Paul Hetherington
Principal Process Engineer at DBD International- Claim this Profile
Click to upgrade to our gold package
for the full feature experience.
-
German -
Topline Score
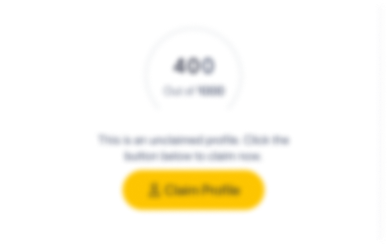
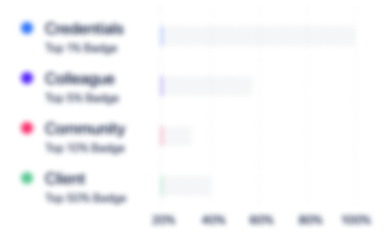
Bio


Experience
-
DBD International
-
United Kingdom
-
Business Consulting and Services
-
1 - 100 Employee
-
Principal Process Engineer
-
Jul 2023 - Present
-
-
Senior Process Engineer
-
Aug 2022 - Jul 2023
-
-
-
OLPHA LIMITED
-
United Kingdom
-
Mechanical Or Industrial Engineering
-
Director/Process Engineering Specialist
-
Jun 2015 - Present
Providing process design resources to numerous clients across numerous industrial sectors Providing process design resources to numerous clients across numerous industrial sectors
-
-
-
Assystem
-
France
-
Business Consulting and Services
-
700 & Above Employee
-
Senior Process Engineer
-
Apr 2022 - Aug 2022
Developing the process design requirements for Rolls Royce SMR - Turbine Island Developing the process design requirements for Rolls Royce SMR - Turbine Island
-
-
-
Px Engineering Consultants Limited
-
United Kingdom
-
Industrial Machinery Manufacturing
-
1 - 100 Employee
-
Senior Process Engineer
-
Oct 2021 - Mar 2022
Independent process engineering support to HAZOP team for Fellside CHP. Checking and originating of steam venting reports and calculations in support of Fellside operations team. Originator and checker for Verdis waste plastics to liquid fuel project for Saltend Chemical works including production of control valve datasheets and line list. Independent process engineering support to HAZOP team for Fellside CHP. Checking and originating of steam venting reports and calculations in support of Fellside operations team. Originator and checker for Verdis waste plastics to liquid fuel project for Saltend Chemical works including production of control valve datasheets and line list.
-
-
-
WHP
-
United Kingdom
-
Pharmaceutical Manufacturing
-
1 - 100 Employee
-
Senior Process Engineer
-
Feb 2021 - Jul 2021
Commissioning of KD Pharma fish oil refining facility at Seal Sands, UK. Feb-April 2021 Engagement Activities and Responsibilities included: Planning, coordinating and executing commissioning activities for fish oil storage vessels and associated process equipment including nitrogen blanketing systems, offloading and transfer pumps, automatic valves and level instruments. Lead process design engineer on a powder compaction project for Merck’s dry powder manufacturing facility in Irvine. April-July 2021. Engagement Activities and Responsibilities included: • Development of the process design from concept to approved for construction status. • Responsible for the preparation of P&IDs, Functional Design Specification, process calculations - line and relief sizing for various parts of the process and clean compressed air systems. • Preparation of line and equipment schedules. • Development of a dust extraction system. • Support in developing the hazardous area classification. • General vendor engagement for equipment and process development including rotary valves, bursting discs, powder compaction unit, air regulators, PSVs and regulating valves. • Attendance in HAZOP and responsible for close out of associated actions. • Support to other engineering disciplines. Show less
-
-
-
Otto Simon
-
United Kingdom
-
Design Services
-
1 - 100 Employee
-
Senior Process Engineer
-
Oct 2019 - Oct 2020
Working on a brownfield modification project to an LDPE plant in the middle east to allow the plant to make grades of EVA polymer. Activities and Responsibilities included: • Responsible for the preparation of PFDs, P&IDs process calculations, vessel, tank, silo and pump sizing for various parts of the process and utility systems.. • Checking of process deliverables as above. • Development of a Xylene Wash System for removal of polymer from the reactor loop and downstream equipment with particular attention to high/low pressure interfaces and safeguarding the integrity of the existing/new equipment. Show less
