Peter Madsen - BSEE, MBA, PMP, VBSS Black Belt
Quality Assurance Manager at Tell Tool INC- Claim this Profile
Click to upgrade to our gold package
for the full feature experience.
Topline Score
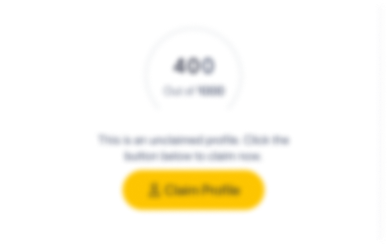
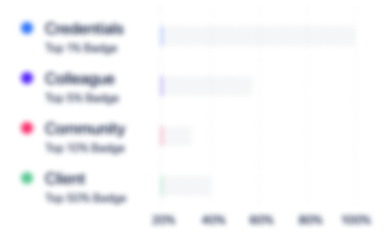
Bio

Curt Brey
I have had the opportunity to work with Peter for ~ 2 years. Peter directs our company’s largest and most complicated projects and all of the associated supporting functions. Peter is easily the best project director I have worked in almost 20 years of high tech new product development. Peter excels in cross-functional leadership, managing large, diverse technical projects with extraordinary detail and complexity. Furthermore, he is one of the most well composed people I know, maintaining consistency in situations of conflict and debate.

John Henderson
Peter has a rare blend of engineering design expertise, coupled with a pragmatic and comprehensive business savvy that provides a powerful foundation for project and team leadership. He is a people-oriented leader that has a reputation for showing his team the path, and driving the results through alignment on roles and responsibilities and conceptual understanding. Peter has a proven track record of handilng the toughest assignments, and delivering on the commitments.

Curt Brey
I have had the opportunity to work with Peter for ~ 2 years. Peter directs our company’s largest and most complicated projects and all of the associated supporting functions. Peter is easily the best project director I have worked in almost 20 years of high tech new product development. Peter excels in cross-functional leadership, managing large, diverse technical projects with extraordinary detail and complexity. Furthermore, he is one of the most well composed people I know, maintaining consistency in situations of conflict and debate.

John Henderson
Peter has a rare blend of engineering design expertise, coupled with a pragmatic and comprehensive business savvy that provides a powerful foundation for project and team leadership. He is a people-oriented leader that has a reputation for showing his team the path, and driving the results through alignment on roles and responsibilities and conceptual understanding. Peter has a proven track record of handilng the toughest assignments, and delivering on the commitments.

Curt Brey
I have had the opportunity to work with Peter for ~ 2 years. Peter directs our company’s largest and most complicated projects and all of the associated supporting functions. Peter is easily the best project director I have worked in almost 20 years of high tech new product development. Peter excels in cross-functional leadership, managing large, diverse technical projects with extraordinary detail and complexity. Furthermore, he is one of the most well composed people I know, maintaining consistency in situations of conflict and debate.

John Henderson
Peter has a rare blend of engineering design expertise, coupled with a pragmatic and comprehensive business savvy that provides a powerful foundation for project and team leadership. He is a people-oriented leader that has a reputation for showing his team the path, and driving the results through alignment on roles and responsibilities and conceptual understanding. Peter has a proven track record of handilng the toughest assignments, and delivering on the commitments.

Curt Brey
I have had the opportunity to work with Peter for ~ 2 years. Peter directs our company’s largest and most complicated projects and all of the associated supporting functions. Peter is easily the best project director I have worked in almost 20 years of high tech new product development. Peter excels in cross-functional leadership, managing large, diverse technical projects with extraordinary detail and complexity. Furthermore, he is one of the most well composed people I know, maintaining consistency in situations of conflict and debate.

John Henderson
Peter has a rare blend of engineering design expertise, coupled with a pragmatic and comprehensive business savvy that provides a powerful foundation for project and team leadership. He is a people-oriented leader that has a reputation for showing his team the path, and driving the results through alignment on roles and responsibilities and conceptual understanding. Peter has a proven track record of handilng the toughest assignments, and delivering on the commitments.

