Pedro Ramirez Beltran
Production Control Manager at Micross Components- Claim this Profile
Click to upgrade to our gold package
for the full feature experience.
-
Español Native or bilingual proficiency
-
Ingles Full professional proficiency
Topline Score
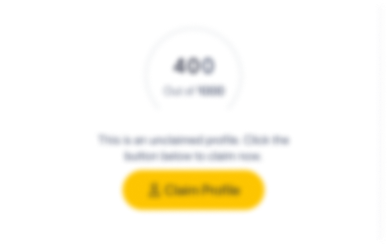
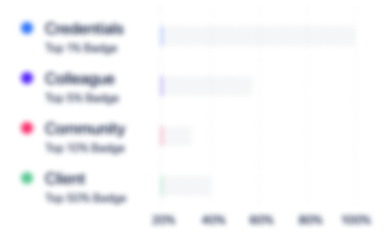
Bio


Experience
-
Micross Components
-
United States
-
Semiconductor Manufacturing
-
200 - 300 Employee
-
Production Control Manager
-
May 2022 - Present
-
-
-
Semtech
-
United States
-
Technology, Information and Internet
-
700 & Above Employee
-
Production Control Manager
-
Nov 2019 - May 2022
-
-
-
iQor
-
United States
-
Outsourcing and Offshoring Consulting
-
700 & Above Employee
-
Program Manager
-
Sep 2016 - Oct 2019
Manage Priorities on production schedules based on Product Introduction, equipment efficiency and Materials supply.•Lead NPI projects and Implementations (Customer Requirements) forwarding to the key players and management project status and, driving goals team to exceed customer expectations.•Develop NPI under 5 Project phases. (Identifying Goals, vision, target completion, Planning Resources, Plan execution, identify risks, Time line/Milestones, Costs, Execution and control and Closure)•Experience in Product Validation (PV), First Article Inspection coordination (FAI), Product Complaint Validation (PCV), PFMEAs, Control Plan (CP), ECOs & CRs.•Plans and Administers procedures and budgets; making sure that procedures and work instructions are efficient in Conjunction with the quality department.•Develops Schedules and manpower requirements for assigned implementations (by Customer Requirements).•Establishes policies which affect subordinate departments and recommend changes to organizational polices; R&R metrics (changes on the Customer Returns).•Part of my activities is continuous improvement through trend reporting analysis and metrics management. Identify and implement new practices and processes that are “best in field” and stablishing clear measurable goals and objectives to determine individual and team results• Work on the Business metrics (KPI): anticipate, meet, and exceed expectations by solving problems quickly and effectively; making customer issues a priority.• Recognizes project's KPIand manage the work within scope, quality, time and cost constraints; suchash TAT (TurnAround Time), OTD (On Time Delivery), LOF (Level Of Fulfillment)•Accountable for overall project success –including; cost, schedule, quality, scope management and KPIs.•Balance the cost, schedule and time frames against the enterprise level project requirements.•Drives continuousimprovement to reach Finance goalsby; weekly, monthly and/or quarter. Show less
-
-
Regional Materials Master Planner
-
Jan 2015 - Sep 2016
• My principal activities: Analyze, maintain, and execute the MRP. Continuously monitor and verify materials pipeline to ensure it meets the MRP requirements. Identify and appropriately address material supply issues. Produce and maintain Backlog reports (by family, volume, locations, order type, aging) and present status to the Customers. Produce and maintain the Backlog future offenders, review strategies to attack proactively. • A weekly activity is to analyze and use historical demand producing future trended forecasts. Identify abnormal demand patterns, using problem solving tools and identifying possible root causes of shortages of components. Produce analytical reports and charts of Customer demand from MRP outputs. Also analyze New Product Introduction Demand; generate component purchasing requirements, and allocating of such demand to different customer locations. • Ensure materials availability through MRP execution, and coordination of materials movement through receiving to production. Proactively eliminate materials liabilities for the company by clearly understanding the ownership (Supplier / Customer). Track and provide supporting data to Business Unit Manager in order to clearly define customer-liable materials with this I provide feedback and support development of Planning initiatives and strategies.• I’m on charge of the Demand Sizing- which is based on properly authorized customer demand, and analyze material and capacity requirements and communicate constraints to the BUL, staff and customer once sizing is complete and an efficient Master production Schedule. Show less
-
-
-
Teleplan International
-
Netherlands
-
IT Services and IT Consulting
-
400 - 500 Employee
-
Production Master Scheduler
-
Sep 2013 - Sep 2014