-
-
-
Worley
-
Australia
-
Professional Services
-
700 & Above Employee
-
Senior Process Engineer
-
Dec 2018 - Jun 2019
Chirag Conventional Gas Lift Project Working on a brownfield modification project to the Chirag offshore platform in the Azerbaijan sector of the Caspian Sea for BP during Define and Execute phases for the project. Activities and Responsibilities included: • Responsible for the preparation of Scope of Work for dynamic simulations, process calculations using HYSYS including Process Safety Time from vessels and sizing control valves for pressurisation/depressurisation of a gas pipeline. • Responsible for checking the FEED report for integrity and cross referencing. • Checking of FEED process deliverables including P&IDs, Safeguarding Diagrams, PFDs. • Updating FEED process deliverables including line lists, Instrument datasheets and equipment datasheets. • Checking Pigging and Control and Operating Philosophies. • Development of pipeline pigging strategies and pigging process operations for presentation and review with the client. Show less
-
-
-
Jacobs
-
United States
-
Business Consulting and Services
-
700 & Above Employee
-
Senior Process Engineer
-
Sep 2018 - Nov 2018
Working in the Sellafield BEP Project Delivery Team. Responsible for preparation of design change proposals, reviewing the design maturity of process documentation and providing checking support of process documentation including air compressor systems and water storage and distribution. Working in the Sellafield BEP Project Delivery Team. Responsible for preparation of design change proposals, reviewing the design maturity of process documentation and providing checking support of process documentation including air compressor systems and water storage and distribution.
-
-
-
M+W Group
-
Germany
-
Semiconductors
-
700 & Above Employee
-
Senior Process Engineer
-
Jun 2015 - Jun 2018
Lead Process Engineer on Dounreay Shaft and Silo Decommissioning Project The Project is to develop the Concept Design for a decommissioning facility to remove, process and package Intermediate Level nuclear Waste from storage facilities on the Dounreay site, Caithness, Scotland. Activities and Responsibilities include: • Lead Process engineer responsible for the development of process deliverables on the project including Process Description, Process Flow Diagrams, Block Flow Diagrams, Mass Balance etc. • Input into multi-discipline design and design management including support of sub-contractors and the Client. • Input into planning and scheduling for Scheme Design. Show less
-
-
-
Amec Foster Wheeler
-
United Kingdom
-
Oil and Gas
-
700 & Above Employee
-
Senior Process Engineer
-
Sep 2011 - Sep 2014
Lead process engineer developing offshore solutions to handling produced water on the Azeri and Deep Water Gunashli Field offshore platforms. Working as part of an integrated multi-discipline team with BP on a Category B ECMS brownfield projects up to and in excess of 200M USD as well as support on smaller Cat C projects onshore and offshore (<15M USD). Activities and Responsibilities include: • Process lead for the development of process options during the early stages of the Dirty Water Injection project (Appraise-Select) which included assessment hydrocyclones, degassers, desanding equipment, fine filtration, solids handling, pigging and direct re-injection of high solids containing produced water offshore. • Support on Cat C projects working as an interface between different project and discipline engineers. • Support for Sangachal Flare design, checking calculations. • Support on Chirag Gas Cap Project developing early solutions to fit around TAR constraints. • Technical lead for FEED team developing pre-Appraise options for process improvements