Paul Hamilton
President, Operational Excellence & Continuos Improvement at Avon Protection- Claim this Profile
Click to upgrade to our gold package
for the full feature experience.
Topline Score
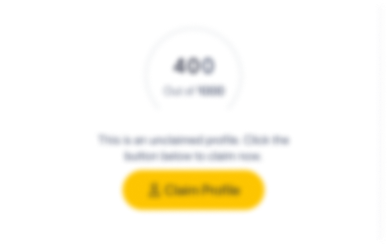
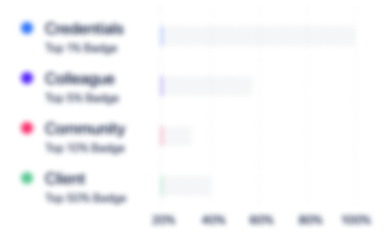
Bio


Experience
-
Avon Protection
-
Defense & Space
-
200 - 300 Employee
-
President, Operational Excellence & Continuos Improvement
-
Apr 2023 - Present
Area of focus: - Establish global operations strategy deployment, execution, and lean operating system. - Deploy end to end value chain optimization, from customer demand through to customer satisfaction. - Empower the Avon team with operational excellence and CI knowledge to organically grow and scale systemically, for decades to come. - Drive business excellence and network optimization throughout the Avon enterprise, as an executive board member. Area of focus: - Establish global operations strategy deployment, execution, and lean operating system. - Deploy end to end value chain optimization, from customer demand through to customer satisfaction. - Empower the Avon team with operational excellence and CI knowledge to organically grow and scale systemically, for decades to come. - Drive business excellence and network optimization throughout the Avon enterprise, as an executive board member.
-
-
-
Smith+Nephew
-
United Kingdom
-
Medical Equipment Manufacturing
-
700 & Above Employee
-
Vice President, Global Operations Strategy, Transformation, and Operational Excellence
-
Dec 2022 - May 2023
Global Operational strategy, transformation, and operational excellence focus: - Improve - Develop - Deploy The "End to End Smith+Nephew Way" value chain operating system Global Operational strategy, transformation, and operational excellence focus: - Improve - Develop - Deploy The "End to End Smith+Nephew Way" value chain operating system
-
-
-
Ultra Electronics Group
-
Defense & Space
-
700 & Above Employee
-
VP of Global Operational Excellence & Continuous Improvement
-
Apr 2021 - Dec 2022
• Strategically constructed the 3-5 year Global Lean Operating System, CI strategy & transformation across (47) plants. • Established the OpEx and CI Transformation Roadmap in first 100 days. • Established the strategic Operating model and daily operations from leaders to the work force. • Deployed the Sprint/Kaizen activity program (kaizen facilitation and valuation), CI principles training for The Board of Directors, C-Suite, and Sr leaders to receive strategy approval to deploy and build an effective OpExCI COE, known as the “Ultra Improvement Group”. • In six months developed and deployed the “Ultra Way” and “One Ultra” programs. • Introduced the Ultra Way Operating System (Strat deployment, SIOP, Ultra Way Operating System, Performance Management tracking, Change Management,). • Empowered (412) colleagues to understand and facilitate Kaizens activities, fostering (945) self-lead activities. • Reported to the corporate CFO, led (4) global Directors, (8) Regional Managers, (18) local OpExCI leaders at strategic sites, and served as a strategic partner to (14) Business Unit Presidents and Vice Presidents. Show less
-
-
-
American Trailer World
-
Richardson, Texas, United States
-
Corporate Director of Lean Mfg., Continuous Improvement (CI) & Operations Support
-
Dec 2019 - Dec 2020