Credentials
-
Project Management Professional (2015)
Project Management InstituteDec, 2015- Oct, 2024 -
VBSS Black Belt (2005)
ITT Inc.Aug, 2005- Oct, 2024
Experience
-
Tell Tool INC
-
United States
-
Aviation and Aerospace Component Manufacturing
-
1 - 100 Employee
-
Quality Assurance Manager
-
Jan 2023 - Present
Management of Quality Organization at Tell Tool. Management of Quality Organization at Tell Tool.
-
-
-
KX Technologies
-
United States
-
Food and Beverage Services
-
1 - 100 Employee
-
Director Of Quality Assurance
-
Jul 2021 - Apr 2022
Director, Quality; Reporting to the President, Residential Filtration products, responsible for the management of the Quality Organization at KX Technologies (including their Singapore location).• Manage the Quality department at all KX Technologies sites. Which includes Quality Assurance, Quality Control, Supplier Quality, and Internal Audit functions. • Responsible for Receiving Inspection (RI), In Process Inspection, and Final Inspection at all facilities. Inspect all parts at RI utilizing Acceptable Quality Limits [ANSI/ASQC Z1.4]. Revamped the entire RI process (and physical inspection location / area) into a professional looking and performing RI function, including the establishment of a Material Review Board (MRB) function.• Responsible for the management and determination of Root Cause and Corrective Action (RCCA) for all Internal Non-Conformances (NC), Supplier Corrective Action Requests (SCAR), and Return Material Authorizations (RMA).• Conducted routine in-house quality audits to ensure that KX Technologies was in conformance with ISO9001:2015. Document all findings and make sure all corrective / preventative actions are accomplished.• Maintain ISO9001:2015 Quality Management Systems certifications at all sites. Including the training of personnel, preparation for on-site audits, and supporting the auditors when on site for certification audits.
-
-
-
IMI Adaptas
-
United States
-
Machinery Manufacturing
-
1 - 100 Employee
-
Director Of Quality Assurance
-
Oct 2019 - Jan 2021
Director, Quality; Reporting to the Chief Operating Officer (COO), responsible for the management of the Quality Organization at Adaptas Solutions.• Manage the Quality department at all Adaptas sites (including their machine shop). Which includes Quality Assurance, Quality Control, Supplier Quality, and Internal Audit functions. • Conducted routine in-house quality audits to ensure that Adaptas was in conformance with ISO9001:2015. Documented all findings and made sure all corrective / preventative actions were accomplished.• Responsible for Receiving Inspection (RI), In Process Inspection, and Final Inspection at all facilities. Inspected all parts at RI utilizing Acceptable Quality Limits [ANSI/ASQC Z1.4 (AQL=1 / Inspection Level=1)]. • Responsible for the management and determination of Root Cause and Corrective Action (RCCA) for all Internal Non-Conformances (NC), Supplier Corrective Action Requests (SCAR), and Return Material Authorizations (RMA).• Identified and became proficient in the utilization of Minitab Statistical Software for process and product verification / validation purposes. Critical when performing Installation Qualification (IQ), Operational Qualification (OQ) and Performance Qualification (PQ) activities for new products being released into production. • Maintain ISO9001:2015 Quality Management Systems certifications at all sites. Including the training of personnel, preparation for on-site audits, and supporting the auditors when on site for certification audits.• Lead effort to transition Adaptas Solution’s Quality Management System (QMS) to ISO13485. Effort involved performing a gap analysis from current ISO9001 certification to ISO13485 certification and leading efforts to eliminate gaps.
-
-
-
Philips
-
Netherlands
-
Hospitals and Health Care
-
700 & Above Employee
-
Senior Consultant - Program Management
-
Aug 2019 - Oct 2019
