Phillip Lacroix, CQA, CQE
Director Quality, Regulatory & Compliance at WEINERT Fiber Optics Inc- Claim this Profile
Click to upgrade to our gold package
for the full feature experience.
Topline Score
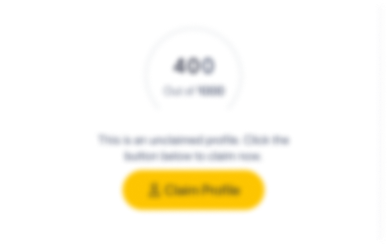
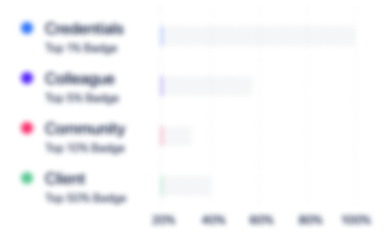
Bio

Ken Robertson
Had the pleasure of working with Phil daily as we shared management responsibilities in a highly challenging, fast paced, complicated environment. Phil impressed my with his impeccable integrity, honest work ethic and extensive experience and understanding of Quality systems. He is a "good guy" and would add value to any team.

Brian Grafe
Phillip brings his extensive Quality Assurance knowledge and experience to bear with professionalism in all circumstances. Dedicated to his craft, he applies his acumen to guide teams in identifying root causes and generating robust solutions. Rather than nurturing a 'gate keeper' mentality, Phil is a team player who strives for win-win solutions that ensure achievement of appropriate quality standards while meeting Operational metrics. Working with Phil has been a pleasure and has contributed to my own professional knowledge and growth.

Ken Robertson
Had the pleasure of working with Phil daily as we shared management responsibilities in a highly challenging, fast paced, complicated environment. Phil impressed my with his impeccable integrity, honest work ethic and extensive experience and understanding of Quality systems. He is a "good guy" and would add value to any team.

Brian Grafe
Phillip brings his extensive Quality Assurance knowledge and experience to bear with professionalism in all circumstances. Dedicated to his craft, he applies his acumen to guide teams in identifying root causes and generating robust solutions. Rather than nurturing a 'gate keeper' mentality, Phil is a team player who strives for win-win solutions that ensure achievement of appropriate quality standards while meeting Operational metrics. Working with Phil has been a pleasure and has contributed to my own professional knowledge and growth.

Ken Robertson
Had the pleasure of working with Phil daily as we shared management responsibilities in a highly challenging, fast paced, complicated environment. Phil impressed my with his impeccable integrity, honest work ethic and extensive experience and understanding of Quality systems. He is a "good guy" and would add value to any team.

Brian Grafe
Phillip brings his extensive Quality Assurance knowledge and experience to bear with professionalism in all circumstances. Dedicated to his craft, he applies his acumen to guide teams in identifying root causes and generating robust solutions. Rather than nurturing a 'gate keeper' mentality, Phil is a team player who strives for win-win solutions that ensure achievement of appropriate quality standards while meeting Operational metrics. Working with Phil has been a pleasure and has contributed to my own professional knowledge and growth.

Ken Robertson
Had the pleasure of working with Phil daily as we shared management responsibilities in a highly challenging, fast paced, complicated environment. Phil impressed my with his impeccable integrity, honest work ethic and extensive experience and understanding of Quality systems. He is a "good guy" and would add value to any team.

