Pramod Vittal Rao
Engineering Manager - Quality Assurance at Nexteer Automotive - India Software Center- Claim this Profile
Click to upgrade to our gold package
for the full feature experience.
-
English -
-
Kannada -
-
Hindi -
Topline Score
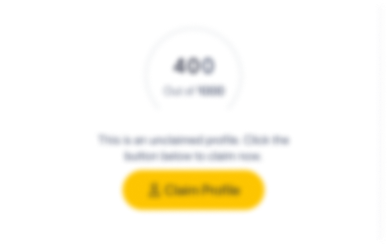
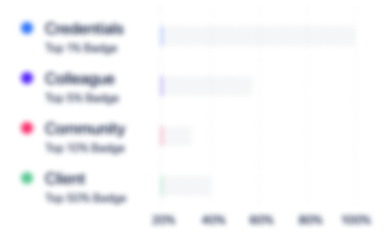
Bio

Keshava P Chandraiah, PMP®CSM®SAFe 6®Agilist
We both worked together at ACS, a Xerox company. Pramod was go getter, used to accomplish the task in a right way with perfect quality. He had always had a excellent strategy to complete any complex task and very reliable worker!! I would recommend he will be an awesome asset for any employer.

Abnish Pradhan
Pramod is a quality passionate person to every extent we discussed. Very focused and detail oriented person. Quite clear to connect and communicate.

Keshava P Chandraiah, PMP®CSM®SAFe 6®Agilist
We both worked together at ACS, a Xerox company. Pramod was go getter, used to accomplish the task in a right way with perfect quality. He had always had a excellent strategy to complete any complex task and very reliable worker!! I would recommend he will be an awesome asset for any employer.

Abnish Pradhan
Pramod is a quality passionate person to every extent we discussed. Very focused and detail oriented person. Quite clear to connect and communicate.

Keshava P Chandraiah, PMP®CSM®SAFe 6®Agilist
We both worked together at ACS, a Xerox company. Pramod was go getter, used to accomplish the task in a right way with perfect quality. He had always had a excellent strategy to complete any complex task and very reliable worker!! I would recommend he will be an awesome asset for any employer.

Abnish Pradhan
Pramod is a quality passionate person to every extent we discussed. Very focused and detail oriented person. Quite clear to connect and communicate.

Keshava P Chandraiah, PMP®CSM®SAFe 6®Agilist
We both worked together at ACS, a Xerox company. Pramod was go getter, used to accomplish the task in a right way with perfect quality. He had always had a excellent strategy to complete any complex task and very reliable worker!! I would recommend he will be an awesome asset for any employer.

Abnish Pradhan
Pramod is a quality passionate person to every extent we discussed. Very focused and detail oriented person. Quite clear to connect and communicate.

