Poochandiran S
Sr.Engineer (Supplier Quality Assurance) at LS Automotive- Claim this Profile
Click to upgrade to our gold package
for the full feature experience.
Topline Score
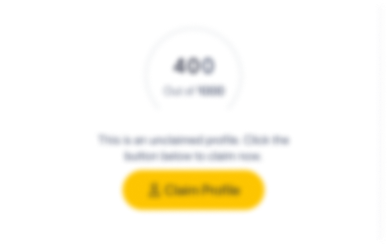
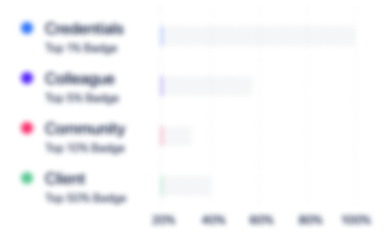
Bio


Experience
-
LS Automotive
-
South Korea
-
Motor Vehicle Manufacturing
-
300 - 400 Employee
-
Sr.Engineer (Supplier Quality Assurance)
-
Apr 2023 - Present
Process Handling: - Injection Molding(Plastic & Insert molding) - Press shop - SMT - Spray Painting Roles and Responsibilities: -Conducting supplier evaluation assessment audit and reporting the results to top management. - Conducting Supplier Audit and closing the observations by close follow-up of supplier as per the plan. -Ensuring the supplier quality level by conducting frequent system audit. -Reviewing the worst supplier quality status with top management and preparing action plan. -Supporting to the internal teams to close the customer complaints related to supplier. -Presenting QRQC meeting report to top management regarding supplier critical quality issue. -Conducting countermeasure verification audit at supplier site. -Analysing the chronic issues of suppliers and guiding them to improve. - Conducting ISIR and 4M approval audit at supplier sites. -Conducting Process study and tool trials and rectification for new projects at supplier sites. Show less
-
-
-
Jinyoung Sandhar Mechatronics Pvt Ltd
-
Chennai, Tamil Nadu, India
-
Quality Assurance Sr.Engineer
-
Aug 2020 - Apr 2023
Responsible for preparing Control Plan, FMEA, Process Flow,SOPs. • Responsible for coordinating and Conducting QMS internal audits, Process audits and Product audits in the manufacturing & assembly processes. • Preparing 8D reports for customer complaints & achieving customer targeted PPM by taking preventive actions. • Analyzing line concerns and taking corrective and preventive action. • Responsible to coordinate with Customers during the audit and implement the Customer requirements within the department. • Responsible for preparing weekly/monthly quality status presentation and review with top management. • Responsible to monitor the Customer Performance Rating & gap analysis • Responsible to prepare and update the all necessary quality reports as required by Customer • PPAP preparation for new part development. • Responsible to Monitor the Cost of Poor quality for Customer returns • Preparing and analyzing Supplier Audit and Assessment reports. • Responsible to organize and conduct the Supplier Meeting at every quarterly • Reviewing of Inspection Standard & PDI reports at Supplier end for accuracy. • Responsible to conduct the Countermeasure verification audit at supplier end to avoid the recurrence of quality issues. • Continual improvements along with team members to reduce the conventional cost of the part (KAIZEN, Quality circle...etc) • Coordinating overall departments to implementation of IATF 16949:2016 standards. • Rising QPCR to production team/supplier & getting effective implementation of action & monitoring. Show less
-
-
-
Arun Engineering
-
Chennai, Tamil Nadu, India
-
Graduate Engineering Trainee
-
May 2014 - Jul 2020
Monitoring the patrol inspection reports and verifying the First, Middle, Last off samples. Supporting to prepare the PPAP Document and G8D, Control plan, PFD, PFMEA. Highlighting the line concerns to the production team to ensuring defect free parts by making on time correction. Carried out Process and Product Audit as per the plan & Maintaining IATF 16949 documents and involved in Quality Management Systems. In depth understanding and perfection in shift handling, manpower planning, and resource allocation. Preparing WHY WHY Analysis to reduce line rejections and improve PPM level. Continual improvements along with team members to reduce the conventional cost of the wheel (KIZEN, Quality circle...etc) Rising QPCR to production team for eliminate the defects by making permanent corrective action. Analysing Line/Customer concerns and finding root causes using Statistical analysis tools. Assist to Manager for closing customer concerns by preparing Corrective actions and preventive actions. Formulation of Q alerts and Quality standards and visual dimensional. Preparing and maintaining the daily and monthly quality status presentation. Coordinate to monthly review meeting for top five rejections along with production team. Supporting to PDI for on time part dispatch. Show less
-
-
Education
-
Anna University
Bachelor of Engineering - BE, Mechanical Engineering -
Govt Boys Higher Secondary School
Community
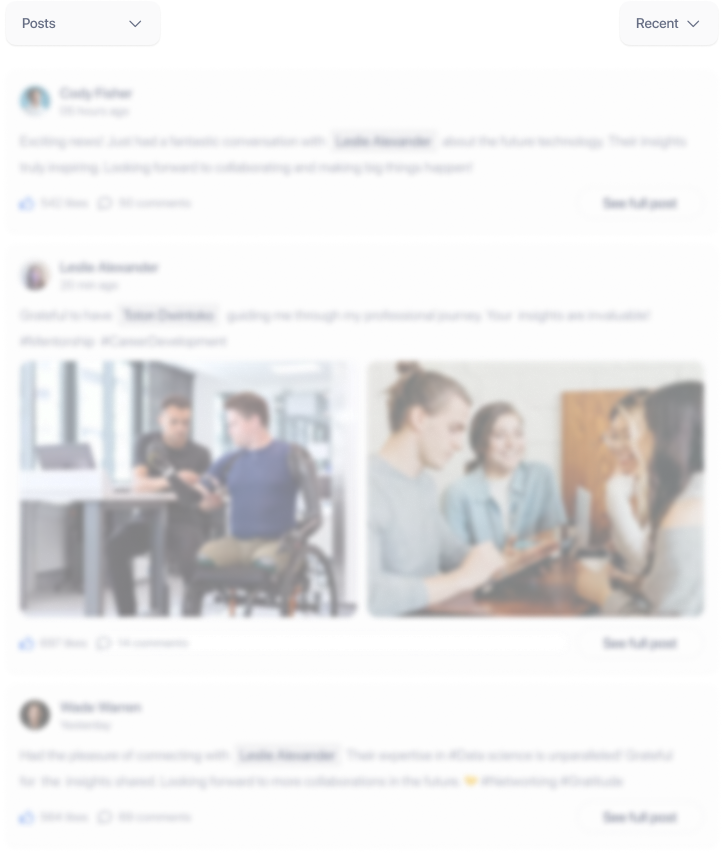