Phil Murtagh
Supply Chain Planning Manager at Mulgowie Farming Company- Claim this Profile
Click to upgrade to our gold package
for the full feature experience.
Topline Score
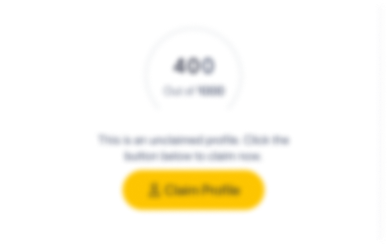
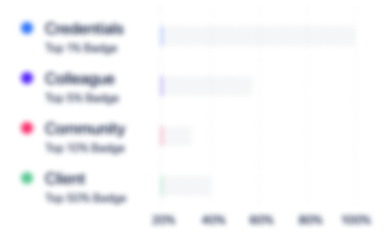
Bio

John Warnock
I worked with Phil Murtagh at Australasian Lubricants Manufacturing Company (ALMC) from 2008 to 2015. Phil was ALMC's Business Analyst in the period 2008-2013 and in this role he reported directly to me, as the CEO. The Business Analyst role was a key senior development role for high potential employees. Phil performed very well in this role for five years and was rewarded with a promotion to the position of Facility Manager for the Lytton manufacturing and distribution facility, when that role became vacant in 2013. In the role of Business Analyst, Phil proved his leadership, interpersonal skills and trustworthiness by very ably supporting the ALMC Board, CEO and senior management team. Phil was highly regarded by the ALMC Board. He attended all Board meetings as the minute secretary, however he was also a trusted advisor due to his depth of knowledge in the business. In this role, Phil also lead a number of critical projects across the ALMC business including business excellence (resulting in an international Class A certification), lean and international performance benchmarking, to name just a few. In these projects, Phil demonstrated that he was able to build relationships, trust and effectively engage with all levels of people within ALMC through to the shop floor. Phil is an intelligent, experienced professional, highly trustworthy, and with great people skills.He has a great depth of knowledge in the areas of supply chain, manufacturing, distribution and business improvement. I would gladly work with Phil again, and recommend him to prospective employers.

Bob Simpson
I have worked with Phil at ALMC from 2012 to 2015. Phil is an effective leader who is results orientated with excellent relationship building skills with internal and external stakeholders. Phil has knowledge and experience in supply chain, manufacturing, warehousing, data analysis to identify opportunities for improvement and operational excellence utilising the Buker methodology. Phil has a keen focus on people, safety and continuous improvement through the implementation of lean methodology and has established a track record of performance improvement through engaging his team. Phil would make a valuable contribution to any role he pursues.

John Warnock
I worked with Phil Murtagh at Australasian Lubricants Manufacturing Company (ALMC) from 2008 to 2015. Phil was ALMC's Business Analyst in the period 2008-2013 and in this role he reported directly to me, as the CEO. The Business Analyst role was a key senior development role for high potential employees. Phil performed very well in this role for five years and was rewarded with a promotion to the position of Facility Manager for the Lytton manufacturing and distribution facility, when that role became vacant in 2013. In the role of Business Analyst, Phil proved his leadership, interpersonal skills and trustworthiness by very ably supporting the ALMC Board, CEO and senior management team. Phil was highly regarded by the ALMC Board. He attended all Board meetings as the minute secretary, however he was also a trusted advisor due to his depth of knowledge in the business. In this role, Phil also lead a number of critical projects across the ALMC business including business excellence (resulting in an international Class A certification), lean and international performance benchmarking, to name just a few. In these projects, Phil demonstrated that he was able to build relationships, trust and effectively engage with all levels of people within ALMC through to the shop floor. Phil is an intelligent, experienced professional, highly trustworthy, and with great people skills.He has a great depth of knowledge in the areas of supply chain, manufacturing, distribution and business improvement. I would gladly work with Phil again, and recommend him to prospective employers.

Bob Simpson
I have worked with Phil at ALMC from 2012 to 2015. Phil is an effective leader who is results orientated with excellent relationship building skills with internal and external stakeholders. Phil has knowledge and experience in supply chain, manufacturing, warehousing, data analysis to identify opportunities for improvement and operational excellence utilising the Buker methodology. Phil has a keen focus on people, safety and continuous improvement through the implementation of lean methodology and has established a track record of performance improvement through engaging his team. Phil would make a valuable contribution to any role he pursues.

