Paul Booth
Maintenance Specialist at CF Fertilisers UK Ltd- Claim this Profile
Click to upgrade to our gold package
for the full feature experience.
-
English -
Topline Score
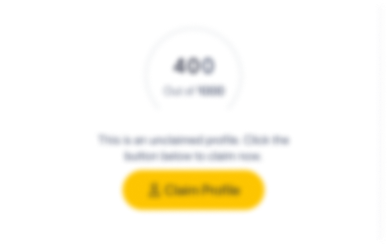
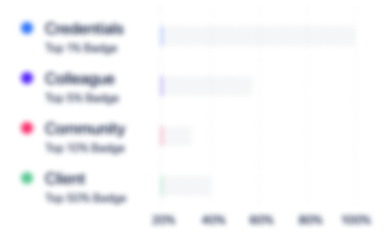
Bio

John Harrison
My experience of Paul is that he was always keen to learn new skill and was enthusiastic in applying those skills to improve efficiency and accuracy within his job. Paul did not just do the job, he always looked to do it better.

John Harrison
My experience of Paul is that he was always keen to learn new skill and was enthusiastic in applying those skills to improve efficiency and accuracy within his job. Paul did not just do the job, he always looked to do it better.

John Harrison
My experience of Paul is that he was always keen to learn new skill and was enthusiastic in applying those skills to improve efficiency and accuracy within his job. Paul did not just do the job, he always looked to do it better.

John Harrison
My experience of Paul is that he was always keen to learn new skill and was enthusiastic in applying those skills to improve efficiency and accuracy within his job. Paul did not just do the job, he always looked to do it better.

