Paul Kline
Field Engineer at CANNON Instrument Company- Claim this Profile
Click to upgrade to our gold package
for the full feature experience.
Topline Score
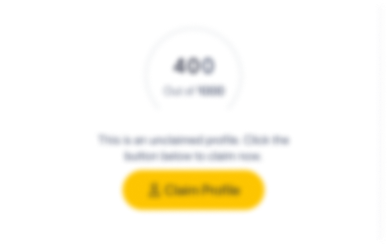
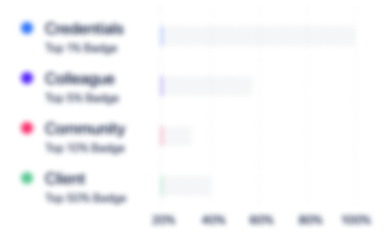
Bio


Experience
-
CANNON Instrument Company
-
United States
-
Appliances, Electrical, and Electronics Manufacturing
-
1 - 100 Employee
-
Field Engineer
-
Sep 2023 - Present
-
-
-
BIOLASE, Inc.
-
United States
-
Medical Equipment Manufacturing
-
200 - 300 Employee
-
Field Services Engineer
-
Sep 2020 - Present
-
-
-
Cartessa Aesthetics
-
United States
-
Medical Equipment Manufacturing
-
100 - 200 Employee
-
Field Engineer
-
Apr 2023 - Sep 2023
-
-
-
ZEISS Industrial Metrology
-
Germany
-
Machinery Manufacturing
-
700 & Above Employee
-
Field Services Engineer
-
Aug 2017 - Sep 2020
-
-
-
Medrad/Bayer
-
Fort Wayne
-
Field Service Engineer
-
Jul 2012 - Sep 2020
-
-
-
Océ - A Canon Company
-
Netherlands
-
Printing Services
-
700 & Above Employee
-
Digital Tech 4
-
Nov 2006 - Jun 2010
-
-
-
NCR Corporation
-
United States
-
IT Services and IT Consulting
-
700 & Above Employee
-
Customer Engineer 3
-
Jul 2005 - Nov 2006
-
-
-
-
Customer Engineer II
-
Jul 2005 - Oct 2006
I was recruited by NCR from a previous customer I serviced with Bancsource. I repaired ATMS and high speed check sorting equipment. Full line NCR trained. This position utilized my years of field and customer service experience while enhancing my organization and time management skills. All of the equipment that I was responsible for had a 98% up time. Oce used NCR as a vendor to service equipment in my region. This resulted in expanding our equipment base while maintaining our quality service and customer satisfaction expectations. Show less
-
-
-
-
Account Manager
-
Jan 2005 - Sep 2005
Bancsource hired me to work their national Wells Fargo contract in Fort Wayne and surrounding areas. I provided service on NCR 7766's, 7780's and Itrans 9810. I work closely with the other remote item processing sites with Wells Fargo and their in house maintenance group. I maintain a 98% up-time and support for Image Mark implementation. I worked on territory yearly service budgets and implemented cost savings procedures. Bancsource hired me to work their national Wells Fargo contract in Fort Wayne and surrounding areas. I provided service on NCR 7766's, 7780's and Itrans 9810. I work closely with the other remote item processing sites with Wells Fargo and their in house maintenance group. I maintain a 98% up-time and support for Image Mark implementation. I worked on territory yearly service budgets and implemented cost savings procedures.
-
-
-
Diebold Nixdorf
-
United States
-
IT Services and IT Consulting
-
700 & Above Employee
-
Customer Service Engineer
-
Feb 2002 - Feb 2003
Implement service and support on high speed Toshiba currency sorters. This was a new product to Diebold after purchasing the assets of Mosler. Contributed to organizing new technical teams to support this product. I acquired an A+ Certification and other software and technical certificates. This position required 24/7 service to Bank Vaults and Casino hard and soft count rooms. Responsible for finding and procuring various vendors for parts and supplies for this equipment while attending to all our customer needs and concerns during the transition period from Mosler to Diebold. Show less
-
-
-
Wells Fargo
-
United States
-
Financial Services
-
700 & Above Employee
-
Technician III
-
Feb 1998 - Feb 2002
Responsible for technical service for main Cash Vault, Statement Services, Item Processing in a team environment. Managed yearly department budgets and contracts/parts procurement for 5 States. Implemented cost saving maintenance programs and preventative maintenance schedules. Coordinated vendor parts availability and resources. Responsible for technical service for main Cash Vault, Statement Services, Item Processing in a team environment. Managed yearly department budgets and contracts/parts procurement for 5 States. Implemented cost saving maintenance programs and preventative maintenance schedules. Coordinated vendor parts availability and resources.
-
-
Education
-
Colorado Aero Tech
FAA Airframe and Power Plant License, Aircraft maintenance and repair
Community
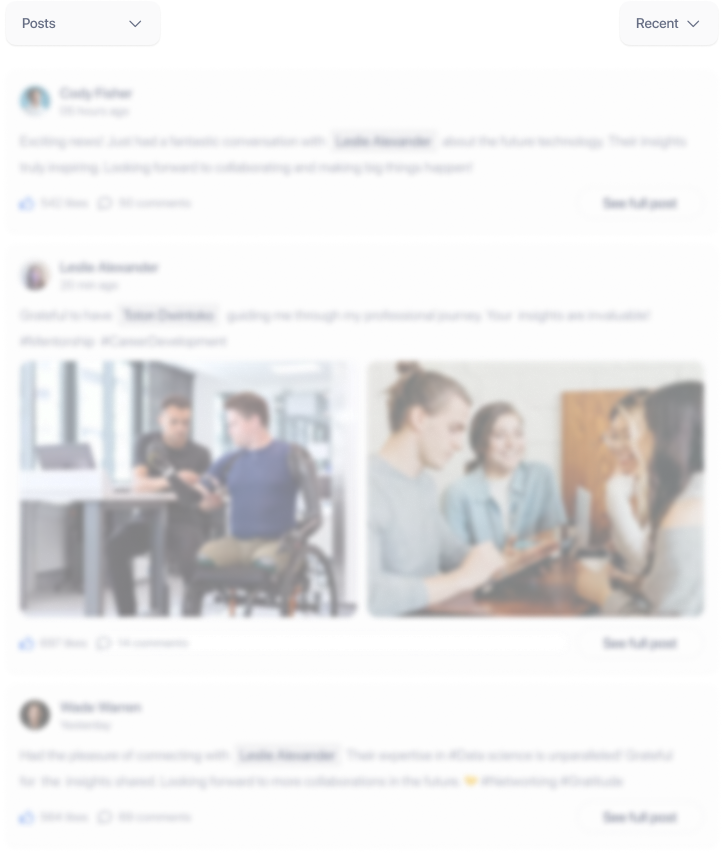