Design, development, manufacture, and distribution of oxygen generators and analyzers; monitors for cardiac output, respiratory mechanics, CO2, and pulse oximetry; including the associated sensors, masks, nasal cannulas, airway adapters and CPAP valves used with these medical devices. Design, development, manufacture, and distribution of oxygen generators and analyzers; monitors for cardiac output, respiratory mechanics, CO2, and pulse oximetry; including the associated sensors, masks, nasal cannulas, airway adapters and CPAP valves used with these medical devices.
-
-
-
Kaman Aerospace Corporation
-
United States
-
Aviation and Aerospace Component Manufacturing
-
400 - 500 Employee
-
Vice President, Quality (KPP)
-
Sep 2017 - Jan 2019
Vice President, Quality; Reported to the division President, was responsible for the management of the Quality Organization at KPP.• Managed the Quality department (approximately 70 personnel) at multiple KPP locations. Which included Quality Assurance, Quality Control, and Supplier Quality functions.• Maintained AS9100D Quality Management Systems certifications at all sites. Including the training of personnel, preparation for on-site audits, and supporting the auditors when on site for certification audits.• Internal Non-Conformances – reduced internally generated production non-conformances by 80% utilizing solid Root Cause and Corrective Action (RCCA) following the DMAIC (Define, Measure, Analyze, Improve, and Control) process.• Supplier Non-Conformances – reduced supplier related non-conformances by 50% utilizing solid Root Cause and Corrective Action (RCCA), Supplier Quality Engineer (SQE) visits/audits of suppliers, and training. In addition, conducted First Article Inspection (FAI) weekly training enforcing AS9102 compliance.• All Non-Conformances (internal/supplier) presented at weekly Sr. CAB (Corrective Action Board) to executive management demonstrating solid RCCA. Sr. CAB was owned, coordinated, and run thru the Quality organization.• Reduced “dock-to-stock” Receiving Inspection (RI) times from months to less than 5 days. This involved hiring and training adequate resources and the proper prioritization of parts being received into RI.• New Product Development (NPD) – allocated / trained Quality personnel to participate on NPD IPDTs (Integrated Product Development Team) to develop new products utilizing Kaman’s Stage Gate Process. This involved not only representing Quality on the IPDTs, but Reliability Engineering (which reported into the Quality Organization).
-
-
Director, Program Management (KPP)
-
Jun 2015 - Sep 2017
Employed as the Director, Program Management reporting to the President of Kaman Precision Products (KPP). Responsible for the management of the Program Management Office (PMO), it's personnel, and all programs (New Product Development (NPD) / legacy programs) at KPP.• Established the Program Management function at KPP. Hired, trained, mentored, and managed all Program Managers.• Implemented multiple Policies & Procedures (P&Ps) for the proper incorporation of Program Management and its disciplines into company culture.• Assigned to represent my division on the corporate PMO council at Kaman Aerospace. This council establishes policies and procedures for the implementation of program management disciplines across all of Kaman Aerospace.
-
-
Director of Product Development, R&D (KPP)
-
May 2012 - Jun 2015
Employed as Director, New Product Development / IR&D reporting to the Vice President of Engineering. Responsible for managing all personnel and related programs / projects in the design engineering and IR&D groups.• Responsible for the management and execution of multiple NPD programs and a multimillion-dollar IR&D budget along with all capital equipment and personnel. Presented the results of multiple IR&D efforts to senior management for further development efforts/budget. • Instrumental in the creation and establishment of KPP's Product and Technology road maps.• Created / established the NPD Stage Gate Process at KPP. This involved creation of the stage gate process map, stage gate activities/deliverables, and pass-fail criteria for moving on to the next gate. In addition, I defined the core team members (and supporting members) on the NPD Integrated Product Development Teams (IPDT), and their respective “Roles/Responsibilities”.• Travel to Aerospace and Defense primes as the technical expert in support new business development.
