Peter Mierke
General Manager ✦ Responsible for planning and execution of complex logistics projects at Logisticus Group- Claim this Profile
Click to upgrade to our gold package
for the full feature experience.
Topline Score
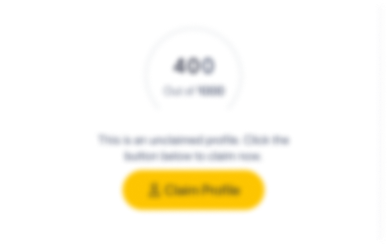
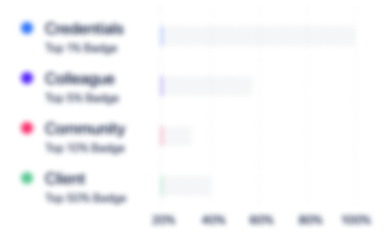
Bio

Vikash Patel
Peter played a large role in developing my leadership and analytical skills. He is a mentor and leader that maintains peer respect because he lives what he preaches. His problem solving skills are unrivaled by most. Peter is a leader that can lead any team to any solution. He is a valuable member of any operation lucky enough to have him.

Vikash Patel
Peter played a large role in developing my leadership and analytical skills. He is a mentor and leader that maintains peer respect because he lives what he preaches. His problem solving skills are unrivaled by most. Peter is a leader that can lead any team to any solution. He is a valuable member of any operation lucky enough to have him.

Vikash Patel
Peter played a large role in developing my leadership and analytical skills. He is a mentor and leader that maintains peer respect because he lives what he preaches. His problem solving skills are unrivaled by most. Peter is a leader that can lead any team to any solution. He is a valuable member of any operation lucky enough to have him.

Vikash Patel
Peter played a large role in developing my leadership and analytical skills. He is a mentor and leader that maintains peer respect because he lives what he preaches. His problem solving skills are unrivaled by most. Peter is a leader that can lead any team to any solution. He is a valuable member of any operation lucky enough to have him.