Brian Grafe
Phillip brings his extensive Quality Assurance knowledge and experience to bear with professionalism in all circumstances. Dedicated to his craft, he applies his acumen to guide teams in identifying root causes and generating robust solutions. Rather than nurturing a 'gate keeper' mentality, Phil is a team player who strives for win-win solutions that ensure achievement of appropriate quality standards while meeting Operational metrics. Working with Phil has been a pleasure and has contributed to my own professional knowledge and growth.
0
/5.0 / Based on 0 ratingsFilter reviews by:
Experience
-
WEINERT Fiber Optics Inc
-
United States
-
Manufacturing
-
1 - 100 Employee
-
Director Quality, Regulatory & Compliance
-
Feb 2023 - Present
-
-
-
Lima Corporate
-
Italy
-
Medical Equipment Manufacturing
-
700 & Above Employee
-
Principal Quality Engineer
-
Dec 2019 - Jan 2023
I am relied upon as a quality subject matter expert delivering quality engineering support and technical guidance to project teams across all phases of operations, while ensuring timely deliverables meet highest quality standards. As such, I… Work hand-in-hand to source/approve best suppliers and negotiate/establish quality agreements Regularly audit suppliers, as well as internal processes to maximize compliance and enact corrective actions whenever necessary. Identify cybersecurity risks across all software development phases. Assume full ownership of all Change Control requests, while maintaining a 95% completion rate for requests in under 30 days. Architected and continue to oversee the organization’s Supplier Management (SM) program and Risk Management (RM) system. The RM System is fully compliant with 14971:2020 standards. Oversaw risk documentation throughout the development and launch of two new FDA-approved medical devices. Show less
-
-
-
Altria
-
United States
-
Manufacturing
-
700 & Above Employee
-
Associate Manager, Regulatory Quality Compliance Audits
-
Feb 2019 - Nov 2019
I was promoted to lead all internal and supplier audits of facilities within the United States and Dominican Republic. As a key part of my role, I completely revamped incoming inspection requirements in accordance with data from a statistically valid program.
-
-
Manager Quality Compliance
-
Feb 2018 - Feb 2019
I joined the company initially ensuring e-vapor batteries and cigarettes complied with strict quality standards via careful audits of Contract Manufacturing Operations (CMO), Suppliers and Contract Design Labs across the globe. For key contributions, I…Was instrumental in substantially improving battery safety and performance.Crafted quality audit processes to align with FDA QSIT guidelines.
-
-
-
Vyaire Medical
-
United States
-
Medical Equipment Manufacturing
-
700 & Above Employee
-
Principal Engineer, Quality
-
Oct 2016 - Nov 2017
I traveled regularly to deliver key quality support over extended projects at IS and international, in addition to managing all supplier quality complaints. Over my time in the role, I… Succeeded in resolving a backlog of 200+ complaints within two months after the transfer of production from NJ to Mexico Directed preparations of the China and Mexicali, Mexico sites for comprehensive FDA audits. China had only one observation noted and Mexico had zero. Project managed the transition of receiving inspections from the US distribution center to a Vyaire site near the supplier’s site in China. Show less
-
-
-
BD
-
United States
-
Architecture and Planning
-
Principal Engineer, Quality
-
Feb 2016 - Sep 2016
I traveled regularly to deliver key quality support over extended projects at IS and international, in addition to managing all supplier quality complaints. Over my time in the role, I…Succeeded in resolving a backlog of 200+ complaints within two months after the transfer of production from NJ to MexicoDirected preparations of the China and Mexicali, Mexico sites for comprehensive FDA audits. China had only one observation noted and Mexico had zero.Project managed the transition of receiving inspections from the US distribution center to a Vyaire site near the supplier’s site in China. Show less
-
-
Principal Engineer, Quality
-
Jan 2015 - Jan 2016
