Paul Moon
Quality Manager at Mokon- Claim this Profile
Click to upgrade to our gold package
for the full feature experience.
Topline Score
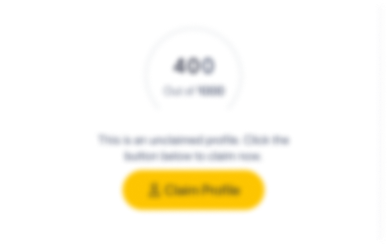
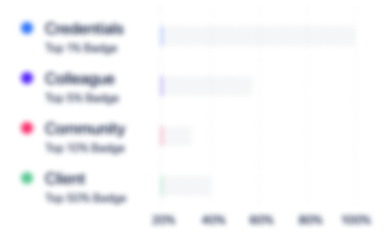
Bio


Experience
-
Mokon
-
United States
-
Machinery Manufacturing
-
1 - 100 Employee
-
Quality Manager
-
Oct 2021 - Present
Oversee the Quality Management System, Document Control, CAPA. Supervise Inspection and Test. Communicate with customers and suppliers on quality matters.
-
-
Senior Quality Engineer
-
Sep 2020 - Oct 2021
Served as Quality Representative for the Quality System. Conducted internal and supplier audits. Managed Document Control system. Managed internal CAPA system. Collected, analyzed and communicated Production quality data. Interfaced with customers and suppliers on quality issues.
-
-
-
Greatbatch Medical
-
United States
-
Medical Equipment Manufacturing
-
500 - 600 Employee
-
Senior Supplier Quality Engineer
-
Feb 2018 - Jan 2020
Monitored supplier quality and acted as primary quality contact to suppliers. Performed supplier audits and tracked resulting corrective action plans. Evaluated and dispositioned nonconforming product received from suppliers and tracked resulting corrective action plans. Participated in qualification activities for new products and suppliers. Evaluated and qualified supplier-driven change requests. Coordinated monthly Supplier Performance meetings. Monitored supplier quality and acted as primary quality contact to suppliers. Performed supplier audits and tracked resulting corrective action plans. Evaluated and dispositioned nonconforming product received from suppliers and tracked resulting corrective action plans. Participated in qualification activities for new products and suppliers. Evaluated and qualified supplier-driven change requests. Coordinated monthly Supplier Performance meetings.
-
-
-
Baxter Healthcare Corporation
-
Medina, NY
-
Sr Engineer, Supplier Quality
-
Mar 2013 - Feb 2018
Monitored supplier quality and acted as primary quality contact to suppliers. Performed supplier audits and tracked resulting corrective action plans. Evaluated and dispositioned nonconforming product received from suppliers and tracked resulting corrective action plans. Participated in qualification activities for new products and suppliers. Maintained supplier scorecards and chaired monthly supplier performance meetings. Monitored supplier quality and acted as primary quality contact to suppliers. Performed supplier audits and tracked resulting corrective action plans. Evaluated and dispositioned nonconforming product received from suppliers and tracked resulting corrective action plans. Participated in qualification activities for new products and suppliers. Maintained supplier scorecards and chaired monthly supplier performance meetings.
-
-
-
Bausch + Lomb
-
United States
-
Pharmaceutical Manufacturing
-
700 & Above Employee
-
Sr. Supplier Quality Specialist
-
Mar 2011 - Feb 2013
Monitored supplier quality and acted as primary quality contact to suppliers. Performed supplier audits and tracked resulting corrective action plans. Managed supplier quality agreements. Assisted Receiving Inspection with gauging and inspection issues. Monitored supplier quality and acted as primary quality contact to suppliers. Performed supplier audits and tracked resulting corrective action plans. Managed supplier quality agreements. Assisted Receiving Inspection with gauging and inspection issues.
-
-
-
Greatbatch Medical
-
United States
-
Medical Equipment Manufacturing
-
500 - 600 Employee
-
Inspection Supervisor
-
Sep 2009 - Nov 2010
Managed Receiving Inspection Department. Developed inspection methods, procedures and acceptance criteria. Trained Technicians and Inspectors. Managed quarantine and disposition of discrepant materials. Monitored and maintained dock-to-stock receiving system. Monitored supplier quality and acted as primary quality contact to suppliers. Performed supplier audits.