Experience
-
Logisticus Group
-
United States
-
Transportation, Logistics, Supply Chain and Storage
-
1 - 100 Employee
-
General Manager ✦ Responsible for planning and execution of complex logistics projects
-
Sep 2020 - Present
Logisticus Group supports wide ranging projects in North and South America by bringing together processes, technology, personnel and business models to deliver a more predictable, controlled, efficient and expedited project.✪ KEY RESPONSIBILITIES:Manages project execution on complex and global supply chains. Focus is on ensuring customer CTQs are met during all milestones of the project life-cycle. Drives a continuous improvement culture, with a strong attention to detail and safety. Responsible for all steps in the project lifecycle from RFQ – Bid strategy & submission – planning - kick/off – execution and close/out.• Organizational Development: Faced with a rapid growth in business volume, organized and implemented a training and development program aimed at developing talent and aligning entire company to work more efficiently. Used internal promotions and a new structure to eliminate silos and improve communication while also significantly reducing internal cycles to process orders. Built competency based models for Project Managers, Engineers, Commercial/Sourcing and Field-Based Personnel.• Driven for Improvement: Driving a focused approach to human behavior, existing conditions and new & mature systems/processes in order to support rapid growth and scaling. This requires positive buy-in from teams across the country including partners and suppliers.• Customer Support Through Creativity: Built a culture aimed at supporting customer needs in all facets of their business. Often, this requires an unorthodox approach and rapid action. In numerous examples, this has grown into portfolio based service offerings and revenue streams.• Strategic Vision: In a growth environment, seeking new business opportunities in current and new industries. Leveraging technology strengths to prepare for growth in volume on existing service offerings as well as new. Focus on long-term relationships with customers build partnership rather than single project execution.
-
-
-
Mitsubishi Power Americas
-
United States
-
Renewable Energy Power Generation
-
700 & Above Employee
-
GM/Plant Manager ✦ Realigned organization, surpassing safety, cost of quality, and delivery goals.
-
Jan 2017 - May 2020
$2B Revenue | 2K Employees (North & South America) | MHPSA is a power generation company specializing in new equipment and service/repair for gas/steam turbines, generators, and all associated support equipment.Recognized for my experience leading operations in the power manufacturing industry, I was promoted from a prior role to direct manufacturing, engineering, planning, warehousing, and logistics operations for gas and steam turbines and service repair in the power generation market.Tackling the cost of quality as a primary task, I introduced and championed Lean methodology and fostered a continuous improvement culture. To stem the attrition of our workforce, I focused on the root cause of low morale, which I found was due mostly to a lack of opportunity for career progression. By implementing a strong development culture to attract and retain top talent, I reversed the outward flow of employees and ensured future growth.✪ KEY PERFORMANCE ACHIEVEMENTS:SAFETY: Decreased safety incidents YOY by implementing a Behavioral-Based Safety (BBS) approach with positive results over multiple business cycles.QUALITY: Exceeded goals in rework, scrap, and warranty claims after leading the site through implementation of ISO standards for QMS (9001), EMS (14001), Energy Management (50001), and Occupational Safety & Health (45001).DELIVERY: Improved on-time delivery from less than 90% to 99.5% and supported complex new power plant construction and outage overhauls.SAVINGS: Reduced costs of manufacturing $300K+ in 1 year in addition to YOY savings in rework, scrap, and warranty claims using aggressive problem-solving techniques and proactive measures in manufacturing processes and employee training.CULTURE: Instituted a training and development program to build the talent bench for future growth. Championed a diversified college intern program and succession plans for women in manufacturing environments.
-
-
DIRECTOR OF OPERATIONS ✦ Slashed material and labor costs and decreased production lead time.
-
Sep 2015 - Dec 2016
I was promoted from my prior role to direct a workforce of 150 and expand the safety, quality, and delivery gains that I achieved for a single product line across varied products and processes. In this role, I standardized a continuous improvement strategy grounded in the Lean philosophy using vertically integrated processes in the manufacture of combustion hardware/components used in heavy-duty industrial gas turbines.🏆 Received Georgia Manufacturer of the Year Award (2015)✪ KEY PERFORMANCE ACHIEVEMENTS:SAFETY: Improved safety metrics such as the OSHA TRIR incident rate after implementing a new BBS program to reduce risk by improving systems, controls, and human behavior. QUALITY: Implemented risk abatement actions such as FMEA and 8-Step problem solving to ensure products were made to specification, on-time, and under budget.DELIVERY: Cut lead time of gas turbine assembly by 2 weeks using Lean manufacturing and waste elimination measures.SAVINGS: Drove down material costs by $1M and labor costs by $150K on gas and steam turbines by developing improved risk analysis approach to continuous improvement.CULTURE: Managed safety, quality, delivery, and cost metrics by setting strategy and goals/objectives with management staff and conducted regular reviews with action-based tactics to achieve results.
-
-
COMBUSTION OPERATIONS MANAGER ✦ Turned around a failing organization within 1 year.
-
Apr 2012 - Sep 2015