Starting with my role based in New Jersey, I was the onsite quality leader during the transfer of production from New Jersey to the Mexico facility. As part of my role, I identified risk management issues and an action plan to close gaps, while working closely with Design Engineering to redesign risk management documentation (DFMEA, PFMEA) to align with corporate formats.
-
-
-
Nurse Assist, Inc.
-
United States
-
Medical Equipment Manufacturing
-
1 - 100 Employee
-
Quality Assurance & Control Manager
-
May 2014 - Oct 2014
I completed a six-month contract overseeing/improving the Quality Management System and representing the organization during customer and regulatory audits. Overall, I orchestrated four customer and two regulatory audits and successfully resolved any audit findings. I completed a six-month contract overseeing/improving the Quality Management System and representing the organization during customer and regulatory audits. Overall, I orchestrated four customer and two regulatory audits and successfully resolved any audit findings.
-
-
-
B. Braun Medical
-
United States
-
Medical Equipment Manufacturing
-
700 & Above Employee
-
Quality Manager, Active Device Operations
-
Jun 2012 - Apr 2014
I accepted responsibility for quality controlling, assuring, and validating all active medical devices designed and manufactured at the site, while partnering with regulatory agencies in the US, Canada, and EU to maximize compliance with 21 CFR 820, CMDR, ISO 13485, and ISO 14971, among others. Over my time with the company, I…Significantly improved the Quality Management System and hosted an FDA audit within the first two weeks of being promote, correcting the six observations noted to officially close the audit within ten months. I responded to and completed three FDA reportable and three non-reportable field corrections. Acted as the Quality Expert across all phases to optimize the design for a new pharmaceutical mixing pump. Show less
-
-
Senior Quality Engineer - OEM
-
Jul 2010 - Jun 2012
In my first role with the group, I quality assured the OEM product portfolio, including new products in development across all phases. For key contributions, I…Defined new product quality requirements, test methods, DFMEA development, sampling plans and hypothesis testing to ensure new products exceeded strict customer requirements and government standards. I crafted the detailed specifications for five new products that were successfully launched.Designed, rolled out, and validated three new product testing methods. Show less
-
-
-
Boston Scientific
-
United States
-
Medical Equipment Manufacturing
-
700 & Above Employee
-
Senior Quality Engineer
-
Dec 2007 - May 2010
With Boston Scientific, I devised/maintained quality control measures to continually maximize quality and safety for a specialized portfolio of industry-leading medical devices. For my work, I was honored with a Silver Achievement Award for Outstanding Leadership in recognition of resolving a key customer complaint. I also introduced changes to optimize a process, slashing the number of noncompliance incidents from 12 to 5. With Boston Scientific, I devised/maintained quality control measures to continually maximize quality and safety for a specialized portfolio of industry-leading medical devices. For my work, I was honored with a Silver Achievement Award for Outstanding Leadership in recognition of resolving a key customer complaint. I also introduced changes to optimize a process, slashing the number of noncompliance incidents from 12 to 5.
-
-
-
Covidien
-
United States
-
Medical Device
-
Senior Quality Engineer
-
2008 - 2008
Lead quality engineering initiatives for a global manufacturer and distributor of innovative medical product solutions encompassing medical devices, imaging solutions, pharmaceutical products, and medical supplies; 2007 revenues exceeded $9B. Oversee high-volume injection-molded medical devices to ensure plant operations comply with all regulations and the highest quality standards. Accountable for evaluating quality concerns, as well as device and component performance cycle from the field to the production floor. Collaborate with manufacturing operators to identify, investigate, and resolve process and product quality issues. Manage the Material Review Board and corrective actions for all product lines. Conduct supplier audits and EO sterilization validation for four product families. Identified $100K worth of savings projects impacting all product families. Recognized as a key "Operation Excellence Member." Show less
-
-