for offshore and onshore assets. • Originator/Checker of process documents including calculations, schedules, PFDs, UFDs, P&IDsTurnaround documents, Basis of Design, SWOT analysis, vendor questionnaires, datasheets. • Input into project level documentation including HAZID, execution plans and schedules. • Analysis of returned vendor information. • Co-ordination and technical support for other groups within the project team. • Management of a team of up to 6 process engineers including the development of 3 Azeri national engineers. • Responsible for the input into Process aspects of the project schedule and the input into man hour estimates. • Preparation and presentation of technical ‘lunch and learn’ topics • Acting Deputy for Principal Process engineer (HoD) during rotations, delegated the responsibility of approval of documents and supervising a department of 25+ engineers and designers. Show less
-
-
-
Jacobs
-
United States
-
Business Consulting and Services
-
700 & Above Employee
-
Process Engineer
-
Feb 2011 - May 2011
Transferred when Jacobs bought Aker Solutions Transferred when Jacobs bought Aker Solutions
-
-
-
Aker Solutions
-
Norway
-
Oil and Gas
-
700 & Above Employee
-
Process Engineer
-
May 2007 - Feb 2011
Process Engineer on Urenco TMF Project • Project Period: November 09 – May 11 • Project size: reimbursable budget in excess of £1 million per month FEED study developing design and costs for nuclear fuels client with an estimated EPC contract price of 350 million euros. Process Engineer for ACKtiv Nuclear Process Group for Sellafield Ltd FGMSP Retrievals Project • Project Period: November 08 –Nov09 • Project Size: Reimbursable contract in excess of £1 million per month • Process Engineer responsible for preparing and developing the project process documentation including, but not limited to the process description, system line sizing calculations, sludge retrieval operations mass balance and pump and equipment calculations. Process and Commissioning Engineer working on Northumbrian Water Bran Sands AMP4 Capital Maintenance Projects • Project Period: May 07 to October 08 • Maintenance and upgrading of large scale municipal/industrial treatment works including regional sludge handling facilities, odour control and industrial waste management. Design and commissioning of refurbished and new equipment including process pumps and valves, odour control, SCADA modifications, tankered waste reception tank facilities, sludge straining, aeration headers, poly-electrolyte dosing, sodium hydroxide preparation and dosing, heat exchangers and hydrated lime plant. • Project Size £20k to £1 million. Show less
-
-
-
Conder Products
-
Peterlee, County Durham
-
Process and Project Engineer
-
Apr 2006 - Apr 2007
Key responsibilities: • Working as part of a small team managing several small-scale sewage treatment contracts (£50-300k). Co-ordinating between factory, client, suppliers, installation and commissioning teams. Collating contract specific information in correct format and place for easy access. • Costing/quoting for technical sales alongside specification and procurement of mechanical/electrical equipment. • Preparing Autocad drawings of treatment plant schemes for client approval and in-house detail design. Liaising with other engineering staff in detail design. • Preparing Operations and Maintenance manuals for treatment schemes including P&IDs and control philosophy • Trouble-shooting mechanical and process problems and designing remedial chemical dosing systems. • Assisting the business in continuous improvement activities using techniques such as 5S, Standard Operations and Kaisen. Mostly active in improving documentation and information access and storage. Show less
-
-
-
Protensive
-
Centre for Life, Newcastle Upon Tyne
-
Research Engineer
-
Apr 2004 - Sep 2005