-
-
-
Gerber Technology, a Lectra Company
-
United States
-
Information Technology & Services
-
300 - 400 Employee
-
Executive Director, Global Programs
-
Sep 2011 - May 2012
Assigned leader of the Global Programs group responsible for managing key programs (New Product Development / Transformation / Business Optimization) for Gerber Technology. These programs spanned multiple facilities and required offshore coordination / management. Assigned leader of the Global Programs group responsible for managing key programs (New Product Development / Transformation / Business Optimization) for Gerber Technology. These programs spanned multiple facilities and required offshore coordination / management.
-
-
-
Gerber Scientific Inc.
-
United States
-
Industrial Automation
-
1 - 100 Employee
-
Executive Director, Project Management
-
Dec 2005 - Sep 2011
Employed as the Executive Director of Project Management (New Product Development) responsible for managing “key strategic” New Product Development (NPD) projects from inception to production release utilizing Gerber Scientifics “stage gate process” for NPD. Employed as the Executive Director of Project Management (New Product Development) responsible for managing “key strategic” New Product Development (NPD) projects from inception to production release utilizing Gerber Scientifics “stage gate process” for NPD.
-
-
-
ITT Inc.
-
United States
-
Industrial Machinery Manufacturing
-
700 & Above Employee
-
New Product Development Manager
-
2000 - 2005
Employed as the Product Development Manager responsible for managing all personnel within the New Product Development Group which included Design Engineering (Electrical/Mechanical), Manufacturing Engineering, Electronic Laboratory (incl. all Technicians), and the Program Management Office (PMO). Responsible for the management of all New Product Development / R&D initiatives, from initial customer contact thru the end of the products life cycle. Employed as the Product Development Manager responsible for managing all personnel within the New Product Development Group which included Design Engineering (Electrical/Mechanical), Manufacturing Engineering, Electronic Laboratory (incl. all Technicians), and the Program Management Office (PMO). Responsible for the management of all New Product Development / R&D initiatives, from initial customer contact thru the end of the products life cycle.
-
-
-
Accu-Time Systems
-
Appliances, Electrical, and Electronics Manufacturing
-
1 - 100 Employee
-
Design Engineering Manager
-
1996 - 2000
Employed as the Manager of Hardware Design / Electrical Designer responsible for hardware / software design. Responsibilities included the design of products from conception to production. Awarded a patent for an "Innovative New Product" Employed as the Manager of Hardware Design / Electrical Designer responsible for hardware / software design. Responsibilities included the design of products from conception to production. Awarded a patent for an "Innovative New Product"
-
-
-
Hamilton Sundstrand
-
United States
-
Aviation and Aerospace Component Manufacturing
-
700 & Above Employee
-
Project Engineer
-
1986 - 1996
Worked as a Project Engineer in the Engine Controls and Accessories division, which produced digital electronic engine controls for military and commercial applications. Worked as a Project Engineer in the Engine Controls and Accessories division, which produced digital electronic engine controls for military and commercial applications.
-
-
Education
-
Western New England University
Master of Business Administration - MBA -
University of Hartford
BSEE, Electrical Engineering
Community
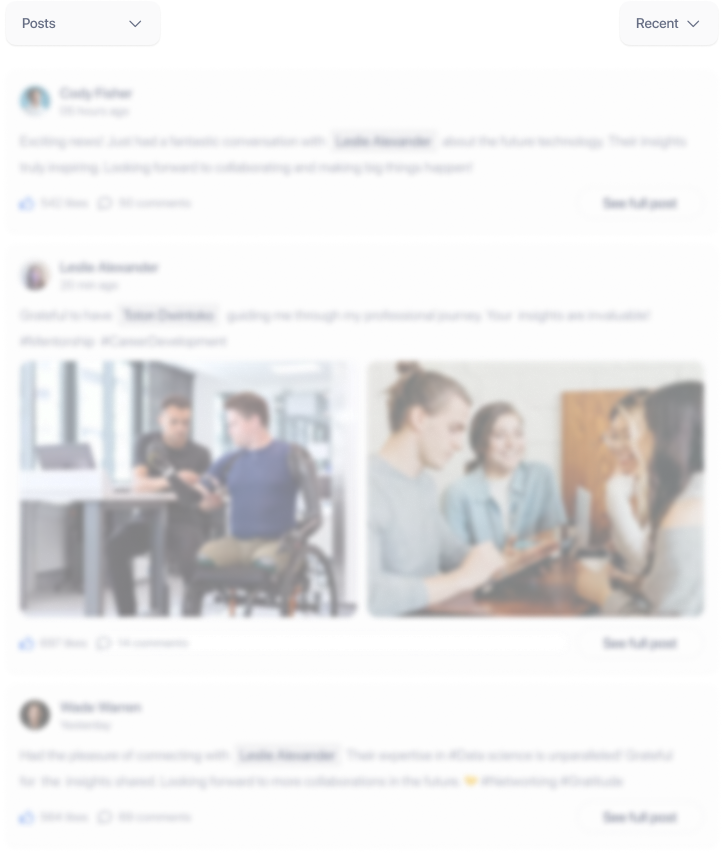