John Warnock
I worked with Phil Murtagh at Australasian Lubricants Manufacturing Company (ALMC) from 2008 to 2015. Phil was ALMC's Business Analyst in the period 2008-2013 and in this role he reported directly to me, as the CEO. The Business Analyst role was a key senior development role for high potential employees. Phil performed very well in this role for five years and was rewarded with a promotion to the position of Facility Manager for the Lytton manufacturing and distribution facility, when that role became vacant in 2013. In the role of Business Analyst, Phil proved his leadership, interpersonal skills and trustworthiness by very ably supporting the ALMC Board, CEO and senior management team. Phil was highly regarded by the ALMC Board. He attended all Board meetings as the minute secretary, however he was also a trusted advisor due to his depth of knowledge in the business. In this role, Phil also lead a number of critical projects across the ALMC business including business excellence (resulting in an international Class A certification), lean and international performance benchmarking, to name just a few. In these projects, Phil demonstrated that he was able to build relationships, trust and effectively engage with all levels of people within ALMC through to the shop floor. Phil is an intelligent, experienced professional, highly trustworthy, and with great people skills.He has a great depth of knowledge in the areas of supply chain, manufacturing, distribution and business improvement. I would gladly work with Phil again, and recommend him to prospective employers.

Bob Simpson
I have worked with Phil at ALMC from 2012 to 2015. Phil is an effective leader who is results orientated with excellent relationship building skills with internal and external stakeholders. Phil has knowledge and experience in supply chain, manufacturing, warehousing, data analysis to identify opportunities for improvement and operational excellence utilising the Buker methodology. Phil has a keen focus on people, safety and continuous improvement through the implementation of lean methodology and has established a track record of performance improvement through engaging his team. Phil would make a valuable contribution to any role he pursues.

John Warnock
I worked with Phil Murtagh at Australasian Lubricants Manufacturing Company (ALMC) from 2008 to 2015. Phil was ALMC's Business Analyst in the period 2008-2013 and in this role he reported directly to me, as the CEO. The Business Analyst role was a key senior development role for high potential employees. Phil performed very well in this role for five years and was rewarded with a promotion to the position of Facility Manager for the Lytton manufacturing and distribution facility, when that role became vacant in 2013. In the role of Business Analyst, Phil proved his leadership, interpersonal skills and trustworthiness by very ably supporting the ALMC Board, CEO and senior management team. Phil was highly regarded by the ALMC Board. He attended all Board meetings as the minute secretary, however he was also a trusted advisor due to his depth of knowledge in the business. In this role, Phil also lead a number of critical projects across the ALMC business including business excellence (resulting in an international Class A certification), lean and international performance benchmarking, to name just a few. In these projects, Phil demonstrated that he was able to build relationships, trust and effectively engage with all levels of people within ALMC through to the shop floor. Phil is an intelligent, experienced professional, highly trustworthy, and with great people skills.He has a great depth of knowledge in the areas of supply chain, manufacturing, distribution and business improvement. I would gladly work with Phil again, and recommend him to prospective employers.

Bob Simpson
I have worked with Phil at ALMC from 2012 to 2015. Phil is an effective leader who is results orientated with excellent relationship building skills with internal and external stakeholders. Phil has knowledge and experience in supply chain, manufacturing, warehousing, data analysis to identify opportunities for improvement and operational excellence utilising the Buker methodology. Phil has a keen focus on people, safety and continuous improvement through the implementation of lean methodology and has established a track record of performance improvement through engaging his team. Phil would make a valuable contribution to any role he pursues.