Credentials
-
IATF certified internal auditor
Omnex IncJun, 2019- Nov, 2024 -
Intacs certified ASPICE provisional assessor
Intacs VDA - Intacs-IN21-1919-24054-01Sep, 2019- Nov, 2024
Experience
-
Nexteer Automotive - India Software Center
-
India
-
Software Development
-
100 - 200 Employee
-
Engineering Manager - Quality Assurance
-
Aug 2023 - Present
Process excellence group - Quality assurance engineering manager, Bangalore.
-
-
Team Supervisor - Quality Assurance
-
Aug 2022 - Jul 2023
-
-
-
Continental
-
Germany
-
Motor Vehicle Manufacturing
-
700 & Above Employee
-
Senior Technical Lead
-
Jan 2022 - Aug 2022
-
-
Software Quality Assurance Manager
-
Aug 2018 - Dec 2021
• Managing a team of Quality engineers who are associated with User Experience Business Area (UX BA). • Mentor and coach project development team, quality team members on ASPICE according to VDA gold blue book guidelines. • Perform ASPICE assessments as Lead-assessor/co-assessor according to ASPICE steering committee schedule which is managed globally. • Core team member for ASPICE Center-of-Excellence team UX BA globally and Technical center India, Bangalore.• Drive and support engineering activities according to ASPICE standards during all project phases (concept, product development, product design, validation, and support to production).• Manage and participate customer specific product/ process assessment from R&D environment. • Supports SW and SYS quality/development engineers in reviews of all work products of the project and verifies that the review execution is compliant to valid specifications and authorizes for release of work products according to schedule• Supports the definition of quality criteria, metrics and determines them as far as project manager has the project measurement matrix in place during initial phase of the project and evaluates quality related data of the project with periodical management reviews. • Responsible for carrying out root cause analysis for project internal quality issues and customer reported defects using 8D, A3 analysis and other quality tools and taking necessary corrective and preventive action for the same. • Participate and Manage RFQ/RFP for new projects from Quality area as key member during new project proposal stage. Show less
-
-
-
Infosys
-
India
-
IT Services and IT Consulting
-
700 & Above Employee
-
Quality Assurance Manager
-
Jan 2018 - Jul 2018
• Experience in implementation of ISO9001:2015 and CMMI Ver 1.3 at an organizational level from end to end including support functions.• Experience in working as Quality manager on ASPICE (PAM 2.5) for automotive software development projects.• Coach and mentor delivery execution teams in ensuring the implementation of organization wide best practices within the different engagements. Official trainer for CMMI dev ver1.3 within Mysore Development Center.• Assisting project team in tailoring the process w.r.t std. QMS and CMMI process development followed within organization as per scope of the projects.• Create quality plan for project and performs project maturity assessments. Reports noncompliance to relevant stakeholders. Review project closure & milestones artifacts and ensure submission.• Analyze the metrics based on Organization benchmarks, perform statistical analysis, conduct correlations among performance metrics to draw specific interferences about project performance and ensure client delivery is met as per schedule.• Develop training content and conduct training/workshops for improvements in projects/process. Lead improvement programs using structured improvement methods such as Six Sigma, Lean, Margin Improvement initiatives. • Develop Process capability baselines (PCB) by analyzing previous closure reports for respective process type projects with help of statistical tools & techniques and ensure high degree of capability within process. Show less
-
-
Sr. Lead - Quality assurance
-
Apr 2014 - Dec 2017