Working for a university spin-out SME research and development company with a £1 million turnover developing new process technologies for the chemical and pharmaceutical industries. Responsibilities: • Design, procurement, assembly, commissioning and operation of laboratory sized process equipment with focus on controlling costs. Hands-on work of all aspects of building and maintaining equipment. • Support of in-house and client project trials utilising chemical laboratory experimentation and analysis. Planning, performing and evaluating experimental work. Reporting work to management and clients. • IT support: Corporate website administrator, updating content and liaising with web designers. Supported aspects of office IT. Show less
-
-
-
Newcastle University
-
United Kingdom
-
Higher Education
-
700 & Above Employee
-
PhD Research Student
-
1999 - 2003
I carried out research activities in the field of Process Intensification, an emerging philosophy in the design and operation of industrial processes. My primary research was investigating rapid crystallisation using a spinning disc reactor to try and control product quality. The key roles and activities included: • Fundamental literature surveys of key technologies and peripheral supporting scientific information. • Extensive chemical laboratory work, designing and setting up experiments, co-ordinating with supervisors, research staff, technical staff and industrial contacts to prioritise work. • Carrying out short term projects for industrial partners which included heat exchanger testing and chemical reaction experiments to determine heat and mass transfer characteristics. • Using numerous analysis techniques such as high-speed cameras and particle size analysers as well as simple instruments used in the laboratory to gather data. • Presentation of data in-house and at national and international conferences. • Technical support for the future development of these technologies within the university and Protensive Limited. • Teaching and demonstration in undergraduate laboratories, setting up labs and aiding teaching and technical staff. Marking assignments and giving feedback support to students. Show less
-
-
-
Enron Power Operations Ltd
-
Seal Sands, Teesside
-
Vacation Engineering Work Placements
-
1996 - 1998
Summer 1996 and 1997, MEng research project Jan-May 1998 I was student engineer based at the cryogenic gas processing plant Key roles and activities: • Study of the efficiency and operability of a gas-fired process heater. I determined its efficiency using mass transfer calculations based on analysis of plant data which I gathered. I also took anecdotal evidence from operations staff as to the difficulties with it’s operation. I then wrote a report recommending ways to improve both efficiency and operability. • Feasiblity study of a Combined Heat and Power scheme on plant. Investigating heat and power demands on-site and reporting findings to operations manager to help determine most suitable gas turbine for project. • HAZOP and general engineering support in investigating equipment retro-fitting requirements and performing calculations for additional pipework modifications. • Cataloguing of the technical drawings in the site archive ready for input into electronic database. • I carried out my 4th year masters degree research project by investigating the issues surrounding a fractionation column on site and suggesting ways in which it may be debottlenecked. I used simulation software packages and anecdotal evidence as to what was affecting the column and how these issues might be resolved. The work was presented as a dissertation at both site and university. Show less
-
-
Education
-
University of Newcastle-upon-Tyne
MEng, Chemical and Process Engineering -
Newcastle University
PhD, Chemcal and Process Engineering: Process Intensification -
Hartlepool 6th Form College
A-level, Maths and Mechanics, Physics, Chemistry, General Studies
Community
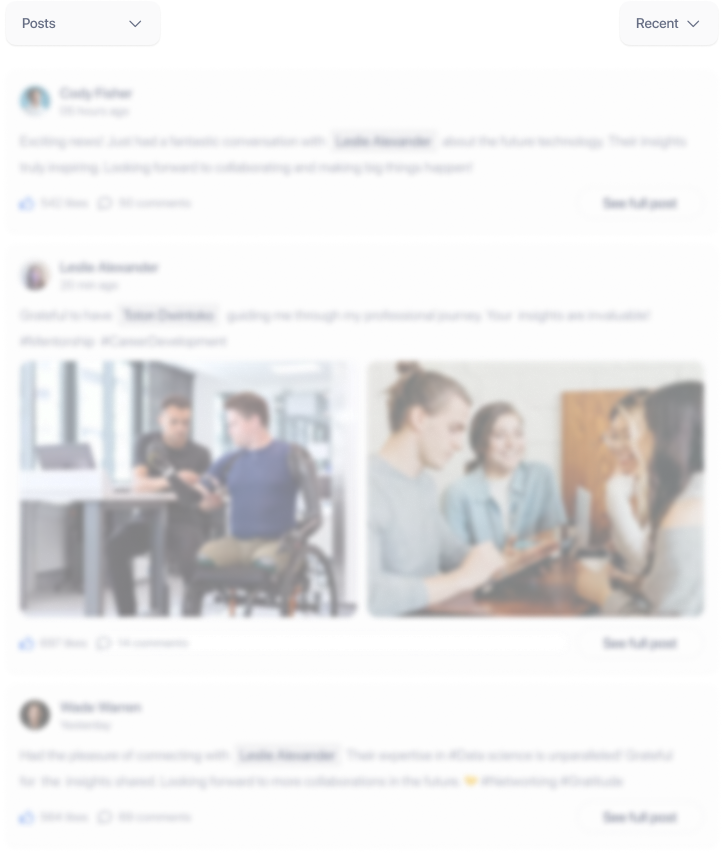