0
/5.0 / Based on 0 ratingsFilter reviews by:
Credentials
-
Lean Inventory Management
LinkedInJan, 2019- Sep, 2024 -
INSEAD (Business School) Business Strategy & Financial Acumen, 2017
-Feb, 2017- Sep, 2024 -
Finance for Company Directors
A.I.C.D. (Aust. Institute of Company Directors)Sep, 2011- Sep, 2024
Experience
-
Mulgowie Farming Company
-
Australia
-
Farming
-
1 - 100 Employee
-
Supply Chain Planning Manager
-
Feb 2020 - Present
“Head hunted” to join Mulgowie – a family owned vertically integrated horticultural grower, packager and marketer of fresh vegetables operating along the entire East coast of Australia. Responsible for stabilizing and optimizing the performance and commercial results of the entire Supply Chain. My achievements to date include: 1. Establishing NEW Daily Supply Chain (Operations Review) meetings with regional Farm, Agronomy, Harvest, Pack-house and Sales Teams to deliver agreed plans, identify and resolve exceptions, and firm plan the next 72 hours with consideration for crop yield and commercial opportunities. 2. Scoping and executing NEW Harvest Scheduling tools which synchronize Agronomy Crop tracking with SAP Production data to more accurately forecast daily and weekly Crop supply volumes. 3. Facilitating Weekly Review and Planning Meetings to review performance, identify exceptions, lead Root Cause Investigations to resolve significant issues, forecast medium term supply and labor resource requirements and build plans to ensure capability and capacity to maximize commercial results. 4. Other responsibilities include: * Facilitating monthly Supply Reviews (Oliver Wight Integrated Business Planning). * Designing and maintaining business SOP for crop volumes per week per region per farm to maintain continuous supply to meet Sales Demand Plans. * Facilitating Transition meetings during Spring and Autumn planting periods.
-
-
-
Hyne Timber
-
Paper and Forest Product Manufacturing
-
200 - 300 Employee
-
Operations Manager
-
Jun 2019 - Jan 2020
Responsible for continuous operation (24 hours x 7 days per week) of multiple timber processing plants at the Hyne Timber Tuan site to process 750,000 m3 of plantation timber per annum. Leading 130 people with 6 direct reports across multiple shift patterns and work centres to optimise safety, uptime, and efficiency of the Green Mill, Dry Mill, Kilns and Treatment Plants. My achievements included: a. Initiating monthly 1:1 sessions with my reports to mentor and support them, b. Reviewing all safety incidents and coaching all managers and coordinators in effective Root Cause Analysis, c. Leading major investigations into a repeat fire in one kiln, and chemical incident in the Treatment Plant, d. Implementing cost effective shift structures based on Lean analysis of work centre performance, e. Leadership and contingency management to maximise uptime during protracted industrial unrest.
-
-
-
Family
-
Retail
-
My "Gap" Year
-
Oct 2017 - Apr 2019
I nominated for a redundancy from Caltex Aust. after 14 years at the Lytton Site. In the next 12 months, I travelled with my wife and family, renovated the house & garden, lost 14 kg and coached my son to a successful Year 12 OP result. I nominated for a redundancy from Caltex Aust. after 14 years at the Lytton Site. In the next 12 months, I travelled with my wife and family, renovated the house & garden, lost 14 kg and coached my son to a successful Year 12 OP result.
-
-
-
Caltex Australia
-
Australia
-
Oil and Gas
-
1 - 100 Employee
-
Lytton Lubricants Operations Manager
-
Apr 2015 - Sep 2017
Responsible for 70 employees at Lytton with 5 direct reports, producing 60 ML p.a. of bulk and packaged oils and greases as the only Caltex production facility in Australia and the major supply point to interstate warehouses and bulk terminals, Optimised the Lytton site within 4 months of transition from ALMC for Caltex Operations (personnel, products & materials), and participated in TR program which eliminated $4.5m in costs from supply chain, manufacturing and distribution over next 2 years, Implemented new Chain of Responsibility and Caltex's behavioural safety management practises for incident reporting, investigation, review and action completion and achieved last 2 years without a LTI, MTI or major spill,
-
-
-
ALMC
-
Australia
-
Oil and Gas
-
1 - 100 Employee
-
Lytton Lubricants Plant Manager
-
Mar 2013 - Apr 2015
Responsible for 110 employees with 6 direct reports, producing 90 ML p.a. for bulk and packaged oils and grease, which was 50% the ALMC business,Focussed initially on improving middle management effectiveness, promoting employee engagement through workplace improvement teams, monthly site meetings, Site Safety Committee, and Site Consultative Committee,Operating cost management – reduced unit cost rate from 18.2 cpL to 17.0 cpL over 2 years on same (90 ML p.a.) base volume via Lean "turn-around", reorganising work practises to eliminate bottle-necks, removing entrenched overtime and improving labour efficiencies,Personally facilitated and coached 12 Lean Improvement Teams working on selected strategic projects across safety, cost, efficiency, quality, process development, equipment management and new equipment design with great success,The major challenge of this role was leading and motivating the site's employees (30 staff & 80 award) for the last 12 months in the lead up to transition, which was successfully achieved via monthly site meetings to discuss performance, impending challenges and strategy we would use to achieve each target,Delivered 30% additional manufactured throughput (above previously demonstrated capacity) in the last 6 months by critical resource planning and workforce alignment (Oct 2014 - April 2015).