Project management, Process improvement, AS 9100, CMMI
-
-
Lead - Quality assurance
-
Jan 2013 - Mar 2014
Project Management, Process mangement, Process Improvement, Six sigma, ISO.............
-
-
-
KPIT
-
India
-
Software Development
-
700 & Above Employee
-
Process Consultant
-
Sep 2012 - Jan 2013
• Worked as Process consultant for Automotive software development division. • Provided process consultancy for automotive development projects and few mechanical development projects within Automotive SBU. • Ensuring process compliance during execution of the projects in various SDLC stages of project. • Worked with project team in preparation of estimations, metric analysis, project planning, monitoring and control, review of configuration management, defect prevention. • Worked with Program lead to review, analyze, interpret all the metrics at projects and account level. • Conduct internal audits and ensure closure of nonconformance. • Review and provide approval for release of project artifacts during release phase of the project to customer as per plan. • Part of team during external ASPICE assessment. Show less
-
-
-
Tata Elxsi
-
India
-
IT Services and IT Consulting
-
700 & Above Employee
-
Senior Quality Engineer
-
Mar 2011 - Aug 2012
• As Senior Engineer - Quality for Industrial Design Group, Transportation design division. • Worked for the automotive client Jaguar Land Rover (JLR) and Tata Motors limited (TML). • Worked in close interaction with Project team, Sales team, Operations team for project planning and monitoring at various SDLC stage of the project. • Responsible for developing new process based on discussion with client/delivery team and monitoring of the same for continuous improvement. • Responsible to Metrics preparation and analyzing the same for decision making. • Responsible for conducting technical review with customer & project team for any technical issues in the project. • Responsible for Conducting Training on ISO 9001:2008, FMEA, 7QC tools, MSA. • Responsible for mentoring projects executed for productivity improvement purpose as per Six Sigma methodology. • Evaluation and approval of monthly quality report (Project wise) and Reporting the same to senior management for further approvals. Show less
-
-
-
-
Senior Supplier Quality Engineer
-
Nov 2008 - Mar 2011
• Worked for client General Motors as Senior Associate - SQA. • Responsible for training suppliers about GM quality requirements, PPAP, APQP, FMEA, SPC and MSA. • Responsible for the review and approval of the PPAP submission from the suppliers. • Responsible for carrying out Internal Quality Audits. • Worked on various supplier quality projects using all above mentioned tools and techniques. • Review all relevant Design Records/ PPAP documentation submitted by Suppliers before approving the Quality of parts shipped and update the same in GM supply power web base. • Responsible for continuous improvements at supplier end and in-house by conducting training and awareness programmes. • Conduct the Technical Review with Customer & Supplier and resolve the Production Related & Measurement related issues raised by the Supplier. Show less
-
-
-
-
Supplier quality engineer
-
Sep 2007 - Nov 2008
• Responsible for the overall quality of supplier-provided components, raw material and sub-assemblies. • Conducting periodic visits at suppliers and sub-contractors place to audit quality systems and review PPAP documents. • Responsible for new part approvals. • Support quarterly business reviews for quality metrics and measurements. • Monitoring Inward inspection, Supplier Quality record maintenance. • Plan and participate in supplier pilot production runs. • Member in PFMEA, Control Plan, MSA, Process Capability Studies and other PPAP activity Team. Show less
-
-
Education
-
PES College of Engg.
BE, Automobile engg -
Maharaja's govt PU college, mysore
PUC, PCME -
Sadvidya high school , mysore
SSLC, English
Community
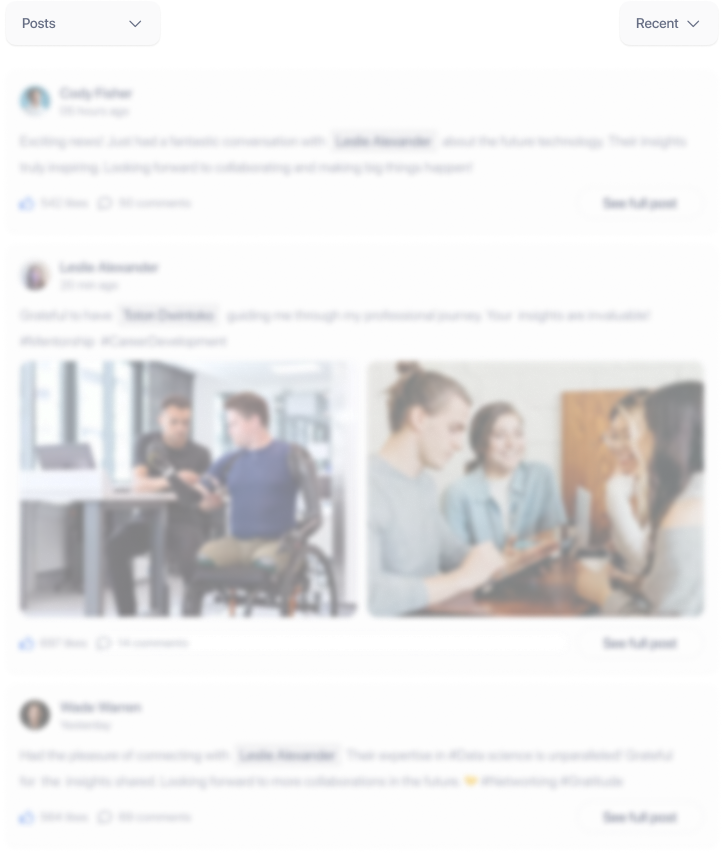