Pieter Nel
Delivery Driver at Canterbury Linen Services- Claim this Profile
Click to upgrade to our gold package
for the full feature experience.
-
English -
-
Afrikaans -
Topline Score
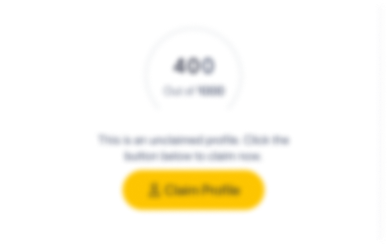
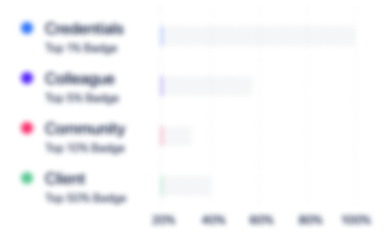
Bio


Credentials
-
Engineering in Aviation Sheet Metal
Denel DynamicsJan, 1982- Nov, 2024 -
South Africa Military Defense forces
South Africa Military Defense ForcesJan, 1979- Nov, 2024
Experience
-
Canterbury Linen Services
-
New Zealand
-
Textile Manufacturing
-
1 - 100 Employee
-
Delivery Driver
-
Feb 2019 - Present
• Responsible for ensuring timely delivery of clean line to Christchurch Hospital on specific routes, reviewing orders before delivery, loading and unloading trucks and providing exceptional customer service to our client base. • Delivering linen to CLS customers in a safe and timely manner. • Reviewing orders before and after delivery to ensure that orders are complete, and the customer is satisfied. • Providing excellent customer service, answering questions, and handling complaints from customers. • Maintaining consistent communication with distribution coordinator. • Cooperating with packing staff. • Performing other duties as assigned • Ownself and time management. Show less
-
-
-
Farrier International
-
650 Halswell Jct Rd, Hornby South, Christchurch 8042
-
Assembler & Stores /Inventory Coordinator
-
Oct 2018 - Nov 2018
• Monitoring and controlling inventory integrity. • Maintaining product identification and location program. • Researching inventory discrepancies and making necessary corrections. • Managing the inventory control function and ensure that all picklists are fulfilled and supplied to each work station on time. • Responsible for overseeing physical inventories/cycle counts/random or receipt audits/reconciliations • Resolving inventory problems in a timely manner. • Documenting and controlling aged & damaged product. • Ensuring that all parts and inventory are on time from suppliers for final installation. • Maintaining Inventory Accuracy Metrics and associated reports for management (and the client as appropriate). • Coordinate and Integrate efforts across operational departments to enhance inventory accuracy. • Liaise with suppliers and ensure that their pricing is as agree and quoted. • Place orders against suppliers and ensure all orders are on-time delivery. • Manufacturing and assembly quality parts to drawing using hand tools for the farrier sailboats. • Provide feedback on possible efficiency improvement in the factory systems and methods Show less
-
-
-
Falcon Manufacturing Group ltd
-
Christchurch NZ
-
Metal fabricator and installer
-
Aug 2018 - Sep 2018
• Fabricate metal parts, such as steel frames, columns, beams, or girders, according to blueprints or instructions from supervisors. • Cut, bend and using metal shears and using a variety of tools and machines to make metal parts or assemble components. • Bolt aligned structural steel members in position for permanent riveting, bolting, or welding into place. • Install metal structural components. • Prepare parts for coating to follow all principles and practices of painting and powder coating application • Construction installations of metal parts Show less
-
-
-
Paramount
-
South Africa
-
Aviation and Aerospace Component Manufacturing
-
100 - 200 Employee
-
Senior Production Planner & Customer Team leader
-
Nov 2014 - Apr 2017
Responsibilities as a Senior Production Planner. •Compile Bill of Material Requirement list on Excel and on ERP. •Liaise with Engineering + Configuration Departments •Compile Data Packs for manufacturing i.e. drawing as per SOPs. •Inventory planning to ensure that there is a sufficient supply of raw material and finished good to meet customer demands. •Create Purchase Orders and Liaise with Supply Chain Manager of delivery dates. •Demand Planning creates reliable forecasts and aligns inventory levels. •Replenishment Planning maintaining order check to ensure that the right product is at the right store in the right quantities •Release Data Packs for internal and subcontract manufacturing and monitor WIP. •Processing of materials by heat treatment and surface treatment as per spec requirements. •Plan and schedule workflow for each department and operation according to established manufacturing sequences-routing, lead times and capacity planning on ERP. •Support shop floor during critical manufacturing processes, updated data packs to improve processes •Support workshop and engineering with prototype development. •Liaise with: my Customers, Store and Dispatch to deliver parts on time to customers as per requirements. •Aircraft Maintenance Planning and flight test support. •Coordinate with Supervision, Quality department and Config department to ensure that all work is carried out to approved standards as per QMS per ISO standards •Support shop floor, final assembly line and all levels of the organization to achieving our goals •Quality inspections and first article inspections to drawings. •Liaise with shop floor and quality department to ensure that all mods, assemblies, and defects are carried out to approved standards •Ensure all documents are updated completed before final delivery. •Logistics control arranges for equipment and materials to be transported to or from offshore or overseas, or between onshore locations. Show less
-
-
-
Aerosud
-
South Africa
-
Airlines and Aviation
-
200 - 300 Employee
-
Senior Production Planner and Customer Service Team Leader Coordinate 3 crews of 40 people .