Following my success with GE Energy, I was hired by MHPSA to steer start-up operations, capacity planning, workforce onboarding and training, equipment procurement, and flow setup. I trained all personnel on Lean principles, focusing the Kaizen activities on eliminating waste and improving product flow.Having met all financial and delivery metrics, I was credited for turning around a failing organization within 1 year by focusing on organizational structure and developing existing talent while attracting new talent for key positions.✪ KEY PERFORMANCE ACHIEVEMENTS:SAFETY: Cut workplace injuries by 50% per year and then to zero for several years.QUALITY: Lowered the cost of quality from $1.5M to $370K in 3 years, instituting a cross-functional approach between engineering and quality functions.DELIVERY: Developed tollgate-based qualification program decreasing cycle time. Improved communication with Japan-based suppliers reducing lead times and costs.SAVINGS: Yielded under-budget results on all line items YOY by developing and managing budget protocols, driving performance gains in all areas.CULTURE: Imbued positive attitude and cast long-term vision to keep doors open, achieving world-class status in safety, quality, delivery, cost, and productivity.
-
-
-
GE Power
-
United States
-
Electric Power Generation
-
700 & Above Employee
-
LOGISTICS OPERATIONS MANAGER ✦ Boosted on-time delivery 20%, cut costs $150K.
-
Jul 2009 - Apr 2012
$37.1B Revenue (2009) | 82K Employees | Founded in 2008 as a subsidiary of General Electric, GE Energy produces engines, turbines, and generators as well as measurement and control systems.As the Logistics Operations Manager for North and South America, Europe, and China, I oversaw a workforce of 125. My overarching role was to direct the multifunctional international team in logistics, customs compliance, and brokerage operations.Leveraging my prior Naval experience, I meticulously detailed the pre-planning of over-dimensional components, multi-leg international shipments, customs release, and material flow for production.During my leadership tenure, we launched and managed $1B global logistics and customs operations for all of GE Energy, including inbound material shipped from suppliers to GE Energy factories as well as outbound finished turbines to project sites.✪ KEY PERFORMANCE ACHIEVEMENTS:SAFETY: Earned highest rating (zero safety incidents) and recognized for multiple best practices from internal and ISO re-certification audits.QUALITY: Instituted QMS development and carrier qualification program, reduced damage to high-value material, lowered the cost of quality, and declined fulfillment risk.DELIVERY: Improved on-time delivery 20% to project sites by focusing on overall trucking and rail quality.SAVINGS: Recouped $150M+ through contract review, market analysis, productivity, pre-positioning of project cargo, and mode optimization.CULTURE: Reorganized operations team to provide dedicated customer service to each business and established regular reviews using a defined scorecard of key metrics to ensure that financial, compliance, quality, and operational goals were met.
-
-
-
GE
-
United States
-
Industrial Machinery Manufacturing
-
700 & Above Employee
-
GAS TURBINE MANUFACTURING ROLES ✦ Progressively promoted to higher leadership roles.
-
Oct 2000 - Jun 2009
After honorably completing 7 years of military service as a U.S. Naval Officer, I was hired by GE Energy and successively promoted to expanded roles along the following career trajectory (in reverse order):STATORS & UNIT ASSEMBLY CELL LEADERAs a recognized expert in the casing supply chain, I was promoted to manage the strategic and tactical fulfillment of the global supply chain. Leading a workforce of 165, I oversaw 3-shift operations.✪ KEY PERFORMANCE ACHIEVEMENTS:SAFETY: Reduced risk of injuries and surpassed 5 years with zero lost-time incidents.SAVINGS/QUALITY: Decreased internal costs by 26% and eliminated the external cost of quality by improving internal processes, tracking defects, and instituting a robust defect review process.DELIVERY: Zero delays to project schedules and 100% attainment of budget goals. Decreased assembly cycle 2 days on high-volume gas turbines.CULTURE: Advocated and initiated organizational structure change to provide increased expertise to supply chain fulfillment and detailed schedule definition, review, and execution.SOURCING QUALITY ENGINEER – STATORS CELLI certified the overall quality of 50+ suppliers. Verified sourced components met drawing and specification requirements, and tested supplier processes for the highest quality and fulfillment best practices. Delivered $2M+ in savings and drove outstanding customer satisfaction ratings.OPERATIONS LEADER – CASINGS/UNIT ASSEMBLY CELLSLed 3 shifts in 2 functional areas in assembly and production, overseeing safety, quality, workforce planning, training, overtime management, and daily tasking.MRP/BUYER CASINGS CELLDirected production and delivery of 30 global suppliers procuring sand castings, large fabrications, and machined casings used in the assembly of gas turbines. My role involved strategic forecasting, supplier negotiation, selection, awarding, and fulfillment while optimizing balance accuracy, inventory levels, logistics, and shop floor planning.
-
-
-
US Navy
-
United States
-
Armed Forces
-
700 & Above Employee
-
NAVAL OFFICER ✦ Proudly served for 7 years
-
May 1993 - Oct 2000
🥇 Awarded 2 Navy and Marine Corps Commendation Medals and 3 Navy and Marine Corps Achievement Medals.OFFICER IN CHARGE, Navy Officer Recruiting Station (Columbia, SC). Supervised Naval officers and civilians in identifying candidates for Naval Commissioning programs in fields, including medical and engineering.NAVIGATOR AND ADMINISTRATIVE OFFICER, USS KINKAID (San Diego, CA). Managed daily operations of the ship, including deployment to the Persian Gulf. Cited as the leader of all junior officers on board.WEAPONS OFFICER AND ENGINEERING DIVISION OFFICER, USS CORONADO (San Diego, CA)
-
-
Education
-
Darla Moore School of Business
MBA, MBA -
University of South Carolina
BS, Geography
Community
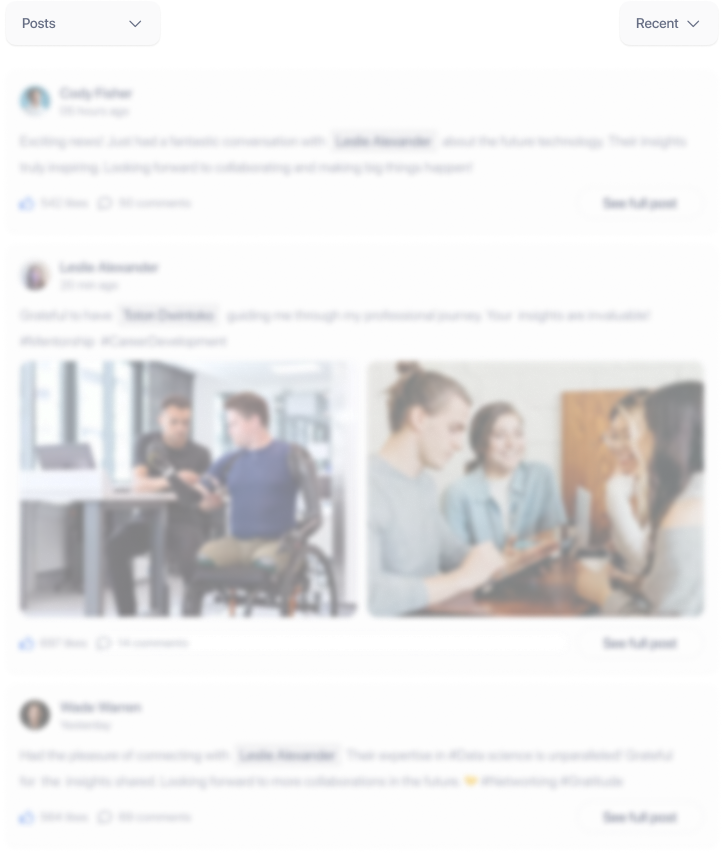