
Peter Blaser
QM Officer / CSO at GRIBI Hydraulics AG- Claim this Profile
Click to upgrade to our gold package
for the full feature experience.
-
English Professional working proficiency
-
German Full professional proficiency
-
Swiss German Native or bilingual proficiency
Topline Score
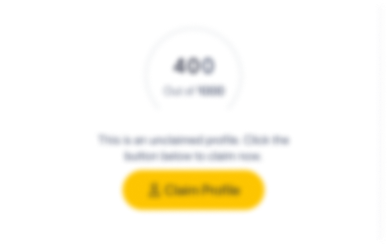
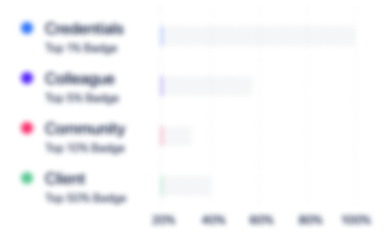
Bio

Samir Gaertner
I have worked with Peter Blaser for many years mas his wisdom, knowledge and people management skills have coached in several occasions. He is a true team member that makes a difference in any organization. Bringing results and setting a long term strategy view.

Samir Gaertner
I have worked with Peter Blaser for many years mas his wisdom, knowledge and people management skills have coached in several occasions. He is a true team member that makes a difference in any organization. Bringing results and setting a long term strategy view.

Samir Gaertner
I have worked with Peter Blaser for many years mas his wisdom, knowledge and people management skills have coached in several occasions. He is a true team member that makes a difference in any organization. Bringing results and setting a long term strategy view.

Samir Gaertner
I have worked with Peter Blaser for many years mas his wisdom, knowledge and people management skills have coached in several occasions. He is a true team member that makes a difference in any organization. Bringing results and setting a long term strategy view.

