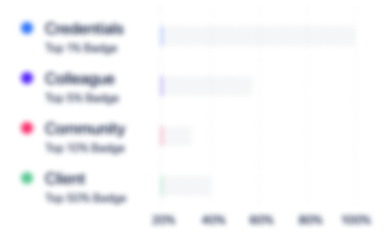
Bio

debaprosad sen
Mr. Prasad is an extra ordinary student,and good designer in cab design.I wish all the success in his life.I hope he will do better in future in the design field.God bless him.D.sen R.T.C INSTITUTE OF TECHNOLOGY RANCHI. EX BITMESRA RANCHI in the dept. of Mechanical engg.

Neelam Pandey Pathak
Prasad is a team player, and detail oriented person. Always on time for his work. Coming with solution and always flagged the critical issue as the team member. And a good friend .

debaprosad sen
Mr. Prasad is an extra ordinary student,and good designer in cab design.I wish all the success in his life.I hope he will do better in future in the design field.God bless him.D.sen R.T.C INSTITUTE OF TECHNOLOGY RANCHI. EX BITMESRA RANCHI in the dept. of Mechanical engg.

Neelam Pandey Pathak
Prasad is a team player, and detail oriented person. Always on time for his work. Coming with solution and always flagged the critical issue as the team member. And a good friend .

debaprosad sen
Mr. Prasad is an extra ordinary student,and good designer in cab design.I wish all the success in his life.I hope he will do better in future in the design field.God bless him.D.sen R.T.C INSTITUTE OF TECHNOLOGY RANCHI. EX BITMESRA RANCHI in the dept. of Mechanical engg.

Neelam Pandey Pathak
Prasad is a team player, and detail oriented person. Always on time for his work. Coming with solution and always flagged the critical issue as the team member. And a good friend .

debaprosad sen
Mr. Prasad is an extra ordinary student,and good designer in cab design.I wish all the success in his life.I hope he will do better in future in the design field.God bless him.D.sen R.T.C INSTITUTE OF TECHNOLOGY RANCHI. EX BITMESRA RANCHI in the dept. of Mechanical engg.

Neelam Pandey Pathak
Prasad is a team player, and detail oriented person. Always on time for his work. Coming with solution and always flagged the critical issue as the team member. And a good friend .

