Peter Turner
Adhesive Applications Manager at APPLIED Adhesives- Claim this Profile
Click to upgrade to our gold package
for the full feature experience.
Topline Score
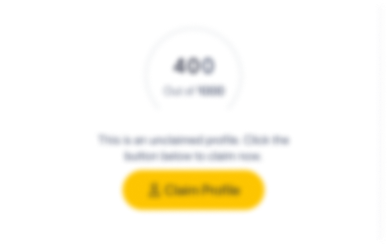
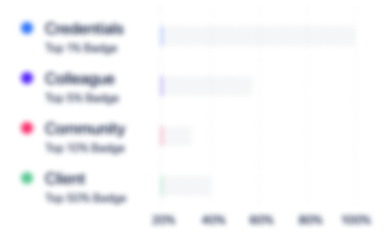
Bio


Experience
-
APPLIED Adhesives
-
United States
-
Chemical Manufacturing
-
100 - 200 Employee
-
Adhesive Applications Manager
-
Oct 2022 - Present
-
-
Applications Engineer
-
Apr 2021 - Present
-
-
Adhesive Application Specialist
-
Jan 2016 - Apr 2021
In-House & On-Site Technical Sales Support and Process Improvement; Identifying adhesive technologies and application processes to exceed customer expectation and meet cost requirements.Developed strong relationships with clients, advocating their requirements while working to find solutions within our organization and supplier base. Also providing continued support to confirm process control and product compliance, or when process change is required.Maintained and developed strong relationships with multiple suppliers within a dynamic and competitive space to find solutions on behalf of customers; often times providing in-house lab testing, qualification and reporting.Worked with suppliers to develop training documentation critical as a resource for internal training and new employee on-boarding, as well as development for our customers and their staff - including presentations and public speaking.Utilized industry standard practices to streamline and promote efficiency within internal lab, material evaluation and sample retention, as well as adding to the repertoire of processes possible in-house. Worked with leadership and operations teams to develop new work queue for technical team which promotes communication, accountability and efficiency while cataloging results for future access. Show less
-
-
Technical Equipment Specialist
-
Jun 2014 - Jan 2016
Provided On-Site and Remote Customer Service and Technical Support for Product Assembly and End-Of-Line Packaging, including equipment installation and technical training for personnel. Strong rapport with customers and sales, providing technical assistance and troubleshooting through training, experience, knowledge and use of available resources; assisted in product recommendation, selection and technical scouting for new product installations. Improved support to sales executives through creation and follow-up on customer quotes. Responded to customer and sales inquiries related to order status, pricing and lead time. Accepted and processed time sensitive customer orders; managed open orders, expedited orders and backorders; communicated status to customers and sales organization. Created supplier purchase orders in a scheduled, timely manner to adequately serve the needs of our external and internal customers, with strong focus on minimizing overhead, supplier lead times and historical tracking of customer demand levels. Managed flow of purchasing related duties, including confirmation, acknowledgement, tracking information and expediting of late or sensitive items. Handled and communicated supplier administrative issues, including supplier mis-shipments, damaged shipments and invoice discrepancies. Administered all aspects of product and inventory decision process, including new product entry, ordering, lot controls and inventory manipulation. Also provided ongoing analysis of alternative product or suppliers to reduce cost and improve value to customers. Utilized contact management system as a resource to inquire; input new account and contact information, update existing information, create sales activities and goals/tasks, track leads and generating reports based on sales metrics from leadership. Show less
-
-
-
Xerox
-
United States
-
Business Consulting and Services
-
700 & Above Employee
-
Processing Analyst
-
Jun 2009 - May 2014
Designed clever processes with versatile solutions to expedite service and create accountability; utilized by the entire organization as well as adopted and implemented by clients and vendors – With documented reduction in process time by as much as 90% in some cases. Created documentation, and provided internal system training, ongoing troubleshooting and global support for colleagues in Mexico, India, and the United States for workflows and applications. Developed and managed metrics used to audit process performance; promote awareness, accountability and proactively targeted opportunities for improvement, efficiency and growth. Special Project Lead, created and initiated effective, bespoke processes to reach requested targets, communicate progress and prevent negative impact on routine workload. Acted as a liaison on behalf of clients with multiple vendors to advocate and resolve escalated and highly complicated issues in an extremely professional, creative, and timely manner. Created positive relationships with clients and colleagues; with excellent focus on providing professional customer service, trusted support and resources above and beyond expectations. Collaborated with clients as a representative to identify and resolve issues; developed and deployed effective Action Matrices and Service Level Agreements to monitor productivity. Conducted loan processing for the mortgage industry, including research, ordering, receiving, imaging, and shipping of sensitive documents in a time sensitive and high volume capacity. Effectively managed multiple projects while adapting to changes in priorities and tracking the status of deliverables requiring a high level of accuracy and urgency. Show less