Experience
-
GRIBI Hydraulics AG
-
Switzerland
-
Machinery Manufacturing
-
1 - 100 Employee
-
QM Officer / CSO
-
Aug 2020 - Present
• Implementation of LEAN improvements • Issueing, maintenance and implementation of the quality management manual and its processes according to ISO 9001:2015, ISO 14001:2015• Communication with customers and authorities• Determination and implementation of corrective measures regarding quality problems • Organization and execution of Audits (authorities, customer, supplier and internal)• Training of employees regarding quality • Implementation of LEAN improvements • Issueing, maintenance and implementation of the quality management manual and its processes according to ISO 9001:2015, ISO 14001:2015• Communication with customers and authorities• Determination and implementation of corrective measures regarding quality problems • Organization and execution of Audits (authorities, customer, supplier and internal)• Training of employees regarding quality
-
-
-
IMI CCI
-
United States
-
Mechanical Or Industrial Engineering
-
700 & Above Employee
-
Manager Quality
-
Apr 2011 - Apr 2019
• Management of quality assurance department (Fossil) - 3 Employees• Implementation of LEAN improvements • Collaboration during Design Failure Mode Analysis DFMEA• Support of the sister companies regardig quality• Monitoring of quality of the sister companies• Issueing, maintenance and implementation of the quality managemen manual and its processes • Communication with customers and authorities• Determination and implementation of corrective measures regarding quality problems • Organization and execution of Audits (authorities, customer, supplier and internal)• Training of employees regarding quality
-
-
-
CCI AG a Division of IMI Nuclear
-
Switzerland
-
Oil and Gas
-
1 - 100 Employee
-
Quality Engineering
-
May 2009 - Mar 2011
Team Leader QA DOC&DR - 8 EmployeesOur team was responsible for:• Review of material certificates• Review of reports• Issuing of inspection certificates• Preparation of final quality documentation• Communication with customers and authorities• Treatment of non-conformity reports• Monitoring of quality during manufacturing• Supporting of production people regarding quality matters• Training of employees regarding quality Team Leader QA DOC&DR - 8 EmployeesOur team was responsible for:• Review of material certificates• Review of reports• Issuing of inspection certificates• Preparation of final quality documentation• Communication with customers and authorities• Treatment of non-conformity reports• Monitoring of quality during manufacturing• Supporting of production people regarding quality matters• Training of employees regarding quality
-
-
-
-
Quality Manager
-
Apr 2007 - Apr 2009
Crossarc ADI SA manufactured rotating discs for the aviation industry. The main customer was Snecma.I was employed as quality manager and performed also some quality assurance and operative activities.Quality Management• Creation and maintaining of the quality management manual according to EN 9100: 2003• Organization and execution of internal and supplier audits• Organization and execution of authority and customer audits• Determination and implementation of corrective measures in case of quality problems• Analysis and presentation of the periodical reporting to management • Training of employees regarding qualityQuality assurance• Managing of quality inspection• Evaluation of non-conformity reports and initiation of corrective actions • Responsible for periodic monitoring of the inspection, test equipmentOperational activities• Responsible for the processes shot peening and balancing• Creation of process and manufacturing specifications • Procurement of products and services• Various sales activities
-
-
-
-
Quality Manager
-
Jan 2003 - Mar 2007
CROSSARC Crossair Engine Repair AG was renamed to CROSSARC AG and was owned by Winpro AG. Manufacturing, refurbishment, repair of aircraft engine components.Quality Management• Creation and maintaining of the quality management manual according to EN 9100: 2003• Creation and maintaining of the Maintenance Organisation Exposition (MOE) according to EASA Part 145 • Organization and execution of internal and supplier audits• Organization and execution of authority and customer audits• Organization and execution of process audits (NADCAP), Thermal spray coating and Electro beam welding EBW.• Determination and implementation of corrective measures in case of quality problems• Analysis and presentation of the periodical reporting to management • Training of employees regarding qualityQuality assurance• Managing of quality inspection• Evaluation of non-conformity reports and initiation of corrective actions • Responsible for periodic monitoring of the inspection, test equipmentOperational activities• Responsible for the processes shot peening and balancing• Creation of process and manufacturing specifications
-
-
-
-
Engine Shop Manager
-
Jan 2000 - Dec 2002
CROSSARC Crossair Engine Repair Center AG was owned by the airline Crossair. Maintenance of the engine (GE CT7-9) has been performed. Furtheremore, Crossarc performed refurbishment of components of the engine Honeywell TFE731 for business jets.Responsibility of the shop Manager was:• Planning of employees' work assignments• Contact person for customers• Disassembly, assembly and testing of aircraft engines (GE CT7-9) and components (Honeywell TFE731)• Performed non-destructive testing (Eddy Current ET) of Fan disk • Creation of process and manufacturing specifications• Issuing of airworthiness certificates “Certifying Staff “
-
-
-
-
Workshop manager "civil aviation"
-
Jan 1998 - Dec 1999
Sulzer AG opened a civil engine shop. Repairs of engine components and overhauls of the CT7 engine were performed.• Contact for customers• Disassembly, assembly of aircraft engines and components
-
-
Construction metalworker
-
Jan 1993 - Dec 1997
Gas turbine rotors• Assembling of compressor and power turbine• Factory assembling of turbine discs• Quality inspection• Creation of quality documentation 3D-Coordinate measuring machine• Operating and programing
-
-
Community
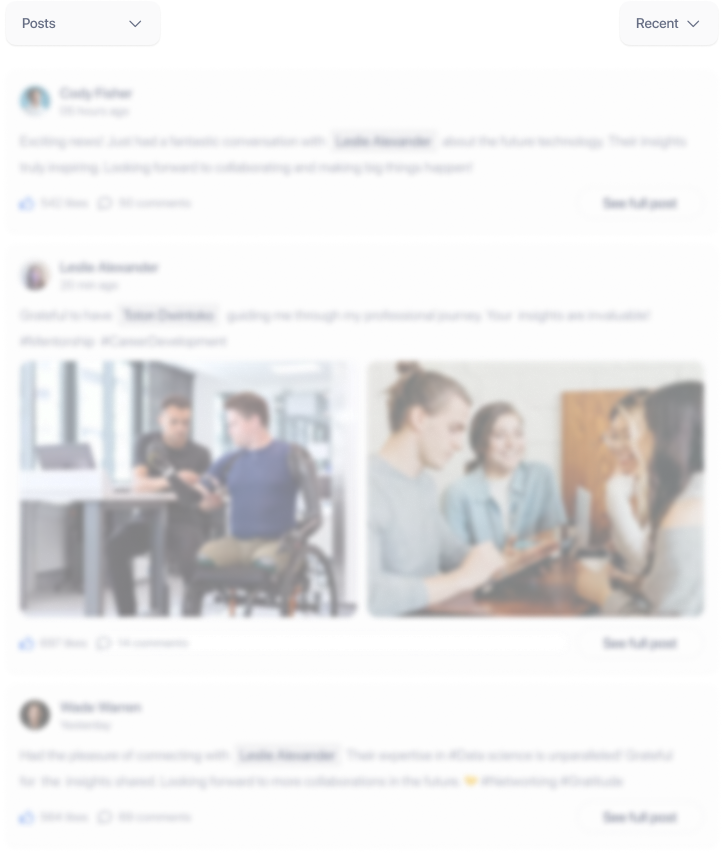