-
Jan 2005 - Nov 2014
Customer Service Team Leader's responsibility. •Supports crew leader in a final assembly line with servicing and modifications with day to day tasks to meet the project deadlines. •Responsible for managing the workflow through the workshop and liaising with production manufacturing to receive part on time for final assemblies. • Manages inventories, stock, and manufacturing including keeping detailed records of inventory use and sales, and advising management on orders where necessary. •Provides encouragement to team members, including communicating team goals and identifying areas for new training or skill checks. •Assists management with hiring processes and new team member training on the job. •Answers team member questions, helps with team member problems and oversees team member work for quality and guideline compliance. •Communicates deadlines and sales goals to team members •Develops strategies to promote team member adherence to company regulations and performance goals. •Conducts team meetings to update members on best practices and continuing expectations. •Generates and shares comprehensive and detailed reports about team performance, mission-related objectives, and deadlines. • Quality inspections of all work carried out as per drawings. •Ensures company brand materials and physical working spaces meet and exceed company presentation standards. •Provides quality customer service, including interacting with customers and suppliers answering customer inquiries, and effectively handling customer complaints. Roles at Paramount Group and Aerosud was the same-Senior Production Planner & Customer Team Leader, roles involved as production planner coordinating manufacturing demands to ensure smooth operations throughout the production and distribution life of a given product. Customer Team Leader coordinating final assembly line to deliver customer deadlines on time. Aerosud merging with Paramount in 2014 Show less
-
-
-
Denel Aviation
-
Aviation and Aerospace Component Manufacturing
-
200 - 300 Employee
-
Materials Requirement Planner
-
Apr 1998 - Dec 2004
. Maintain master data. Deliver customer orders in time. Give status reports of customer orders. Action all new requirements . Monitor movements of all WIP requirements. Liaise with MPS to re-schedule customer orders. Overseeing the production life cycle for purchase and manufacturing demands, to ensure customer forecast and supply plans are in place.. Analysis production processes and workflow to identify bottle necks to improved processes. . Production progress reports. Liaise with Production Control, Procurement, MPS and Project Management.. Planning and monitoring the materials and products used by your company. Ensure that the company doesn't run out of the materials needed to produce its products and also manage the flow of inventory support work shop and make sure products are properly shipped to customers. . Liaise with Supervisors that all modifications on aircraft is been carried out as per mod specifications before final delivery.. Ensured all work was carried out to approve standards and all paper work was in order before delivery . Support logistics and dispatched to arrange delivery on time. Show less
-
-
Engineering Sheet Metal Worker
-
Jan 1982 - Apr 1998
. Review documentation for maintenance of aircraft on appropriate forms.. Ensures compliance with Service Bulletins, Instructions and Airworthiness Directives.. Repair, rework, install and fabricate the complex aircraft structural assemblies, both internal and external.. Maintains aircraft maintenance technical directives, forms, records, and historical data as required.. Complies with safety and tool control program requirements.. Provides on-the-job training to new employees as required by Crew Chief.. Pre assembles major assemblies in jigs and on bench work as per requirements before final installation.. Manufacturing of sheet metal parts to drawings using hand tools and machines to the final product. . Supervision experience as crew chief. . Manufacturing of drill jigs and press tools to form sheet metal parts. Strip, replaced repair and assemble defect mechanical part as per aircraft manuals..Perform checks; carry out inspections and removal of components.. Prototyping development experience • Experience Crew leader coordinating final assembly line and Manufacturing Show less
-
-
Education
-
Denel Aviation Training School & National Training Council Department of Manpower
Engineering Trade, Aviation Sheet Metal Worker -
Erasmus High School
High School, Machine Shop Technology/Assistant
Community
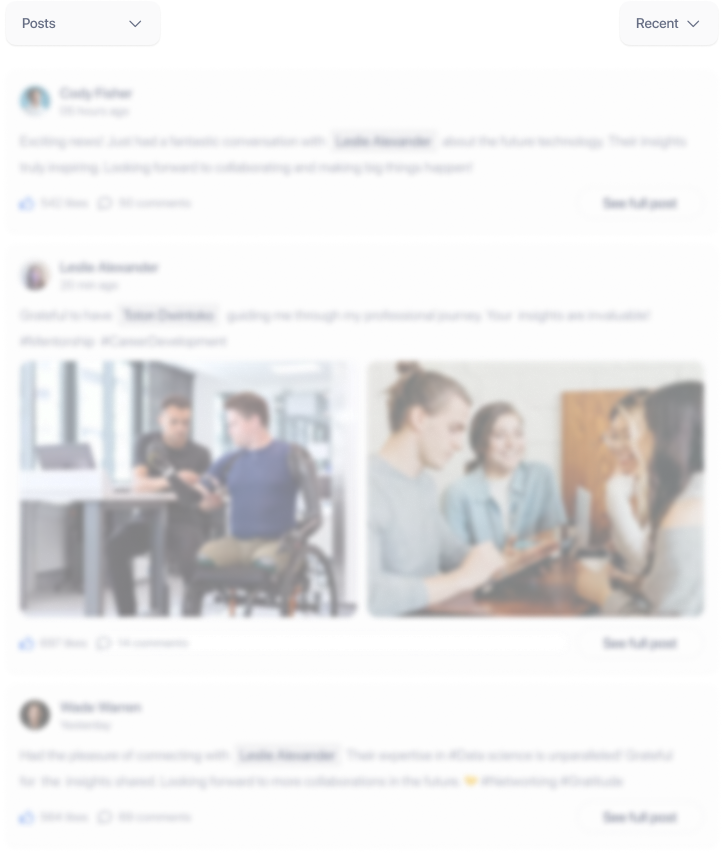