
Philip Weston
Purchasing and Supply Chain Manager at Omlet Ltd- Claim this Profile
Click to upgrade to our gold package
for the full feature experience.
Topline Score
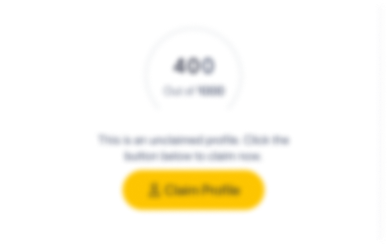
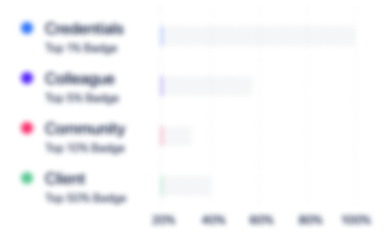
Bio

Jane Rawden
I met Phil whilst delivering the Senior Leadership and Development Programme within Helix Lighting. Phil is a professional manager who is results driven and can lead, manage and motivate his team. He has applied his knowledge and skills to increase motivation within the team directly relating to an improvement in performance. People projects have included change management and restructuring. Phil’s strength within the leadership team was as a knowledgeable and driven Operations Manager and a coach and mentor to his colleagues within the senior team.

Jane Rawden
I met Phil whilst delivering the Senior Leadership and Development Programme within Helix Lighting. Phil is a professional manager who is results driven and can lead, manage and motivate his team. He has applied his knowledge and skills to increase motivation within the team directly relating to an improvement in performance. People projects have included change management and restructuring. Phil’s strength within the leadership team was as a knowledgeable and driven Operations Manager and a coach and mentor to his colleagues within the senior team.

Jane Rawden
I met Phil whilst delivering the Senior Leadership and Development Programme within Helix Lighting. Phil is a professional manager who is results driven and can lead, manage and motivate his team. He has applied his knowledge and skills to increase motivation within the team directly relating to an improvement in performance. People projects have included change management and restructuring. Phil’s strength within the leadership team was as a knowledgeable and driven Operations Manager and a coach and mentor to his colleagues within the senior team.

Jane Rawden
I met Phil whilst delivering the Senior Leadership and Development Programme within Helix Lighting. Phil is a professional manager who is results driven and can lead, manage and motivate his team. He has applied his knowledge and skills to increase motivation within the team directly relating to an improvement in performance. People projects have included change management and restructuring. Phil’s strength within the leadership team was as a knowledgeable and driven Operations Manager and a coach and mentor to his colleagues within the senior team.

