Peter Shery
Mechanical Designer at CAE- Claim this Profile
Click to upgrade to our gold package
for the full feature experience.
Topline Score
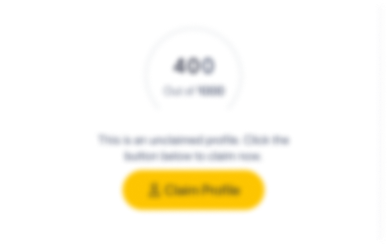
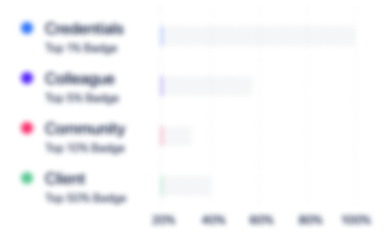
Bio


Experience
-
CAE
-
Canada
-
Aviation and Aerospace Component Manufacturing
-
700 & Above Employee
-
Mechanical Designer
-
Nov 2018 - Present
-
-
-
Gradesavers
-
Canada
-
Education Management
-
1 - 100 Employee
-
Mechanical Drawing Course Tutor
-
Mar 2018 - Jun 2018
• Trained a mini group of students in a mechanical drawing class (MECH 211 at Concordia University) in 2 hour class sessions• Prepared and reviewed course material with the students at each session • Trained a mini group of students in a mechanical drawing class (MECH 211 at Concordia University) in 2 hour class sessions• Prepared and reviewed course material with the students at each session
-
-
-
University of Windsor
-
Canada
-
Higher Education
-
700 & Above Employee
-
Design of an Impacting Sled Machine (M.A.Sc. Side Project)
-
Sep 2015 - Sep 2017
• Proposed solutions for a pneumatic, high-energy impact testing machine during team design reviews• Identified wheel support structure as limiting feature, solving the problem by applying linear motion bearings instead and modifying the frame rails on which the bearings slide
-
-
Design of an Adaptive Cutting Device for Improved Crashworthiness (M.A.Sc.)
-
May 2015 - Aug 2017
• Developed a circular cutting device capable of adaptively adjusting the blade quantity immediately prior to impacting and slicing through a thick aluminum extrusion to dissipate kinetic energy more effectively than conventional, passive structures used in crash safety• Designed 10 iterations of device, resolving potential problems with each new design configuration comprising of a large mechanical and electronic assembly using 3D modeling software CATIA V5• Produced drawings for all parts following drafting standards, including support fixture for device and jig which maintains extrusion elevated and self-centered• Prepared BOM and cost estimates of cutting device materials and stock parts• Provided technical support to (1) computer technologist during fabrication of electronic system and (2) machinists during manufacturing of mechanical parts• Developed a test setup to confirm the numerical simulation results of the cutter deployment, considering ease of manufacturing, ease of assembly, interchangeability, and instrumentation• Validated the cutter motion dynamics using laser displacement transducers and a high-speed camera to detect the rotating cutters with image tracking software• Validated the impact load of cutters with a load cell integrated in the experimental setup• Provided advisor with timely progress updates and recommendations in concise written documentation of results as well as in meetings and oral presentations• Handled new deliverables requested by advisor and adapted to change of M.A.Sc. project scope accordingly
-
-
Graduate Teaching Assistant: Mechanics of Materials Course
-
Jan 2016 - May 2016
• Supported students questions for in-class assignments during weekly tutorial sessions• Developed a lab report outline for the course and provided examples for each section• Helped students in their report writing, course theory and problem-solving• Marked lab reports, assignments, and exams• Invigilated midterm and final exam
-
-