-
-
Quality Engineer
-
Feb 2003 - Sep 2009
Monitored and maintained Quality for various production lines. Coordinated quality activities for development and qualification of new implantable capacitor models and implantable battery modifications. Developed inspection and process control methods, procedures and acceptance criteria. Monitored SPC data, developed and performed studies and analysis for process improvement.
-
-
-
Woodward, Inc.
-
United States
-
Aviation and Aerospace Component Manufacturing
-
700 & Above Employee
-
Quality Assurance Engineer
-
Jan 2001 - Feb 2003
Primary contact to customers for quality issues including contract review, complaints, corrective actions, new model development and training of personnel to customer and regulatory requirements. Acted as Designated Quality Representative for Honeywell Aircraft ES&S, and Pratt & Whitney Canada.
-
-
Quality Systems Engineer
-
Jan 2000 - Jan 2001
Maintained the Quality Management System. Insured compliance to ISO 9000, AS9000 and Federal Aviation Authority (FAA) requirements. Performed internal quality audits. Hosted Regulatory and customer quality audits.
-
-
-
Greatbatch Medical
-
United States
-
Medical Equipment Manufacturing
-
500 - 600 Employee
-
Inspection Supervisor
-
Jan 1993 - Jan 2000
Managed Receiving Inspection Department. Developed inspection methods, procedures and acceptance criteria. Trained Technicians and Inspectors. Managed quarantine and disposition of discrepant materials. Monitored supplier quality and acted as primary quality contact to suppliers. Performed supplier audits. Implemented dock-to-stock receiving system Managed Receiving Inspection Department. Developed inspection methods, procedures and acceptance criteria. Trained Technicians and Inspectors. Managed quarantine and disposition of discrepant materials. Monitored supplier quality and acted as primary quality contact to suppliers. Performed supplier audits. Implemented dock-to-stock receiving system
-
-
Education
-
University at Buffalo
Bachelor of Science - BS, Business Administration -
University at Buffalo
Associate of Science - AS, Engineering Mechanics
Community
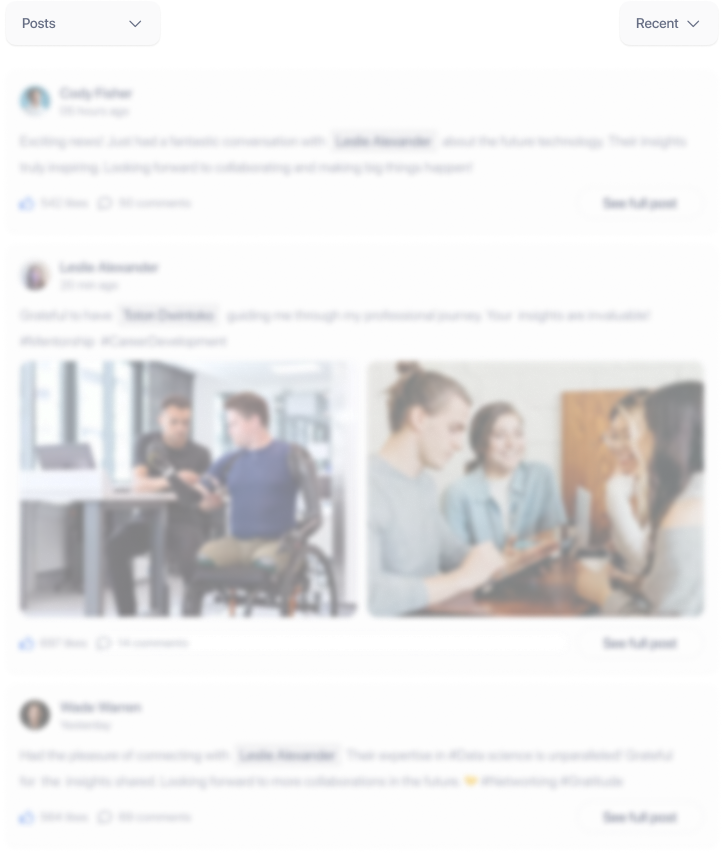