Experience
-
Mahindra Automotive North America
-
United States
-
Motor Vehicle Manufacturing
-
200 - 300 Employee
-
Senior Engineer - Body Structures
-
Dec 2021 - Present
Got the opportunity to rejoin Team Mahindra after a gap of almost one year. Working as Senior Engineer - Body Structures Design for a BEV (Born Electric Vehicle) : - • Designing a Top hat (Upper Body Structure) for an EV- SUV based on a Modular Under body Platform. • Designing Body side Outer Skin panel and its Structure including reinforcement ring and Inner Panel ring. • Material (thickness and grade) selection, optimization of sections, weight and performance of structure. • Contributing in manufacturing discussions and development of modular underbody platform as well. • Created and managing complete EBOM structure in CATIA and PLM (Team Center) right from scratch. Show less
-
-
-
Lordstown Motors
-
United States
-
Motor Vehicle Manufacturing
-
100 - 200 Employee
-
Design and Release Engineer - Body Structures
-
Jan 2021 - Dec 2021
Worked as Design and Release Engineer for Body Structures : - • Studied the overall packaging of EV platform to understand opportunities for improvement. Effectively resolved second row passenger Ingress-Egress issue with new Floor design and also optimized the waterfall feature taking into consideration Battery and its HV cable routing. This resulted in improved second row foot room and allowed us to have better stowage space under the second row seat. • Redesigned complete Floor panel to Side sill joinery for better side pole and side impact performance. This enabled us to improve manufacturing process, spot weld access and achieve dimensional stability. • Optimized front and second row seat mounting cross member and seat mounting bracket structures which resulted in ~ 8Kg of weight reduction and associated cost savings without degrading any safety performance of the vehicle. • Created complete new design for Rear wall panel of the pick-up Truck and its associated structure to enhance NVH performance, joinery with Body side LH/RH structures and simplify assembly sequence • Redesigned Child restraint ISO bracket on BIW Rear Wall with improved weld layout to meet regulatory requirement of safety criteria with overall system weight saving of ~0.5 kg • Worked extensively for finalizing Drain Plugs and NVH sticker strategy with appropriate and balanced focus on performance and cost of overall sealing system for the Body in White. • Actively supported Prototype (EP & VP) builds in the Plant at Lordstown, OH and participated in the physical parts buy off activities at supplier end to ensure the quality parameters of the BIW parts and subassemblies are met per design specifications to minimize build issues on assembly line in plant. • Created and managed complete EBOM structure in CATIA and PLM (Team Center) right from concept development to final production release Show less
-
-
-
Mahindra Automotive North America
-
United States
-
Motor Vehicle Manufacturing
-
200 - 300 Employee
-
Senior Design Engineer - BIW Structures
-
Apr 2017 - Dec 2020
Worked as Senior Design Engineer for underbody BIW structure of SUV : - • Extensive packaging study done for vehicle aggregate systems pertinent to cab underbody design viz Drive Shaft, Transmission, Frames, Fuel Tank, Body mounts, Brake and other routings, Park Brake, Suspension, Wheels etc. • Based on packaging feasibility assessment conceptualized, engineered and designed complete underbody structure. The Underbody architecture is defined keeping in mind the possible Load path and structural strength • Decided full material and thickness matrix along with manufacturing processes for all the parts in the structure • Worked extensively with manufacturing teams to optimize process sequence, spot weld feasibility and logistics • Got the Underbody structure validated in CAE for Safety, Durability and NVH performance including side impact • Actively supported Engineering and Validation Prototype (EP & VP) builds and testing activities in India • Got all the designed parts GD&T done along with relevant APQP activities including DFM, DFA, DVP & DFMEA • Created and managed complete EBOM structure in CATIA and PLM from first part to entire production release • Constant focus on part and assembly cost, weight, performance, optimization and process complexity throughout the project to make it more cost and investment effective without compromising vehicle performance • Modeling of entire structure done personally in Catia V5 for all the Floor parts including Floor panels, Center Tunnel, Long Members, Cross Members, Body mount parts, Side sill panels and Side pole crash box to name a few Show less
-
-
-
Detroit Engineered Products
-
United States
-
Motor Vehicle Manufacturing
-
300 - 400 Employee
-
Lead Product Engineer - EV Platform
-
Nov 2016 - Apr 2017
Worked as Lead Engineer for EV and PHEV BIW structures and Underbody Platform Design :- • Carried out Packaging and Sectional study of vehicle layouts provided by Karma Automotive Packaging Team for both EV and PHEV platforms including Battery, Motors, Suspension, Wheel Envelopes, Carpet, Pedal controls etc. • Created master sections and designed initial underbody structure for both the vehicle variants for given packaging • Devised mixed material strategy for maximum possible modularity, optimized weight, process feasibility and cost • Coordinated all the reviews, meetings, communications and data management with client Karma Automotive • Devised a unique cost-effective concept for modular Dash Panel to suit both the car and SUV platforms • Created EBOM structure in CATIA based on initial Manufacturing feedbacks and proposed assembly sequence • Hands-on designing of entire Rear Floor parts in Catia V5 including Floor panels, Long Members, Cross Members, Rear Bumper Beam, Dash Panels, Wheel house and Seat Mounting members to suit Aluminum extrusion process Show less
-
-
-
Honda R&D Americas, LLC
-
United States
-
Motor Vehicle Manufacturing
-
700 & Above Employee
-
Senior Project Engineer - BIW Structures