-
-
Business Analyst
-
Aug 2007 - Feb 2013
Coordinated monthly Supply Chain (ERP) Analysis and evaluation for the entire ALMC business and led improvement activities with successful achievement of two (2) Class A certifications from the Buker Corporation (USA) in 2010 and again in 2012,Project leader for an International Benchmarking Studies of Lubricant Manufacturers conducted by PIMS/MALIK, responsible for data consolidation for three manufacturing plants, report submission, interpretation of results and summary reports to the Board and Performance Review sub-committee of our competitive position and opportunities in 2009 and 2011.Reporting directly to the CEO, I co-ordinated and prepared Board and sub-committee meetings, papers, minutes and managed deleted actions. I participated in Board Risk and Strategy workshops and documented ALMC Strategy and Business Plans arising. I completed other tasks and projects for the Board and Senior Management Team and other strategic and root cause analysis projects as assigned by the CEO,
-
-
Base Oil Supply Manager
-
Nov 2007 - Oct 2012
Recognising my previous experience as an ALMC Production Manager and in managing a bulk shipping terminal, I was appointed as Base Oil Supply Manager, responsible for Base Oil imports totalling 155 ML p.a. (worth >$300m p.a.) over 32 grades across 3 manufacturing sites for 5 years – involving multiple, overseas and local suppliers,The key activity was designing an annual supply plan (based on SAP demands) and allocating various supply shipments to the shareholders (BP and Caltex), who were responsible for securing supply to the joint venture from global suppliers. These were governed by three legal agreements and overall “balances” were reported to Board and sub-committees every month,Strategic sourcing initiatives and changes in demand required detailed analysis and a coordinated response. My role was to assess and evaluate options before requesting the preferred supply plan. I was recognised as an SME internally and by both shareholders and international suppliers,Developed and introduced weekly monitoring of dynamic demand accuracy and resultant supply plan effects. This provided a process for ensuring consistent and optimised supply to all three manufacturing sites and success in executing many strategic initiatives.
-
-
Lytton Production Manager
-
Jul 2003 - Oct 2007
Responsible for 82 ML p.a. of Oil and 5 Mkg p.a. of Grease production at the Lytton site with 7 direct and 52 indirect employees,Initial challenge was to stabilise and deliver consistent performance from Lytton manufacturing. I achieved this via combination of scheduling and performance improvement practises (bulk scheduling, work instruction reviews, competency training, biennial maintenance shut-downs, 5S Housekeeping, OEE recording, etc.…),During 2006-7, the Lytton site underwent a $15m upgrade in 2006-7 which required constant coordination with Engineering and construction activities. The site expanded to 85 ML p.a. and personnel from the BP/Castrol plant at Eagle Farm were transferred to Lytton, requiring significant effort in team building and training.