-
-
-
Clim-a-tech Industries
-
Minneapolis, MN
-
Quality Control Lead
-
Feb 2005 - Dec 2008
Worked within a ISO 9001:2008 compliant environment and implemented Lean Manufacturing and Six Sigma methodologies; Maintained less than three parts per million rejection rate. Teamed with Sales Department and R&D Department; collaborated on new products and revisions, including modified design and material changes to solve and exceed expected performance of products and reduce cost, using CAD Software, CNC Machining and EDM. Maintained communication with customers to continuously monitor and modify processes and update documentation to remain compliant, retain performance, and minimize rejections. Created official documentation required for clients, including Failure Mode Analysis reports, Production Part Approval Process, First Article Inspection Reports and Process Capability. Authored Standard Operation Procedures, and technical documentation needed for process and product compliance, maximum efficiency, cost reduction and internal quality audits. Lowered costs and reduced waste by implementing Statistical Process Control; working with Chief Financial Officer, Plant Manager, Inspectors and Operators to increase efficiency and up-time. Trained employees, and developed an on-going schedule of programs to maintain levels of proficiency; focused on retention of quality standards and revisions to process and product. Conducted incoming material testing, in-process and final quality inspection using Blueprints, SOPs, CpK Analysis, Calipers, Optical Comparators, Durometers, MiniTab and other gauges. Show less
-
-
-
Linhoff Photo & Imaging
-
Minneapolis, MN
-
Process & Technical Support
-
Sep 2003 - Jan 2005
Offered quick and accurate technical service for a diverse equipment list in a highly demanding environment, with special consideration given to the impact unforeseen issues can have on small business. Maintained process control using mechanical and chemical analysis using hydrometers and optical densitometers with advanced knowledge of color space and the photographic process. Created proactive maintenance and training program that promoted punctuality and led to fewer quality issues and reduced cost. Experienced color, slide, and B&W film development and printing including hand processing, push/pull processing and dodge/burn printing. Created a ‘First-In, First-Out’ inventory system to maximize performance and reduce waste, while maintaining proper supply levels. Oversaw daily start-up and maintenance of photographic equipment including hardware and software troubleshooting. Show less
-
-
-
Proex Photo Systems, Inc.
-
United States
-
Photography
-
Technical District Manager
-
Sep 1996 - Sep 2003
Bench testing, diagnostics, repair, and development using wire diagrams, electrical schematics, and scopes to troubleshoot issues down to the circuit board or component level. Demonstrated high level of mechanical and electrical aptitude and problem solving. Responsible for installation and maintenance of new software and hardware. Provided on-site and 24 hour phone support of processing and digital equipment for retail locations. Exceptional management and prioritizing of workforce, production and assets. Professional and expeditious resolution in special circumstances to minimize issues with customers and suppliers. Worked closely with vendors and clients to resolve serious issues, including recommendations for design modification and material alternatives; developing new products and processes. Maintained exceptional communication throughout the resolution process and coordinated priorities via written and verbal channels and offered alternatives to reduce delays. Proactively trained employees on application and equipment troubleshooting, repairing, maintaining, and monitoring of issues; creating a self-sufficient first line of defense for issues. Kept accurate and organized inventory, tracking, and purchasing of equipment, parts, and supplies for timely repair and minimizing effects on production. Maintained strict process control and conducted hazardous waste handling and removal. Strict adherence to OSHA policies. Show less
-
-
Education
-
Dakota County Technical College
Photographic Technology -
Normandale Community College
Associate of Arts (A.A.) -
Burnsville Senior High School
General Education
Community
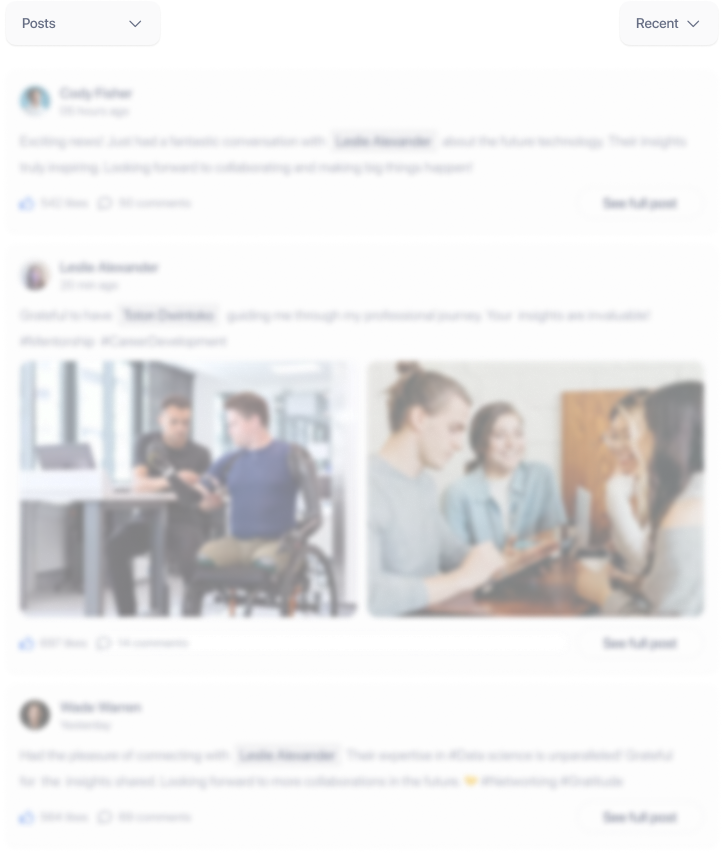