Graduate Teaching Assistant: Aerospace Propulsion Course
-
May 2015 - Aug 2015
• Participated in professor’s lectures to follow course curriculum of newly introduced course• Presented tutorial sessions to the class weekly solving problems on course material• Supported students questions in person and online• Marked quizzes and exams
-
-
-
Concordia University
-
Canada
-
Higher Education
-
700 & Above Employee
-
Design of a Blended Wing Body Drone (Capstone Project)
-
Sep 2013 - Apr 2014
• Designed and manufactured 3 prototypes of an innovative drone with a team of 6 involving multiple disciplines while meeting budget constraints• Determined ideal specifications for propulsion system (i.e. number of batteries, motor type, propeller) while respecting the 2014 AIAA Design Build Fly competition regulations• Validated the theoretical propulsion predictions with experimental thrust and battery discharge tests• Generated the final capstone design report and AIAA design report in parallel • Generated the final capstone design report and AIAA design report in parallel
-
-
-
Pratt & Whitney Canada
-
Canada
-
Airlines and Aviation
-
700 & Above Employee
-
Research Intern: Review of Gear Scoring Methodologies
-
May 2013 - Sep 2013
• Earned an NSERC Undergraduate Industrial Research Award• Improved the complex problem of reliably predicting gear scoring by developing an analytical heat transfer model of the reduction gear box of a P&WC engine• Wrote an instruction manual on the heat transfer modeling procedure for other P&WC engines• Developed a user-friendly spreadsheet to predict scoring probability in bevel gears based on a complex AGMA standard • Earned an NSERC Undergraduate Industrial Research Award• Improved the complex problem of reliably predicting gear scoring by developing an analytical heat transfer model of the reduction gear box of a P&WC engine• Wrote an instruction manual on the heat transfer modeling procedure for other P&WC engines• Developed a user-friendly spreadsheet to predict scoring probability in bevel gears based on a complex AGMA standard
-
-
-
Concordia University
-
Canada
-
Higher Education
-
700 & Above Employee
-
Aircraft Landing Gear Design
-
Sep 2012 - Dec 2012
• Engineered a more light-weight and load-bearing retractable landing gear for the Piper Arrow IV with a team of four • Designed all components for fatigue durability (i.e. tire, fork, cylindrical sliding member, torque link, oleo-strut, brace struts, lugs)• Selected a suitable hydraulic cylinder and linear motion bearing for the shock absorber• Reduced mass of landing gear using fewer brace struts, aluminum-based alloys where possible, and a single-sided fork • Engineered a more light-weight and load-bearing retractable landing gear for the Piper Arrow IV with a team of four • Designed all components for fatigue durability (i.e. tire, fork, cylindrical sliding member, torque link, oleo-strut, brace struts, lugs)• Selected a suitable hydraulic cylinder and linear motion bearing for the shock absorber• Reduced mass of landing gear using fewer brace struts, aluminum-based alloys where possible, and a single-sided fork
-
-
Education
-
Concordia University
Bachelor's degree, Mechanical Engineering -
University of Windsor
Master of Applied Science, Mechanical Engineering -
Dawson College
Pre-University Degree, Pure and Applied Science -
Heritage Regional High School
High School Diploma
Community
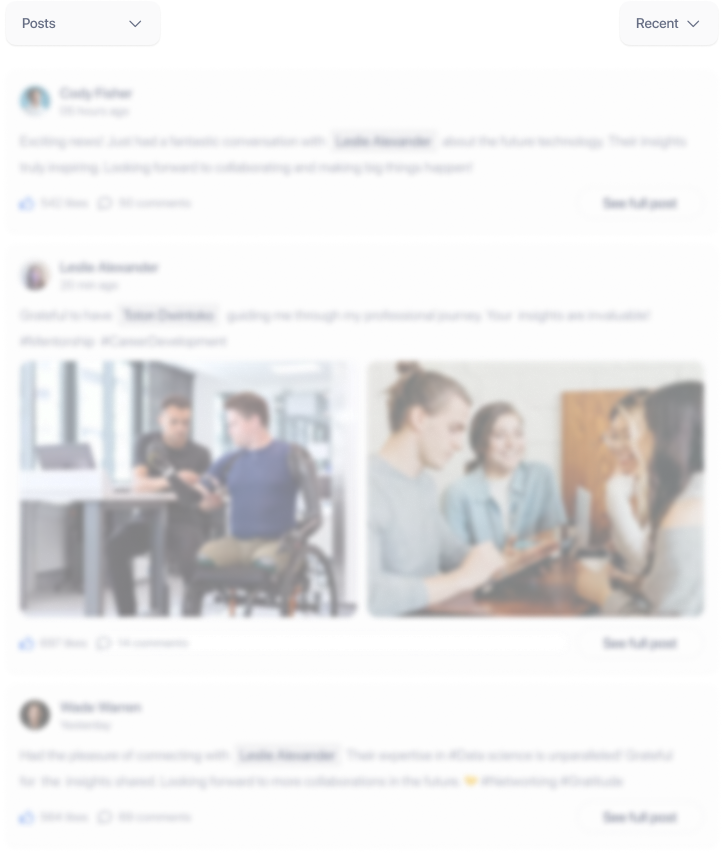