Credentials
-
Prince2 Practitioner
MAEGIS LIMITEDMar, 2016- Oct, 2024
Experience
-
CF Fertilisers UK Ltd
-
United Kingdom
-
Chemical Manufacturing
-
100 - 200 Employee
-
Maintenance Specialist
-
Sep 2020 - Present
-
-
-
SAICA Pack U.K. Ltd
-
United Kingdom
-
1 - 100 Employee
-
Maintenance Manager
-
Jan 2019 - Present
Outline Maintenance lead in a FMCG business, with a team of 4 Reliability Engineers, 6 Shift Engineers, a Storeman and various Contractors. Key Responsibilities Leading planned and reactive maintenance strategy – Auditing and developing PM, SOP, SsoW. Staff development – Implementation of training plans, Process/Area ownership, Improving team communication (Eng & Ops) Improve reliability and performance OEE – MTBF & MTTR strategic improvement plans. Improve the site team performance with strong leadership and direction. Strict budget management – Activity risk management and prioritisation. Health, Safety & Environment – Complete site management safety audits and lead department meetings. Key Achievements/Projects Advancing contractor management for improved control and safety, reviewing and updating permits and contractor RAMS with all site visits coordinated and scheduled & Implementing new service contracts. No control measures previously in place. Developing RCA methodology and processes within both maintenance and operations teams to achieve MTBF and MTTR both going in the right direction consistently through time in the business. Improving site BRC rating from C to A during recent audits. Overhaul Project for site fire fighting sprinkler systems, equipment and process alongside FM Global auditing. Implemented a new maintenance schedule and reporting structure, to increase PPM compliance above 95%. New reporting of work completion and of reactive work enabled new KPI tracking and Asset Reliability investigation. Responsible for creating and implementing a Tier system for all outstanding work, managing expectations, prioritisation, feedback, impact, resource requirements and costs. Previously there was no visibility of outstanding work, resources or costs required. Show less
-
-
-
-
Maintenance Scheduler
-
Oct 2016 - Nov 2018
Outline Create and implement the scheduler position from scratch in a top tier COMAH chemical site. Key Achievements/Projects Setting up all new procedures and processes to move the business forward with maintenance by improving efficiency, utilisation and schedule compliance using TPM principles. Setting up and running a full PM review and update. Setting up the integration and communication between planners, supervisors, engineers, contractors, mechanical, electrical, instrumentation trades and operations. Developing several cost reducing initiatives and doubling the utilisation of the maintenance trades on plant. Creating and executing several projects to reduce work backlog from >3k to <300. Reducing PM backlog from >300 to <30 rolling. Show less
-
-
-
ZF Group
-
Germany
-
Motor Vehicle Manufacturing
-
700 & Above Employee
-
Production Planner
-
Jan 2016 - Oct 2016
Working in a temporary position after being made redundant from the Steelworks due to the business liquidating. Working in a temporary position after being made redundant from the Steelworks due to the business liquidating.
-
-
-
-
Reliability Engineer
-
Nov 2013 - Oct 2015
OutlineTo work with all Engineering and Operational teams to improve asset reliability and uptime.Key ResponsibilitiesIdentification and implementation of strategies to improve asset and process reliability in order to meet the business, Safety, Environmental, Financial and Operational objectives at minimum cost and in the safest manner within a top tier COMAH site.Key Achievements/ProjectsManaging a maintenance task analysis project, completely renewing all plant maintenance plans on SAP through a rigorous process of functional location and equipment auditing, risk ranking and PM development using RCM & TPM.Creating and implementing new procedures for tracking delays and production losses, leading RCA for operations and maintenance.Project managing and scheduling a £1m shutdown with strict time and cost constraints, high risk work and interface issues.Being part of a site wide (over 10 plants), maintenance strategy team led by the UK Engineering Director. Made redundant due to business failing. Show less
-
-
Maintenance Planner
-
Apr 2013 - Nov 2013
Part of the maintenance planning team at Redcar Coke Ovens to ensure the smooth running of all maintenance tasks on plant. Responsible for updating the planning process to provide daily and monthly KPI information for job completion.Quickly became a SAP super user with detailed knowledge for MM and PM (Material Management & Plant Maintenance).
-
-
-
TMD Friction UK Ltd
-
Automotive
-
100 - 200 Employee
-
Production Planner
-
May 2007 - Apr 2013
Production planning, Production reports, KPI, NPI & Customer OTIF. Responsible for overhauling, streamlining and improving the planning process and system & integrating new planning EPS software into the business. Reducing planning team requirement from 3 to 1. Carrying out internal audits to automotive standard TS16949. Production planning, Production reports, KPI, NPI & Customer OTIF. Responsible for overhauling, streamlining and improving the planning process and system & integrating new planning EPS software into the business. Reducing planning team requirement from 3 to 1. Carrying out internal audits to automotive standard TS16949.
-
-
-
Nifco UK Limited
-
United Kingdom
-
Motor Vehicle Manufacturing
-
100 - 200 Employee
-
Unit Production Manager
-
Aug 2003 - Jan 2007
Operational Management in a 2nd Tier Automotive manufacturing plant. Man Management, Training, 5S, Kaizen, Customer Service, RCA, TS16949/ISO9001, Quality Auditing, NPI, Continuous Improvement, Production Planning. Operational Management in a 2nd Tier Automotive manufacturing plant. Man Management, Training, 5S, Kaizen, Customer Service, RCA, TS16949/ISO9001, Quality Auditing, NPI, Continuous Improvement, Production Planning.
-
-
Education
-
TEESSIDE UNIVERSITY
Bachelor’s Degree, Mechanical Engineering -
Oakham School
High School, Mathematics, Physics, Electronics, Design & Technology
Community
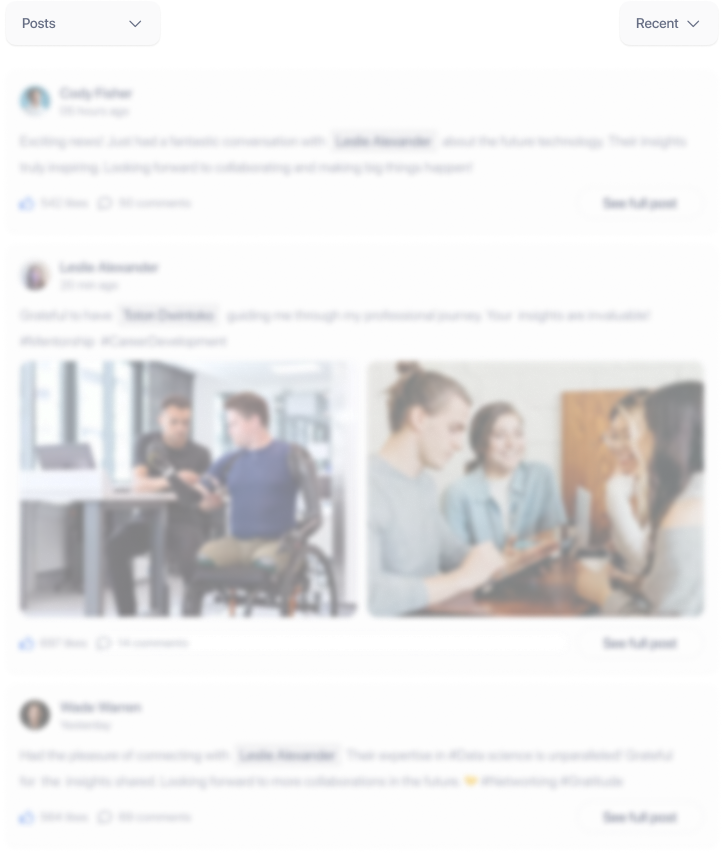