• The first activity there was to create a weekly rolling Master Production Plan for designated products. Utilize the production capacity, taking into consideration the sales forecast, historical sales, and new business opportunities. Analyzed and identify risks associated with the options built into the Master Production Plan, including Repairing lead times Full analysis of customer monthly demand vs company statements and real requirements. • Important activities such as: to perform supply demand analysis each quarter, highlighting areas of concern for the next 12 months. Make delivery commitments on MTO products, which involve checking uncommitted material and availability of capacity. Develop inventory targets and manage production to achieve targeted inventory levels on both a cost and unit basis. Maintain finished goods inventory at target levels in ensure high service levels, i.e. product availability. • Once of my metrics was: the Project finished goods inventory levels on a quarterly basis. Achieve desired corporate inventory turn targets. And the follow up to the daily schedule with an order and sequence for the operation team. Expedites and control any backorder for any model, to prioritize according backlog and urgent request from the customer. Insure coordination with plant schedulers to execute Production Plan on a weekly and monthly basis. Monitor actual output versus the Master Production Plan. Identify gaps and drive solutions, including a metric on production performance to the requested production schedule. Show less
-
-
-
Jabil
-
United States
-
Appliances, Electrical, and Electronics Manufacturing
-
700 & Above Employee
-
Production Master Scheduler
-
Aug 2010 - Sep 2013
• My main activity, Ensures that the Master Production Schedule is loaded in alignment with customer contract(s) and liability agreements so that the materials team maintains conformance to the company. Full analysis of customer monthly demand vs company statements and real requirements.• Drives a systematic process to receive, evaluate and fulfill customer demand across the business unit. Ensure the execution and deployment of company standard planning strategies and systems where possible and implement customized solutions where necessary. Manage the overall demand plan and capacity analysis for the BU. Balance capacity across manufacturing sites as required. Show less
-
-
Process Engineer
-
Oct 2007 - Aug 2010
• I was in charge on the quick and accurate Troubleshooting on Process, providing quick responses for quality and repair issues that require sustaining engineering expertises: PFMEA, APQP/PPAP. With daily activities such as: monitoring trends in functional areas, reporting this information to management and customers, and initiating corrective actions as necessary. Prepares daily, weekly, monthly and quarterly data as required strives to achieve excellence in all goals.• Collaborate with support departments to increase production lines’ Productivity and Efficiency the Control and handling de Exclusive orders of the Client. Collaborated as well, with the CI (Customer Improvements) department using Lean Manufacturing Techniques; Kaizen, Pokayoke, implement 5S’s, designed tooling, fixtures or Pokayokes and to get a justification and evaluate the principal areas for an improvement project; Analyzes and plans work, space requirements, workflow and process flow to maximum efficiency. Estimation on production times, TACT Time, statistical methods and estimate future requirements for determine product specifications also participated to create documents and implements procedures that ensure continued operational excellence throughout any single production line into the plant. • Full handle of orders, to have an overview of the revenue of the month. Fixing troubles with invoices, prices, and system problems; high communication with Suppliers and Customer. Verifies that machine maintenance is performed as scheduled on assigned line(s) Reporting in general; KPI’s/Paretto’s. Show less
-
-
Production Supervisor
-
Sep 2004 - Oct 2007
• Participate in the selection, training and evaluation and discipline of the personnel Coordination and Supervision. I provided direct supervision to group of employees with the responsibility to get results based on costs, methods and personnel. Collaborated with support departments to increase production lines’ Productivity and Efficiency with a control and handling of exclusive orders of the Client, to complete the target.• Supervision and Coordination of Shipments, Receiving and WIP with Production Reports and Support to Production Lines also, operations activities to reach Production Goals using ability to work under pressure with Highly flexible and self motivated following 5’s in the organization, document control. Show less
-
-
Education
-
Instituto Politécnico Nacional
PMP, Project Management -
The University of Texas Rio Grande Valley
Bachelor's degree, Project Management -
Rubio Vazquez y Asociados
APICS Training, Business Administration and Management, General -
Universidad Autonoma de Tamaulipas
Ingeniero Industrial -
Universidad Autónoma de Tamaulipas
Ingeniería industrial
Community
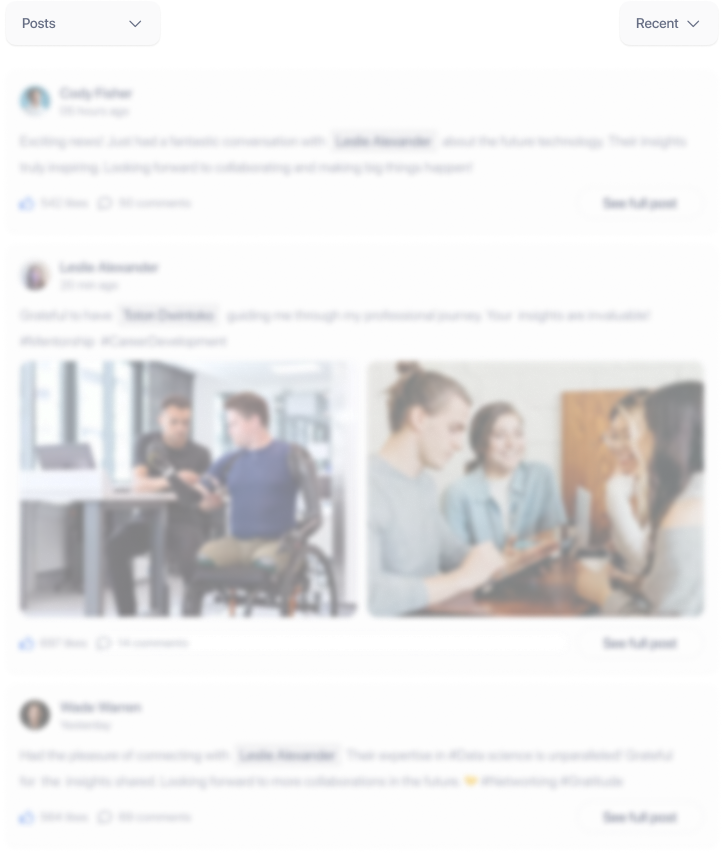