-
-
Senior Quality Engineer
-
2006 - 2008
Drove quality improvement operations for a world-leading developer, manufacturer, and marketer of cutting-edge medical device products and services. Ensured customer and regulatory compliance metrics consistently met the highest standards and status quo. Evaluated quality concerns and device and component performance from the field to the production floor. Listened to operators regarding concerns. Identified root of quality issues and implemented swift solutions. Conducted manufacturing system audits to comply with ISO 13485 and FDA standards. Operated optical inspection equipment, design / assemble fixtures, and program a leak tester. Gathered and maintained yield data for product lines and customer complaints / returns. Collaborated with multifaceted corporate teams to maintain and enhance processes. Wrote weekly and monthly quality metrics reports and validation protocols for new products. Developed Oracle quality modules and taught facility personnel in proper use. Trained inspectors on new policies, procedures, and processes. Reduced inspection time while maintaining the highest level of quality by revising related procedures. Decreased open complaint process / resolution implementation from 180+ to 30 days. Increased DUR first-pass production from 89% to 98% utilizing Six-Sigma initiatives encompassing Kaizen, Kanban, DOE, and various additional tools. Devised weekly dashboard and management statistics for CAPA and continuous improvement. Improved throughput 20%, reduced travel 33%, and balanced TAKT time by participating in a LEAN project that revised the layout and movement of a product in DUR value stream. Show less
-
-
-
Foster Corporation
-
United States
-
Plastics Manufacturing
-
1 - 100 Employee
-
Quality Manager
-
2004 - 2006
Led multi-site quality directives for a leading developer and manufacturer of state-of-the-art material solutions. Developed and implemented OQ and PQ protocols for mixing active pharmaceuticals in plastics. Accountable for inspections at; plants. Served as key contact to customers in assessing needs, complaints, and quality issues. Identified, tracked, and executed comprehensive solutions. Analyzed and assessed all quality operations and recommended improvement programs that met customer, regulatory (FDA), and company compliance measures. Responsible for maintaining and documenting the highest quality performance metrics and submit results to management teams. Oversaw the operations of lab equipment including ash ovens, viscosity machines, microscopes, and presses. Reduced floor product lead time customer service rates from seven to two days by utilizing a balanced workflow, spaghetti diagram, Kaizen (layout and process flow), and Kanban (scheduling board). Introduced a new product line and established related production and testing parameters utilizing Six-Sigma initiatives including DOE and Kanban. Spearheaded the successful implementation of a cGMP Quality system within one year. Decreased customer complaints 10% using root cause analysis and enhanced communication techniques. Show less
-
-
-
GENERAL CABLE CORPORATION
-
United States
-
Computer Hardware Manufacturing
-
Quality Assurance Manager
-
1998 - 2003
Accountable for ensuring the attainment of quality and assembly initiatives for a leading manufacturer of copper, aluminum, and fiber optic wire and cable products. Led team of six associates in maintaining quality measures / metrics that met customer, company, and regulatory guidelines. Responsible for managing and allocating a $250K budget. Operated OTDR's and environmental chamber's equipment. Liaised with customers in resolving all complaints. Improved quality rating 10% for major customers; successfully reduced complaints 8% within the first two years by instituting a new tracking system. Spearheaded Navy approved MIL testing procedures and performed all reliability testing. Created test plans for new products released to production and implemented new laser micrometers for on-line testing purposes; successfully obtained related testing equipment and trained all associates. Show less
-
-
Education
-
University of Illinois Urbana-Champaign
Bachelors of Science (BS), Ceramic Engineering -
Keller Graduate School of Management of DeVry University
Masters of Science (MS), Project Management
Community
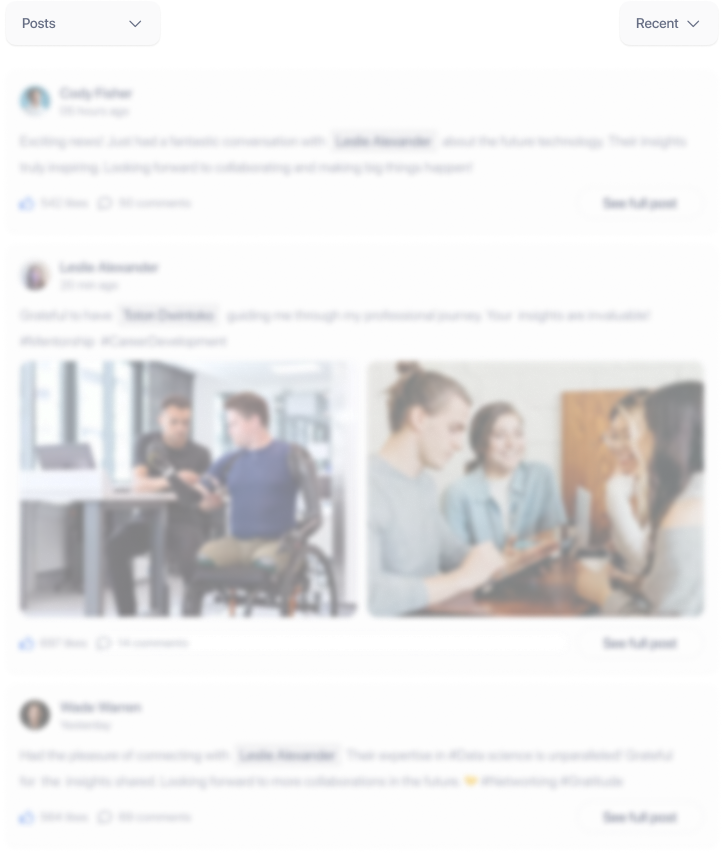