Experience
-
Omlet Ltd
-
Manufacturing
-
1 - 100 Employee
-
Purchasing and Supply Chain Manager
-
Mar 2018 - Present
-
-
-
Uponor
-
Finland
-
Wholesale Building Materials
-
700 & Above Employee
-
European Warehouse and Logistics Project Manager
-
Sep 2016 - Jan 2018
Key Achievements: ● Successfully specified, sourced and implemented the transfer of the UK Warehouse to a third part service provider in 2016 which provided flexible solutions and demonstrated cost savings of 30%● Engage with business partners form other disciplines including Sales, Marketing, Finance and product managers to ensure total business objectives are achieved.● Gain insights into the needs of the business; set objectives in line with organisational needs, including scope, content, timings and budget; plan work schedules and deadlines to meet the agreed needs● Collaborate with Senior Managers and other departments including Sales, Marketing, Finance and Product Managers to identify and analyse core requirements and key features of projects● Managed the insights of managers, directors and stakeholders, helping to ensure all parties agreed with the current scope and roadmap of projects
-
-
South West (Europe) Supply Chain Manager
-
Oct 2014 - Sep 2016
Key Achievements:● Achieved cost reductions against an annual budget of 2 Mill Euros incurred costs, and 1 million Euros of inbound and outbound freight● Developed supply chain solutions both internally and with customers to provide the highest levels of ‘customer on time in full service’ levels recorded for Uponor, whilst achieving reduced lead-times where appropriate.● Developed a customer centric philosophy within the supply chain functions to become more customer facing and focusedKey Responsibilities:● Full accountability for logistics and supply chain management for Italy, France, Spain, Portugal, UK and Ireland, with annual gross sales of approx. 85 mill Euros across distribution sites ● Full management of implementing company distribution/logistical strategies, direction and tactics working toward the achievement of corporate objectives● Managed the delivery schedule of a wide variety of items to multiple international sites through different routes● Managed stock levels, delivery times and transport costs; coordinated and controlled the order cycle; evaluated performance and quality and to plan improvements● Allocated and managed staff resources according to changing needs● Liaised and negotiated with customers and suppliers; developed business by gaining new contracts, analysing logistical problems and producing new solutions
-
-
UK Supply Chain Manager
-
Mar 2012 - Oct 2014
In the position of UK Supply Chain Manager I have Total Management and budgetary control of the Supply Chain responsibilities that include: Warehouse and Distribution development, Planning and Purchasing, internal supply development, site building service and Health & Safety.I initiated internal projects that focused on building agile solutions, whilst reducing costs and process complexity, and developed inter department communication across Sales functions, Customer service, planning and warehouse and dispatching teams. Annual cost savings of £200k, whilst improving lead-times by 20%, and OTIF 11% .
-
-
-
-
Operations Manager
-
Feb 2002 - Apr 2012
KEY ACHEIVEMENTS• Managed the design and installation of 110,000 square foot warehouse build.• Project led the installation of SAGE1000 ERP system and Datalinx WMS system on time and within the budget of £285,000.• I successfully worked and resolved technical and supply issues in China with key suppliers, whilst sourcing and benchmarking new suppliers. On time delivery was improved from 55% to 98%.• Seamless integration of business acquisition maintaining customer service • Created shift pick/pack operation, shipping 2.4m sku's to retail outlets• Improved transport fleet utilisation by 20% by load planning initiatives• Created backhaul relationships with customers to reduce costs and carbon footprint. • Managed a budget of £1,850K & recruited / recruited a team of 120 multi-functional staff (inc manufacturing staff)• Introduced KPIs, for increased accountability & to ensure 'best practice'• Responsible for all aspects of supply chain distribution, warehouse & inventory control• Recruitment, training, appraisals & career development of key staff• Enabled 12% headcount reduction through introduction of new technology• I have introduced new routes to market for high street retailers. • Implemented PI cycles counts and managed stock shrinkage loss to less 0.1%• I have embraced best practice with regard to stock rotation, pick routes and storage• Responsibility for contract negation for UK based transport and suppliers. And have reduced costs in a time of pressure on margins.• I’m successful in leading and coaching teams and where necessary performance management, including disciplinary, dismissal and redundancy with a track rate of no tribunals to dateTechnical Skills• Prince 2 project management qualified• CILT level 5 Professional diploma in Logistics and Transport (currently studying)• Microsoft Excel and Word• Microsoft Project• Clarizen Project management
-
-
-
-
Production Manager
-
Jan 1989 - Feb 2001
G&A manufacturing were the UK’s largest manufacturer of precious metal jewelry. I managed and or developed various highly skilled departments. In 2000 I was appointed to a project team of four to plan, cost and facilitate the relocation of manufacturing to Thailand. G&A manufacturing were the UK’s largest manufacturer of precious metal jewelry. I managed and or developed various highly skilled departments. In 2000 I was appointed to a project team of four to plan, cost and facilitate the relocation of manufacturing to Thailand.
-
-
Education
-
Bournville School Birmingham
Community
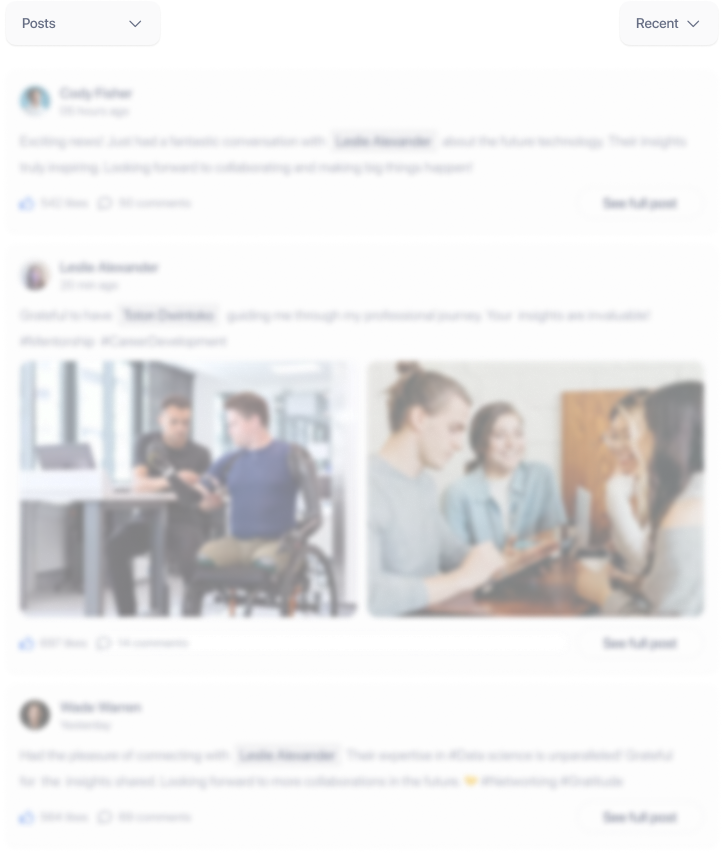