
Pea Sian Tan
Purchasing Manager at DSG (MALAYSIA) SDN. BHD.- Claim this Profile
Click to upgrade to our gold package
for the full feature experience.
Topline Score
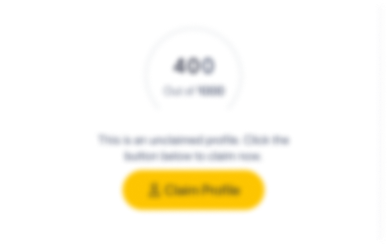
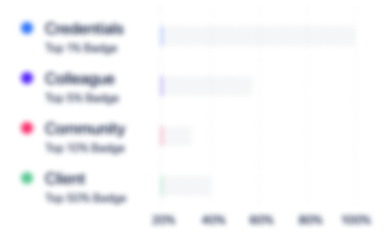
Bio


Experience
-
DSG (MALAYSIA) SDN. BHD.
-
Malaysia
-
Manufacturing
-
1 - 100 Employee
-
Purchasing Manager
-
Dec 2014 - Present
1. Handle indirect company purchases, agreements and contracts.• Identifying and implementing cost saving and cost avoidance opportunities effectively.• Keep abreast of the market trends and new sourcing opportunities• Work with Product Development and Marketing on product development projects• Work with Engineering, Operations and Supply Chain in any efficiency or cost saving projects• Be the country coordinator of collator of information between Central Purchasing and Operations team2. Managing People• Develop competent organizational skills and structure to support the business needs• Coach and supervise the team in order to bring out the best in them• Proactively develop talent / career management plan for team3. Customer and Supplier Management• Liaising between suppliers, manufacturers, relevant internal departments and customers• Identifying potential suppliers, visiting existing supplier, building and maintaining good relationship with them• Evaluate suppliers’ performance with recommendations4. Strategic Planning• Developing an organization’s purchasing strategy - optimizing the balance between price, sustainability, risk management and ethical issues.• Forecasting price trends and impact on future activities-highlighting risks and opportunities with recommendations.• Good in networking with all existing and potential supplier.5. Report directly to Managing Director.Additional function1. 2018 Annual Dinner President2. Internal auditor for ISO 9001 and GMP3. Leader for VMI project4. Leader to PEFC COC projectKey Accomplishments:i. Average yearly cost saving and cost avoidance RM1.2mil (~10% from purchase amount)ii. Implementation of e-Procurement system together with ITiii. Simplified purchasing procedure and process - from manual print PO and manual email PO pdf to supplier change to system auto print PO and auto email to supplier - paperless price comparison and e-approval
-
-
-
Top Glove
-
Malaysia
-
Medical Equipment Manufacturing
-
300 - 400 Employee
-
Purchasing Assistant Manager
-
Aug 2013 - Nov 2014
1. Leader for different team on• Centralized spare part and consumable Procurement with 6 purchasing subordinates and 13 store subordinate.• HQ new project purchase and former centralization with 2 purchasing subordinates• Purchasing factory ranking criteria by setting the KPI to fulfill company requirement2. PO approver for• Centralized spare part and consumable purchase• Others factories spare part and consumable purchase with more than RM10,000• HQ IT purchase• Ipoh and Thailand factories purchase3. Design purchasing SAP customize report and request IT to create and SAP purchasing report analyzer4. Source new supplier for hardware, consumable items, IT purchase and other ad-hoc items5. Implemented rebate scheme for hardware and consumable vendor6. Negotiate competitive price and payment term with vendor7. Prepare & analyze various purchasing report8. To manage 30 HQ and factory purchasers and problem solving for purchasing matters.9. Report Directly to Purchasing and Business Development Senior ManagerKey Accomplishments:i. Success implement of organized two teams of spare part and consumable procurement with reducing stock and get lowest price negotiation on bulk quantity Total saving per year RM500,000/yearii. Successful in rebate scheme implementation to hardware and consumable vendor with saving amount RM50,000/yeariii. Negotiated for IT meter reading program with total yearly saving RM200,000/year