-
Jan 2016 - Nov 2016
Worked as Sr Project Engineer for weight reduction in Upper Body of Honda Pilot :- • Designed new side panels and joinery for Side Structure with Hot Formed Ultra High strength steel (UHSS) materials • Designed new panels like Aluminum Roof along with Front and rear Header structures for pasted roof concept • Study and implementation of structural adhesives and crash toughened adhesives in existing weld flanges • Designed Plastic side garnishes and their mounting scheme for light weighting to replace current steel panels • Implementation of DVD sheets for roof stiffness improvement to eliminate current steel roof arches • Designed “Roof testing Buck” to evaluate and validation of roof stiffness after roof structure optimization • Overall weight reduction of 45 Kg achieved in upper structure of Pilot BIW and proposal submitted to management Show less
-
-
-
Tata Motors
-
India
-
Motor Vehicle Manufacturing
-
700 & Above Employee
-
Senior Manager - Cabin Design - BIW & Trims
-
Apr 2012 - Jan 2016
• Was responsible and leading a team of 6 design engineers for design, engineering and development of BIW and Trims for Tata – Indigo Model Year’13 Refresh Programs from project kick-off to Start of Production (SOP) • Conducted Styling (Studio engineering) feasibility of new styling surface and feasibility of vehicular changes impact • Carried out Sectional study and finalized master sections for affected BIW structural parts like Panel Front Floor, Engine Mounts, Front Crash Members, Battery Tray and Trims Parts like Map pocket, Garnish, Bumpers, Roof Rack • Developed various design concepts and for all affected BIW panels and Trims parts • Discussed feasibilities of concepts with manufacturing teams and suppliers and implemented the suggestions • Got prototype and fitment trials done alongside CAE validation of the design. Implemented feedbacks received • Effective liaising with various departments like Product Planning, Homologation, Metallurgy, Vendor development • Participated in Design Reviews, CFT meetings as a Project lead and released the designs for final mass production • Got two cash rewards for cost reduction and VAVE proposals submitted in company’s reduction drive Show less
-
-
-
Eicher Trucks and Buses
-
India
-
Motor Vehicle Manufacturing
-
700 & Above Employee
-
Manager - Cabin Design
-
Dec 2010 - Mar 2012
• Was responsible and leading a team of 5 design engineers for complete design, engineering and development of BIW structure for a new Cabin of Heavy Commercial Truck • Performed Styling, Ergonomic and Regulatory feasibilities for the new Class-A surfaces received from Styling Team • Did Packaging Feasibility with Engine and Transmission for determining Floor Height and underbody tunnel shape • Spearheaded Simultaneous Engineering activity involving Korean manufacturing experts and weld line suppliers for Cabin Assembly sequence finalization, Checking Fixture design, weld and sealer application and line buy-off • Released designs for Proto Builds and CAE. Got the four poster Shaker test conducted in regulated Test facility • Jotted six design guideline documents as company knowledge base creation and future reference for designers • Received cash prize for intra company suggestion drive for my Business Practice Improvement Suggestions Show less
-
-
-
Mahindra Navistar Automotives Ltd.
-
Motor Vehicle Manufacturing
-
100 - 200 Employee
-
Manager - Cabin Design
-
Jul 2006 - Dec 2010
• Completed manufacturing feasibility of cabin panels including Floor, Roof, Firewall and Doors using Auto-Form • Prepared extensive DVP document for Commercial Truck cabin including all the aggregates like Trims, Seals, Mechanisms, Carpets, Closures and BIW structure by studying various Design Documents, Benchmarks, Supplier DVPs and Regulatory (ECE, AIS, FMVSS) standards pertaining to Truck Cabin and its performance requirements • Was responsible for leading a team of 4 designers to develop a Drive away chassis (Cowl) variant of Truck • Extensive benchmarking and customer interaction done on actual field to capture their needs before design start • Was pivotal in Conceptualizing, designing and developing complete Cowl structure from inception to production • Designed and developed majority floor structure CAD model personally in Catia V5 for all the Floor parts including Floor panels, Structural Members, Body mount and Trim parts like Engine Hood, Canopy and ECU covers • Participated and led the simultaneous engineering activity with Korean consultant and BIW line supplier for entire DFM, DFA, GD&T and Stack up analysis activity for the production release design. • Always focused on cost optimization right from the beginning. Applied many frugal design techniques, efficient part design strategies, tool commonalities and saved an estimated sum of Rs.30 Million in tooling and material cost Show less
-
-
-
Tata Technologies
-
India
-
IT Services and IT Consulting
-
700 & Above Employee
-
Senior Design Engineer - Formability Analysis
-
Jan 2000 - Jun 2006
• Carried out One Step and Incremental formability simulations of around 200 BIW Panels of Cars, Trucks, SUVs • Created die surfaces for the BIW panels with best possible tipping direction and die depth for blank cost saving • Worked on High strength steels, Aluminum and tailor welded blank technologies for BIW parts and simulation • Devised a new systematic procedure to find out trim-line development of parts for die cutting • Carried out a unique of its kind study with crash safety team to assess the effect of using stamped component from FEA software in CAE crash test instead of using CAD models with constant thickness. This study was well appreciated and later a paper presented in Altair Seminar in Bangalore in 2006 Show less
-
-
Education
-
Birla Institute of Technology, Mesra
M.E. - Design, Mechanical Engineering -
Yashwantrao Chavan Maharashtra Open University
MBA, Finance -
Shivaji University
B.E., Mechanical Engineering -
Awards and Other Achievements
Community
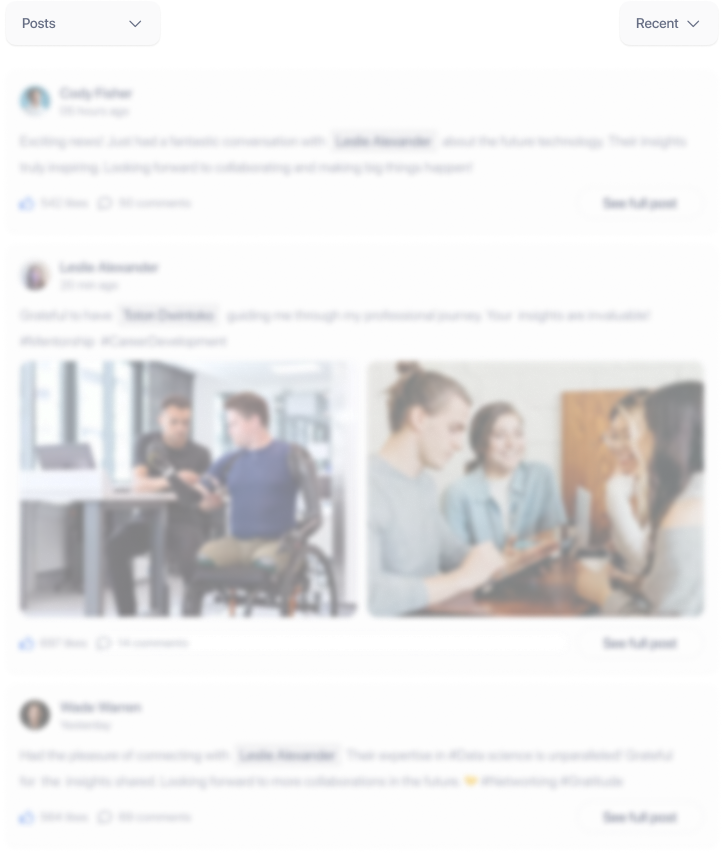