• Strategically constructed the 3-year Corporate Lean Operating System, CI strategy / road map across (25) plants. • Aligning (4) subsidiary acquisitions through effective Lean/CI vision, mission, and cascading metrics. • Achieved $9.1 Million dollars gross labor savings, exceeding the $6.8 million-dollar annual target. • Cascaded the corporate Kaizen Activity Initiative, enabling the completion of (82) productivity Kaizen events, improving labor hours/unit, First Pass Yield, Standard Work, problems solving and Lean Daily Management. • Report to COO, and lead the corporate Lean-CI Team of, (3) directors, (4) Lean Practitioners, (4) Lean Leaders, (3) Lean Change Agents, (Mentored (52) Operations Plant Managers and General Managers). Show less
-
-
-
Xylem
-
United States
-
Industrial Machinery Manufacturing
-
700 & Above Employee
-
Global Operations Support Sr. Leader - Equipment Reliabilty, Quality, Logistics, Material Handling
-
Feb 2017 - Nov 2019
Strategically cascaded the 1-3-year global Objectives, Goals, Strategies, and Measures (OGSM) initiatives. • Pioneered the inception of the Equipment/Tool Reliability, Preventative Maintenance, Global Operational Logistics, and Material Handling functions with the value stream. • Pioneered the company’s first TPM & Asset Management initiative (equipment inspection, tool replenishment, tool repair, preventative and proactive maintenance, work process flow, and build forecasting). • Achieved (18+% year over year) improvement in equipment utilization through deploying the corporate equipment utilization, availability & OEE initiative and Continuous Improvement programs. • Strengthened the corporate and department O & M, Capex, R&M budgets ($112 million). • Achieved an (43%) increase in On-time Delivery results from 51% up to 94% (year over year). • Achieved a (32%) reduction in Safety Incidents through implementation of a Workplace Organization program. • Achieved a (41%) efficiency gain in productivity through implementation of a Lean Daily Management initiative. • Spear header, and deployed the Continuous Improvement roadmap, principles, practices & training programs. • Reported to COO, Lead (53) Operations professionals, across (4) plants (Operations, Equipment Maintenance, Operational Logistics, and Material Handling functions) in North America (Canada, US). Provide global operations strategic direction for (3) international plants. Show less
-
-
-
Luminant
-
United States
-
Utilities
-
700 & Above Employee
-
Senior Mine/Plant Director - Maintenance & Reliability
-
Oct 2014 - Oct 2016
-
-
Regional Maintenance & Reliability Sr. Leader
-
Oct 2010 - Sep 2014
-
-
Corporate Lean Operating System Sr. Manager
-
Mar 2008 - Sep 2010
-
-
-
Toyota North America
-
United States
-
Motor Vehicle Manufacturing
-
700 & Above Employee
-
Operations Management Development Division (OMDD) - Toyota Production System Change Agent/Consultant
-
Jun 2005 - Mar 2008
-
-
-
Toyota Motor Corporation
-
Motor Vehicle Manufacturing
-
700 & Above Employee
-
Mid Management- Department Leader
-
Jan 1997 - May 2005
Roles Held: • Staff Group Leader (TPS Department, 2004-2005) • Spec II Group Leader (Plastics Department, 2001-2003) • Spec I Group leader ( Production, 2000-2001) • Team Leader/Front-Line Supervisor, (Production,1998-2000) • Team Member (Production, 1997-1998) Roles Held: • Staff Group Leader (TPS Department, 2004-2005) • Spec II Group Leader (Plastics Department, 2001-2003) • Spec I Group leader ( Production, 2000-2001) • Team Leader/Front-Line Supervisor, (Production,1998-2000) • Team Member (Production, 1997-1998)
-
-
Education
-
San Jose State University
Bachelor’s Degree
Community
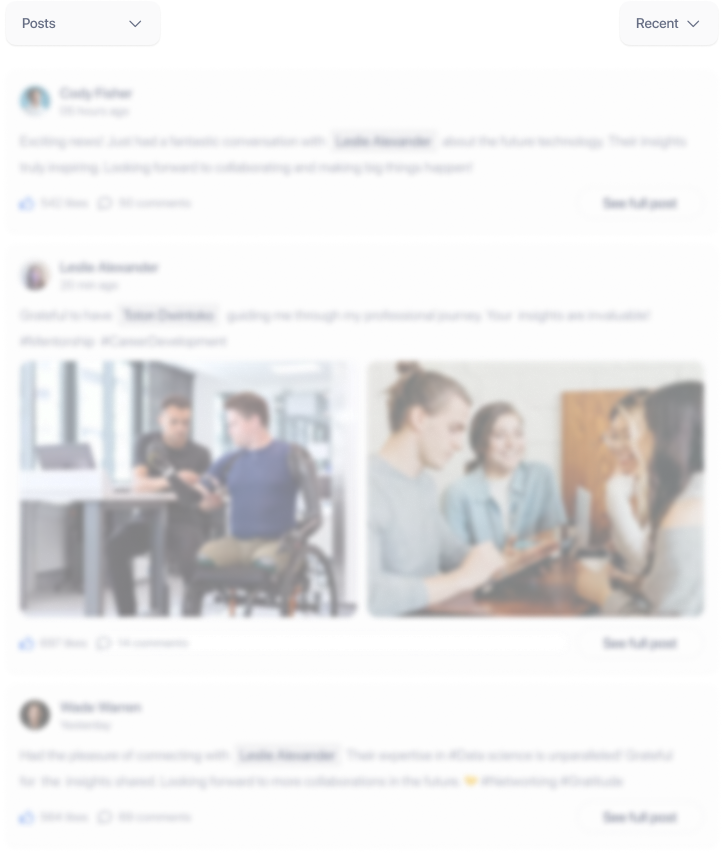