-
-
-
-
Purchasing Development Assistant Manager
-
Dec 2008 - Jul 2013
1. Prepare analysis, reporting of actual (SAP) and forecast model material cost monthly2. Price Contract and cost table comparison and analysis for local & oversea parts (injection, press, assembly, electrical, etc...) 3. Model comparison and analysis with subsidiary4. Model & Part Cost analysis5. Estimate next 3 months forecast model material ratio (SAP) and analyze6. New vendor development7. Cost reduction strategy8. Value engineering strategy9. Raw Material (Resin) price negotiation, purchase and monitoring delivery10. Monitor Raw Material LME trend and action11. Report directly to Purchasing Development Sr. ManagerAdditional Function1. Support to purchasing department2. Project base cost saving activityKey Accomplishments:i. Best Innovation Award - Thailand plant’s model transferred project: Saving USD 3Mil/mthii. Best Task Force Team Award – Cost reduction & value engineering strategy: Saving USD 0.6Mil/mthiii. Best Employee Award – Overall contribution to company
-
-
-
-
Material Planning & Purchase Executive
-
May 2006 - Dec 2008
1. Materials Reconciliation - Metals , chemicals & compounds2. Materials Planning Local & Import3. Materials Listing, Price History and Purchases4. Consumables Planning5. Consumables Listing, Price History and Purchases6. Stationery Stock Take and Order 7. Source for alternative supplier. 8. Monitor suppliers' performance and to conduct suppliers' performance evaluation.ExportPrepare export shipping document: Invoice, Packing List, Form D, B/L.Import1. Check shipping schedule and obtain the documents (Inv, PL, B/L, COA)2. Inform forwarder and provide documents/ information as requested3. Check incoming qty and update on balance stock from MIDA approval qty4. Check and renew CJ5 when its dueAd Hoc Purchases1. Received Purchase Requisition (PR)2. Obtain 3 quotations if possible and prepare price comparison.3. Price Negotiation, issue Purchase Order (PO)and obtain approval4. After approval, distribute POs, fax to supplier, filling and follow up to ensure orders are delivered.Local Customers1. Attend customer vendor briefing every month.2. Window for customer contact3. Inform customer for delivery arrangementsAdditional Function1. As APQP team member for new product development.2. As Internal Auditor for ISO 16949.3. As Sport Club treasurer.4. As Annual Dinner team member.
-
-
-
APM PLASTICS SDN. BHD.
-
Malaysia
-
Plastics Manufacturing
-
1 - 100 Employee
-
QA Officer
-
Jul 2004 - May 2006
1. QA incoming and outgoing monitoring for plastic / polymer based automotive components.2. Testing and checking for new material to purchasing or R&D for cost reduction.3. Conduct audit to new suppliers and selected suppliers yearly and assist on vendor development.4. To arrange external calibration and internal verification for all inspection and testing tools.5. Monitor and update ISO records.6. Report directly to QA Manager.7. Prepare monthly rejection report in Quality Improvement Team Meeting.Additional Function1. Involve in plant improvement study, e.g. Kaizen, Innovative and Creative Circle (ICC), Pokka Yoke, First-In-First-Out, 5S.2. As a FMEA team member for new product development.3. As internal auditor for ISO 14001
-
-
Education
-
Universiti Sains Malaysia
Bachelor's degree, Physics
Community
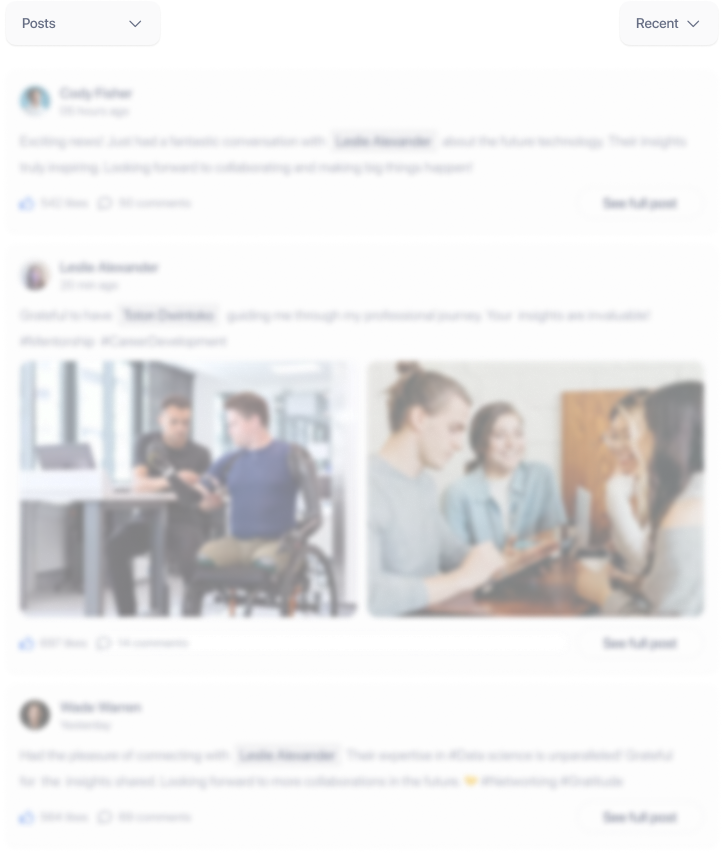