-
-
-
-
State & Terminal Manager
-
Apr 2000 - Mar 2003
This facility handled the import and export of bulk liquid products from tanker ships to shore based tanks to road tankers, and visa versa. Historically it had handled fats and vegetable oils but had started to offer chemical storages and I was recruited as the Terminal Manager with a view to improving OH&S compliance. After 2 years of intensive investment and business growth, I was promoted to new position of State Manager. My achievements included: Designed and implemented maintenance systems for tanks, pipelines and safety equipment, Introduced safety committee, risk assessments, housekeeping audits, weekly toolbox talks, designed and implemented National safety reporting, implemented Environmental protocols, Managed major expansion project worth over $8.5 million in 2002 to achieve EBIT growth from $6M to $8.9M over three years with an annual throughput of 300,000 MT, Interaction with Government bodies - Environmental Protection Authority, Port of Brisbane Corporation and Dangerous Goods Licensing branch to mutual satisfaction, personally completed Development Applications to Brisbane City Council for total expenditures worth over $8.5 million, Leading member of Pinkenba Mutual Aid Group for local industries, emergency services and community groups.
-
-
-
-
12 Years with Dulux Paints (originally part of ICI Australia, then Orica and now independent).
-
Jan 1988 - Mar 2000
I commenced working for Dulux as an engineering graduate and progressed into Operations roles, moving to various sites in different states and 2 x overseas secondments. I also had significant exposure to retails sales as part of my executive development. Major roles and activities are listed below: Qld Warehouse & Distribution Manager & Transition Co-ordinator - Rocklea, Brisbane 12 months SA Warehouse & Distribution Manager, Site & Senior Manager - Regency Park, Adelaide, 3 years Manufacturing Manager Acratex Coatings - Beverley, Adelaide, 8 months Manufacturing Improvement Manager - ICI Paints, Indonesia, 10 months Operations Manager, ICI Dulux PNG - Lae, PNG, 3 years Production Manager, ICI Paints - Padstow, Sydney, 7 months Berger Paints Retail Sales Executive (for ICI Dulux) - SEQ, 18 months Package Filling and Interstate Dispatch Coordinator, ICI Dulux - Rocklea, Brisbane, 14 months Junior Management Trainee - secondment to USA and UK, 10 months Dispersion Supervisor, ICI Dulux - Clayton, Melbourne, 7 months Operations Development Engineer, ICI Dulux - Clayton, Melbourne, 6 months
-
-
Education
-
RMIT University
Bachelor's degree, Chemical Engineering
Community
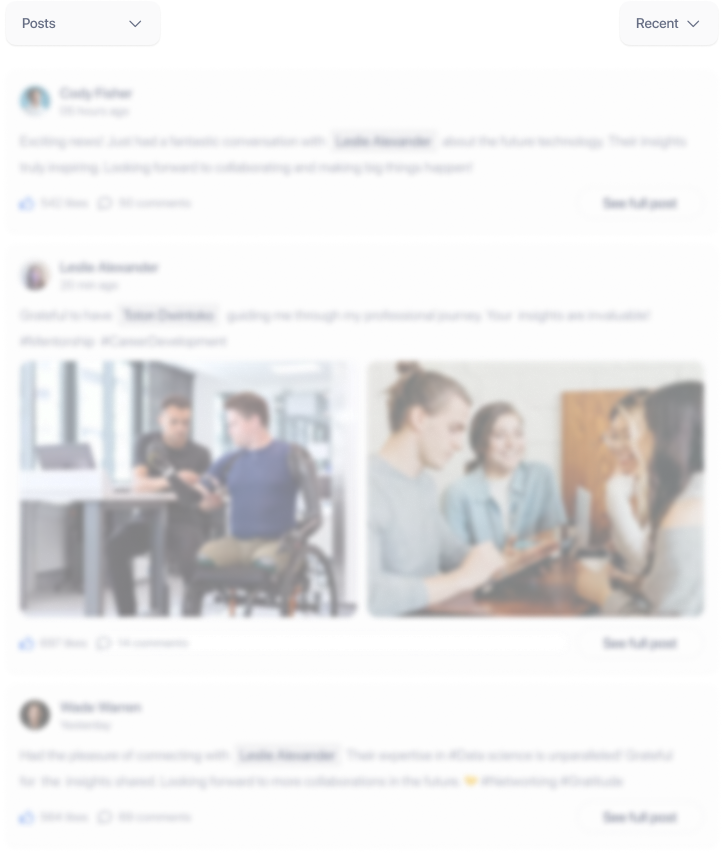